The History of Printed Circuit Boards
Early Developments
The concept of printed circuit boards can be traced back to the early 20th century. In 1903, Albert Hanson, a German inventor, filed a patent for a method of creating an electrical connection by bonding wire to a flat surface. This laid the foundation for the development of PCBs.
The Advent of PCBs
In the 1920s, Charles Ducas, an American inventor, created a method for electroplating circuit patterns onto an insulated surface. This technique was further refined by Paul Eisler, an Austrian engineer, who developed the first printed circuit board for a radio set in 1936.
Widespread Adoption
During World War II, PCBs played a crucial role in military applications, such as proximity fuses for artillery shells. The demand for compact and reliable electronic devices drove the advancement of PCB technology. In the 1950s and 1960s, PCBs became more widely adopted in consumer electronics, revolutionizing the industry.
The Manufacturing Process of PCBs
Design and Layout
The PCB manufacturing process begins with the design and layout of the circuit. Engineers use specialized software to create schematic diagrams and convert them into a physical layout. The layout determines the placement of components, traces, and vias on the PCB.
Substrate Preparation
The substrate, typically made of fiberglass or other insulating materials, is cleaned and prepared for the subsequent steps. Copper foil is laminated onto the substrate to form the conductive layer.
Photoresist Application
A photoresist layer is applied to the copper-clad substrate. This light-sensitive material will be used to transfer the circuit pattern onto the copper layer.
Exposure and Development
The photoresist-coated substrate is exposed to UV light through a photomask, which contains the circuit pattern. The exposed areas of the photoresist become soluble and are removed during the development process, revealing the desired circuit pattern on the copper layer.
Etching
The exposed copper areas are etched away using a chemical solution, leaving only the desired circuit pattern on the substrate.
Drilling and Plating
Holes are drilled in the PCB to accommodate through-hole components and vias. The holes are then plated with a conductive material, typically copper, to establish electrical connections between layers.
Solder Mask and Silkscreen
A solder mask layer is applied to the PCB to protect the copper traces and prevent solder bridges. A silkscreen layer is added to provide component labels, logos, and other markings.
Surface Finishing
The exposed copper areas are coated with a protective finish, such as HASL (Hot Air Solder Leveling), ENIG (Electroless Nickel Immersion Gold), or OSP (Organic Solderability Preservative), to prevent oxidation and enhance solderability.
Assembly and Testing
The manufactured PCB undergoes a final inspection and testing process to ensure its functionality and adherence to specifications. Components are then soldered onto the PCB using various techniques, such as through-hole or surface mount technology (SMT).
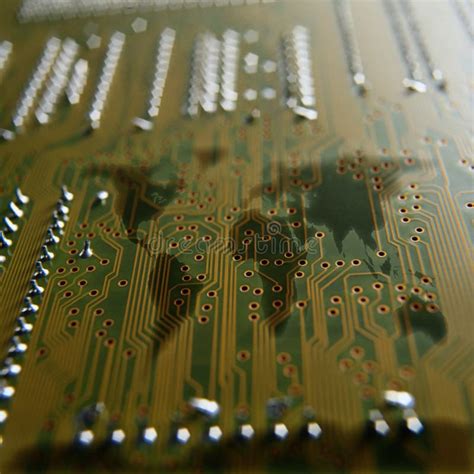
Types of PCBs
Single-sided PCBs
Single-sided PCBs have conductive traces and components on only one side of the substrate. They are the simplest and most cost-effective type of PCB, suitable for basic electronic applications.
Double-sided PCBs
Double-sided PCBs have conductive traces and components on both sides of the substrate. Vias are used to establish electrical connections between the two layers. Double-sided PCBs offer higher component density and more complex circuitry compared to single-sided PCBs.
Multi-layer PCBs
Multi-layer PCBs consist of multiple layers of conductive traces separated by insulating layers. They can have four, six, eight, or even more layers, allowing for highly complex and dense circuitry. Multi-layer PCBs are commonly used in advanced electronic devices, such as smartphones, computers, and aerospace systems.
Flexible PCBs
Flexible PCBs, also known as flex circuits, are made from flexible materials like polyimide or polyester. They can bend and conform to various shapes, making them ideal for applications that require flexibility or where space is limited. Flexible PCBs are commonly used in wearable devices, medical equipment, and automotive electronics.
Rigid-Flex PCBs
Rigid-flex PCBs combine the benefits of both rigid and flexible PCBs. They consist of rigid sections connected by flexible sections, allowing for three-dimensional configurations and improved reliability in applications that require both stability and flexibility.
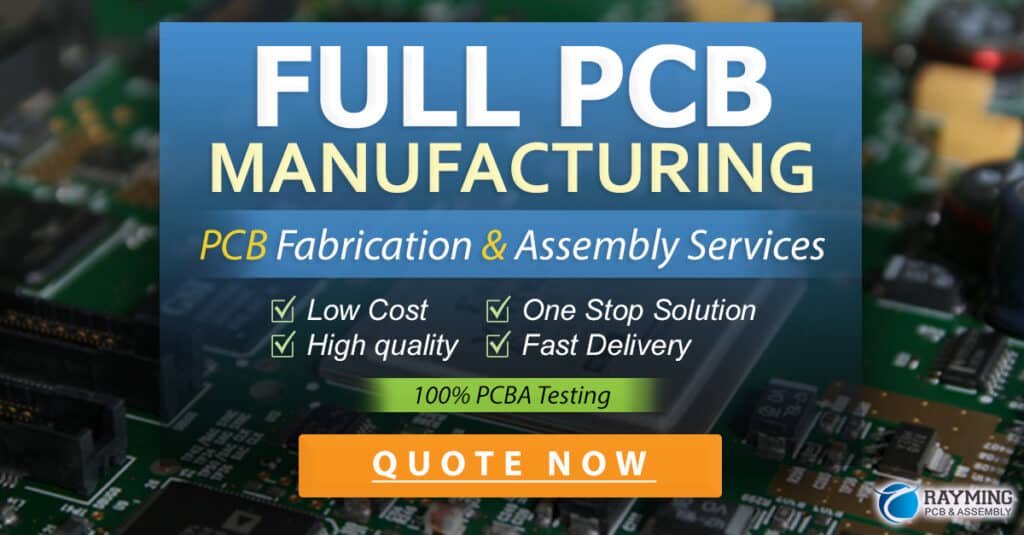
Applications of PCBs
Consumer Electronics
PCBs are ubiquitous in consumer electronics, such as smartphones, tablets, laptops, televisions, and gaming consoles. They enable the miniaturization and functionality of these devices, allowing for compact and feature-rich products.
Automotive Electronics
Modern vehicles rely heavily on PCBs for various systems, including engine control units (ECUs), infotainment systems, safety features, and driver assistance technologies. PCBs in automotive applications must withstand harsh environments and meet stringent reliability requirements.
Medical Devices
PCBs play a crucial role in medical devices, such as patient monitors, diagnostic equipment, and implantable devices. They enable the miniaturization and precision required for medical applications, while adhering to strict regulatory standards for safety and reliability.
Industrial Automation
PCBs are essential components in industrial automation systems, such as programmable logic controllers (PLCs), sensors, and actuators. They enable the control and monitoring of industrial processes, improving efficiency and productivity.
Aerospace and Defense
PCBs used in aerospace and defense applications must meet rigorous standards for reliability, durability, and performance. They are found in avionics systems, satellites, military communication devices, and weapon systems.
Renewable Energy
PCBs play a vital role in renewable energy systems, such as solar inverters, wind turbine controllers, and energy storage systems. They enable the efficient conversion, control, and management of renewable energy sources.
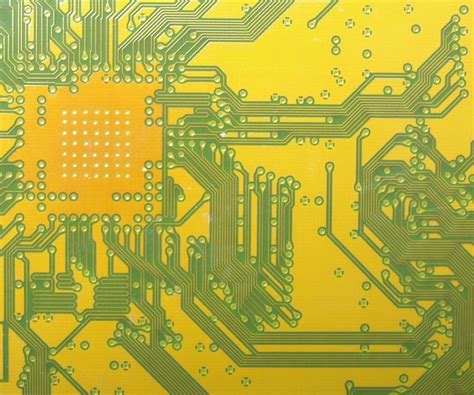
Future Trends in PCB Technology
Miniaturization
The demand for smaller and more compact electronic devices continues to drive the miniaturization of PCBs. Advancements in materials, manufacturing processes, and component packaging enable the creation of high-density PCBs with finer pitch and smaller form factors.
High-Speed and High-Frequency PCBs
As data rates and operating frequencies increase, PCBs must be designed to handle high-speed signals and minimize signal integrity issues. Advanced materials, such as low-loss dielectrics and high-performance laminates, are being developed to meet these requirements.
Embedded Components
Embedded components, such as resistors, capacitors, and even active components, are being integrated directly into the PCB substrate. This approach saves space, reduces parasitic effects, and improves overall system performance.
3D Printing of PCBs
3D printing technology is being explored for the fabrication of PCBs. Additive manufacturing techniques, such as inkjet printing and aerosol jet printing, enable the creation of complex, three-dimensional PCB Structures with unique geometries and embedded components.
Environmentally Friendly Materials
There is a growing emphasis on the use of environmentally friendly materials in PCB manufacturing. Halogen-free laminates, lead-free solders, and biodegradable materials are being developed to reduce the environmental impact of PCBs and comply with regulatory requirements.
Frequently Asked Questions (FAQ)
-
What is the difference between a PCB and a printed wiring board (PWB)?
A PCB and a PWB are often used interchangeably, but there is a slight difference. A PWB refers to a board with only conductive traces, while a PCB includes both conductive traces and components mounted on the board. -
What is the typical lifespan of a PCB?
The lifespan of a PCB depends on various factors, such as the quality of materials, manufacturing process, operating environment, and usage conditions. Generally, a well-designed and manufactured PCB can last for several years or even decades, depending on the application. -
Can PCBs be recycled?
Yes, PCBs can be recycled. The recycling process involves separating the various materials, such as copper, gold, and plastics, for reuse. However, the recycling of PCBs is a complex process due to the presence of hazardous substances and the need for specialized equipment. -
What is the difference between through-hole and surface mount technology (SMT)?
Through-hole technology involves mounting components with leads that are inserted into holes drilled in the PCB and soldered on the opposite side. SMT, on the other hand, involves mounting components directly onto the surface of the PCB without the need for drilled holes. SMT allows for higher component density and faster assembly compared to through-hole technology. -
What is the role of vias in PCBs?
Vias are conductive pathways that connect different layers of a PCB. They allow electrical signals to travel between layers, enabling more complex routing and higher component density. Vias can be through-hole, blind, or buried, depending on their starting and ending layers.
Conclusion
PCBs have revolutionized the electronics industry, enabling the creation of compact, reliable, and high-performance devices. From their humble beginnings in the early 20th century to their ubiquitous presence in modern electronics, PCBs have undergone significant advancements in design, manufacturing, and materials.
As technology continues to evolve, PCBs will play an increasingly crucial role in shaping the future of electronics. Miniaturization, high-speed requirements, embedded components, 3D printing, and environmentally friendly materials are just a few of the trends driving the development of PCB technology.
Understanding the fundamentals of PCBs, their manufacturing process, types, applications, and future trends is essential for engineers, designers, and enthusiasts in the electronics industry. By staying informed and embracing new advancements, we can unlock the full potential of PCBs and create innovative electronic solutions that push the boundaries of what is possible.
Leave a Reply