Understanding High-Speed Signals
What are High-Speed Signals?
High-speed signals are electrical signals that have a high frequency and fast rise and fall times. These signals are typically used in applications such as high-speed digital interfaces, high-bandwidth analog circuits, and radio frequency (RF) systems. The frequency range for high-speed signals can vary depending on the application, but it generally starts at around 100 MHz and can go up to several gigahertz (GHz).
Signal Integrity Challenges
As signal frequencies increase, several factors can impact signal integrity:
-
Reflections: When a signal encounters an impedance mismatch, a portion of the signal is reflected back to the source, causing signal distortion and reducing the overall signal quality.
-
Crosstalk: Crosstalk occurs when a signal from one trace induces unwanted energy into an adjacent trace, leading to signal interference and potential data corruption.
-
Electromagnetic Interference (EMI): High-speed signals can generate electromagnetic radiation that can interfere with nearby electronic devices or cause the PCB to fail electromagnetic compatibility (EMC) regulations.
-
Attenuation: As signals travel through the PCB traces, they experience attenuation due to losses in the dielectric material and the resistance of the copper traces. This can lead to reduced signal strength and integrity.
High-Speed PCB Design Considerations
To address the challenges associated with high-speed signals, PCB designers must consider several key factors:
Material Selection
The choice of PCB material is critical in High-Speed Design. The dielectric constant (Dk) and dissipation factor (Df) of the material determine the signal propagation speed and losses, respectively. Low-loss materials with stable Dk and Df values over the frequency range of interest are preferred for high-speed applications. Some common high-speed PCB materials include:
- FR-4: A cost-effective and widely used material suitable for frequencies up to about 2 GHz.
- Rogers RO4000 series: A high-performance laminate with low Dk and Df values, suitable for frequencies up to 10 GHz.
- Isola I-Speed: A low-loss material designed for high-speed digital applications up to 25 GHz.
Controlled Impedance
To minimize reflections and ensure proper signal transmission, the characteristic impedance of the PCB traces must be carefully controlled. The target impedance value depends on the application and the components used, but common values include 50Ω for RF systems and 100Ω for differential pairs in high-speed digital interfaces.
To achieve controlled impedance, designers must consider factors such as:
- Trace width and thickness
- Dielectric thickness
- Trace spacing
- Ground plane placement
Specialized PCB Design Software with impedance calculation tools can help designers optimize trace geometries to meet the target impedance.
Signal Routing
Proper signal routing is essential to minimize crosstalk, reflections, and EMI. Some best practices for high-speed signal routing include:
-
Minimize trace length: Shorter traces reduce the opportunity for signal degradation and interference.
-
Avoid sharp corners: Use 45-degree angles or smooth curves instead of 90-degree corners to minimize reflections.
-
Maintain consistent trace spacing: Consistent spacing between traces helps maintain the desired characteristic impedance and reduces crosstalk.
-
Use ground planes: Placing ground planes adjacent to high-speed signals helps maintain a constant impedance and provides shielding against EMI.
-
Implement differential pairs: Use differential signaling for high-speed digital interfaces to minimize EMI and improve noise immunity.
Power Integrity
Maintaining a clean and stable power supply is crucial for high-speed PCBs. Noise and fluctuations in the power supply can impact signal integrity and lead to system malfunction. Some strategies for ensuring power integrity include:
-
Decoupling capacitors: Place decoupling capacitors close to power pins of high-speed components to provide a local, low-impedance power source and filter out high-frequency noise.
-
Power plane segmentation: Divide the power plane into separate regions for analog, digital, and noisy circuits to minimize interference.
-
Minimize power trace inductance: Use wide, short traces for power delivery to reduce inductance and minimize voltage drops.
-
Use power filters: Implement power filters, such as Ferrite Beads or pi-filters, to suppress high-frequency noise on power lines.
Simulation and Verification
Given the complexity of high-speed PCB design, simulation and verification are essential to ensure the design meets performance requirements before fabrication. Several types of simulations can be performed:
-
Signal integrity simulation: Analyze the quality of high-speed signals, including reflections, crosstalk, and eye diagrams, to ensure reliable data transmission.
-
Power integrity simulation: Evaluate the power distribution network’s impedance, voltage drops, and noise levels to ensure a stable power supply for high-speed components.
-
EMI simulation: Assess the PCB’s electromagnetic emissions and susceptibility to ensure compliance with EMC regulations and minimize interference with other electronic devices.
Advanced PCB design software packages often include simulation tools that can help designers identify and resolve issues early in the design process.
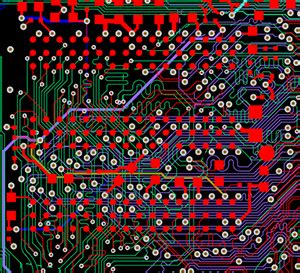
High-Speed PCB Layout Techniques
In addition to the design considerations mentioned above, several layout techniques can help optimize high-speed PCB performance:
Layer Stackup
A well-designed layer stackup is crucial for high-speed PCBs. Some guidelines for an effective high-speed layer stackup include:
-
Use dedicated signal layers: Assign high-speed signals to dedicated layers to minimize interference with other signals and components.
-
Implement ground planes: Place ground planes adjacent to high-speed signal layers to provide a low-impedance return path and minimize EMI.
-
Symmetrical stackup: Use a symmetrical layer stackup to balance copper distribution and minimize warpage during manufacturing.
-
Minimize dielectric thickness: Thinner dielectrics between signal layers and ground planes help reduce signal attenuation and improve impedance control.
Layer | Material | Thickness (mm) | Purpose |
---|---|---|---|
Top | Copper | 0.035 | High-speed signals |
2 | FR-4 | 0.2 | Ground plane |
3 | Copper | 0.035 | Power plane |
4 | FR-4 | 0.2 | Ground plane |
Bottom | Copper | 0.035 | High-speed signals |
Example of a simple 4-layer high-speed PCB stackup
Via Optimization
Vias are essential for connecting signals across different layers of the PCB, but they can also introduce discontinuities and reflections. To minimize the impact of vias on high-speed signals:
-
Minimize via count: Reduce the number of vias in high-speed signal paths to minimize impedance discontinuities and reflections.
-
Use microvias: Smaller-diameter vias, such as microvias, have lower inductance and capacitance, making them better suited for high-speed signals.
-
Implement via shielding: Place ground vias adjacent to high-speed signal vias to provide shielding and reduce crosstalk.
-
Optimize via stubs: Minimize the length of via stubs (unused portions of through-hole vias) to reduce reflections and resonances.
Trace Matching
For high-speed differential pairs and buses, it is essential to match the length and delay of the traces to ensure proper signal timing and minimize skew. Some techniques for trace matching include:
-
Length matching: Adjust the routing of traces to ensure that the length of each trace in a differential pair or bus is equal.
-
Delay matching: In cases where length matching is not possible, add deliberate meandering or serpentine sections to equalize the delay between traces.
-
Phase tuning: Implement phase-tuning techniques, such as adjusting trace widths or using delay lines, to fine-tune the timing of high-speed signals.
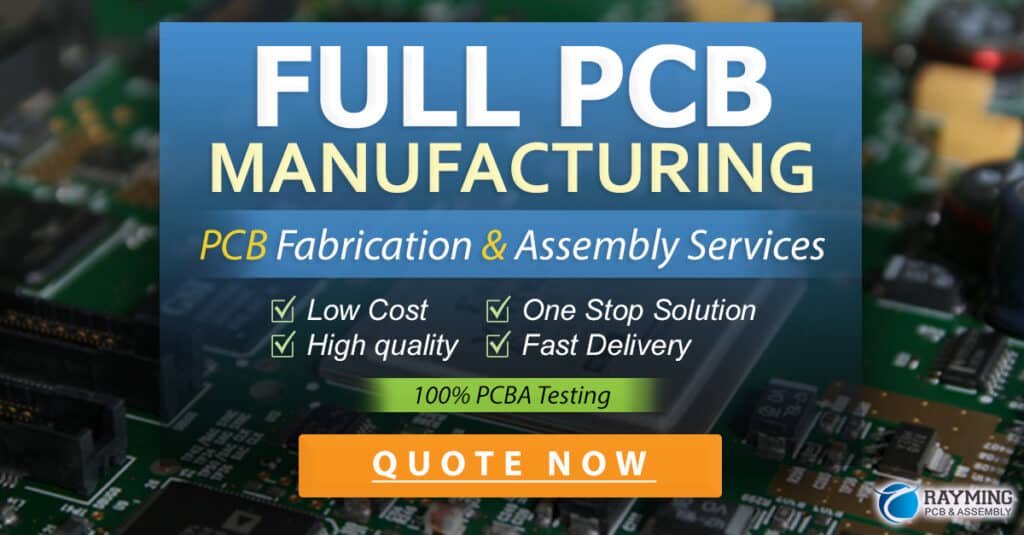
Testing and Validation
After fabrication, high-speed PCBs must undergo rigorous testing and validation to ensure they meet the desired performance criteria. Some common tests for high-speed PCBs include:
-
Time-Domain Reflectometry (TDR): TDR measurements help characterize impedance discontinuities and reflections along a transmission line.
-
Vector Network Analysis (VNA): VNA tests measure the frequency-dependent behavior of the PCB, including S-parameters, insertion loss, and return loss.
-
Eye Diagram Analysis: Eye diagrams provide a visual representation of the quality of a high-speed digital signal, including jitter, noise, and bit error rate.
-
EMI Testing: EMI tests ensure that the PCB complies with relevant electromagnetic compatibility standards and does not interfere with other electronic devices.
By performing these tests and analyzing the results, engineers can identify and address any issues with the high-speed PCB design before the product goes into mass production.
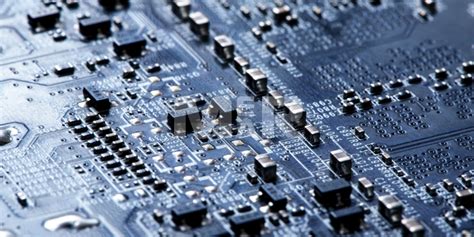
Frequently Asked Questions (FAQ)
-
What is the difference between a high-speed PCB and a standard PCB?
A high-speed PCB is specifically designed to handle high-frequency signals and fast data transmission rates, typically above 100 MHz. In contrast, a standard PCB is designed for lower-frequency applications and may not have the same level of signal integrity and power integrity considerations as a high-speed PCB. -
What are the most common challenges in high-speed PCB design?
The most common challenges in high-speed PCB design include maintaining signal integrity, minimizing crosstalk and EMI, ensuring proper impedance control, and maintaining power integrity. These challenges arise due to the high frequencies and fast rise and fall times of the signals, which can lead to reflections, interference, and signal degradation. -
What materials are best suited for high-speed PCBs?
Materials with low dielectric constant (Dk) and dissipation factor (Df) values are preferred for high-speed PCBs. These materials help minimize signal attenuation and maintain stable impedance over the desired frequency range. Some common high-speed PCB materials include FR-4 (for frequencies up to 2 GHz), Rogers RO4000 series (up to 10 GHz), and Isola I-Speed (up to 25 GHz). -
Why is simulation important in high-speed PCB design?
Simulation is crucial in high-speed PCB design because it allows designers to analyze the performance of the PCB before fabrication. Signal integrity simulations help assess the quality of high-speed signals, while power integrity simulations evaluate the stability of the power distribution network. EMI simulations ensure that the PCB complies with electromagnetic compatibility regulations. By identifying and resolving issues early in the design process, simulations can save time and cost in the long run. -
What testing methods are used to validate high-speed PCB designs?
Common testing methods for high-speed PCBs include Time-Domain Reflectometry (TDR) to characterize impedance discontinuities, Vector Network Analysis (VNA) to measure frequency-dependent behavior, Eye Diagram Analysis to assess the quality of high-speed digital signals, and EMI Testing to ensure compliance with electromagnetic compatibility standards. These tests help validate the performance of the high-speed PCB and identify any issues that need to be addressed before mass production.
In conclusion, high-speed PCB design is a complex and challenging field that requires careful consideration of signal integrity, power integrity, and electromagnetic compatibility. By understanding the unique characteristics of high-speed signals, selecting appropriate materials, implementing proper layout techniques, and conducting thorough simulations and testing, designers can create high-performance PCBs that meet the demands of today’s advanced electronic systems. As technology continues to evolve, the importance of high-speed PCB design will only grow, making it an essential skill for electronics engineers in the future.
Leave a Reply