What is a PCB?
A Printed Circuit Board (PCB) is a flat board made of insulating material with electrical connections etched or printed on its surface. PCBs are used to mechanically support and electrically connect electronic components using conductive pathways, tracks or signal traces.
PCBs are the foundation of almost all modern electronic devices. They are found in everything from simple one-transistor circuits to complex computer motherboards and smartphone logic boards. PCBs allow for electronics to be made much smaller, faster, and more reliable compared to older point-to-point wiring methods.
Types of PCBs
There are three main types of PCBs:
Type | Layers | Applications |
---|---|---|
Single-layer | One conductive layer, usually copper | Simple circuits, low-cost devices |
Double-layer | Two conductive layers separated by an insulating layer | Most common, used in a wide range of devices |
Multi-layer | Three or more conductive layers separated by insulating layers | Complex devices requiring high component density |
Other specialized PCB types include:
- Flexible PCBs: Made with flexible insulating material to fit in tight spaces
- Rigid-Flex PCBs: Combines rigid and flexible sections for unique packaging requirements
- High Frequency PCBs: Designed for high frequency signals with controlled impedance
- Metal Core PCBs: Uses a metal core for enhanced heat dissipation
PCB Design Workflow
The PCB design process typically follows these steps:
-
Schematic Capture: The circuit is drawn as a schematic diagram using EDA (Electronic Design Automation) software. The schematic defines the electrical connections between components.
-
Component Placement: Components are arranged on the board outline in the EDA software, taking into account factors like signal integrity, EMI, heat dissipation, and manufacturing constraints.
-
Routing: The connections between components are routed on the various layers of the board according to design rules. The goal is to complete all required connections while minimizing signal integrity issues and manufacturing challenges.
-
Design Rule Check (DRC): The completed layout is checked against a set of design rules to verify spacing, trace width, and other requirements are met. Errors must be corrected before proceeding.
-
Output Generation: The design files are output in industry standard formats like Gerber and drill files for fabrication, assembly drawings, and bill of materials.
-
Fabrication: The finished design is sent to a PCB manufacturer who will produce the physical boards.
-
Assembly and Test: The fabricated boards are populated with components and tested to verify functionality.
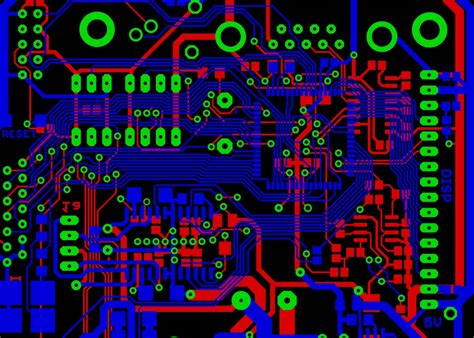
Key PCB Design Considerations
Numerous factors must be considered when designing a PCB to ensure proper functionality, reliability, and manufacturability:
Schematic Design
- Selecting the right components for the application
- Ensuring proper connectivity and pinouts
- Power delivery and decoupling
- Signal integrity for sensitive circuits
- Testability requirements
Physical Layout
- Board size and layer count targets
- Component placement for routing, heat dissipation, and assembly
- Routing signals on appropriate layers
- Length and impedance matching for critical signals
- Proper grounding and avoiding ground loops
- Power planes for low impedance power delivery
- Keep out areas for mechanical constraints
- Manufacturing capabilities and design rules
Signal Integrity
Signal integrity refers to the quality of electrical signals as they travel through the interconnects on a PCB. The goal is to ensure signals arrive at their destination pins undistorted and at the correct time. Major signal integrity considerations include:
-
Reflections: Occur when signals encounter an impedance mismatch along the transmission path. Can cause ringing, overshoot, and undershoot which distorts the signal shape. Proper terminations and controlling trace impedance are used to minimize reflections.
-
Crosstalk: Occurs when signals on adjacent traces induce unwanted voltages onto each other due to electromagnetic coupling. Can cause logic errors in digital circuits and noise in analog circuits. Proper spacing, orthogonal routing on adjacent layers, and differential signaling help combat crosstalk.
-
Timing Issues: Signals must arrive at their destination at the specified times for synchronous circuits to operate correctly. Trace length matching, delay tuning, and phase control are used to ensure proper timing.
Electromagnetic Compatibility (EMC)
EMC ensures the PCB does not radiate or conduct excessive electromagnetic interference (EMI) and is not susceptible to external EMI sources. Key EMC methods include:
- Minimizing current loop areas to reduce radiated emissions
- Proper grounding and shielding to contain electric and magnetic fields
- Filtering to attenuate conducted emissions
- Transient suppression to protect against ESD and voltage spikes
Thermal Management
Proper thermal management is critical to ensure components operate within acceptable temperature ranges. Methods to control temperature rise in a PCB include:
- Placing hot components near board edges or away from thermally sensitive devices
- Providing adequate copper area for heat sinking
- Using thermal vias to conduct heat to inner planes or opposite side
- Selecting a PCB substrate material with suitable thermal properties
- Incorporating heatsinks, fans, or other active cooling methods
Design for Manufacturing (DFM)
DFM ensures the board can be fabricated and assembled reliably and cost-effectively by considering the capabilities and limitations of the manufacturing processes. Key aspects include:
- Adhering to the manufacturer’s design rules for minimum pitch, spacing, and hole sizes
- Providing sufficient space for assembly machines to place and solder components
- Minimizing the use of vias and controlling aspect ratios
- Avoiding acid traps and designing for proper etching
- Specifying appropriate surface finishes and solder mask
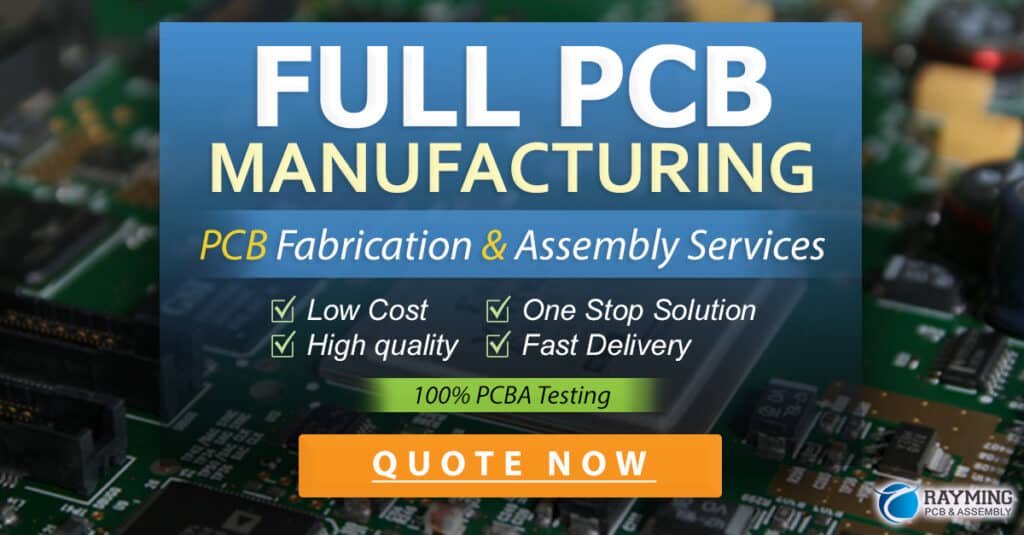
PCB Design Software
EDA software is used to create schematics, perform simulations, and design the physical PCB layout. Major PCB design software packages include:
Software | Vendor | Key Features |
---|---|---|
Altium Designer | Altium | Schematic, layout, routing, simulation, MCAD integration |
OrCAD / Allegro | Cadence | Schematic, analog simulation, constraint-driven PCB layout |
EAGLE | Autodesk | Schematic, layout, autorouter for simple boards |
KiCad | Open Source | Schematic, layout, SPICE Simulation, 3D viewer |
These packages offer schematic capture, component libraries, automatic and interactive routing, design rule checking, and output file generation. More advanced tools integrate with mechanical CAD, support signal and power integrity simulation, and automate complex constraints.
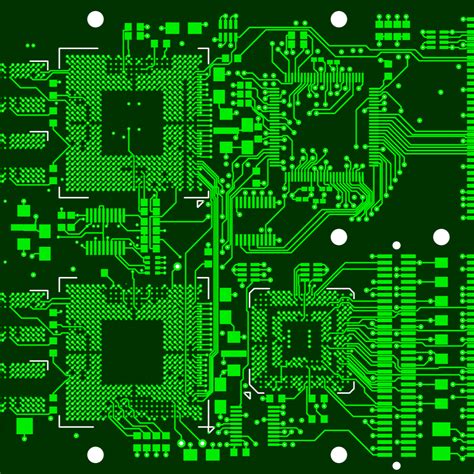
Frequently Asked Questions
What is the difference between a PCB and a breadboard?
A breadboard is a temporary prototyping tool for creating circuits without soldering. Components are plugged into the breadboard’s holes which are internally connected by strips of metal. PCBs are permanent and designed to be manufactured with copper traces providing the electrical connectivity.
How much does it cost to design and manufacture a PCB?
The cost of PCB design depends on the complexity of the circuit, the hourly rate of the engineer, and any specialized software or tools required. Simple designs may only be a few hundred dollars while complex boards can cost tens of thousands in engineering time.
PCB Fabrication and assembly costs depend on the number of layers, board size, materials, surface finish, and quantity. Setup fees can range from $200-$1000 and per board costs are typically $1-$20 depending on complexity and quantity. Very simple 2-layer boards may cost under $1 each in volume while complex multilayer boards with tight tolerances and specialty materials can exceed $100 each.
What are the most common PCB assembly methods?
The two primary PCB assembly methods are through-hole and surface mount.
Through-hole mounting involves inserting component leads through drilled holes in the board and soldering them to pads on the opposite side. This older method is used for large components, connectors, and in high-reliability applications but is more expensive than SMT.
Surface mount technology (SMT) mounts components directly to pads on the surface of the board. Components are smaller, boards can be more densely populated, and assembly can be automated making SMT the dominant method today. The main disadvantages are smaller parts can be difficult to hand solder and rework.
What are vias and why are they used?
Vias are copper plated holes drilled in a PCB to route a signal from one layer to another. They allow the circuit to span multiple layers with electrical connections between layers. There are several types of vias:
- Through vias spanning the entire board from top to bottom
- Blind vias connecting an outer layer to an inner layer
- Buried vias connecting two inner layers with no connection to the outer layers
Vias are essential for routing flexibility but they do add cost and potential reliability issues so designers try to minimize their use, especially blind and buried vias. Microvias are very small diameter vias which minimize the area impact and are used for high-density interconnect (HDI) PCB designs.
What is the most challenging part of the PCB design process?
The most challenging aspects of PCB design depend on the application but some common difficulties include:
- Managing signal integrity for High-Speed Designs
- Routing dense BGA and connector breakouts with high pin counts
- Fitting the required circuitry in the allocated space
- Achieving the target cost while meeting performance and reliability goals
- Keeping up with changing requirements throughout the design cycle
Following good design practices, planning ahead for the most constrained areas, and leveraging the EDA software’s automation capabilities are important to overcoming these challenges. Open communication with the whole development team and PCB manufacturers is also critical for success.
Leave a Reply