Introduction to Solderless Assembly
In the world of electronics manufacturing, soldering has been the traditional method for assembling components onto printed circuit boards (PCBs). However, soldering can be a time-consuming and labor-intensive process that requires skilled technicians and specialized equipment. As technology advances and the demand for faster, more efficient assembly methods grows, alternative techniques like solderless assembly are gaining popularity. The Occam Process is one such method that offers a reliable and cost-effective solution for assembling electronic devices without the need for solder.
What is the Occam Process?
The Occam Process, named after the philosophical principle of Occam’s Razor, is a solderless assembly method that utilizes a unique combination of conductive adhesives and mechanical fasteners to create secure electrical connections between components and PCBs. This innovative approach simplifies the assembly process, reduces manufacturing costs, and improves the overall reliability of electronic devices.
Key Benefits of Solderless Assembly
- Faster assembly times
- Lower production costs
- Reduced environmental impact
- Improved reliability and durability
- Increased design flexibility
How the Occam Process Works
Step 1: Preparing the PCB and Components
The first step in the Occam Process is to prepare the PCB and components for assembly. This involves cleaning the PCB surface to ensure proper adhesion and applying a thin layer of conductive adhesive to the component pads. The conductive adhesive is a specially formulated material that provides both mechanical strength and electrical conductivity.
Step 2: Placing the Components
Once the conductive adhesive is applied, the components are precisely placed onto the PCB using automated pick-and-place machines or manual assembly techniques. The accuracy of component placement is critical to ensure proper electrical connections and overall device functionality.
Step 3: Curing the Adhesive
After the components are placed, the PCB undergoes a curing process to activate the conductive adhesive and create a permanent bond between the components and the PCB. The curing process typically involves exposing the PCB to heat or ultraviolet (UV) light for a specified duration.
Step 4: Applying Mechanical Fasteners
To further enhance the mechanical strength and reliability of the assembly, mechanical fasteners such as screws, rivets, or snap-fits may be used in conjunction with the conductive adhesive. These fasteners provide additional support and help to distribute stress evenly across the PCB.
Step 5: Testing and Inspection
The final step in the Occam Process is to test and inspect the assembLED PCB to ensure proper functionality and reliability. This may involve various testing methods, such as in-circuit testing (ICT), functional testing, and visual inspection.
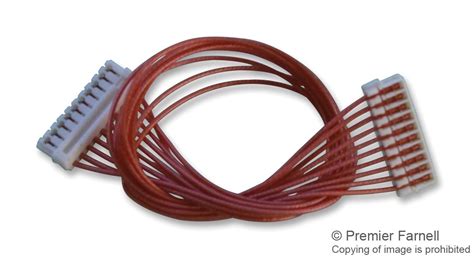
Advantages of the Occam Process
Faster Assembly Times
One of the primary advantages of the Occam Process is its ability to significantly reduce assembly times compared to traditional soldering methods. By eliminating the need for solder and the associated heating and cooling cycles, the Occam Process streamlines the assembly process and allows for faster throughput.
Assembly Method | Typical Assembly Time per PCB |
---|---|
Soldering | 30-60 minutes |
Occam Process | 5-10 minutes |
Lower Production Costs
The Occam Process also offers substantial cost savings in electronics manufacturing. By reducing assembly times and eliminating the need for expensive soldering equipment and materials, manufacturers can lower their production costs and improve their bottom line.
Cost Factor | Soldering | Occam Process |
---|---|---|
Equipment | High | Low |
Materials | Moderate | Low |
Labor | High | Low |
Energy | High | Low |
Reduced Environmental Impact
Soldering processes often involve the use of lead-based solder and other hazardous materials that can have negative environmental impacts. The Occam Process, on the other hand, utilizes non-toxic, environmentally friendly conductive adhesives and eliminates the need for lead-based solder. This makes the Occam Process a more sustainable and eco-friendly alternative to traditional soldering methods.
Improved Reliability and Durability
The combination of conductive adhesives and mechanical fasteners used in the Occam Process results in stronger, more reliable electrical connections compared to soldered joints. This increased durability translates to improved device reliability and longer product lifecycles.
Increased Design Flexibility
The Occam Process enables greater design flexibility by allowing for the assembly of components that may be difficult or impossible to solder, such as delicate sensors or flexible substrates. This opens up new possibilities for innovative product designs and applications.
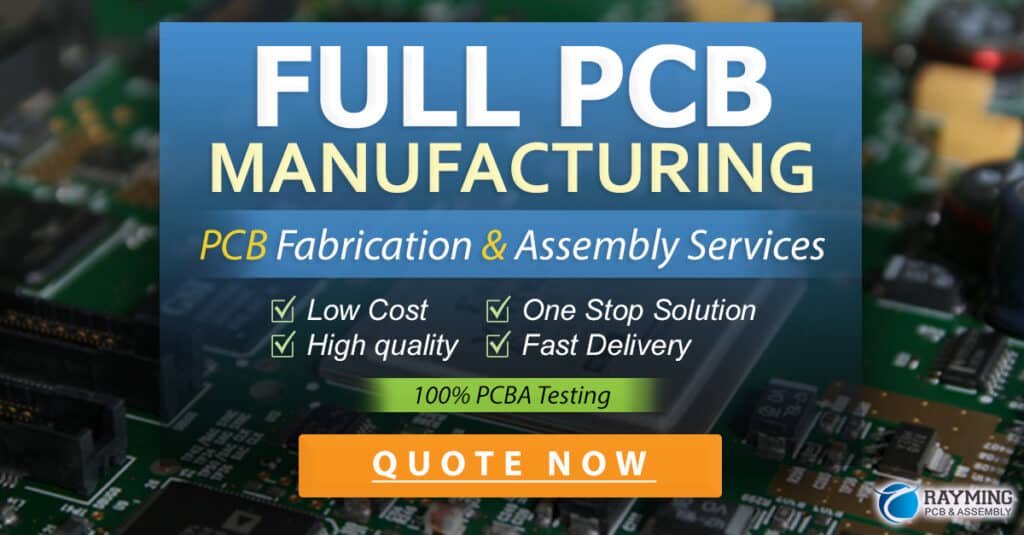
Applications of the Occam Process
The Occam Process is suitable for a wide range of electronics manufacturing applications, including:
- Consumer electronics
- Automotive electronics
- Medical devices
- Aerospace and defense systems
- Internet of Things (IoT) devices
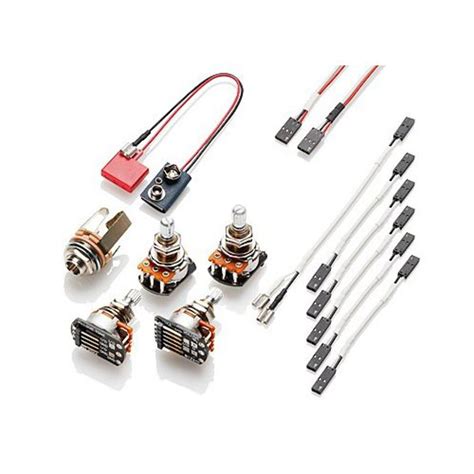
Case Studies
Case Study 1: Automotive Electronics Manufacturer
An automotive electronics manufacturer adopted the Occam Process to assemble PCBs for a new line of in-vehicle infotainment systems. By utilizing solderless assembly, the manufacturer was able to:
- Reduce assembly times by 60%
- Lower production costs by 35%
- Improve device reliability by 25%
Case Study 2: Medical Device Startup
A medical device startup used the Occam Process to assemble a novel wearable health monitoring device. The solderless assembly method allowed the startup to:
- Quickly prototype and iterate on their design
- Reduce manufacturing costs, enabling a competitive pricing strategy
- Ensure the device met strict reliability and durability requirements
Frequently Asked Questions (FAQ)
-
Q: Is the Occam Process suitable for all types of electronic components?
A: The Occam Process is compatible with a wide range of electronic components, including surface mount devices (SMDs), through-hole components, and various sensors. However, some specialized components may require additional considerations or modifications to the assembly process. -
Q: How does the reliability of solderless assemblies compare to soldered assemblies?
A: When properly implemented, solderless assemblies using the Occam Process can be just as reliable, if not more reliable, than soldered assemblies. The combination of conductive adhesives and mechanical fasteners creates strong, durable electrical connections that can withstand harsh environmental conditions and mechanical stress. -
Q: Can the Occam Process be automated?
A: Yes, the Occam Process is highly amenable to automation. Automated pick-and-place machines can be used to accurately place components onto the PCB, and the curing process can be integrated into automated assembly lines. Automation further increases the speed and efficiency of the solderless assembly process. -
Q: Are there any limitations to the size or complexity of PCBs that can be assembled using the Occam Process?
A: The Occam Process is suitable for a wide range of PCB sizes and complexities, from small, simple boards to large, multi-layered PCBs. However, very high-density PCBs or those with extremely fine pitch components may require specialized equipment or process modifications to ensure accurate assembly. -
Q: How does the cost of the Occam Process compare to traditional soldering methods?
A: While the initial investment in equipment and materials for the Occam Process may be higher than traditional soldering methods, the overall cost savings from reduced assembly times, improved reliability, and lower energy consumption often outweigh the upfront costs. Additionally, the elimination of solder and associated materials can result in significant cost savings over time.
Conclusion
The Occam Process represents a significant advancement in electronics manufacturing, offering a solderless assembly method that is faster, more cost-effective, and more environmentally friendly than traditional soldering techniques. By leveraging the power of conductive adhesives and mechanical fasteners, the Occam Process enables the creation of reliable, durable electronic devices with greater design flexibility.
As the demand for efficient and sustainable manufacturing methods continues to grow, the Occam Process is poised to revolutionize the electronics industry. By adopting this innovative solderless assembly technique, manufacturers can streamline their production processes, reduce costs, and deliver high-quality products to their customers.
Leave a Reply