Understanding PCB Lead Times and Risk Factors
Printed circuit board (PCB) manufacturing is a complex process with many steps, from design and prototyping to fabrication, assembly, and testing. The total time it takes from ordering a PCB to receiving the finished product is known as the lead time.
PCB lead times can vary significantly depending on a number of factors. Some of the key variables that impact lead times include:
- PCB complexity (number of layers, materials, features)
- Order quantity
- Manufacturing capacity and demand
- Component availability
- Quality control and testing requirements
- Shipping method
Delays or extended lead times can occur when issues arise related to any of these factors. For companies that rely on PCBs for their products, mitigating the risks of long lead times is critical to avoid production delays, increased costs, and customer dissatisfaction.
Common Causes of Extended PCB Lead Times
There are several common issues that can result in longer than expected PCB manufacturing lead times:
-
Design issues – Problems with the PCB design data or files provided by the customer can cause delays. This includes incorrect or incomplete data, incompatible file formats, design rule violations, etc.
-
Part sourcing delays – Difficulty procuring the necessary components and materials can extend lead times, especially for PCBs with specialized components that have limited availability or long manufacturer lead times.
-
Fabrication issues – PCB fab houses can encounter equipment malfunctions, material defects, capacity constraints, or quality control problems that slow down production. More complex PCB designs are also more prone to fabrication issues.
-
Shipping delays – Disruptions to global shipping and logistics networks due to things like natural disasters, labor shortages, or customs issues can result in longer transport times. Relying on slower shipping methods to save costs can also add days or weeks.
While some of these risk factors may be outside your direct control, there are proactive steps you can take to minimize delays. Effective supply chain management, design optimization, clear communication, and supplier diversification are all strategies to help reduce the chances of extended PCB lead times.
Analyzing Your PCB Supply Chain
To start mitigating the risks of PCB lead time disruptions, it’s important to fully understand your current supply chain. Map out the entire PCB pipeline from design creation to the moment the finished boards arrive at your facility. This should include:
- Design service providers
- Component suppliers and distributors
- Bare board fabrication partners
- PCB assembly providers
- Any intermediaries (brokers, agents, logistics providers, etc.)
For each partner or supplier in the chain, gather data on their typical lead times, order capacities, communication and data exchange processes, and historical performance. Identify any potential bottlenecks or single points of failure.
Finding Weak Links in the Supply Chain
As you analyze your PCB supply chain, look out for weak links that could be particularly vulnerable to disruptions. These may include:
- Suppliers with poor on-time delivery rates
- Fabrication partners running at very high capacity utilization
- Component suppliers with a history of part shortages or obsolescence issues
- Logistics providers relying on frequently congested ports or trade lanes
Aim to quantify the impact that a disruption to each of these links could have on your lead times and overall production. A simple risk assessment matrix can help visualize this:
Supply Chain Area | Probability of Disruption | Impact of Disruption | Risk Level |
---|---|---|---|
PCB Design | Low | High | Medium |
Part Procurement | Medium | High | High |
Fabrication | Low | Medium | Low |
Assembly | Medium | Medium | Medium |
Shipping/Logistics | High | High | High |
This basic analysis highlights part procurement and shipping as two high risk areas to focus on. Your supply chain assessment may reveal different priorities depending on your specific partners and processes. The key is to identify the most significant potential disruption points.
Strengthening Supply Chain Resilience
With a clear picture of where your biggest lead time risks lie, you can take targeted steps to reinforce your supply chain.
Some options to consider:
-
Diversify suppliers – Avoid relying on a single supplier for critical components or services. Having alternate sources in different regions builds in redundancy.
-
Establish long-term agreements – Negotiate contracts with suppliers that include lead time guarantees and give you priority in the event of capacity constraints.
-
Improve forecasting – Share forecasts with all supply chain partners as early as possible. Use historical data to anticipate demand spikes or seasonality.
-
Build up inventory – While “just in time” inventory management is ideal, strategically accumulating extra stock of critical long lead time parts can provide a buffer.
-
Monitor supplier performance – Regularly collect data on lead times, quality, and communication from all PCB supply chain partners. Quickly address any negative trends before they cause major issues.
Investing time and resources into supply chain resilience efforts can pay off in smoother, more consistent PCB lead times. It’s an ongoing process that requires continuous monitoring and adjustment as market conditions change.
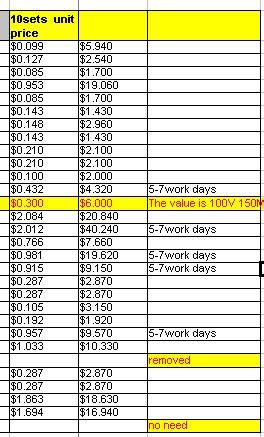
Optimizing PCB Design for Manufacturing
PCB lead times don’t just depend on your suppliers – the design of the board itself can have a major impact. Decisions made during the design phase, from material and component selection to physical layout, directly affect the ease and speed of manufacturing.
Design for Manufacturability Best Practices
To avoid PCB design-related delays, follow these design for manufacturability (DFM) principles:
-
Adhere to fab house capabilities – Understand the equipment and process limitations of your fabrication partner. Avoid pushing the boundaries on minimum trace widths, spacing, or drill sizes.
-
Use standard specifications – Whenever possible, design PCBs using conventional materials, thicknesses, and surface finishes. Specialized materials or processes often have longer lead times.
-
Minimize unique parts – Select components that are widely available and have multiple manufacturer options. Custom or niche components are more likely to have long lead times or supply shortages.
-
Provide comprehensive documentation – Include complete bills of materials (BOMs), assembly drawings, and Gerber files. Clearly communicate any special requirements and make sure all design data uses standard file formats.
-
Plan for test and inspection – Design in test points, fiducials, and other features that streamline the quality control process. This helps minimize delays due to inspection failures or rework.
Applying DFM best practices consistently can have a significant impact on lead times. One case study found that a company was able to reduce their average PCB lead time from 4 weeks to 2 weeks by implementing a robust DFM review process and design guidelines.
The Benefits of Design Standardization
Another way to leverage design to compress lead times is through standardization. Creating a library of proven, reusable design blocks that can be dropped into multiple projects saves time in both design and manufacturing.
Standardized designs typically use a well-defined set of materials, layer stackups, components, and layout rules. This familiarity helps streamline quoting, sourcing, and fabrication as the manufacturing process is repeated.
Standardization also makes it easier to pre-order and stock common raw materials and parts. If multiple PCB designs all use the same base materials and components, you can place bulk orders in advance knowing that the inventory will be used. This inventory buffer helps protect against future supply shortages causing delays.
Design Approach | Average Lead Time | Benefits | Drawbacks |
---|---|---|---|
Custom per project | 4-6 weeks | Maximum design flexibility | Higher risk of delays and supply issues |
Partial standardization | 3-4 weeks | Good balance of flexibility and predictability | Requires upfront effort to define standards |
Full standardization | 2-3 weeks | Fastest, most predictable lead times | Limited design options, upfront investment |
The level of standardization that makes sense depends on your product mix and design needs. But most organizations can benefit from at least some level of design reuse and commonization to make lead times more consistent.
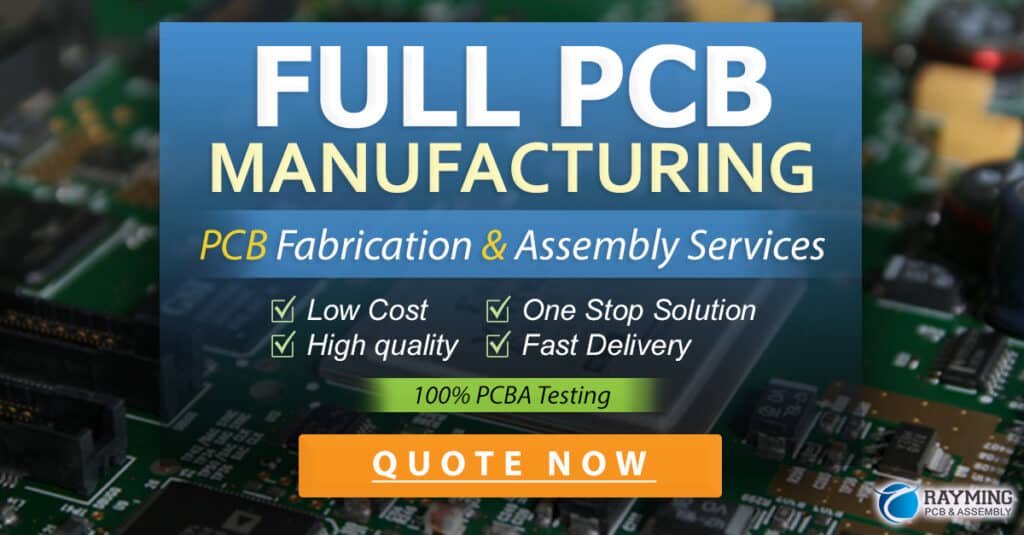
Managing the PCB Ordering Process
The way you manage the actual ordering process for PCBs can also have an impact on lead times. Effective communication, clear documentation, and smart order management all help avoid delays and keep your PCB pipeline running smoothly.
Keys to Effective PCB Ordering
Here are some best practices to follow when placing PCB orders:
-
Request multiple quotes – Get quotes from at least 3-4 different suppliers to compare lead times, pricing, and capabilities. Don’t just focus on the cheapest option.
-
Provide complete data packages – Include all necessary design files, BOMs, drawings, and special instructions in the RFQ package. Make sure data is provided in the formats requested by each supplier.
-
Specify all requirements upfront – Clearly communicate any special needs related to materials, surface finishes, tolerances, testing, or shipping. Getting all requirements agreed upon before placing the order avoids mid-stream changes.
-
Allow reasonable production time – Understand each supplier’s standard lead time for the type of PCB you are ordering. Add some buffer to the delivery date to account for potential delays. Rushed orders are more prone to quality issues.
-
Track order status proactively – Request regular order status updates from your supplier at predefined milestones. Address any issues as soon as they are identified rather than waiting until the delivery deadline.
Following a comprehensive PCB ordering checklist helps ensure that you aren’t contributing to delays through incomplete data or poor communication. It also makes it easier to hold suppliers accountable for meeting their promised lead times.
Leveraging Supplier Certifications and Capabilities
PCB supplier certifications and special capabilities can also be a factor in lead times. Depending on your industry and product requirements, you may need PCBs that comply with certain quality standards or regulations:
- ISO 9001
- IATF 16949 (automotive)
- AS9100D (aerospace)
- IPC class 2 or 3
- UL listing
- RoHS
Suppliers with the appropriate certifications already have the processes and controls in place to efficiently produce compliant PCBs. If you work with a non-certified supplier, they may need extra time to implement special processes or source compliant materials.
Certain PCB features or specifications may also require specialized supplier capabilities:
- HDI or microvias
- Flex or rigid-flex
- Heavy copper
- RF materials
- Embedded components
If your design uses these non-standard technologies, seek out suppliers with a proven track record in that capability. They will be better equipped to estimate accurate lead times and deliver on schedule.

Resolving Lead Time Disruptions
Even with robust supplier management and design practices, disruptions can still happen. When faced with a sudden delay or shortage, quick action is needed to get your PCB pipeline back on track.
Responding to Supply Shortages
When a component or raw material shortage threatens to derail production, consider these options:
-
Authorize alternate parts – If your supplier recommends a substitute component, promptly review and approve the change if it meets requirements. The faster you sign off, the sooner they can procure the new part.
-
Expedite shipping – If a part is available but has a long transport time, see if paying for expedited shipping can make up time overall. Compare the expedite fees to the potential cost of production delays.
-
Split the order – If the full part quantity isn’t immediately available, ask the supplier to process a partial shipment to begin production. Remaining parts can be sent later and the final boards shipped as soon as the order is complete.
In some cases, redesigning the PCB to use a different component may be necessary. While this adds upfront time, it can pay off in faster production and a more stable supply.
Accelerating Fabrication and Assembly
If a PCB Fabrication or assembly delay arises, work closely with your supplier to explore acceleration options:
- Authorize overtime or extra shifts to make up production time
- Discuss which production steps can be streamlined or run in parallel
- Offer to assist with any testing, inspection, or QA tasks that can be done in-house
- Explore alternate manufacturing partners that may have more capacity
Collaborative problem-solving is key. Maintaining open lines of communication and working together to find creative solutions maximizes the chances of making up lost time.
Future-Proofing Your PCB Lead Times
As technology and market conditions continuously evolve, strategies for maintaining quick, reliable PCB lead times must also adapt. Taking a proactive, forward-looking approach to PCB supply chain management helps you stay ahead of potential lead time obstacles.
Investing in Supply Chain Visibility
End-to-end supply chain visibility is becoming increasingly important to identify lead time risks early. Aim to build a centralized, real-time view of:
- Supplier inventory levels and production schedules
- Inbound and outbound order tracking
- Manufacturing status of all in-production orders
- Key component lead times and availability
Cloud-based supply chain management platforms make it possible to integrate data streams from multiple systems and partners. Artificial intelligence and predictive analytics tools can further enhance visibility by flagging potential issues and recommending solutions.
While there is an upfront investment required to implement these systems, the long-term value can be significant. One recent study found that companies with advanced supply chain visibility averaged 15% shorter lead times compared to their less-mature peers.
Embracing Agile Manufacturing Practices
Applying agile methodologies to your PCB design and manufacturing processes can also help compress lead times. Key principles of agile manufacturing include:
- Modular product architectures that enable design flexibility
- Small batch sizes and frequent production runs
- Rapid prototyping and iteration
- Cross-functional teams that can quickly pivot as needed
For PCB manufacturing, an agile approach could involve practices like:
- Designing modular PCB platforms that can be easily customized
- Keeping some partially assembLED PCBs in stock for quick final customization
- Implementing a kanban system with suppliers to enable small, frequent deliveries
- Forming integrated project teams with key suppliers for seamless collaboration
The transition to agile manufacturing requires a significant mindset shift and upfront planning. But the resulting flexibility and responsiveness can be a major advantage in hitting aggressive lead time targets.
Staying Ahead of Component End-of-Life
A major driver of future component shortages and lead time spikes is the inevitable end-of-life (EOL) of older parts. PCB designers need to be proactive in identifying components nearing obsolescence and planning for their replacement.
Some strategies to stay ahead of EOL disruptions:
- Partner with component suppliers and distributors that offer product lifecycle management (PLM) services and share EOL data proactively
- Set up automated notifications for EOL announcements on key components
- Design in alternate or second-source components from the beginning
- Consider redesigning PCBs to use newer, more readily available components before EOL
Waiting until the last minute to address EOL components leaves you at the mercy of the spot market and shortens the window to redesign and requalify replacement parts. Proactive lifecycle management helps you make the transition smoothly and avoid panic-driven shortages or redesigns.
Conclusion
Maintaining quick, consistent PCB lead times requires a multifaceted approach that addresses potential risks and bottlenecks at every stage of the process. From initial design decisions to supplier selection and order management, opportunities exist to streamline processes and build in resilience.
Some of the most impactful strategies to mitigate PCB lead time risks include:
- Thoroughly mapping and monitoring your PCB supply chain
- Applying DFM principles and standardizing designs as much as possible
- Carefully selecting and pre-qualifying multiple suppliers for each component and service
- Maintaining open lines of communication and collaboration with all supply chain partners
- Leveraging technology for real-time supply chain visibility
- Proactively planning for component EOL and other lifecycle disruptions
Ultimately, compressing PCB lead times is an ongoing journey that requires continuous improvement and adaptation as new challenges arise. But organizations that prioritize lead time optimization and risk mitigation will be well-positioned to keep their production lines running smoothly in the face of any obstacle.
Frequently Asked Questions
- How long does it typically take to receive a PCB order?
Standard lead times for PCB orders vary based on board complexity, manufacturing partner, and order quantity. Simple 2-layer boards in small volumes may have lead times as short as 5-7 days, while complex multi-layer boards in higher volumes are more likely to be in the 3-4 week range. However, many factors can affect these estimates.
- What are the biggest factors that impact PCB lead times?
Some of the top factors that influence PCB lead times include:
- Number of layers and overall board complexity
- Special material or component requirements
- Selected surface finish, via type, and other specifications
- Fabrication partner capacity and capability
- Component availability and lead times
- Testing and inspection requirements
The specific impact of each factor varies by project, but in general more complex PCBs with non-standard requirements are at higher risk for longer lead times.
- How can I speed up my PCB order?
There are a few options to compress PCB manufacturing lead times:
- Select a domestic or local fabrication partner instead of offshoring
- Choose standard materials and specifications when possible
- Pay expedite fees for faster processing and shipping
- Provide complete, accurate design data packages to your supplier
- Proactively communicate and quickly answer any questions from your supplier
In many cases, faster lead times do come with a cost premium. It’s important to balance your need for speed with your budget constraints.
- What should I do if a component shortage is delaying my PCB order?
When faced with a component shortage, take these steps:
1
Leave a Reply