Introduction to PCB-DFA
Design for Assembly (DFA) is a crucial aspect of Printed Circuit Board (PCB) design that focuses on optimizing the assembly process to improve efficiency, reduce costs, and minimize errors. By following DFA guidelines, designers can create PCBs that are easier to manufacture, assemble, and test, ultimately leading to a more reliable and cost-effective product. In this article, we will explore the key principles of PCB-DFA and provide practical guidelines for implementing them in your PCB design process.
The Importance of PCB-DFA
Reduced Assembly Time and Costs
One of the primary benefits of incorporating DFA principles into your PCB design is the reduction of assembly time and costs. By designing PCBs that are easier to assemble, you can minimize the time required for manual labor, reduce the need for specialized equipment, and streamline the overall production process. This, in turn, leads to lower manufacturing costs and faster time-to-market for your products.
Improved Product Quality and Reliability
PCB-DFA guidelines also contribute to improved product quality and reliability. By designing PCBs that are less prone to assembly errors, you can minimize the risk of defects and malfunctions in the final product. Additionally, DFA principles often promote the use of standardized components and simplified designs, which can further enhance the reliability and longevity of your PCBs.
Enhanced Collaboration and Communication
Implementing DFA guidelines requires close collaboration between PCB designers, manufacturing engineers, and other stakeholders involved in the product development process. This collaboration fosters better communication, knowledge sharing, and problem-solving, ultimately leading to a more efficient and effective design process.
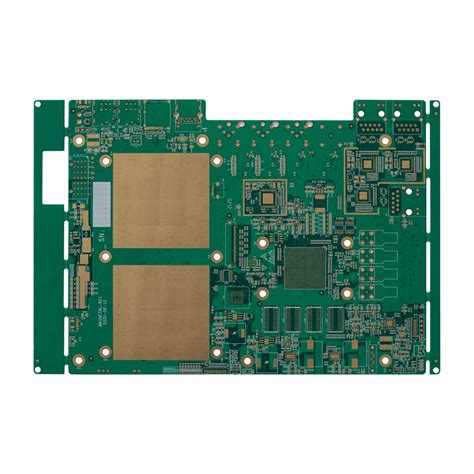
Key Principles of PCB-DFA
Simplicity and Standardization
One of the core principles of PCB-DFA is simplicity and standardization. By using standardized components, minimizing the number of unique parts, and simplifying the overall design, you can reduce the complexity of the assembly process and minimize the potential for errors. This approach also makes it easier to source components, maintain inventory, and troubleshoot issues that may arise during production.
Accessibility and Orientation
Accessibility and orientation are critical factors in PCB-DFA. Components should be placed in a manner that allows for easy access during the assembly process, with sufficient clearance for automated pick-and-place machines or manual soldering. Additionally, components should be oriented consistently to minimize the need for manual adjustments and reduce the risk of assembly errors.
Minimizing Manual Processes
PCB-DFA guidelines emphasize the importance of minimizing manual processes in favor of automated assembly techniques. By designing PCBs that are compatible with automated pick-and-place machines, solder paste application, and reflow soldering processes, you can improve the speed, accuracy, and consistency of the assembly process. This not only reduces the risk of human error but also enables higher production volumes and faster throughput.
Design for Testability
Design for Testability (DFT) is an essential aspect of PCB-DFA. By incorporating testability features into your PCB design, you can facilitate efficient testing and debugging during the manufacturing process and throughout the product’s lifecycle. This may include the use of test points, boundary-scan architecture, and built-in self-test (BIST) capabilities, among other techniques.
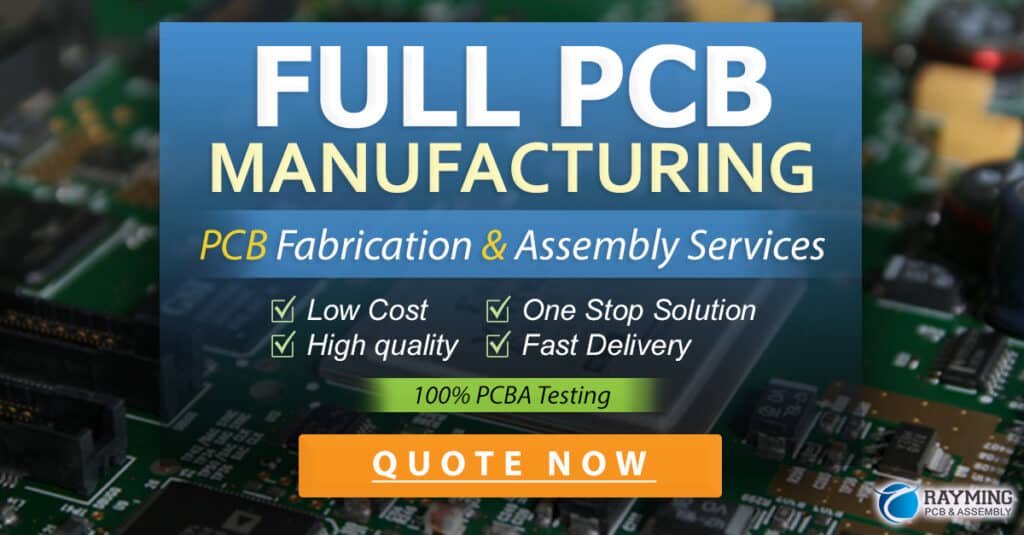
PCB-DFA Guidelines for Component Selection and Placement
Choosing the Right Components
When selecting components for your PCB design, consider the following DFA guidelines:
- Use standardized components whenever possible to reduce inventory complexity and simplify the assembly process.
- Opt for surface-mount devices (SMDs) over through-hole components, as they are more compatible with automated assembly processes.
- Choose components with appropriate package sizes and lead pitches to ensure compatibility with your assembly equipment and processes.
Component Placement Guidelines
Proper component placement is crucial for efficient PCB assembly. Follow these guidelines:
- Group similar components together to minimize the need for tool changes and streamline the assembly process.
- Provide adequate spacing between components to allow for easy access and minimize the risk of bridging or short circuits.
- Orient components consistently, with pin 1 indicators facing the same direction, to reduce the potential for assembly errors.
- Place components on one side of the board whenever possible to simplify the assembly process and reduce costs.
Footprint and Land Pattern Considerations
When designing footprints and land patterns for your components, keep these DFA guidelines in mind:
- Use standardized footprints and land patterns that are compatible with your assembly processes and equipment.
- Provide sufficient clearance around component pads to accommodate solder paste application and prevent bridging.
- Incorporate fiducial marks to assist with component alignment and placement during automated assembly.
- Consider the use of self-centering features, such as chamfered edges or tapered pads, to help components align properly during reflow soldering.
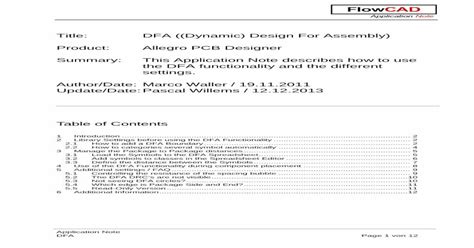
PCB-DFA Guidelines for Board Layout and Routing
Board Size and Shape
When designing the overall layout of your PCB, consider the following DFA guidelines:
- Minimize the board size to reduce material costs and improve handling during the assembly process.
- Use standard board shapes and avoid irregular or complex contours to simplify fabrication and assembly.
- Incorporate panelization features, such as v-grooves or tab-routing, to facilitate efficient board separation and minimize handling damage.
Routing and Trace Considerations
Proper routing and trace design can significantly impact the assembly process. Follow these guidelines:
- Use appropriate trace widths and spacing to accommodate your assembly processes and ensure reliable connections.
- Avoid sharp angles or abrupt changes in trace direction to minimize the risk of signal integrity issues and manufacturing defects.
- Provide sufficient clearance between traces and components to prevent short circuits and simplify the assembly process.
- Use via-in-pad design, when appropriate, to reduce board size and improve component placement flexibility.
Solder Mask and Silkscreen Design
Solder mask and silkscreen design play a crucial role in PCB-DFA. Consider these guidelines:
- Use a clear and legible silkscreen to provide assembly instructions, component identifiers, and orientation indicators.
- Ensure that the solder mask apertures are appropriately sized to accommodate solder paste application and prevent bridging.
- Provide adequate clearance between solder mask openings and component pads to allow for proper solder joint formation.
- Consider using color-coded solder masks or component identifiers to assist with manual assembly processes.
PCB-DFA Guidelines for Assembly Process Optimization
Solder Paste Application
Solder paste application is a critical step in the PCB assembly process. Follow these DFA guidelines:
- Use stencils with appropriate aperture sizes and shapes to ensure consistent solder paste deposition.
- Consider the use of step stencils or variable-thickness stencils to accommodate components with different height profiles.
- Optimize the solder paste printing process to minimize defects, such as bridging, insufficient deposition, or misalignment.
Component Placement and Reflow Soldering
Efficient component placement and reflow soldering are essential for successful PCB assembly. Keep these guidelines in mind:
- Use automated pick-and-place machines, when possible, to improve placement accuracy and speed.
- Optimize the placement sequence to minimize the need for tool changes and streamline the assembly process.
- Ensure that the reflow soldering profile is appropriately tuned for your specific components and board design.
- Implement process controls and monitoring to identify and correct any issues that may arise during the assembly process.
Inspection and Testing
Inspection and testing are critical for ensuring the quality and reliability of your assembLED PCBs. Consider these DFA guidelines:
- Incorporate automated optical inspection (AOI) or x-ray inspection into your assembly process to identify defects and ensure proper component placement.
- Use in-circuit testing (ICT) or functional testing to verify the electrical performance and functionality of your assembled PCBs.
- Implement statistical process control (SPC) techniques to monitor and optimize your assembly processes over time.
- Establish a comprehensive quality control plan that includes regular audits, supplier management, and continuous improvement initiatives.
Case Studies and Examples
To illustrate the benefits of implementing PCB-DFA guidelines, let’s explore a few real-world case studies and examples.
Case Study 1: Smartphone Motherboard Redesign
A smartphone manufacturer redesigned their device’s motherboard to incorporate DFA principles. By simplifying the component layout, using standardized parts, and optimizing the routing and trace design, they were able to reduce the assembly time by 25% and improve the overall yield by 15%. The redesign also enabled them to use automated assembly processes more effectively, further reducing costs and improving product quality.
Case Study 2: Medical Device PCB Optimization
A medical device company applied DFA guidelines to optimize the PCB design for one of their critical monitoring devices. By selecting components with standardized footprints, improving the board layout for accessibility, and incorporating testability features, they were able to streamline the assembly process and reduce the risk of defects. The optimized design resulted in a 30% reduction in assembly costs and a 20% improvement in product reliability.
Example 1: Component Placement Optimization
Consider a PCB design with a mix of through-hole and surface-mount components. By grouping similar components together, orienting them consistently, and providing adequate spacing, the assembly process can be significantly streamlined. For example, placing all the through-hole components on one side of the board and the surface-mount components on the other can minimize the need for manual soldering and improve the efficiency of automated placement processes.
Example 2: Solder Mask and Silkscreen Design
A well-designed solder mask and silkscreen can greatly assist with the assembly process. For instance, using a clear and legible silkscreen to indicate component orientation, polarity, and reference designators can reduce the risk of assembly errors and improve the speed of manual placement. Similarly, ensuring that the solder mask apertures are appropriately sized and spaced can prevent bridging and other soldering defects, ultimately improving the quality of the assembled PCBs.
Frequently Asked Questions (FAQ)
1. What is Design for Assembly (DFA) in the context of PCB design?
Design for Assembly (DFA) is a set of principles and guidelines that aim to optimize the PCB design for efficient and cost-effective assembly. By considering factors such as component selection, placement, routing, and testability, DFA helps to streamline the assembly process, reduce costs, and improve product quality.
2. Why is PCB-DFA important for product development?
PCB-DFA is crucial for product development because it directly impacts the manufacturing cost, time-to-market, and overall quality of the final product. By implementing DFA guidelines, designers can create PCBs that are easier to assemble, less prone to defects, and more reliable, ultimately resulting in a more competitive and profitable product.
3. What are some key principles of PCB-DFA?
Some key principles of PCB-DFA include simplicity and standardization, accessibility and orientation, minimizing manual processes, and design for testability. These principles guide designers in making decisions that optimize the PCB design for efficient assembly and improved product quality.
4. How can component selection and placement impact the assembly process?
Component selection and placement play a critical role in the assembly process. By choosing standardized components, using surface-mount devices, and grouping similar components together, designers can simplify the assembly process and reduce the need for manual intervention. Proper component placement also ensures accessibility, minimizes the risk of defects, and enables the use of automated assembly techniques.
5. What are some best practices for board layout and routing in the context of PCB-DFA?
Best practices for board layout and routing in PCB-DFA include minimizing board size, using standard shapes, incorporating panelization features, and ensuring appropriate trace widths and spacing. Designers should also consider the use of via-in-pad design, provide sufficient clearance between components and traces, and optimize the solder mask and silkscreen design to assist with the assembly process.
Conclusion
In conclusion, implementing DFA guidelines in your PCB design process is essential for creating efficient, cost-effective, and high-quality products. By focusing on simplicity, standardization, accessibility, and testability, you can streamline the assembly process, reduce costs, and improve product reliability. The guidelines and best practices discussed in this article provide a solid foundation for incorporating PCB-DFA principles into your design workflow.
Remember, successful implementation of PCB-DFA requires close collaboration between designers, manufacturing engineers, and other stakeholders involved in the product development process. By fostering open communication, sharing knowledge, and continuously refining your design and assembly processes, you can unlock the full potential of PCB-DFA and create products that excel in the marketplace.
As you embark on your next PCB design project, keep these DFA guidelines in mind and strive to create designs that are optimized for efficient assembly and superior performance. By doing so, you’ll be well on your way to developing products that meet the evolving needs of your customers and stand out in an increasingly competitive landscape.
Leave a Reply