Myth 1: More Layers Always Mean Better Performance
One of the most pervasive PCB myths is that adding more layers to a PCB will always improve its performance. While it’s true that multi-layer PCBs can offer certain advantages, such as reduced noise and improved signal integrity, adding layers isn’t always necessary or beneficial.
The Truth about PCB Layers
The number of layers in a PCB should be determined by the specific requirements of the design, such as:
- Signal integrity
- Power distribution
- Component placement
- Manufacturing constraints
Adding layers unnecessarily can actually lead to several problems, including:
- Increased manufacturing costs
- Longer lead times
- Reduced reliability due to increased complexity
In fact, many high-performance PCBs can be successfully designed with just two or four layers, provided that proper design techniques are used.
Number of Layers | Typical Applications |
---|---|
1 | Simple circuits, low-cost applications |
2 | Most common, suitable for many applications |
4 | Complex designs, high-speed digital, mixed-signal |
6 or more | Very complex designs, high-density interconnect (HDI) |
When to Consider Adding Layers
There are some situations where adding layers to a PCB can be beneficial:
- When the design requires a large number of power and ground planes for improved power distribution and noise reduction
- When the design includes high-speed digital signals that require careful control of impedance and crosstalk
- When the component density is very high and additional routing space is needed
However, before adding layers, designers should always consider alternative approaches, such as:
- Optimizing component placement and routing
- Using smaller components and finer pitch sizes
- Employing advanced design techniques, such as HDI or rigid-flex
Myth 2: Autorouting Is Always the Best Option
Another common PCB myth is that autorouting is always the best way to route a PCB. While autorouting tools can be very powerful and efficient, they are not a substitute for human expertise and judgment.
The Limitations of Autorouting
Autorouting tools work by applying a set of predefined rules and algorithms to route the traces on a PCB. However, these rules and algorithms are not perfect and can sometimes lead to suboptimal results, such as:
- Inefficient use of routing space
- Violations of design rules or constraints
- Poor signal integrity or EMI performance
In addition, autorouting tools can struggle with complex designs that require a high degree of customization or manual intervention.
When to Use Autorouting
Despite its limitations, autorouting can be a useful tool in certain situations:
- For simple designs with few constraints and requirements
- As a starting point for manual routing, to quickly generate a basic layout that can be refined by hand
- For large, repetitive designs where manual routing would be too time-consuming
However, for most high-performance or critical designs, manual routing is still the preferred approach. By carefully controlling the placement and routing of each trace, designers can ensure that the PCB meets all of its requirements and performs optimally.
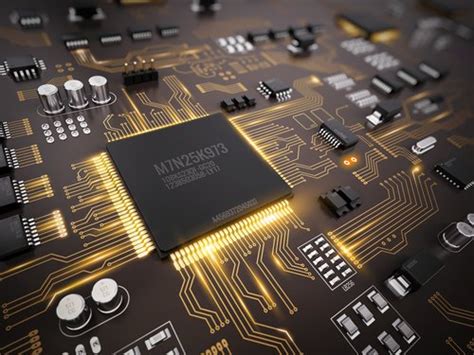
Myth 3: Grounding Can Be an Afterthought
Grounding is a critical aspect of PCB design, but it’s often treated as an afterthought or ignored altogether. This can lead to a host of problems, from poor signal integrity to EMI issues.
The Importance of Grounding
Proper grounding is essential for several reasons:
- It provides a low-impedance return path for signals, reducing noise and improving signal integrity
- It helps to minimize EMI by providing a shield against external interference
- It ensures that all components have a common reference voltage, preventing ground loops and other issues
Without proper grounding, even the most carefully designed PCB can suffer from poor performance or reliability issues.
Best Practices for Grounding
To ensure proper grounding in your PCB design, follow these best practices:
- Use a solid ground plane on one or more layers of the PCB, covering as much area as possible
- Connect all ground pins of components to the ground plane using short, low-impedance traces
- Use multiple vias to connect ground planes on different layers, minimizing inductance
- Avoid splitting the ground plane or creating long, narrow ground traces
- Use separate ground planes for analog and digital sections of the PCB, connected at a single point
By paying attention to grounding from the beginning of the design process, you can avoid many common issues and ensure that your PCB performs as intended.
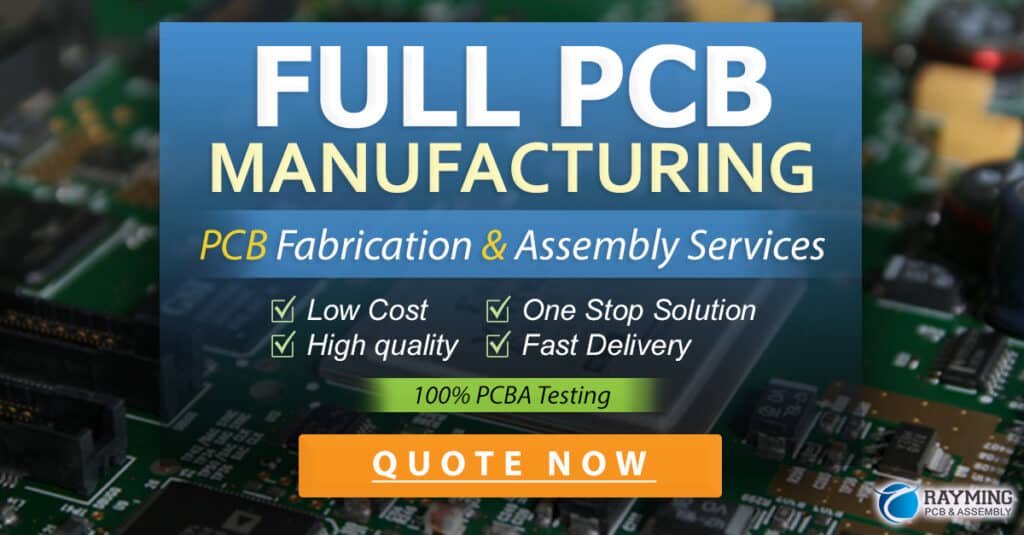
Myth 4: All Components Are Created Equal
Not all components are created equal, and choosing the wrong component for your PCB design can lead to problems down the line. It’s important to carefully consider the specifications and quality of each component before including it in your design.
Factors to Consider When Choosing Components
When selecting components for your PCB, consider the following factors:
- Electrical specifications, such as voltage and current ratings, frequency response, and noise performance
- Mechanical specifications, such as package size, pin count, and thermal characteristics
- Quality and reliability, including manufacturer reputation, failure rates, and environmental ratings
- Availability and lead times, especially for critical or custom components
Using substandard or counterfeit components can lead to a host of problems, from poor performance to premature failure.
Strategies for Selecting High-Quality Components
To ensure that you are using high-quality components in your PCB design, follow these strategies:
- Choose reputable manufacturers with a track record of quality and reliability
- Use authorized distributors to source components, rather than gray market or unknown suppliers
- Verify the authenticity of components using visual inspection, electrical testing, or other methods
- Consider using component libraries or pre-approved parts lists to streamline the selection process
By carefully selecting and verifying each component in your PCB design, you can avoid many common issues and ensure a high-quality end product.
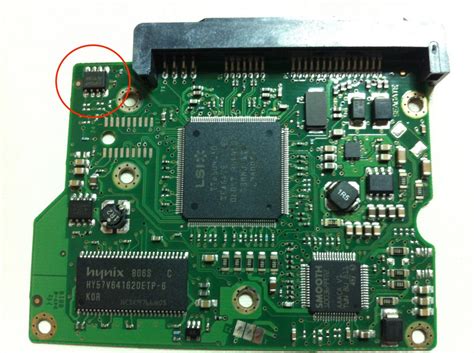
Myth 5: Testing Is Optional
Finally, one of the most dangerous PCB myths is that testing is optional or can be skipped to save time and money. In reality, testing is a critical step in the PCB design process that can catch issues before they become costly problems.
The Benefits of PCB Testing
PCB testing offers several key benefits:
- Verifying that the PCB functions as intended and meets all design requirements
- Catching manufacturing defects or assembly issues before the PCB is shipped
- Ensuring that the PCB is reliable and will perform well in the field
- Providing data for process improvement and quality control
Skipping testing can lead to delays, rework, and even product recalls, all of which can be far more costly than the testing itself.
Types of PCB Testing
There are several types of PCB testing that can be performed, depending on the specific requirements of the design:
- Visual inspection, to check for obvious defects or assembly issues
- Automated optical inspection (AOI), using cameras and image processing to detect problems
- In-circuit testing (ICT), to verify the functionality of individual components and circuits
- Functional testing, to ensure that the PCB meets its overall performance and functionality requirements
- Environmental testing, to verify that the PCB can withstand the expected operating conditions, such as temperature, humidity, and vibration
By incorporating testing into your PCB design process, you can catch issues early, reduce costs, and ensure a high-quality end product.
Frequently Asked Questions (FAQ)
1. How do I choose the right number of layers for my PCB design?
The number of layers in your PCB design should be determined by the specific requirements of your application, such as signal integrity, power distribution, and component placement. In general, simple designs can often be implemented with two layers, while more complex designs may require four or more layers. Consider factors such as cost, manufacturability, and performance when deciding on the number of layers.
2. When should I use autorouting, and when should I route manually?
Autorouting can be a useful tool for simple designs or as a starting point for manual routing. However, for most high-performance or critical designs, manual routing is the preferred approach. Manual routing allows you to carefully control the placement and routing of each trace, ensuring that the PCB meets all of its requirements and performs optimally.
3. What are some best practices for ensuring proper grounding in my PCB design?
To ensure proper grounding in your PCB design, use a solid ground plane on one or more layers of the PCB, covering as much area as possible. Connect all ground pins of components to the ground plane using short, low-impedance traces, and use multiple vias to connect ground planes on different layers. Avoid splitting the ground plane or creating long, narrow ground traces, and use separate ground planes for analog and digital sections of the PCB, connected at a single point.
4. How can I ensure that I am using high-quality components in my PCB design?
To ensure that you are using high-quality components in your PCB design, choose reputable manufacturers with a track record of quality and reliability, and use authorized distributors to source components. Verify the authenticity of components using visual inspection, electrical testing, or other methods, and consider using component libraries or pre-approved parts lists to streamline the selection process.
5. What types of testing should I perform on my PCB design?
There are several types of PCB testing that can be performed, depending on the specific requirements of your design. These include visual inspection, automated optical inspection (AOI), in-circuit testing (ICT), functional testing, and environmental testing. By incorporating testing into your PCB design process, you can catch issues early, reduce costs, and ensure a high-quality end product.
Conclusion
PCB design is a complex process that requires careful consideration of many factors, from component selection to grounding and testing. By busting these common PCB myths and following best practices, you can create high-quality, reliable PCBs that meet the needs of your application.
Remember to choose the right number of layers for your design, use manual routing for critical traces, pay attention to grounding from the beginning, select high-quality components, and incorporate testing into your process. By doing so, you can avoid common pitfalls and ensure the success of your PCB design.
Leave a Reply