Understanding the Basics of BOM
What is a BOM?
A Bill of Materials (BOM) is a comprehensive list of all the components, parts, and materials required to manufacture a product. In the context of PCB design, a BOM is a crucial document that lists all the electronic components and hardware needed to assemble a printed circuit board (PCB). It serves as a roadmap for the manufacturing process, ensuring that all necessary components are accounted for and procured in the correct quantities.
Why is a BOM Important in PCB Design?
A well-organized and accurate BOM is essential for several reasons:
-
Procurement: The BOM helps the purchasing department identify and procure the required components from suppliers in the correct quantities.
-
Cost Estimation: By listing all the components and their quantities, the BOM enables accurate cost estimation for the PCB project.
-
Assembly: The manufacturing team relies on the BOM to ensure that all components are available and correctly placed during the PCB assembly process.
-
Quality Control: A comprehensive BOM helps maintain consistency and quality throughout the manufacturing process by providing a clear reference for component specifications.
-
Revision Management: As PCB designs evolve, the BOM serves as a record of the changes made to the component list, allowing for better revision control.
Key Elements of a PCB BOM
A typical PCB BOM includes the following essential information:
1. Component Designator
Each component on the PCB is assigned a unique designator, such as R1 for a resistor or C3 for a capacitor. These designators are used to identify the components on the PCB Schematic and layout.
2. Component Description
A brief description of each component, including its function and key specifications, helps identify the correct part during procurement and assembly.
3. Manufacturer Part Number
The manufacturer part number is a unique identifier assigned by the component manufacturer. It is essential for procuring the exact component specified in the design.
4. Quantity
The BOM should specify the quantity of each component required for a single PCB assembly. This information is crucial for accurate procurement and inventory management.
5. Reference Designator
In addition to the individual component designators, the BOM may include reference designators that indicate where each component is located on the PCB, such as “U1” for an integrated circuit.
6. Supplier Information
The BOM may include information about the preferred suppliers for each component, including supplier part numbers and lead times. This helps streamline the procurement process.
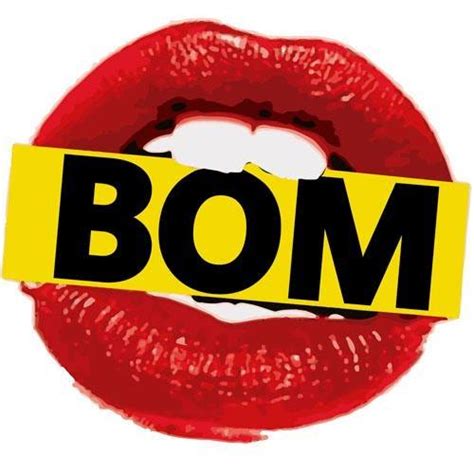
Types of BOMs in PCB Design
There are several types of BOMs used in PCB design, each serving a specific purpose:
1. Engineering BOM (EBOM)
The EBOM is created by the design team and includes all the components required for the PCB design. It may include multiple options for each component, allowing for flexibility in sourcing and procurement.
2. Manufacturing BOM (MBOM)
The MBOM is derived from the EBOM and is tailored for the manufacturing process. It includes the specific components and quantities required for production, taking into account factors such as availability, lead times, and cost.
3. Assembly BOM (ABOM)
The ABOM is a subset of the MBOM and focuses on the components and materials required for the PCB assembly process. It may exclude components that are not directly mounted on the PCB, such as enclosures or packaging materials.
4. Configurable BOM (CBOM)
A CBOM is used for PCB designs that have multiple configurations or variations. It includes all the possible components and their quantities for each configuration, allowing for easy customization of the final product.
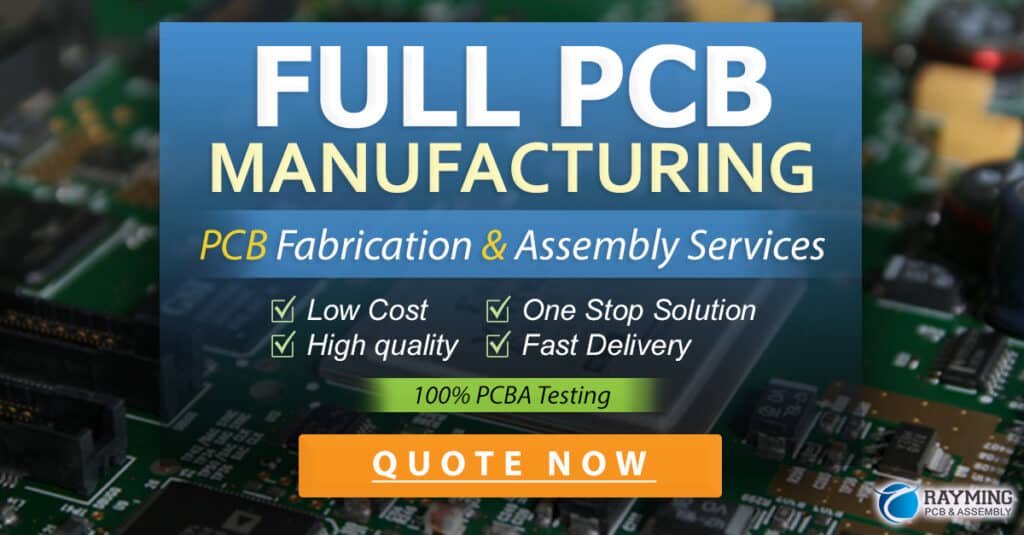
BOM Management Best Practices
Effective BOM management is crucial for avoiding delays, errors, and cost overruns in PCB design and manufacturing. Here are some best practices to follow:
1. Standardize BOM Format
Establish a standard format for your BOMs, including the required fields, units of measurement, and nomenclature. This ensures consistency and reduces the risk of errors.
2. Use Automated Tools
Utilize PCB Design Software with integrated BOM management features to automatically generate and update BOMs based on the schematic and layout. This saves time and minimizes the risk of manual errors.
3. Validate BOM Data
Regularly validate the BOM data against the schematic and layout to ensure accuracy and completeness. This helps catch any discrepancies early in the design process.
4. Collaborate with Stakeholders
Involve all relevant stakeholders, such as procurement, manufacturing, and quality control teams, in the BOM review process. Their input can help identify potential issues and optimize the BOM for production.
5. Version Control
Implement a version control system for your BOMs to track changes and revisions throughout the design process. This helps maintain a clear record of updates and ensures that all teams are working with the latest version.
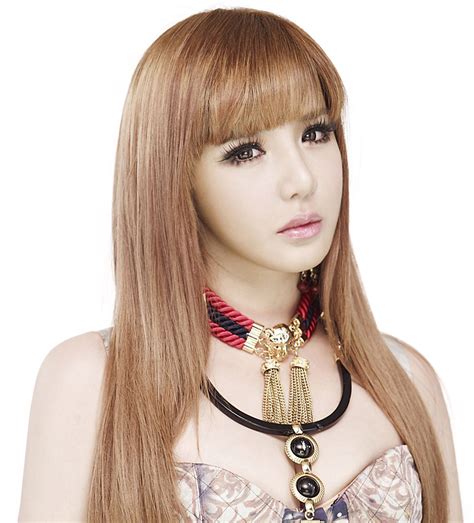
Common BOM Mistakes to Avoid
To ensure a smooth PCB design and manufacturing process, avoid these common BOM mistakes:
1. Incomplete or Inaccurate Data
Ensure that all required fields in the BOM are complete and accurate, including component descriptions, manufacturer part numbers, and quantities. Incomplete or inaccurate data can lead to procurement issues and assembly delays.
2. Inconsistent Formatting
Inconsistent formatting, such as mixing units of measurement or using different naming conventions, can cause confusion and errors. Adhere to the established BOM format and standards.
3. Outdated Components
Using outdated or obsolete components in the BOM can result in procurement challenges and potential redesigns. Regularly review and update the BOM to ensure that all components are current and readily available.
4. Lack of Communication
Failing to communicate BOM changes or updates to all relevant stakeholders can lead to confusion and delays. Establish clear communication channels and processes for BOM updates and revisions.
5. Manual Errors
Relying on manual data entry or updates can introduce errors into the BOM. Use automated tools and processes wherever possible to minimize the risk of manual errors.
BOM Example
To illustrate the structure and content of a typical PCB BOM, consider the following example:
Designator | Description | Manufacturer Part Number | Quantity | Reference Designator | Supplier |
---|---|---|---|---|---|
R1, R2 | 10kΩ, 0.25W, 1% Resistor | ABC-10K-0.25W-1% | 2 | R1, R2 | Supplier A |
C1 | 10µF, 50V, Ceramic Capacitor | XYZ-10uF-50V-CER | 1 | C1 | Supplier B |
U1 | Microcontroller, 32-bit, 64KB Flash | MCU-32B-64KB-QFP | 1 | U1 | Supplier C |
LED1 | LED, Red, 0805 Package | LED-RED-0805 | 1 | LED1 | Supplier A |
This simplified example shows the essential information typically included in a PCB BOM, such as component designators, descriptions, manufacturer part numbers, quantities, reference designators, and supplier information.
FAQ
1. What is the difference between an EBOM and an MBOM?
An Engineering BOM (EBOM) is created by the design team and includes all the components required for the PCB design, allowing for flexibility in sourcing and procurement. A Manufacturing BOM (MBOM) is derived from the EBOM and is tailored for the manufacturing process, including the specific components and quantities required for production.
2. How can I ensure the accuracy of my BOM?
To ensure the accuracy of your BOM, regularly validate the BOM data against the schematic and layout, use automated tools for BOM management, and involve all relevant stakeholders in the BOM review process.
3. What should I do if a component in my BOM becomes obsolete?
If a component in your BOM becomes obsolete, you should update the BOM with a suitable alternative component that meets the required specifications. Communicate the change to all relevant stakeholders and ensure that the new component is procured for production.
4. How can I manage BOMs for PCB designs with multiple configurations?
For PCB designs with multiple configurations, use a Configurable BOM (CBOM) that includes all the possible components and their quantities for each configuration. This allows for easy customization of the final product and streamlines the manufacturing process.
5. What are the consequences of an inaccurate or incomplete BOM?
An inaccurate or incomplete BOM can lead to procurement issues, assembly delays, and potential redesigns. It can also result in increased costs and longer lead times for the PCB project. Ensuring the accuracy and completeness of the BOM is crucial for a smooth and efficient PCB design and manufacturing process.
Conclusion
A well-managed and accurate Bill of Materials (BOM) is a critical component of successful PCB design and manufacturing. By understanding the key elements, types, and best practices of BOM management, PCB designers can ensure that their projects are completed on time, within budget, and to the required quality standards. By avoiding common BOM mistakes and utilizing automated tools and processes, designers can streamline the PCB design and manufacturing process, reducing the risk of errors and delays.
Leave a Reply