What Causes Short Circuits on PCBs?
Short circuits on PCBs can occur due to several reasons:
-
Manufacturing defects: Improper etching, drilling, or plating during the PCB manufacturing process can lead to unintended connections between traces or components.
-
Design flaws: Inadequate spacing between traces or improper component placement can result in short circuits.
-
Mechanical damage: Mishandling or excessive stress on the PCB can cause traces to break or components to become dislodged, creating short circuits.
-
Environmental factors: Exposure to moisture, dust, or other contaminants can cause short circuits on PCBs.
Visual Inspection for Short Circuits
The first step in testing for short circuits on a PCB is to perform a visual inspection. This involves examining the board closely for any visible defects or anomalies that could indicate a short circuit.
What to Look For During Visual Inspection
-
Solder bridges: Excessive solder between adjacent pads or traces can create a conductive path, resulting in a short circuit.
-
Damaged traces: Cracks, scratches, or breaks in the PCB Traces can cause short circuits.
-
Misaligned components: Improperly placed or rotated components can create unintended connections between their leads and adjacent traces.
-
Foreign objects: Conductive debris, such as metal shavings or solder splashes, can cause short circuits if they come into contact with exposed traces or pads.
Tools for Visual Inspection
To perform a thorough visual inspection, you will need the following tools:
-
Magnifying glass or microscope: A magnifying glass or microscope with at least 10x magnification will help you identify small defects or anomalies on the PCB.
-
Adequate lighting: Proper lighting is essential for visual inspection. Use a bright, adjustable light source to illuminate the PCB from various angles.
-
Inspection mirror: An inspection mirror can help you examine hard-to-reach areas on the PCB, such as the underside of components or between tightly spaced traces.
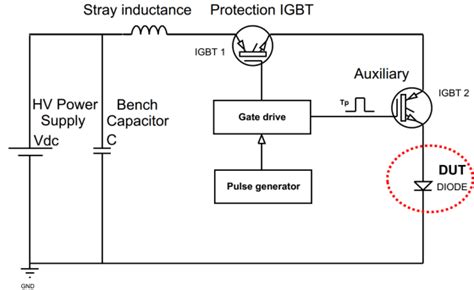
Continuity Testing for Short Circuits
Continuity testing is a simple and effective method for detecting short circuits on a PCB. It involves using a multimeter to check for unintended connections between points on the board.
How to Perform Continuity Testing
-
Set your multimeter to the continuity or resistance mode: Most digital multimeters have a dedicated continuity testing mode, often indicated by a diode symbol or a beeping sound.
-
Identify the points to test: Refer to the PCB Schematic or layout to determine which points should be isolated from each other. These points can include component pads, test points, or specific traces.
-
Connect the multimeter probes: Touch one probe to the first point and the other probe to the second point. If there is continuity (a short circuit), the multimeter will display a low resistance value or emit a beeping sound.
-
Test all relevant points: Repeat the process for all points on the PCB that should be isolated from each other.
Interpreting Continuity Testing Results
When performing continuity testing, you may encounter the following results:
Result | Interpretation | Action |
---|---|---|
Open circuit (infinite resistance) | No short circuit detected | Proceed to the next test point |
Low resistance (typically < 10 Ω) | Short circuit detected | Investigate and repair the short circuit |
High resistance (> 10 Ω) | Possible poor connection or damaged trace | Investigate and repair if necessary |
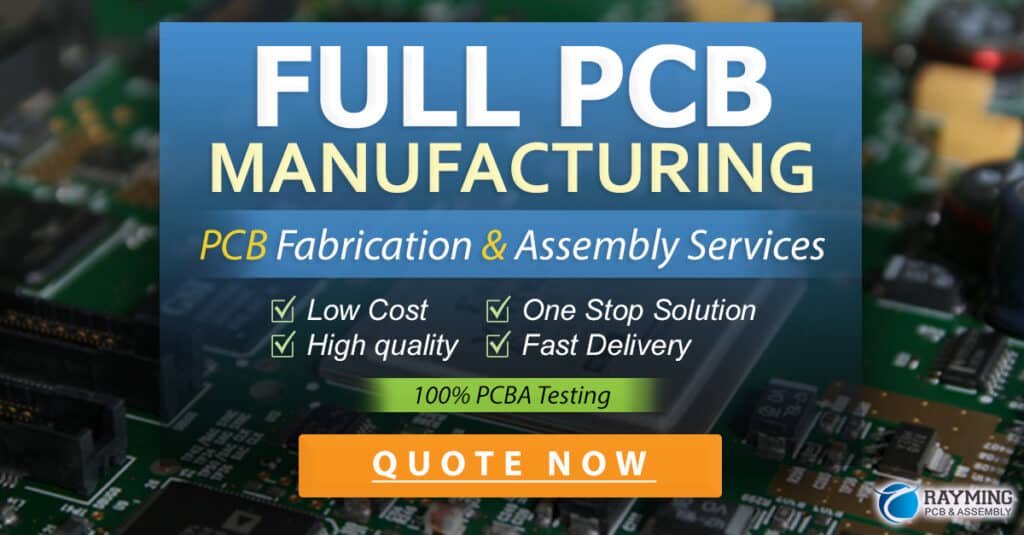
Advanced Short-Circuit Testing Techniques
While visual inspection and continuity testing are effective for detecting many short circuits, some PCBs may require more advanced testing methods. These techniques are particularly useful for high-density boards or those with complex layouts.
Flying Probe Testing
Flying probe testing is an automated method that uses multiple moving probes to test for short circuits and other defects on a PCB. The probes are programmed to touch specific points on the board and perform electrical tests, such as continuity and resistance measurements.
Advantages of flying probe testing:
1. High accuracy: Flying probe testers can detect short circuits and other defects with high precision, even on densely populated boards.
-
Flexibility: The probes can be programmed to test any point on the PCB, making it adaptable to various board designs and layouts.
-
Speed: Flying probe testers can perform tests quickly, making them suitable for high-volume production.
Automated Optical Inspection (AOI)
AOI is a non-contact testing method that uses high-resolution cameras and image processing software to detect short circuits and other defects on PCBs. The system captures images of the board and compares them to a reference image or design data to identify anomalies.
Advantages of AOI:
1. Fast and efficient: AOI systems can inspect PCBs at high speeds, making them ideal for high-volume manufacturing.
-
Consistent results: AOI eliminates human error and subjectivity, providing consistent and reliable inspection results.
-
Defect detection: In addition to short circuits, AOI can detect a wide range of defects, such as missing components, incorrect component placement, and solder defects.
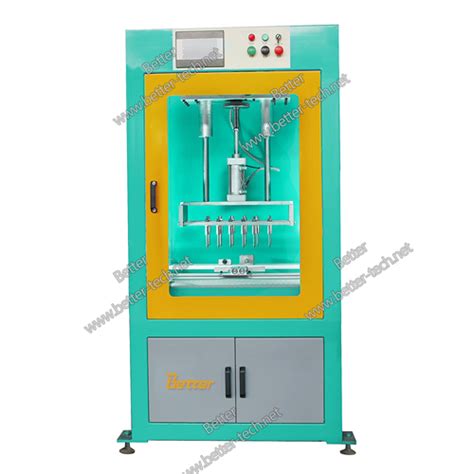
Repairing Short Circuits on PCBs
Once a short circuit has been detected, it is essential to repair it promptly to prevent further damage to the PCB or connected components. The repair method will depend on the nature and location of the short circuit.
Common Short Circuit Repair Methods
-
Solder bridge removal: If a short circuit is caused by a solder bridge, use a soldering iron and solder wick or a desoldering pump to remove the excess solder.
-
Trace repair: For damaged or broken traces, use a sharp knife or scalpel to scrape away the damaged portion of the trace. Then, use a conductive ink pen or a small wire to bridge the gap and restore connectivity.
-
Component replacement: If a short circuit is caused by a damaged or improperly placed component, carefully remove the component using a soldering iron or hot air rework station. Clean the pads and replace the component with a new one.
Tips for Successful Short Circuit Repairs
-
Work in a clean, well-lit environment: A clean workspace and adequate lighting will help you identify and repair short circuits more effectively.
-
Use the right tools: Ensure you have the appropriate soldering iron, solder, and other tools for the repair job.
-
Refer to the PCB documentation: Always consult the PCB schematic, layout, and assembly drawings to ensure you are repairing the correct components and traces.
-
Test after repair: After completing the repair, perform continuity testing and visual inspection to verify that the short circuit has been successfully eliminated.
Frequently Asked Questions (FAQ)
-
What is the difference between a short circuit and an open circuit?
A short circuit occurs when there is an unintended connection between two points in a circuit, allowing current to flow through an undesired path. An open circuit, on the other hand, is a break in the conductive path, preventing current from flowing altogether. -
Can short circuits damage electronic components?
Yes, short circuits can cause excessive current flow, leading to overheating and permanent damage to electronic components. In some cases, short circuits can even cause fires or explosions. -
How can I prevent short circuits on PCBs during the design phase?
To prevent short circuits during the design phase, ensure adequate spacing between traces and components, follow recommended design guidelines for your chosen manufacturing process, and use design rule checks (DRCs) to identify potential issues before sending the board for fabrication. -
What should I do if I suspect a short circuit on a PCB but cannot locate it visually?
If you cannot locate a short circuit through visual inspection, use continuity testing or advanced techniques like flying probe testing or AOI to isolate the problem area. Consult the PCB documentation and trace the circuit path to narrow down the search area. -
Can short circuits occur after a PCB has been assembled and in use?
Yes, short circuits can develop over time due to factors such as mechanical stress, environmental exposure, or component degradation. Regular inspections and testing can help identify and address short circuits before they cause significant damage or malfunctions.
Conclusion
Short circuits on PCBs can lead to malfunctions, component damage, and even safety hazards. By understanding the causes of short circuits and employing proper testing and repair techniques, you can ensure the reliability and longevity of your electronic products.
Visual inspection and continuity testing are essential first steps in identifying short circuits, while advanced methods like flying probe testing and AOI offer increased accuracy and efficiency for more complex boards.
When repairing short circuits, always work in a clean environment, use the appropriate tools, and refer to the PCB documentation to ensure a successful repair. After completing the repair, perform thorough testing to verify that the short circuit has been eliminated and the board functions as intended.
By implementing a comprehensive short-circuit testing and repair process, you can minimize the risk of product failures, improve customer satisfaction, and protect your company’s reputation in the competitive electronics industry.
Leave a Reply