Introduction to PCB
A Printed Circuit board (PCB) is a fundamental component in modern electronic devices. It is a flat board made of insulating materials, such as fiberglass or composite epoxy, with conductive pathways etched or printed onto its surface. These pathways, known as traces, connect various electronic components, including resistors, capacitors, integrated circuits, and connectors, to form a complete electrical circuit.
PCBs have revolutionized the electronics industry by providing a compact, reliable, and cost-effective means of assembling electronic circuits. They are used in a wide range of applications, from simple consumer electronics to complex industrial equipment, aerospace systems, and medical devices.
History of PCBs
The concept of printed circuit boards can be traced back to the early 20th century. In 1903, Albert Hanson, a German inventor, filed a patent for a method of creating conductive pathways on an insulating material. However, it wasn’t until the 1940s that PCBs began to gain widespread adoption.
During World War II, the United States military heavily invested in the development of PCB technology to improve the reliability and efficiency of electronic equipment used in military applications. In 1943, Paul Eisler, an Austrian engineer working in the United Kingdom, developed a method for etching conductive pathways onto a non-conductive substrate, which laid the foundation for modern PCB manufacturing techniques.
In the following decades, PCB technology continued to evolve, with the introduction of double-sided boards, multilayer boards, and surface-mount technology (SMT). These advancements allowed for the creation of more complex circuits and the miniaturization of electronic devices.
PCB Manufacturing Process
The PCB manufacturing process involves several steps, each requiring precision and adherence to strict quality control measures. The following is an overview of the main steps involved in PCB production:
1. PCB Design
The first step in creating a PCB is designing the circuit using specialized software, such as Eagle, KiCad, or Altium Designer. The designer creates a schematic diagram that represents the electrical connections between components and then translates this schematic into a physical layout of the PCB.
During the layout process, the designer must consider factors such as component placement, trace width and spacing, power distribution, signal integrity, and manufacturing constraints. The final design is then exported as a set of files, typically Gerber files, which are used to guide the manufacturing process.
2. Substrate Preparation
The substrate, or base material, for the PCB is typically a thin, flat sheet of insulating material, such as FR-4 (a type of fiberglass-reinforced epoxy laminate). The substrate is cut to the desired size and shape, and any necessary holes are drilled for through-hole components or mounting purposes.
3. Copper Cladding
The substrate is then clad with a thin layer of copper on one or both sides, depending on whether the PCB is single-sided or double-sided. The copper layer is typically applied using an electroplating process or by laminating a pre-clad copper foil onto the substrate.
4. Etching
The next step is to remove unwanted copper from the substrate to create the desired conductive pathways. This is achieved through a process called etching. The copper-clad substrate is coated with a photoresist material, which hardens when exposed to ultraviolet (UV) light.
The PCB design files are used to create a photomask, which is placed on top of the photoresist-coated substrate. The photomask blocks UV light in areas where copper should remain and allows UV light to pass through in areas where copper should be removed.
After exposing the photoresist to UV light, the board is placed in a developer solution, which removes the unexposed photoresist. The board is then placed in an etching solution, typically ferric chloride or ammonium persulfate, which dissolves the copper in areas not protected by the hardened photoresist. Finally, the remaining photoresist is stripped away, leaving the desired copper traces on the substrate.
5. Soldermask Application
A soldermask, also known as a solder resist, is a protective coating applied to the PCB to prevent solder from bridging between traces and to protect the copper traces from oxidation and damage. The soldermask is typically green in color but can also be found in other colors, such as blue, red, or black.
The soldermask is applied using a similar process to the photoresist coating used during etching. The board is coated with a photosensitive soldermask material, exposed to UV light through a photomask, and then developed to remove the unexposed areas.
6. Silkscreen Printing
The silkscreen layer is used to add text, logos, and component identifiers to the PCB. This layer is typically white but can also be found in other colors. The silkscreen is applied using a screen printing process, where ink is forced through a fine mesh screen onto the PCB surface.
7. Surface Finish
To protect the exposed copper traces and pads and to enhance solderability, a surface finish is applied to the PCB. Common surface finishes include:
- Hot Air Solder Leveling (HASL): A thin layer of solder is applied to the copper surfaces using a hot air leveling process.
- Organic Solderability Preservative (OSP): A thin, organic coating is applied to the copper surfaces to prevent oxidation.
- Electroless Nickel Immersion Gold (ENIG): A layer of nickel is plated onto the copper surfaces, followed by a thin layer of gold.
8. Electrical Testing
After the PCB manufacturing process is complete, the boards undergo electrical testing to ensure they function as intended. This may include continuity tests, insulation resistance tests, and functional tests, depending on the complexity of the PCB and its intended application.
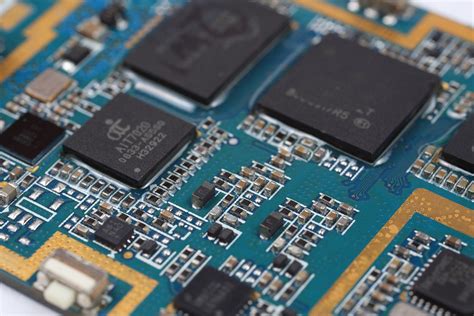
Types of PCBs
There are several types of PCBs, each with its own unique characteristics and manufacturing requirements. The most common types include:
1. Single-sided PCBs
Single-sided PCBs have conductive traces on only one side of the substrate. They are the simplest and most cost-effective type of PCB but are limited in terms of circuit complexity and density.
2. Double-sided PCBs
Double-sided PCBs have conductive traces on both sides of the substrate, allowing for more complex circuits and higher component density compared to single-sided boards. The two sides of the board are connected using through-hole vias.
3. Multilayer PCBs
Multilayer PCBs consist of three or more layers of conductive traces separated by insulating layers. These boards offer the highest circuit density and complexity but are also the most expensive to manufacture. Multilayer PCBs are used in applications that require high-speed signal processing, such as smartphones, computers, and telecommunications equipment.
4. Flexible PCBs
Flexible PCBs, also known as flex circuits, are made using a flexible substrate material, such as polyimide or polyester. These boards can bend and twist without damaging the conductive traces, making them ideal for applications where space is limited, or the device requires a non-planar design.
5. Rigid-Flex PCBs
Rigid-flex PCBs combine the benefits of both rigid and flexible PCBs. They consist of rigid PCB sections connected by flexible PCB sections, allowing for three-dimensional packaging and improved reliability in applications subject to vibration or mechanical stress.
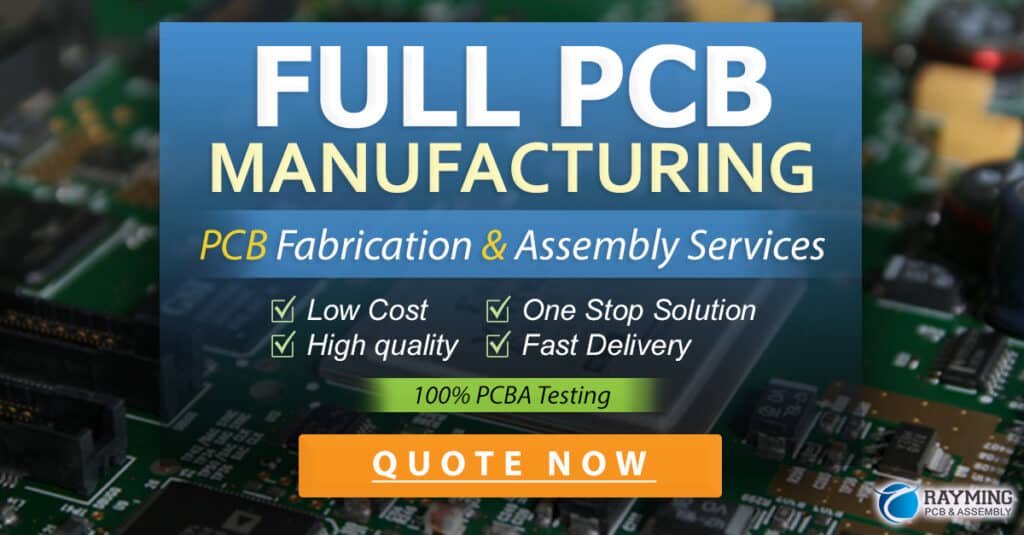
PCB Design Considerations
When designing a PCB, several factors must be considered to ensure optimal performance, reliability, and manufacturability. Some of the most important design considerations include:
1. Component Placement
Proper component placement is crucial for ensuring signal integrity, reducing noise and interference, and facilitating efficient manufacturing. Components should be placed in a logical manner, with related components grouped together and adequate spacing between components to allow for proper soldering and inspection.
2. Trace Width and Spacing
The width and spacing of traces on a PCB depend on several factors, including the current carrying requirements, the desired impedance, and the manufacturing capabilities of the PCB fabricator. Traces should be wide enough to handle the expected current without excessive heating, while maintaining sufficient spacing to prevent signal crosstalk and short circuits.
3. Power Distribution
Proper power distribution is essential for ensuring stable and reliable operation of the electronic circuit. Power traces should be sufficiently wide to minimize voltage drop and heat generation, and decoupling capacitors should be placed close to power-hungry components to reduce noise and supply ripple.
4. Signal Integrity
Signal integrity refers to the quality of the electrical signals transmitted through the PCB. To maintain signal integrity, designers must consider factors such as trace impedance, termination, and routing. High-speed signals may require special considerations, such as the use of differential pairs, controlled impedance traces, and careful attention to trace length matching.
5. Thermal Management
Proper thermal management is necessary to prevent overheating of components and to ensure reliable operation of the electronic circuit. Designers should consider the power dissipation of components, the thermal conductivity of the PCB substrate, and the use of thermal vias, heatsinks, or other cooling methods as needed.
6. Manufacturing Constraints
PCB designers must also consider the manufacturing capabilities and constraints of the PCB fabricator. This includes factors such as minimum trace width and spacing, hole sizes, and soldermask and silkscreen tolerances. Designers should work closely with the fabricator to ensure that the PCB design is manufacturable and cost-effective.
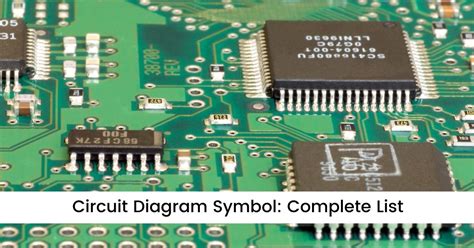
PCB Assembly Techniques
Once the PCB has been fabricated, the electronic components must be attached to the board to create a functional electronic assembly. There are two primary methods for PCB assembly: through-hole assembly and surface-mount assembly.
1. Through-hole Assembly
Through-hole assembly involves inserting component leads through holes drilled in the PCB and soldering them to pads on the opposite side of the board. This method is often used for larger components or those subject to mechanical stress, such as connectors and transformers.
The through-hole assembly process typically involves the following steps:
- Component insertion: Components are inserted into the drilled holes on the PCB, either manually or using automated insertion machines.
- Wave soldering: The PCB is passed over a molten solder wave, which solders the component leads to the pads on the bottom side of the board.
- Inspection and cleaning: The assembled PCB is inspected for solder bridges, cold solder joints, or other defects, and any flux residue is cleaned from the board.
2. Surface-mount Assembly
Surface-mount assembly, also known as surface-mount technology (SMT), involves attaching components directly to pads on the surface of the PCB without the use of through-holes. SMT components are typically smaller and have shorter leads than through-hole components, allowing for higher component density and improved high-frequency performance.
The surface-mount assembly process typically involves the following steps:
- Solder paste application: A thin layer of solder paste, consisting of tiny solder spheres suspended in a flux matrix, is applied to the component pads on the PCB using a stencil or screen printing process.
- Component placement: Surface-mount components are placed onto the solder paste-coated pads using automated pick-and-place machines or, in some cases, manually.
- Reflow soldering: The PCB is passed through a reflow oven, which heats the board in a controlled manner, causing the solder paste to melt and form a permanent electrical and mechanical bond between the components and the pads.
- Inspection and cleaning: The assembled PCB is inspected for proper component placement, solder joint quality, and other defects, and any flux residue is cleaned from the board.
PCB Testing and Quality Control
To ensure the reliability and functionality of the assembled PCB, various testing and quality control methods are employed. Some common testing techniques include:
1. Visual Inspection
Visual inspection is the first line of defense in PCB quality control. Inspectors visually examine the PCB for defects such as solder bridges, cold solder joints, component misalignment, or damaged components. Visual inspection can be performed manually or using automated optical inspection (AOI) systems.
2. Automated Optical Inspection (AOI)
AOI systems use high-resolution cameras and image processing software to automatically detect and classify defects on the PCB. These systems can quickly inspect large numbers of PCBs and identify defects that may be difficult to spot with the naked eye.
3. X-ray Inspection
X-ray inspection is used to examine solder joints and other features that are hidden from view, such as those under ball grid array (BGA) components. X-ray systems can detect voids, cracks, or other defects in solder joints that could compromise the reliability of the assembly.
4. In-circuit Testing (ICT)
In-circuit testing involves using a bed-of-nails fixture to make electrical contact with specific points on the PCB and verify the presence, orientation, and value of components, as well as the continuity and isolation of traces. ICT can detect faults such as missing or incorrectly placed components, short circuits, and open circuits.
5. Functional Testing
Functional testing involves applying power to the assembled PCB and verifying that it performs its intended function. This may include testing the board’s response to various inputs, measuring output signals, and checking for any anomalies or deviations from the expected behavior.
Applications of PCBs
PCBs are used in virtually every electronic device, from simple consumer gadgets to complex industrial and military systems. Some common applications include:
1. Consumer Electronics
PCBs are found in a wide range of consumer electronics, such as smartphones, tablets, laptops, televisions, gaming consoles, and home appliances. The compact size and high component density of modern PCBs have enabled the development of increasingly sophisticated and feature-rich consumer devices.
2. Automotive Electronics
PCBs play a crucial role in modern automobiles, controlling various systems such as engine management, braking, steering, navigation, and entertainment. The harsh operating environment in vehicles, including extreme temperatures, vibration, and moisture, requires the use of rugged, high-reliability PCBs.
3. Industrial Automation and Control
PCBs are used extensively in industrial automation and control systems, such as programmable logic controllers (PLCs), sensors, actuators, and human-machine interfaces (HMIs). These boards must be designed to withstand the harsh conditions found in industrial environments, including dust, moisture, and electromagnetic interference (EMI).
4. Medical Devices
PCBs are essential components in a wide range of medical devices, from simple monitoring equipment to complex imaging systems and implantable devices. Medical PCBs must meet stringent quality and reliability standards and are often subject to regulatory requirements such as ISO 13485 and FDA approval.
5. Aerospace and Defense
PCBs used in aerospace and defense applications must be designed to withstand extreme environmental conditions, such as high altitudes, radiation, and shock and vibration. These boards often require the use of specialized materials, such as polyimide substrates, and must meet strict reliability and traceability requirements, such as those outlined in the AS9100 quality management standard.
Future Trends in PCB Technology
As electronic devices continue to evolve and become more sophisticated, PCB technology must keep pace to support these advancements. Some of the key trends shaping the future of PCB design and manufacturing include:
1. Miniaturization
The demand for smaller, more compact electronic devices is driving the development of ever-smaller PCBs with higher component density. This trend is being enabled by advancements in PCB materials, such as high-density interconnect (HDI) substrates, and manufacturing processes, such as microvias and embedded components.
2. High-speed Design
As data rates continue to increase, PCB designers must contend with the challenges of high-speed signal integrity, such as impedance matching, crosstalk, and signal loss. Advanced PCB design techniques, such as differential signaling and controlled impedance routing, are becoming increasingly important for maintaining signal integrity in high-speed applications.
3. Additive Manufacturing
Additive manufacturing, also known as 3D printing, is emerging as a potential alternative to traditional PCB manufacturing methods. Additive manufacturing enables the creation of complex, three-dimensional PCB structures and the integration of conductive traces and components within the substrate itself. While still in the early stages of development, additive manufacturing could revolutionize PCB design and manufacturing in the future.
4. Sustainability
As environmental concerns continue to grow, there is increasing pressure on the electronics industry to adopt more sustainable practices. This includes the development of eco-friendly PCB materials, such as halogen-free substrates and lead-free solders, as well as the implementation of recycling and disposal programs for end-of-life PCBs.
Frequently Asked Questions (FAQ)
-
What is the difference between a PCB and a PCBA?
A PCB (Printed Circuit Board) is the bare board with copper traces and pads, while a PCBA (Printed Circuit Board Assembly) is a PCB with electronic components soldered onto it, forming a complete electronic assembly. -
What is the most common PCB substrate material?
FR-4, a glass-reinforced epoxy laminate, is the most widely used PCB substrate material due to its good mechanical and electrical properties, cost-effectiveness, and wide availability. -
What is the purpose of a soldermask on a PCB?
A soldermask is a protective coating applied to the PCB that prevents solder from bridging between traces and pads during the assembly process. It also protects the copper traces from oxidation and damage. -
What is the difference between through-hole and surface-mount components?
Through-hole components have long leads that are inserted into holes drilled in the PCB and soldered to pads on the opposite side
Leave a Reply