The History of PCBs
The development of PCBs can be traced back to the early 20th century. In 1903, Albert Hanson, a German inventor, filed a patent for a method of creating an electrical connection by bonding a metal foil onto an insulating board. This laid the foundation for the concept of printed circuit boards.
In the 1920s, Charles Ducas, an American inventor, created a method for electroplating circuit patterns onto an insulated surface. This process was further refined in the 1940s by Paul Eisler, an Austrian engineer, who developed a method for etching copper foil to create circuit patterns on a non-conductive substrate.
The widespread adoption of PCBs began in the 1950s, driven by the growth of the electronics industry and the demand for more compact and reliable electronic devices. The introduction of through-hole technology and the development of automated assembly processes further accelerated the use of PCBs in various applications.
Decade | Key Developments |
---|---|
1900s | Albert Hanson patents a method for bonding metal foil onto an insulating board |
1920s | Charles Ducas develops a method for electroplating circuit patterns |
1940s | Paul Eisler refines the process of etching copper foil to create circuit patterns |
1950s | Widespread adoption of PCBs begins, driven by the growth of the electronics industry |
The Composition of a PCB
A typical PCB consists of several layers, each serving a specific purpose:
-
Substrate: The base material, usually made of fiberglass or composite epoxy, provides mechanical support and electrical insulation.
-
Copper layers: Thin sheets of copper are laminated onto the substrate. These layers are etched to create the conductive pathways that connect the electronic components.
-
Solder mask: A protective layer applied over the copper traces to prevent short circuits and oxidation. It also provides insulation and improves the aesthetics of the board.
-
Silkscreen: A printed layer that adds text, logos, and component identifiers to the PCB, making it easier to assemble and troubleshoot.
The number of copper layers in a PCB can vary depending on the complexity of the circuit design. Single-layer boards have copper traces on only one side, while double-layer boards have copper on both sides. Multi-layer PCBs can have four, six, eight, or more layers, allowing for more complex routing and better signal integrity.
Layer | Purpose |
---|---|
Substrate | Provides mechanical support and electrical insulation |
Copper | Creates conductive pathways to connect electronic components |
Solder Mask | Prevents short circuits, oxidation, and provides insulation |
Silkscreen | Adds text, logos, and component identifiers for easier assembly |
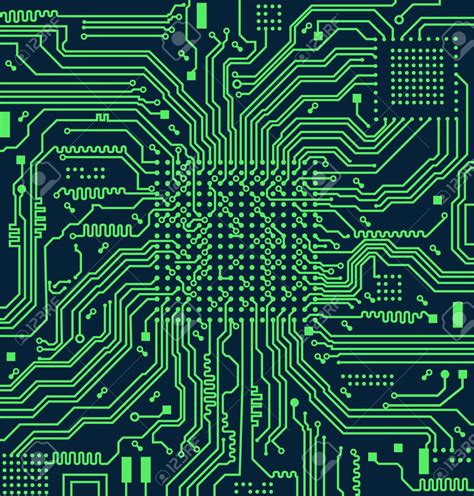
Types of PCBs
There are several types of PCBs, each designed to meet specific requirements:
-
Rigid PCBs: These are the most common type, made from a solid substrate material that does not flex. They are used in a wide range of applications, from consumer electronics to industrial equipment.
-
Flexible PCBs: Made from flexible materials like polyimide, these PCBs can bend and conform to various shapes. They are often used in applications where space is limited or where the board needs to fit into a non-planar enclosure.
-
Rigid-Flex PCBs: A combination of rigid and flexible PCBs, these boards have both rigid and flexible sections. They are used in applications that require the benefits of both types, such as in aerospace and military equipment.
-
High-Density Interconnect (HDI) PCBs: These boards feature finer trace widths and smaller vias, allowing for higher component density and improved signal integrity. HDI PCBs are commonly used in smartphones, tablets, and other compact electronic devices.
PCB Type | Characteristics | Common Applications |
---|---|---|
Rigid | Made from a solid substrate, does not flex | Consumer electronics, industrial equipment |
Flexible | Made from flexible materials, can bend and conform to shapes | Aerospace, wearable devices |
Rigid-Flex | Combines rigid and flexible sections | Aerospace, military equipment |
HDI | Features finer traces and smaller vias for higher component density | Smartphones, tablets, compact devices |
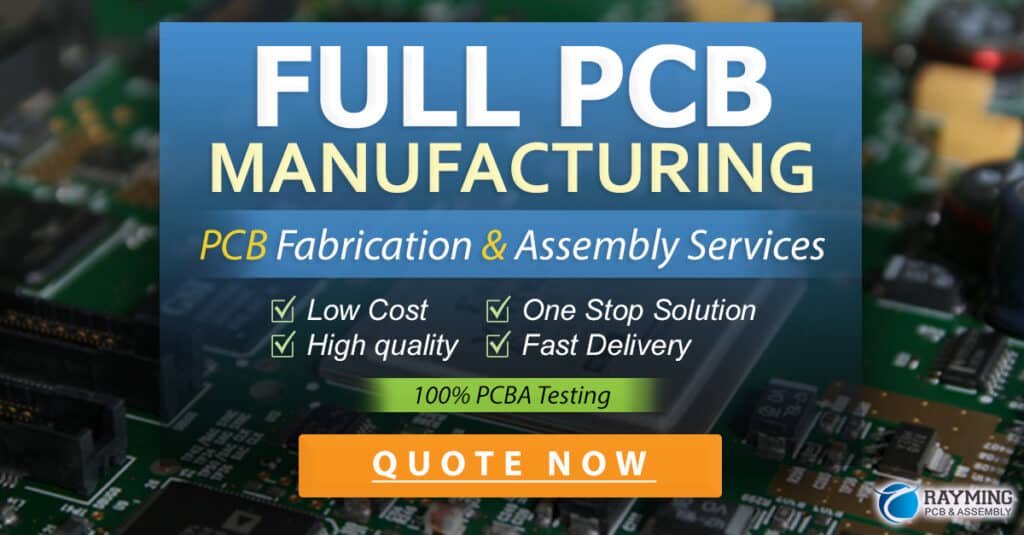
The PCB Design Process
Designing a PCB involves several stages:
-
Schematic capture: The circuit diagram is created using electronic design automation (EDA) software. This schematic represents the electrical connections between components.
-
Component placement: The physical layout of the components on the board is determined, taking into account factors such as signal integrity, thermal management, and manufacturability.
-
Routing: The conductive traces are designed to connect the components according to the schematic. This process involves determining the optimal path for each connection while adhering to design rules and constraints.
-
Design rule check (DRC): The completed design is checked against a set of predefined rules to ensure that it meets manufacturing requirements and will function as intended.
-
Gerber file generation: The final design is exported as a set of Gerber files, which are used by PCB manufacturers to fabricate the board.
Stage | Purpose |
---|---|
Schematic Capture | Create the circuit diagram using EDA software |
Component Placement | Determine the physical layout of components on the board |
Routing | Design conductive traces to connect components according to schematic |
Design Rule Check | Ensure the design meets manufacturing requirements and constraints |
Gerber File Generation | Export the final design for PCB fabrication |
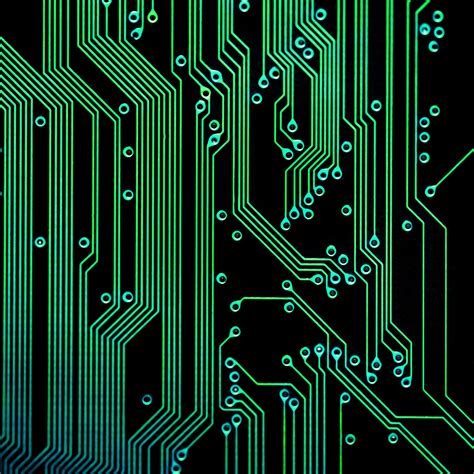
PCB Manufacturing
Once the design is finalized, the PCB is ready for manufacturing. The process typically involves the following steps:
-
Printing: The conductive pattern is printed onto the substrate using a photoresist layer and a light-sensitive film.
-
Etching: The unwanted copper is removed using a chemical etching process, leaving only the desired conductive traces.
-
Drilling: Holes are drilled into the board to accommodate through-hole components and to create vias that connect different layers.
-
Plating: A thin layer of copper is deposited onto the drilled holes to ensure proper electrical connection between layers.
-
Solder mask application: The solder mask is applied to protect the copper traces and prevent short circuits.
-
Silkscreen printing: The silkscreen layer is printed onto the board, adding text, logos, and component identifiers.
-
Surface finish: A protective finish, such as HASL (Hot Air Solder Leveling) or ENIG (Electroless Nickel Immersion Gold), is applied to the exposed copper to prevent oxidation and improve solderability.
Manufacturing Step | Purpose |
---|---|
Printing | Transfer the conductive pattern onto the substrate |
Etching | Remove unwanted copper, leaving only the desired conductive traces |
Drilling | Create holes for through-hole components and vias |
Plating | Deposit a thin layer of copper onto drilled holes for proper connection |
Solder Mask Application | Protect copper traces and prevent short circuits |
Silkscreen Printing | Add text, logos, and component identifiers |
Surface Finish | Apply a protective finish to prevent oxidation and improve solderability |
The Importance of PCBs in Modern Electronics
PCBs have revolutionized the electronics industry by enabling the creation of compact, reliable, and cost-effective electronic devices. Some of the key benefits of using PCBs include:
-
Miniaturization: PCBs allow for the dense packaging of electronic components, enabling the development of smaller and more portable devices.
-
Reliability: The robust construction and precise manufacturing processes of PCBs ensure consistent performance and longevity.
-
Cost-effectiveness: Automated assembly processes and the ability to produce PCBs in large quantities make them an economical choice for electronic products.
-
Flexibility: PCBs can be designed to fit various form factors and can be customized to meet specific application requirements.
-
Signal integrity: Proper PCB design techniques help maintain signal integrity, minimizing noise, crosstalk, and other issues that can affect the performance of electronic circuits.
Benefit | Description |
---|---|
Miniaturization | Dense packaging of components enables smaller and more portable devices |
Reliability | Robust construction and precise manufacturing ensure consistent performance |
Cost-effectiveness | Automated assembly and large-scale production make PCBs economical |
Flexibility | Customizable design to fit various form factors and application requirements |
Signal Integrity | Proper design techniques minimize noise, crosstalk, and other performance issues |
Future Trends in PCB Technology
As electronic devices continue to evolve, so does PCB technology. Some of the emerging trends in PCB design and manufacturing include:
-
Increased adoption of HDI: The demand for smaller, more powerful devices is driving the growth of HDI PCBs, which offer higher component density and improved signal integrity.
-
Advanced materials: New substrate materials, such as high-frequency laminates and ceramic-based substrates, are being developed to meet the requirements of emerging applications, such as 5G and automotive electronics.
-
Embedded components: Integrating passive components, such as resistors and capacitors, directly into the PCB substrate can save space and improve performance.
-
3D printing: Additive manufacturing techniques are being explored for PCB fabrication, potentially enabling faster prototyping and more complex geometries.
-
Environmental sustainability: There is a growing emphasis on using eco-friendly materials and processes in PCB manufacturing to reduce the environmental impact of electronic waste.
Trend | Description |
---|---|
Increased HDI Adoption | Higher component density and improved signal integrity for smaller, more powerful devices |
Advanced Materials | New substrate materials for emerging applications like 5G and automotive electronics |
Embedded Components | Integration of passive components into the PCB substrate to save space and improve performance |
3D Printing | Additive manufacturing techniques for faster prototyping and more complex geometries |
Environmental Sustainability | Focus on eco-friendly materials and processes to reduce the environmental impact of electronic waste |
Frequently Asked Questions (FAQ)
-
What is the difference between a PCB and a breadboard?
A breadboard is a prototyping tool used for temporarily building and testing electronic circuits. It allows for quick and easy changes to the circuit design. In contrast, a PCB is a permanent, manufactured board that provides a stable and reliable platform for the final electronic product. -
Can PCBs be repaired?
In some cases, PCBs can be repaired by skilled technicians. However, the feasibility of repair depends on factors such as the extent of the damage, the complexity of the circuit, and the availability of replacement components. In many cases, replacing the entire PCB is more cost-effective and reliable than attempting a repair. -
What is the difference between through-hole and surface-mount components?
Through-hole components have leads that are inserted into holes drilled in the PCB and soldered on the opposite side. Surface-mount components are placed directly onto the surface of the PCB and soldered in place. Surface-mount technology allows for smaller components and higher component density, while through-hole technology is often used for larger components or in applications where mechanical strength is a priority. -
How long does it take to manufacture a PCB?
The manufacturing time for a PCB depends on various factors, such as the complexity of the design, the number of layers, and the chosen manufacturing process. Simple, two-layer PCBs can be manufactured in as little as 24 hours, while more complex, multi-layer boards may take several weeks. On average, most PCBs can be manufactured within 1-2 weeks. -
What is the typical lifespan of a PCB?
The lifespan of a PCB depends on factors such as the quality of the materials used, the manufacturing process, and the operating environment. In general, a well-designed and properly manufactured PCB can last for several decades under normal use conditions. However, exposure to extreme temperatures, humidity, or other environmental stressors can shorten the lifespan of a PCB.
In conclusion, PCBs have played a crucial role in the development of modern electronics, enabling the creation of compact, reliable, and cost-effective devices. As technology continues to advance, PCB design and manufacturing processes will evolve to meet the ever-growing demands for smaller, faster, and more efficient electronic products. By understanding the fundamentals of PCBs, including their composition, types, and manufacturing processes, engineers and enthusiasts can better appreciate the critical role these circuit boards play in our increasingly connected world.
Leave a Reply