What is a Printed Circuit Board (PCB)?
A Printed Circuit Board is a thin, flat board made of insulating material, typically fiberglass or composite epoxy, with conductive copper traces printed on its surface. These copper traces are designed to connect the various electronic components mounted on the board, such as resistors, capacitors, integrated circuits (ICs), and connectors. The PCB acts as both a structural support and an electrical interconnect for these components.
Types of PCBs
There are several types of PCBs, each with its own unique characteristics and applications:
-
Single-sided PCB: These PCBs have copper traces on only one side of the board. They are the simplest and most cost-effective type of PCB, suitable for low-complexity circuits.
-
Double-sided PCB: These PCBs have copper traces on both sides of the board, allowing for more complex circuits and higher component density. The two sides are connected using vias, which are small holes plated with conductive material.
-
Multi-layer PCB: These PCBs consist of multiple layers of insulating material and copper traces stacked on top of each other. They offer the highest component density and are used in complex, high-performance electronic devices.
-
Flexible PCB: These PCBs are made of flexible insulating material, allowing them to bend and conform to various shapes. They are commonly used in wearable electronics, medical devices, and aerospace applications.
-
Rigid-Flex PCB: These PCBs combine the features of rigid and flexible PCBs, with rigid sections for mounting components and flexible sections for connecting them. They offer the benefits of both types of PCBs and are used in applications that require both high component density and flexibility.
PCB Type | Layers | Complexity | Cost | Applications |
---|---|---|---|---|
Single-sided | 1 | Low | Low | Simple circuits, low-power devices |
Double-sided | 2 | Medium | Medium | More complex circuits, higher component density |
Multi-layer | 3+ | High | High | Complex, high-performance devices |
Flexible | 1-2 | Medium | Medium-High | Wearable electronics, medical devices, aerospace |
Rigid-Flex | 2+ | High | High | Applications requiring both high density and flexibility |
The PCB Manufacturing Process
The PCB manufacturing process involves several steps, each of which is critical to ensuring the quality and reliability of the final product.
1. PCB design
The first step in the PCB manufacturing process is the design phase. Engineers use specialized software to create a schematic diagram of the circuit and then lay out the physical arrangement of components and copper traces on the board. This layout is then converted into a set of files that can be used to manufacture the PCB.
2. PCB fabrication
Once the PCB design is complete, the fabrication process begins. The main steps in PCB fabrication include:
-
Copper clad laminate: A thin layer of copper is bonded to the insulating substrate material.
-
Drilling: Holes are drilled into the board for mounting components and creating vias.
-
Plating: The holes are plated with a conductive material, typically copper, to create electrical connections between layers.
-
Etching: Unwanted copper is removed from the board using a chemical etching process, leaving only the desired copper traces.
-
Solder mask application: A protective layer of solder mask is applied to the board, exposing only the areas where components will be soldered.
-
Silkscreen printing: Text and symbols are printed on the board for identification and assembly purposes.
3. PCB Assembly
After the PCB is fabricated, the components are mounted on the board. This can be done using two main methods:
-
Through-hole assembly: Components with long leads are inserted into holes drilled in the board and soldered in place.
-
Surface-mount assembly: Components with small, flat contacts are placed directly on the surface of the board and soldered in place.
4. PCB Testing and Inspection
Once the PCB is assembled, it undergoes various testing and inspection procedures to ensure its functionality and quality. These may include:
-
Visual inspection: The board is visually checked for defects, such as missing components or solder bridges.
-
Automated optical inspection (AOI): An automated system uses cameras to inspect the board for defects.
-
X-ray inspection: X-rays are used to inspect the internal structure of the board, particularly for multi-layer PCBs.
-
Electrical testing: The board is powered on and tested for proper functionality, short circuits, and open connections.
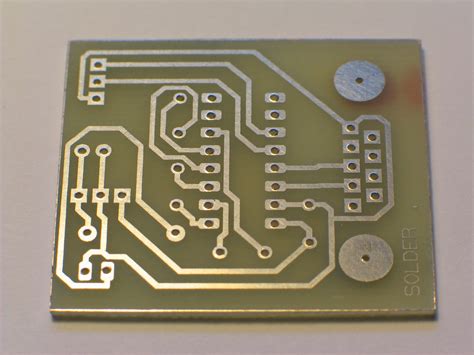
The Importance of PCBs in Modern Electronics
PCBs play a crucial role in modern electronics, enabling the creation of compact, reliable, and high-performance devices. Some of the key benefits of PCBs include:
-
Miniaturization: PCBs allow for the dense packaging of electronic components, enabling the creation of smaller, more compact devices.
-
Reliability: The robust construction and precise manufacturing of PCBs ensure high reliability and long-term performance.
-
Cost-effectiveness: PCBs enable mass production of electronic devices, reducing manufacturing costs and making technology more accessible.
-
Design flexibility: PCBs can be customized to suit the specific requirements of various applications, from consumer electronics to industrial systems.
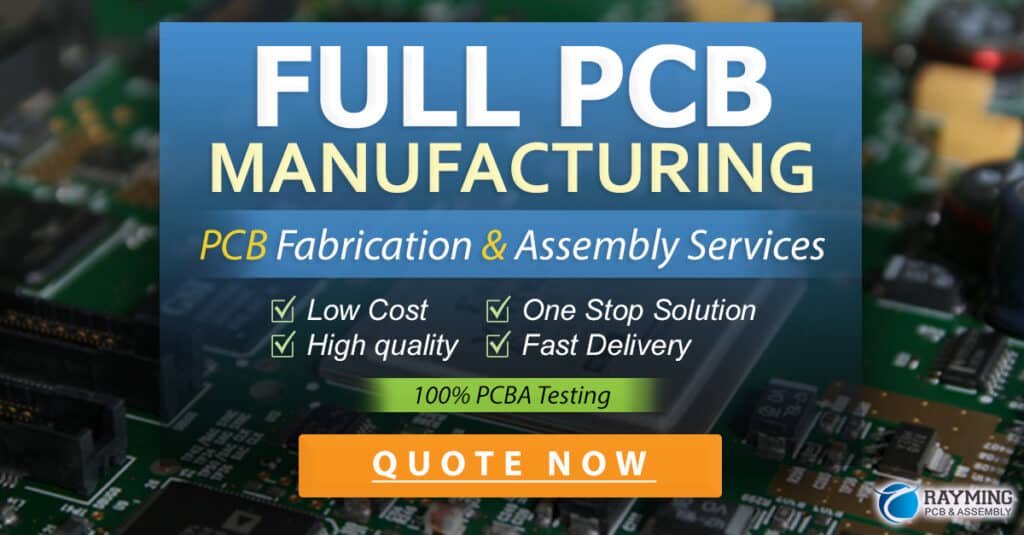
Applications of PCBs
PCBs are used in a wide range of applications across various industries, including:
-
Consumer electronics: Smartphones, tablets, laptops, televisions, and other household devices.
-
Automotive: Engine control units, infotainment systems, and advanced driver assistance systems (ADAS).
-
Medical devices: Diagnostic equipment, patient monitoring systems, and implantable devices.
-
Aerospace and defense: Avionics, satellite systems, and military communication equipment.
-
Industrial automation: Process control systems, robotics, and machine vision systems.
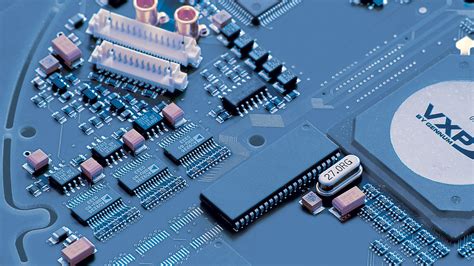
The Future of PCBs
As electronic devices continue to evolve and become more complex, PCBs will play an increasingly important role in enabling new technologies and applications. Some of the key trends shaping the future of PCBs include:
-
Miniaturization: The demand for smaller, more compact devices will drive the development of advanced PCB manufacturing techniques, such as embedded components and 3D printing.
-
High-speed design: As data rates continue to increase, PCBs will need to be designed to support higher frequencies and minimize signal integrity issues.
-
Advanced materials: New substrate materials, such as high-frequency laminates and ceramic-based PCBs, will be developed to meet the demands of emerging applications.
-
Sustainable manufacturing: There will be a growing emphasis on environmentally friendly PCB manufacturing processes and materials, such as lead-free solders and halogen-free laminates.
Frequently Asked Questions (FAQ)
-
What is the difference between a PCB and a printed wiring board (PWB)?
A PCB and a PWB are essentially the same things. The term “printed wiring board” was used in the early days of the technology, but “printed circuit board” has become the more common term in recent years. -
How long does it take to manufacture a PCB?
The lead time for PCB manufacturing depends on various factors, such as the complexity of the design, the number of layers, and the chosen manufacturing process. Simple, single-sided PCBs can be manufactured in a few days, while complex, multi-layer boards may take several weeks. -
What is the minimum feature size that can be achieved on a PCB?
The minimum feature size depends on the PCB manufacturing process and the capabilities of the manufacturer. Modern PCB fabrication techniques can achieve trace widths and spacing as small as 0.0254 mm (1 mil) or even smaller for advanced applications. -
Can PCBs be repaired if they are damaged?
In some cases, PCBs can be repaired if they are damaged. However, the feasibility of repair depends on the extent of the damage and the complexity of the board. It is often more cost-effective to replace a damaged PCB than to attempt a repair. -
How can I ensure the quality and reliability of my PCBs?
To ensure the quality and reliability of your PCBs, it is important to work with a reputable PCB manufacturer that follows strict quality control processes. Additionally, designing your PCBs with best practices in mind, such as proper component placement and signal routing, can help minimize the risk of defects and failures.
In conclusion, Printed Circuit Boards (PCBs) are essential components in modern electronics, providing a platform for connecting and supporting various electronic components. With their ability to enable miniaturization, reliability, cost-effectiveness, and design flexibility, PCBs have become indispensable in a wide range of applications, from consumer electronics to aerospace and defense. As technology continues to advance, PCBs will play a crucial role in shaping the future of electronics, driving innovation and enabling new possibilities.
Leave a Reply