Introduction to Transmission Line Impedance
Transmission lines are essential components in high-speed electronic systems, serving as the conduits for signal propagation between various components. The characteristic impedance of a transmission line is a critical parameter that determines how well signals are transmitted and received. Accurately measuring and controlling the impedance of transmission lines is crucial for ensuring signal integrity and minimizing reflections, which can lead to signal distortion and degradation.
In this article, we will explore the concept of transmission line impedance and discuss the use of printed circuit boards (PCBs) as a means to measure and characterize transmission line impedance. We will delve into the principles behind transmission line theory, the importance of impedance matching, and the various techniques and considerations involved in designing and fabricating PCBs for impedance measurement.
Understanding Transmission Line Theory
What is a Transmission Line?
A transmission line is a specialized cable or structure designed to carry electrical signals from one point to another with minimal loss and distortion. Transmission lines are commonly used in applications such as high-speed digital circuits, radio frequency (RF) systems, and telecommunications networks. They are characterized by their ability to propagate electromagnetic waves along their length while maintaining a consistent characteristic impedance.
Characteristic Impedance
The characteristic impedance of a transmission line is a fundamental property that describes the ratio of the voltage to the current traveling along the line. It is determined by the physical properties of the transmission line, such as its geometry, materials, and surrounding environment. The characteristic impedance is typically denoted by the symbol Z0 and is measured in ohms (Ω).
For a lossless transmission line, the characteristic impedance is given by the following equation:
Z0 = √(L/C)
where L is the inductance per unit length and C is the capacitance per unit length of the transmission line.
Impedance Matching
Impedance matching is a critical concept in transmission line design. When a signal encounters a change in impedance along its path, a portion of the signal is reflected back towards the source. These reflections can cause signal distortion, ringing, and other undesirable effects that degrade signal integrity.
To minimize reflections and ensure maximum power transfer, it is essential to match the impedance of the source, the transmission line, and the load. When the impedances are matched, the signal can propagate along the transmission line with minimal reflections, resulting in cleaner and more reliable signal transmission.
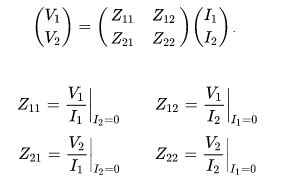
PCBs for Transmission Line Impedance Measurement
Why Use PCBs?
Printed circuit boards (PCBs) offer a convenient and effective platform for measuring and characterizing transmission line impedance. PCBs provide a controlled and repeatable environment for designing transmission line structures with specific impedance characteristics. By carefully selecting the materials, dimensions, and layout of the PCB, engineers can create transmission lines with well-defined impedances that can be easily measured and analyzed.
PCB Material Selection
The choice of PCB material is crucial for achieving accurate impedance measurements. The dielectric constant (Dk) and dissipation factor (Df) of the PCB material directly impact the impedance of the transmission lines. Common PCB materials used for impedance-controlled designs include FR-4, Rogers, and Isola.
FR-4 is a popular and cost-effective PCB material that offers good electrical and mechanical properties. However, its dielectric constant and dissipation factor can vary, making it less suitable for high-precision impedance measurements.
Rogers and Isola materials, on the other hand, offer more stable dielectric properties and are often preferred for high-frequency and impedance-sensitive applications. These materials have well-controlled dielectric constants and lower dissipation factors, enabling more accurate impedance measurements.
PCB Stack-up and Thickness
The PCB stack-up, which refers to the arrangement of conductive and dielectric layers, plays a significant role in determining the impedance of transmission lines. The thickness of the dielectric layers, along with the width and spacing of the conductive traces, directly influence the characteristic impedance.
To achieve a specific target impedance, engineers must carefully design the PCB stack-up, considering factors such as the number of layers, the thickness of each layer, and the dielectric properties of the materials used. Impedance calculators and simulation tools are often employed to optimize the stack-up design and ensure the desired impedance is achieved.
Transmission Line Geometry
The geometry of the transmission lines on the PCB is another critical factor in impedance measurement. The width, thickness, and spacing of the conductive traces determine the inductance and capacitance per unit length, which in turn affect the characteristic impedance.
Common transmission line geometries used on PCBs include microstrip, stripline, and coplanar waveguide (CPW). Each geometry has its own advantages and considerations for impedance control.
-
Microstrip: Microstrip transmission lines consist of a conductive trace on the top layer of the PCB, with a ground plane on the bottom layer. The impedance of microstrip lines is influenced by the width of the trace, the thickness of the dielectric layer, and the dielectric constant of the PCB material.
-
Stripline: Stripline transmission lines are embedded within the PCB, with conductive traces sandwiched between two ground planes. Stripline offers better shielding and isolation compared to microstrip, but requires more complex PCB fabrication.
-
Coplanar Waveguide (CPW): CPW transmission lines have a conductive trace with ground planes on either side, all on the same layer of the PCB. CPW provides good impedance control and is often used for high-frequency applications.
Impedance Measurement Techniques
Several techniques can be used to measure the impedance of transmission lines on PCBs. The most common methods include:
-
Time Domain Reflectometry (TDR): TDR measures the impedance by sending a fast rise time pulse along the transmission line and analyzing the reflections. By measuring the amplitude and timing of the reflections, the impedance profile of the transmission line can be determined.
-
Vector Network Analyzer (VNA): VNA measures the scattering parameters (S-parameters) of the transmission line over a range of frequencies. By analyzing the S-parameters, the characteristic impedance and other transmission line properties can be extracted.
-
Impedance Test Coupons: Impedance test coupons are specialized PCB structures designed specifically for impedance measurement. These coupons typically include a series of transmission line segments with known lengths and geometries. By measuring the impedance of these coupons, the impedance of the actual transmission lines can be inferred.
PCB Layout Considerations
Proper PCB layout is essential for accurate impedance measurement and control. Some key considerations include:
-
Trace Routing: Transmission line traces should be routed with consistent width and spacing to maintain a uniform impedance along their length. Avoid abrupt changes in trace geometry, as they can introduce impedance discontinuities.
-
Ground Planes: Ensure continuous and uninterrupted ground planes beneath the transmission lines to provide a stable reference for impedance control. Avoid gaps or splits in the ground plane that can affect the impedance.
-
Via Placement: Minimize the use of vias on transmission line traces, as vias can introduce impedance discontinuities. If vias are necessary, use controlled-impedance via structures or via stitching techniques to maintain impedance consistency.
-
Trace Length Matching: For differential transmission lines, ensure that the lengths of the positive and negative traces are closely matched to maintain differential impedance and minimize skew.
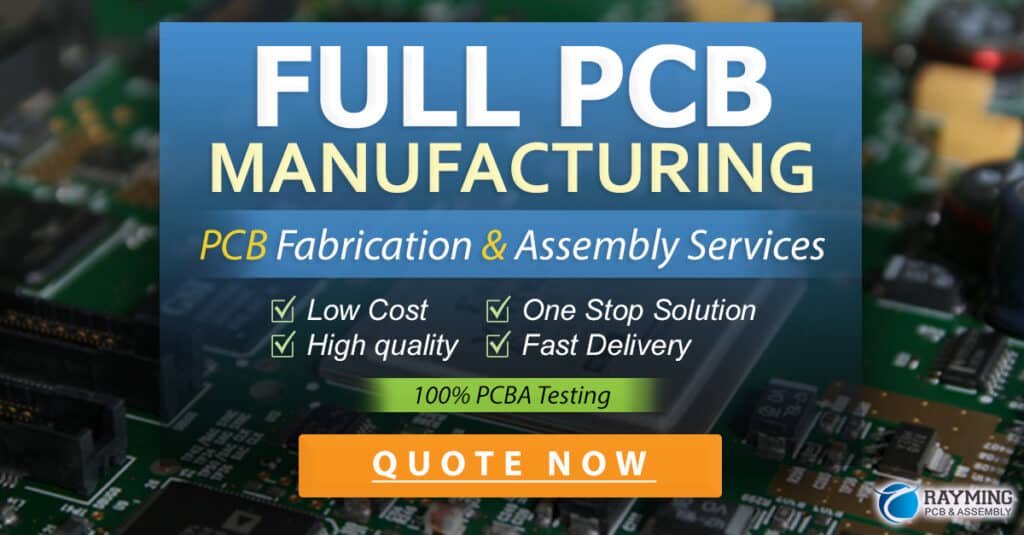
Designing PCBs for Impedance Measurement
Impedance Calculation and Simulation
Before designing PCBs for impedance measurement, it is essential to calculate the target impedance based on the system requirements and the desired transmission line geometry. Impedance calculators and simulation tools, such as Polar SI9000 or Hyperlynx, can be used to determine the necessary trace width, spacing, and dielectric thickness to achieve the target impedance.
These tools take into account the PCB material properties, stack-up, and transmission line geometry to provide accurate impedance predictions. They can also help identify potential impedance discontinuities and optimize the PCB design for better impedance control.
Impedance Test Coupon Design
Impedance test coupons are specialized PCB structures designed specifically for measuring and verifying the impedance of transmission lines. These coupons typically include a series of transmission line segments with known lengths and geometries, such as microstrip or stripline.
When designing impedance test coupons, consider the following guidelines:
- Include multiple test segments with different lengths to characterize the impedance over a range of trace lengths.
- Use the same PCB material, stack-up, and trace geometry as the actual design to ensure accurate impedance representation.
- Provide clear labeling and reference points for probing and measurement.
- Include calibration structures, such as short, open, and load standards, to calibrate the measurement equipment.
PCB Fabrication and Assembly
Once the PCB design is finalized, it is important to work closely with the PCB fabrication and assembly vendor to ensure accurate and consistent impedance control. Provide clear specifications and requirements for the PCB material, stack-up, and impedance tolerances.
During the fabrication process, the vendor should adhere to strict manufacturing guidelines, including:
- Precise control of dielectric thickness and uniformity.
- Accurate etching and patterning of conductive traces.
- Proper lamination and bonding of PCB Layers.
- Adequate testing and quality control measures to verify impedance consistency.
After fabrication, the PCB should be assembled with care to maintain the integrity of the transmission lines. Proper soldering techniques, component placement, and handling procedures should be followed to minimize any potential impact on the impedance.
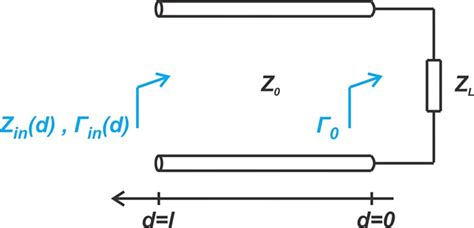
Measuring and Analyzing Impedance Results
Impedance Measurement Setup
To measure the impedance of transmission lines on a PCB, a suitable measurement setup is required. The setup typically includes:
- Measurement Equipment: TDR oscilloscope or VNA, depending on the measurement technique chosen.
- Probes and Connectors: High-quality probes and connectors that are compatible with the measurement equipment and the PCB.
- Calibration Standards: Short, open, and load calibration standards to calibrate the measurement equipment and ensure accurate results.
Measurement Procedure
The measurement procedure may vary depending on the specific measurement technique and equipment used. However, the general steps include:
-
Calibrate the measurement equipment using the calibration standards to remove any systemic errors and ensure accurate measurements.
-
Connect the probes or connectors to the impedance test coupons or transmission line segments on the PCB.
-
Configure the measurement settings, such as the pulse rise time for TDR or the frequency range for VNA.
-
Perform the impedance measurement and capture the results.
-
Analyze the measurement data to determine the characteristic impedance, impedance profile, and any impedance discontinuities.
Data Analysis and Interpretation
The measured impedance data should be carefully analyzed to assess the quality of the transmission lines and identify any issues. Some key aspects to consider include:
-
Characteristic Impedance: Compare the measured impedance values to the target impedance specified in the design. Check for consistency and any deviations from the expected value.
-
Impedance Profile: Examine the impedance profile along the length of the transmission line. Look for any abrupt changes or discontinuities that may indicate impedance mismatches or design issues.
-
Reflection Coefficient: Calculate the reflection coefficient based on the measured impedance and the system impedance. A low reflection coefficient indicates good impedance matching and minimal signal reflections.
-
Frequency Response: For VNA measurements, analyze the frequency response of the transmission line. Check for any resonances, losses, or variations in impedance over the desired frequency range.
Troubleshooting and Optimization
If the measured impedance results do not meet the desired specifications or exhibit significant issues, troubleshooting and optimization may be necessary. Some common strategies include:
-
Review the PCB design: Double-check the PCB stack-up, material properties, and transmission line geometry to ensure they match the intended design.
-
Analyze the measurement setup: Verify that the measurement equipment is properly calibrated and that the probes and connectors are in good condition.
-
Identify impedance discontinuities: Locate any impedance discontinuities or mismatches and determine their root cause, such as improper trace routing, via placement, or component placement.
-
Optimize the PCB layout: Make necessary adjustments to the PCB layout, such as modifying trace widths, spacing, or dielectric thickness, to achieve better impedance control.
-
Consider alternative materials or geometries: If the current PCB material or transmission line geometry is not providing the desired impedance characteristics, explore alternative options that may offer better performance.
Best Practices and Guidelines
To ensure accurate and reliable impedance measurements using PCBs, consider the following best practices and guidelines:
-
Use high-quality PCB materials with well-controlled dielectric properties to minimize variations in impedance.
-
Follow consistent design rules and guidelines for trace width, spacing, and routing to maintain impedance uniformity.
-
Minimize the use of vias and layer transitions on transmission line traces to reduce impedance discontinuities.
-
Provide adequate ground planes and stitching vias to ensure a stable reference plane for impedance control.
-
Use appropriate termination and matching techniques to minimize reflections and ensure proper signal integrity.
-
Conduct thorough simulations and modeling to predict and optimize the impedance characteristics before PCB fabrication.
-
Collaborate closely with PCB fabrication and assembly vendors to ensure adherence to impedance specifications and manufacturing guidelines.
-
Perform comprehensive testing and measurement to validate the impedance characteristics and identify any issues early in the design cycle.
-
Document and maintain detailed records of the impedance measurements, design files, and any modifications for future reference and troubleshooting.
Conclusion
Measuring and controlling transmission line impedance is crucial for ensuring signal integrity and reliable performance in high-speed electronic systems. PCBs provide a practical and effective platform for designing, fabricating, and measuring transmission line structures with specific impedance characteristics.
By understanding the principles of transmission line theory, selecting appropriate PCB materials and geometries, and following best practices for PCB design and measurement, engineers can accurately characterize and optimize the impedance of transmission lines.
Effective impedance control through PCB design and measurement techniques enables the development of robust and high-performance electronic systems, minimizing signal distortion, reflections, and other impedance-related issues.
As technology continues to advance and signal speeds increase, the importance of precise impedance control and measurement will only continue to grow. By staying up-to-date with the latest techniques, tools, and guidelines, engineers can effectively tackle the challenges of transmission line impedance and ensure the reliability and performance of their designs.
Frequently Asked Questions (FAQ)
-
Q: What is the importance of impedance matching in transmission lines?
A: Impedance matching is crucial for minimizing signal reflections and ensuring maximum power transfer between the source, transmission line, and load. When impedances are matched, signals can propagate along the transmission line with minimal distortion and loss, resulting in cleaner and more reliable signal transmission. -
Q: How does the choice of PCB material affect impedance measurements?
A: The choice of PCB material directly influences the impedance of transmission lines. The dielectric constant (Dk) and dissipation factor (Df) of the PCB material determine the electrical properties of the transmission line. Materials with well-controlled and stable dielectric properties, such as Rogers or Isola, are preferred for accurate impedance measurements. -
Q: What are the common transmission line geometries used on PCBs?
A: The most common transmission line geometries used on PCBs are microstrip, stripline, and coplanar waveguide (CPW). Microstrip lines have a conductive trace on the top layer and a ground plane on the bottom layer. Stripline lines are embedded within the PCB, sandwiched between two ground planes. CPW lines have a conductive trace with ground planes on either side, all on the same layer. -
Q: What is the purpose of impedance test coupons on PCBs?
A: Impedance test coupons are specialized PCB structures designed specifically for measuring and verifying the impedance of transmission lines. These coupons include a series of transmission line segments with known lengths and geometries, allowing engineers to accurately characterize the impedance of the actual transmission lines on the PCB. -
Q: What are some best practices for ensuring accurate impedance measurements on PCBs?
A: Some best practices for accurate impedance measurements on PCBs include using high-quality PCB materials with well-controlled dielectric properties, following consistent design rules for trace geometry and routing, minimizing the use of vias and layer transitions, providing adequate ground planes and stitching vias, and conducting thorough simulations and testing to validate the impedance characteristics.
Leave a Reply