What is Intrusive Soldering?
Intrusive soldering, also known as through-hole soldering, is a technique used in electronics manufacturing where electronic components are soldered directly onto a printed circuit board (PCB) by inserting their leads through holes drilled in the board. This method of soldering has been widely used for decades and remains a reliable and cost-effective solution for many applications.
Advantages of Intrusive Soldering
- Strong mechanical connection
- Easy to inspect and repair
- Suitable for high-power applications
- Cost-effective for low-volume production
Disadvantages of Intrusive Soldering
- Requires drilling holes in the PCB
- Consumes more space on the PCB
- Not suitable for high-density designs
- Slower assembly process compared to surface-mount technology (SMT)
When to Use Intrusive Soldering
1. High-Power Applications
Intrusive soldering is often the preferred method for high-power applications, such as power supplies, motor controllers, and audio amplifiers. The through-hole components used in these applications, such as large capacitors and transformers, can handle higher currents and voltages compared to their surface-mount counterparts. The strong mechanical connection provided by intrusive soldering ensures a reliable and stable connection in these demanding environments.
2. Prototyping and Low-Volume Production
When prototyping or producing small quantities of a product, intrusive soldering can be a more cost-effective solution compared to SMT. Through-hole components are generally less expensive than their surface-mount equivalents, and the assembly process can be performed manually without the need for specialized equipment. This makes intrusive soldering an attractive option for hobbyists, students, and small businesses.
3. Mechanical Stress and Vibration
In applications where the PCB is subjected to mechanical stress or vibration, intrusive soldering provides a more robust connection compared to SMT. The leads of through-hole components are inserted through the PCB and soldered on the opposite side, creating a strong mechanical bond that can withstand greater physical forces. This makes intrusive soldering suitable for applications such as automotive electronics, industrial control systems, and aerospace equipment.
4. Ease of Inspection and Repair
Intrusive soldering allows for easier visual inspection of the solder joints compared to SMT. The solder joints are visible on both sides of the PCB, making it easier to identify any defects or poor connections. Additionally, if a component needs to be replaced, it can be easily desoldered and removed without damaging the PCB or surrounding components. This ease of inspection and repair makes intrusive soldering a good choice for applications where maintainability is a key concern.
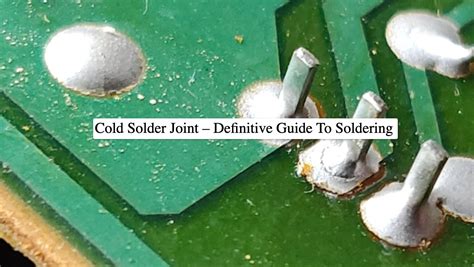
Techniques for Successful Intrusive Soldering
To ensure a reliable and high-quality solder joint when using intrusive soldering, consider the following techniques:
- Use the appropriate soldering iron tip size and temperature for the component and PCB.
- Apply a small amount of solder to the iron tip to promote heat transfer.
- Place the soldering iron tip in contact with both the component lead and the PCB pad simultaneously.
- Feed solder into the joint, allowing it to melt and flow around the lead and pad.
- Remove the soldering iron and allow the joint to cool without disturbing it.
Tip Size | Temperature | Application |
---|---|---|
0.8 mm | 320-360°C | Small components, fine-pitch leads |
1.2 mm | 360-400°C | Medium components, standard leads |
2.4 mm | 400-450°C | Large components, heavy-gauge leads |
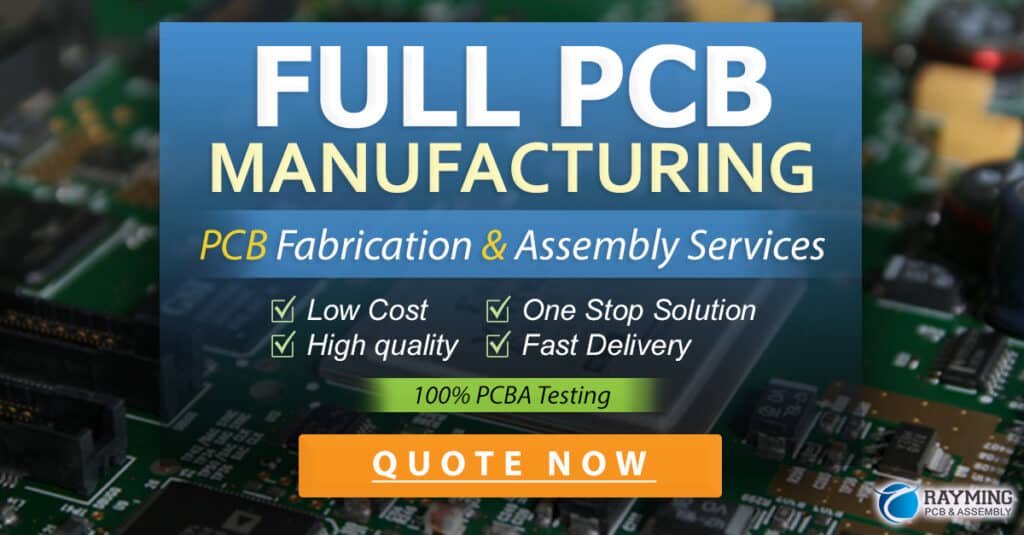
Combining Intrusive Soldering with Surface-Mount Technology
In some cases, it may be advantageous to use a combination of intrusive soldering and SMT on the same PCB. This approach allows designers to take advantage of the benefits of both technologies, such as using through-hole components for high-power or mechanically stressed parts while utilizing the space-saving and high-density capabilities of SMT for other components.
When combining intrusive soldering and SMT, consider the following:
- Design the PCB layout to accommodate both through-hole and surface-mount components.
- Ensure proper clearance between components to avoid interference during soldering.
- Use a solder mask to prevent solder bridging between closely spaced pads.
- Assemble the through-hole components first, followed by the surface-mount components.
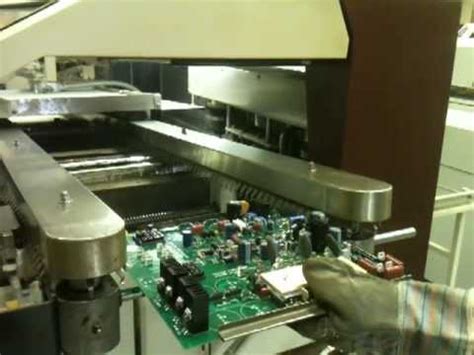
Frequently Asked Questions (FAQ)
1. Can intrusive soldering be automated?
Yes, intrusive soldering can be automated using wave soldering or selective soldering machines. Wave soldering involves passing the PCB over a molten solder wave, which solders all the through-hole components simultaneously. Selective soldering uses a focused solder fountain to solder specific components or areas on the PCB.
2. What type of solder should be used for intrusive soldering?
Tin-lead (SnPb) solder alloys, such as 63/37 or 60/40, are commonly used for intrusive soldering due to their low melting point, good wetting properties, and reliability. However, with the increasing focus on environmental regulations, lead-free solder alloys, such as SAC (tin-silver-copper) or SN100C (tin-copper-nickel), have gained popularity.
3. How can I prevent solder bridging when using intrusive soldering?
To prevent solder bridging, ensure that the component leads are properly trimmed and spaced apart. Use a soldering iron with an appropriately sized tip and avoid applying excessive solder. A solder mask can also help prevent bridging by isolating adjacent pads.
4. Can intrusive soldering be used for surface-mount components?
While intrusive soldering is primarily used for through-hole components, it can be used for certain surface-mount components with leads, such as TO-220 or TO-247 packages. However, this is less common, and SMT is generally the preferred method for surface-mount components.
5. How do I choose the right soldering iron tip size for intrusive soldering?
The soldering iron tip size should be selected based on the size of the component leads and PCB pads. A larger tip is suitable for heavy-gauge leads and large pads, while a smaller tip is better for fine-pitch leads and small pads. Refer to the table in the “Techniques for Successful Intrusive Soldering” section for guidance on tip size selection.
Conclusion
Intrusive soldering remains a valuable technique in electronics manufacturing, offering a strong mechanical connection, ease of inspection and repair, and suitability for high-power applications. While SMT has become increasingly popular, intrusive soldering still has its place in prototyping, low-volume production, and applications requiring mechanical robustness.
By understanding the advantages and limitations of intrusive soldering, as well as the techniques for successful implementation, designers and manufacturers can make informed decisions on when and how to use this soldering method effectively. Whether used alone or in combination with SMT, intrusive soldering continues to be a reliable and cost-effective solution for many electronic applications.
Leave a Reply