Introduction to Rugged PCB Enclosures
In today’s world, electronic devices are exposed to various environmental challenges, such as extreme temperatures, moisture, dust, and physical impact. To ensure the reliable operation and longevity of these devices, it is crucial to protect the sensitive printed circuit boards (PCBs) within them. This is where rugged PCB enclosures come into play. A rugged PCB enclosure is designed to provide enhanced protection against harsh conditions, ensuring the integrity and functionality of the electronic components inside.
Key Characteristics of Rugged PCB Enclosures
- Durability
- Environmental resistance
- Thermal management
- Electromagnetic interference (EMI) shielding
- Customizability
Materials Used in Rugged PCB Enclosures
Common Materials for Rugged PCB Enclosures
Material | Properties | Applications |
---|---|---|
Aluminum | Lightweight, good thermal conductivity, corrosion-resistant | Outdoor electronics, industrial control systems |
Stainless Steel | High strength, corrosion-resistant, temperature-resistant | Marine environments, food processing equipment |
Polycarbonate | Impact-resistant, lightweight, electrically insulating | Portable devices, automotive electronics |
ABS (Acrylonitrile Butadiene Styrene) | Strong, lightweight, heat-resistant | Consumer electronics, medical devices |
Selecting the Right Material for Your Application
When choosing a material for your rugged PCB enclosure, consider the following factors:
- Environmental conditions (temperature, humidity, corrosive substances)
- Mechanical requirements (impact resistance, vibration)
- Electrical properties (insulation, EMI shielding)
- Weight and portability
- Cost and manufacturability
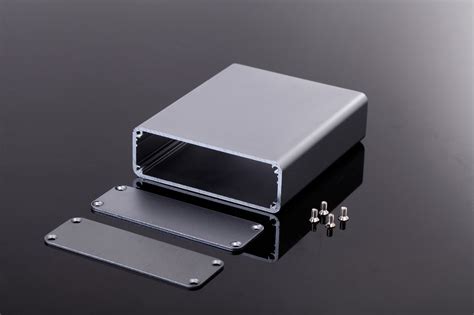
Design Considerations for Rugged PCB Enclosures
Ingress Protection (IP) Rating
The IP rating system classifies the degree of protection provided by an enclosure against the intrusion of solid objects, dust, and water. A higher IP rating indicates better protection.
IP Rating | Protection Level |
---|---|
IP54 | Protected against dust and splashing water |
IP65 | Dust-tight and protected against water jets |
IP67 | Dust-tight and protected against temporary immersion in water |
IP68 | Dust-tight and protected against continuous immersion in water |
Thermal Management
Proper thermal management is essential to prevent overheating and ensure the reliable operation of electronic components. Rugged PCB enclosures should incorporate features such as:
- Heat sinks
- Cooling fins
- Ventilation slots or fans
- Thermally conductive materials
Mechanical Strength and Vibration Resistance
Rugged PCB enclosures must withstand physical stress and vibration. Design considerations include:
- Reinforced corners and edges
- Thick walls and sturdy construction
- Shock-absorbing mounts or cushioning
- Secure fastening methods (screws, bolts, latches)
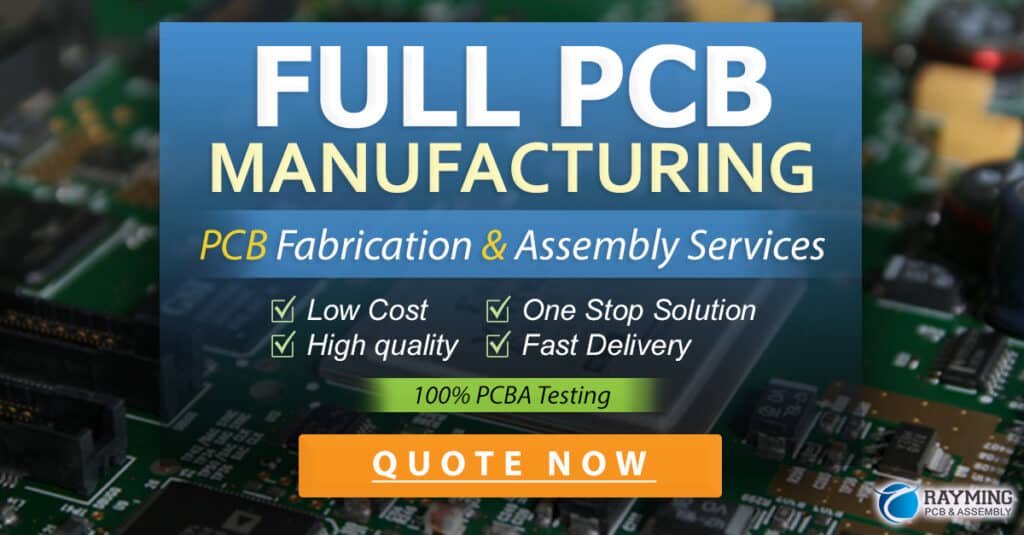
Manufacturing Techniques for Rugged PCB Enclosures
CNC Machining
CNC (Computer Numerical Control) machining is a precise and versatile manufacturing method for creating rugged PCB enclosures. It offers:
- High dimensional accuracy
- Consistent quality
- Rapid prototyping and low-volume production
- Compatibility with various materials
Injection Molding
Injection molding is a cost-effective manufacturing technique for high-volume production of rugged PCB enclosures. Benefits include:
- Rapid production of complex shapes
- Consistent quality and repeatability
- Wide range of material options
- Cost-effectiveness for large quantities
3D Printing
3D printing, also known as additive manufacturing, is an innovative method for creating custom rugged PCB enclosures. Advantages include:
- Rapid prototyping and design iterations
- Complex geometries and intricate features
- Low-volume production and customization
- Reduced lead times and tooling costs

Testing and Certification of Rugged PCB Enclosures
Environmental Testing
Rugged PCB enclosures must undergo rigorous environmental testing to ensure their performance under various conditions. Common tests include:
- Temperature cycling
- Humidity exposure
- Salt spray corrosion
- Vibration and shock testing
- Dust and water ingress testing
Compliance with Industry Standards
Rugged PCB enclosures should comply with relevant industry standards to ensure their suitability for specific applications. Some important standards include:
- MIL-STD-810: Environmental Engineering Considerations and Laboratory Tests (military)
- IEC 60529: Degrees of Protection Provided by Enclosures (IP Code)
- NEMA 250: Enclosures for Electrical Equipment (industrial)
- UL 50/50E: Enclosures for Electrical Equipment (safety)
Applications of Rugged PCB Enclosures
Industrial Automation and Control Systems
Rugged PCB enclosures are essential for industrial automation and control systems, where reliability and durability are paramount. They protect sensitive electronics from:
- Dust, dirt, and debris
- Oil, grease, and chemicals
- Extreme temperatures and humidity
- Vibration and physical impact
Aerospace and Defense Electronics
In aerospace and defense applications, rugged PCB enclosures must withstand severe environmental conditions and meet stringent reliability requirements. Key considerations include:
- Resistance to high altitudes and pressure changes
- Protection against extreme temperatures and thermal shock
- Shielding against electromagnetic interference (EMI)
- Compliance with military standards (e.g., MIL-STD-810)
Automotive Electronics
Rugged PCB enclosures play a crucial role in protecting automotive electronics from harsh conditions encountered in vehicles. They must be designed to withstand:
- Temperature fluctuations and thermal cycling
- Vibration and mechanical shock
- Exposure to moisture, salt, and chemicals
- Electromagnetic interference from other vehicle systems
Outdoor and Marine Electronics
Outdoor and marine electronics require rugged PCB enclosures that can withstand exposure to the elements. Important factors include:
- Waterproofing and corrosion resistance
- UV stability and resistance to salt spray
- Thermal management in high-temperature environments
- Impact resistance and mechanical durability
Frequently Asked Questions (FAQ)
1. What is the difference between IP65 and IP67 ratings for rugged PCB enclosures?
Both IP65 and IP67 ratings indicate that the enclosure is completely dust-tight. However, IP65 provides protection against water jets from any direction, while IP67 offers protection against temporary immersion in water (up to 1 meter for 30 minutes).
2. Can rugged PCB enclosures be customized to fit my specific application?
Yes, rugged PCB enclosures can be customized to meet the unique requirements of your application. Manufacturers offer customization options such as custom dimensions, cutouts, connectors, and finishes to ensure the best fit and functionality for your specific needs.
3. How do I choose the right material for my rugged PCB enclosure?
When selecting a material for your rugged PCB enclosure, consider factors such as environmental conditions, mechanical requirements, electrical properties, weight, and cost. Common materials include aluminum, stainless steel, polycarbonate, and ABS. Consult with a qualified enclosure manufacturer to determine the most suitable material for your application.
4. What is the role of EMI shielding in rugged PCB enclosures?
EMI (electromagnetic interference) shielding is essential in rugged PCB enclosures to protect sensitive electronic components from external electromagnetic fields and prevent the device from emitting interference that could affect other nearby electronics. Enclosures with proper EMI shielding ensure the reliable operation of the device and compliance with electromagnetic compatibility (EMC) regulations.
5. How can I ensure my rugged PCB enclosure meets the necessary industry standards?
To ensure your rugged PCB enclosure meets the required industry standards, work with a reputable manufacturer who has experience in designing and producing enclosures for your specific industry. They can guide you through the process of selecting the appropriate materials, design features, and testing procedures to ensure compliance with relevant standards such as MIL-STD-810, IEC 60529, NEMA 250, or UL 50/50E.
Conclusion
Rugged PCB enclosures are essential for protecting sensitive electronic components in harsh environments and demanding applications. By understanding the key characteristics, materials, design considerations, manufacturing techniques, testing requirements, and industry standards, you can select the most suitable rugged PCB enclosure for your specific needs. Working with experienced enclosure manufacturers and following best practices in design and testing will ensure the reliability, durability, and performance of your electronic devices in challenging conditions.
Leave a Reply