What Are Vias?
Vias are small holes that are drilled through the layers of a PCB to create electrical connections between different layers of the board. They are typically filled with a conductive material, such as copper, to allow electrical signals to pass through the board from one layer to another. Vias are an essential component of PCB design, as they allow designers to create complex circuits that would otherwise be impossible to achieve using traditional methods.
There are several different types of vias that are commonly used in PCB design, including:
Via Type | Description |
---|---|
Through-hole via | A via that extends through all layers of the PCB |
Blind via | A via that connects an outer layer to an inner layer, but does not extend through the entire board |
Buried via | A via that connects two or more inner layers, but does not extend to the outer layers of the board |
The Advantages of Via in Pad Technology
Via in Pad technology offers several significant advantages over traditional PCB design methods. Some of the key benefits include:
Reduced Board Size and Weight
By embedding vias directly within the layers of the PCB, designers can create more compact and lightweight designs. This is particularly important in applications where space and weight are at a premium, such as in mobile devices, wearables, and aerospace equipment.
Improved Signal Integrity
Via in Pad technology can help to improve signal integrity by reducing the length of the electrical paths between components. This can help to minimize signal loss and distortion, resulting in better overall performance and reliability.
Increased Design Flexibility
With Via in Pad technology, designers have greater flexibility when it comes to component placement and routing. This can allow for more complex and sophisticated designs that would be difficult or impossible to achieve using traditional methods.
Faster Time-to-Market
By simplifying the PCB design and manufacturing process, Via in Pad technology can help to reduce development times and speed up time-to-market for new products. This can be a significant advantage in today’s fast-paced and highly competitive marketplace.
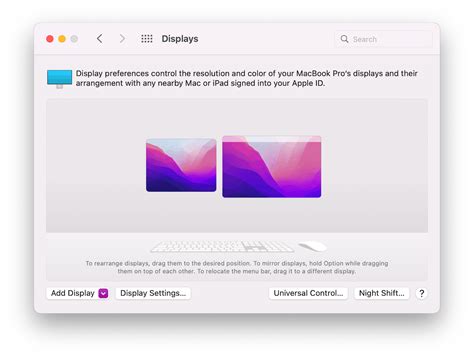
How Via in Pad Technology Works
Via in Pad technology involves the creation of vias that are embedded directly within the layers of the PCB. This is accomplished using a specialized manufacturing process that involves several key steps:
Step 1: Via Formation
The first step in the Via in Pad process is to create the vias themselves. This is typically done using a laser drilling process, which allows for the creation of very small and precise holes through the layers of the PCB.
Step 2: Via Filling
Once the vias have been created, they must be filled with a conductive material to allow electrical signals to pass through the board. This is typically done using a specialized plating process that deposits a layer of copper or other conductive material onto the walls of the via.
Step 3: Pad Formation
After the vias have been filled, the next step is to create the conductive pads that will be used to connect components to the board. This is typically done using a photolithography process, which involves the use of light-sensitive chemicals to create the desired pattern on the surface of the PCB.
Step 4: Component Placement
Once the pads have been created, the final step is to place the components onto the board and solder them in place. This is typically done using an automated pick-and-place machine, which can quickly and accurately place components onto the board in the desired locations.
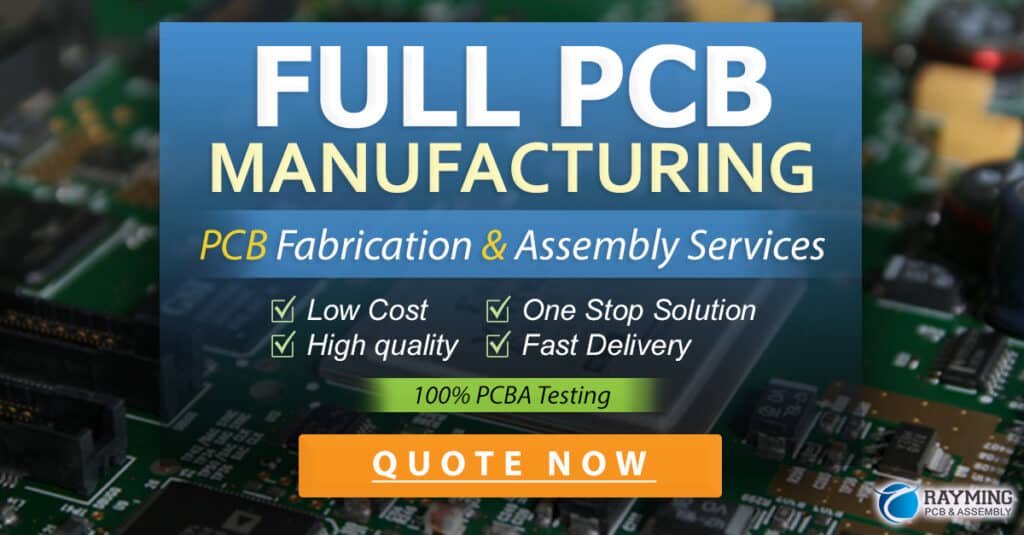
Applications of Via in Pad Technology
Via in Pad technology has found widespread use in a variety of different applications, ranging from consumer electronics to aerospace and defense. Some of the most common applications include:
Mobile Devices
Via in Pad technology is widely used in the design and manufacture of mobile devices, such as smartphones and tablets. By enabling more compact and lightweight designs, this technology has helped to drive the development of increasingly powerful and feature-rich mobile devices.
Wearables
Wearable technology, such as smartwatches and fitness trackers, also relies heavily on Via in Pad technology. By allowing for the creation of smaller and more flexible PCBs, this technology has enabled the development of wearable devices that are comfortable to wear and easy to use.
Aerospace and Defense
In the aerospace and defense industries, Via in Pad technology is used to create highly reliable and durable PCBs that can withstand the rigors of harsh environments and extreme conditions. This technology is particularly important in applications where failure is not an option, such as in military equipment and spacecraft.
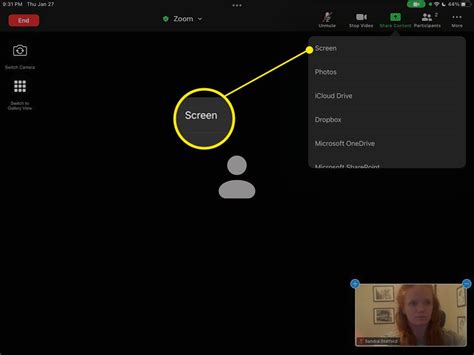
Frequently Asked Questions (FAQ)
1. What is the difference between Via in Pad and traditional PCB design?
Via in Pad technology differs from traditional PCB design in that it involves the creation of vias that are embedded directly within the layers of the board itself. This allows for more compact and lightweight designs, as well as improved signal integrity and greater design flexibility.
2. What are the benefits of using Via in Pad technology?
Some of the key benefits of Via in Pad technology include reduced board size and weight, improved signal integrity, increased design flexibility, and faster time-to-market for new products.
3. What types of applications use Via in Pad technology?
Via in Pad technology is used in a wide range of applications, including mobile devices, wearables, aerospace and defense, and more.
4. How does the Via in Pad manufacturing process work?
The Via in Pad manufacturing process involves several key steps, including via formation, via filling, pad formation, and component placement. These steps are typically carried out using specialized equipment and processes, such as laser drilling and photolithography.
5. Is Via in Pad technology more expensive than traditional PCB design?
While Via in Pad technology can be more expensive than traditional PCB design methods, the benefits it offers in terms of reduced size and weight, improved performance, and faster time-to-market can often outweigh the additional costs. Additionally, as this technology becomes more widely adopted, the costs associated with it are likely to decrease over time.
Leave a Reply