Introduction to Turnkey PCB Assembly
Turnkey PCB (Printed Circuit Board) assembly is a comprehensive service that encompasses the entire process of designing, manufacturing, and assembling printed circuit boards. This service is designed to streamline the PCB production process, allowing clients to receive fully functional and tested PCBs without the need to manage multiple vendors or handle individual stages of the manufacturing process.
In today’s fast-paced electronics industry, turnkey PCB assembly has become increasingly popular due to its efficiency, cost-effectiveness, and ability to reduce time-to-market for various products. This article will delve into the details of turnkey PCB assembly, its advantages, the process involved, and the factors to consider when choosing a turnkey PCB assembly provider.
Understanding the Basics of PCB Assembly
Before exploring turnkey PCB assembly, it is essential to understand the fundamentals of PCB assembly. A printed circuit board is a flat board made of insulating materials, such as fiberglass or plastic, with conductive pathways etched or printed onto its surface. These pathways, known as traces, connect various electronic components, such as resistors, capacitors, and integrated circuits (ICs), to form a functional electronic circuit.
PCB assembly is the process of placing and soldering these electronic components onto the printed circuit board according to a specific design. The primary methods of PCB assembly include:
- Through-hole assembly (THA): Components with long leads are inserted through holes drilled in the PCB and soldered onto the opposite side.
- Surface-mount assembly (SMA): Components with small leads or no leads at all are placed directly onto the surface of the PCB and soldered in place.
Modern PCB assembly often combines both through-hole and surface-mount techniques to accommodate a wide range of component types and sizes.
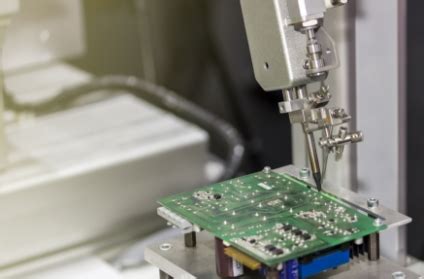
The Turnkey PCB Assembly Process
Turnkey PCB assembly involves several stages, each of which is crucial to ensuring the quality and functionality of the final product. The typical steps in the turnkey PCB assembly process include:
1. PCB Design and Prototyping
The first stage of turnkey PCB assembly is the design and prototyping phase. In this stage, the client provides the turnkey PCB assembly provider with a schematic or concept of the desired electronic circuit. The provider’s engineering team then creates a detailed PCB layout using specialized software, such as Altium Designer or OrCAD.
The PCB layout includes the placement of components, the routing of traces, and the creation of any necessary mechanical features, such as mounting holes or cutouts. Once the layout is complete, the provider may produce a prototype PCB to verify the design and functionality before proceeding to full-scale production.
2. PCB Fabrication
After the PCB design is finalized and approved, the next stage is PCB fabrication. This process involves the following steps:
a. Creating a photomask: A photomask is a transparent sheet with the PCB layout printed on it. This mask is used to transfer the layout onto the copper-clad board.
b. Applying photoresist: The copper-clad board is coated with a light-sensitive material called photoresist.
c. Exposing and developing: The photomask is placed on top of the photoresist-coated board and exposed to UV light. The exposed areas of the photoresist harden, while the unexposed areas remain soluble.
d. Etching: The board is then placed in an etching solution, which removes the copper from the areas not protected by the hardened photoresist, leaving behind the desired conductive traces.
e. Drilling: Holes are drilled into the board to accommodate through-hole components and provide connections between layers in multi-layer boards.
f. Finishing: The board undergoes various finishing processes, such as applying a solder mask to protect the copper traces and adding silkscreen labels for component identification.
3. Component Sourcing and Procurement
While the PCB is being fabricated, the turnkey PCB assembly provider sources and procures the necessary electronic components based on the bill of materials (BOM) provided by the client or generated from the PCB design. This stage involves:
a. Verifying component availability and lead times
b. Negotiating with suppliers for the best prices and delivery schedules
c. Ensuring that all components meet the required specifications and quality standards
d. Managing inventory to ensure sufficient stock for production
4. PCB Assembly
With the fabricated PCB and sourced components in hand, the turnkey PCB assembly provider proceeds to the assembly stage. This stage typically involves:
a. Solder paste application: A thin layer of solder paste is applied to the PCB’s pads using a stencil or screen printing process.
b. Component placement: Surface-mount components are placed onto the solder paste using a pick-and-place machine, while through-hole components are inserted manually or with the help of automated insertion machines.
c. Soldering: The populated PCB is then passed through a reflow oven, which melts the solder paste and creates a permanent electrical and mechanical connection between the components and the PCB.
d. Inspection: The assembled PCB undergoes visual and automated optical inspection (AOI) to identify any defects, such as misaligned components, solder bridges, or insufficient solder joints.
e. Rework and repair: If any defects are found during the inspection, the PCB is sent for rework and repair to correct the issues.
5. Testing and Quality Control
To ensure the functionality and reliability of the assembled PCBs, the turnkey PCB assembly provider conducts various tests and quality control measures, including:
a. In-circuit testing (ICT): This test verifies the presence, orientation, and value of individual components on the PCB using a bed-of-nails fixture.
b. Functional testing: The assembled PCB is powered on and subjected to a series of tests to verify its performance and functionality according to the client’s specifications.
c. Boundary scan testing: This test method, also known as JTAG testing, uses built-in test circuitry to verify the interconnections and functionality of digital components on the PCB.
d. Environmental testing: In some cases, the assembled PCBs may undergo environmental tests, such as temperature cycling, humidity exposure, or vibration testing, to ensure their durability and reliability in the intended operating conditions.
6. Packaging and Shipping
Once the assembled PCBs have passed all the necessary tests and quality control measures, they are packaged and shipped to the client. The packaging is designed to protect the PCBs from damage during transit and may include anti-static bags, bubble wrap, or custom-designed boxes.
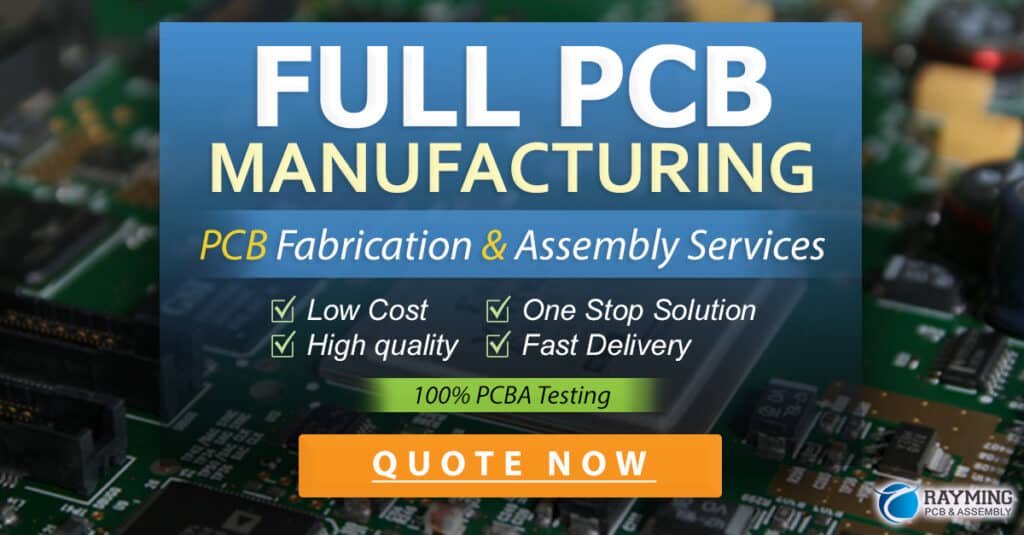
Advantages of Turnkey PCB Assembly
Turnkey PCB assembly offers several advantages over managing the PCB production process in-house or through multiple vendors:
-
Time-saving: By outsourcing the entire PCB assembly process to a single provider, clients can save significant time and effort that would otherwise be spent coordinating with multiple vendors and managing individual stages of the production process.
-
Cost-effective: Turnkey PCB assembly providers often have established relationships with component suppliers and can leverage economies of scale to obtain better pricing for components and materials. This can result in lower overall costs for the client compared to sourcing components and managing the assembly process independently.
-
Expertise and experience: Turnkey PCB assembly providers have teams of experienced engineers, technicians, and quality control professionals who are well-versed in the latest PCB design, fabrication, and assembly techniques. This expertise ensures that the assembled PCBs meet the highest quality standards and perform reliably in the intended application.
-
Access to advanced technology: Turnkey PCB assembly providers invest in state-of-the-art equipment and software to offer the most advanced PCB fabrication and assembly capabilities. This allows clients to take advantage of the latest technologies without having to invest in expensive equipment or train their own personnel.
-
Scalability: Turnkey PCB assembly providers can easily scale their production capacity to meet the client’s changing needs, from small prototype runs to large-scale production. This scalability enables clients to respond quickly to market demands and adjust their production volumes as needed.
-
Reduced risk: By entrusting the entire PCB assembly process to a single, experienced provider, clients can reduce the risk of errors, delays, or quality issues that may arise when managing multiple vendors or handling the process in-house.
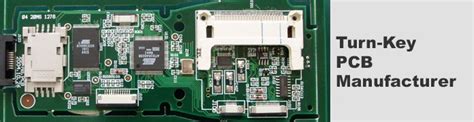
Factors to Consider When Choosing a Turnkey PCB Assembly Provider
When selecting a turnkey PCB assembly provider, clients should consider the following factors to ensure they choose a partner that can meet their specific needs and deliver high-quality results:
-
Technical capabilities: Ensure that the provider has the necessary equipment, software, and expertise to handle the specific requirements of your PCB design, such as multi-layer boards, high-density interconnects, or specialized components.
-
Quality control measures: Look for a provider that has a robust quality management system in place, with strict quality control measures and testing procedures to ensure the reliability and performance of the assembled PCBs.
-
Experience and track record: Choose a provider with a proven track record of successfully completing projects similar to yours, and consider their experience in your specific industry or application.
-
Communication and customer support: Select a provider that maintains clear and open communication throughout the project, and offers responsive customer support to address any questions or concerns that may arise.
-
Pricing and lead times: Compare pricing and lead times from multiple providers to ensure you are getting a competitive deal without compromising on quality or delivery schedules.
-
Certifications and standards: Verify that the provider adheres to relevant industry standards and certifications, such as ISO 9001 for quality management, IPC standards for PCB fabrication and assembly, or RoHS compliance for environmental regulations.
Frequently Asked Questions (FAQ)
1. What is the minimum order quantity for turnkey PCB assembly?
Minimum order quantities for turnkey PCB assembly vary among providers, but many offer low-volume production runs and even prototype quantities. Some providers specialize in high-volume production, while others cater to smaller-scale projects. It is best to discuss your specific requirements with potential providers to find one that can accommodate your needs.
2. How long does the turnkey PCB assembly process typically take?
The lead time for turnkey PCB assembly depends on several factors, such as the complexity of the PCB design, the availability of components, and the production volume. Simple PCB designs with readily available components may be assembled in as little as a few days, while more complex projects or high-volume orders may take several weeks. Most providers will provide an estimated lead time based on your specific project requirements.
3. Can turnkey PCB assembly providers handle both through-hole and surface-mount components?
Yes, most turnkey PCB assembly providers are equipped to handle both through-hole and surface-mount components. However, it is essential to communicate your specific component requirements to the provider to ensure they have the necessary equipment and expertise to accommodate your needs.
4. How can I ensure the quality of the assembled PCBs?
To ensure the quality of the assembled PCBs, choose a turnkey PCB assembly provider with a strong quality management system and strict quality control measures. Look for providers that adhere to industry standards, such as IPC, and have a track record of delivering high-quality products. Additionally, discuss your quality expectations and testing requirements with the provider upfront to ensure they can meet your needs.
5. Can turnkey PCB assembly providers assist with PCB design and component selection?
Many turnkey PCB assembly providers offer PCB design and component selection services as part of their overall offering. These providers can work with you to optimize your PCB design for manufacturability, reliability, and cost-effectiveness, and can also help you select the most suitable components for your application. However, the extent of these services may vary among providers, so it is best to inquire about their specific capabilities and experience in these areas.
Conclusion
Turnkey PCB assembly is a comprehensive service that streamlines the entire process of designing, manufacturing, and assembling printed circuit boards. By outsourcing this complex process to a single, experienced provider, clients can save time, reduce costs, and ensure the highest quality and reliability of their assembled PCBs.
When choosing a turnkey PCB assembly provider, clients should consider factors such as technical capabilities, quality control measures, experience, communication, pricing, and adherence to industry standards. By selecting the right partner, clients can leverage the many advantages of turnkey PCB assembly to bring their electronic products to market faster, more efficiently, and with greater confidence in their performance and reliability.
As the electronics industry continues to evolve and demand for high-quality, reliable PCBs grows, turnkey PCB assembly will remain an essential service for businesses of all sizes and across various sectors. By understanding the intricacies of the turnkey PCB assembly process and partnering with the right provider, companies can position themselves for success in today’s competitive market.
Characteristic | Through-hole Assembly (THA) | Surface-mount Assembly (SMA) |
---|---|---|
Component types | Components with long leads that are inserted through holes | Components with small leads or no leads, placed directly on the PCB surface |
PCB design requirements | Requires drilling holes for component leads | No holes needed, allowing for higher component density |
Assembly process | Manual or automated insertion of components through holes | Automated pick-and-place machines for high-speed assembly |
Soldering method | Wave soldering or manual soldering | Reflow soldering using solder paste and a reflow oven |
Suitability for automation | Limited automation potential due to manual insertion | Highly suitable for automated assembly processes |
PCB size and complexity | Suitable for larger, less complex PCBs | Enables smaller, more complex PCB designs with higher component density |
Rework and repair | Easier to rework and replace individual components | More challenging to rework and repair due to smaller component sizes |
Cost considerations | Higher assembly costs due to manual labor and larger PCB sizes | Lower assembly costs due to automation and smaller PCB sizes |
Leave a Reply