What is Solder Mask?
Solder mask, also known as solder resist or solder stop, is a protective coating applied to the copper traces of a PCB. Its primary purpose is to prevent accidental short circuits and protect the copper from oxidation and other environmental factors. Solder mask is typically applied as a liquid or dry film and then cured using UV light or heat.
Functions of Solder Mask
- Insulation: Solder mask acts as an insulating layer, preventing unintended electrical connections between adjacent copper traces.
- Protection: The coating shields the copper from oxidation, corrosion, and physical damage during handling and assembly.
- Aesthetics: Solder mask is available in various colors, with green being the most common. It gives the PCB a professional and finished appearance.
- Solder Control: The solder mask defines the areas where solder should be applied during the assembly process, preventing solder bridging and ensuring precise component placement.
Solder mask application Process
- Cleaning: The PCB is thoroughly cleaned to remove any contaminants or debris.
- Solder Mask Application: The liquid or dry film solder mask is applied to the PCB using screen printing, curtain coating, or photoimaging techniques.
- Curing: The solder mask is cured using UV light or heat, depending on the type of mask used.
- Inspection: The PCB is inspected for any defects or inconsistencies in the solder mask coverage.
What is Solder Paste?
Solder paste is a mixture of tiny solder particles suspended in a flux medium. It is used to form electrical and mechanical connections between components and the PCB during the surface mount assembly process. Solder paste is applied to the PCB pads using a stencil or syringe, and then the components are placed on top of the paste deposits.
Composition of Solder Paste
Solder paste consists of two main ingredients:
- Solder Alloy Particles: Tiny spheres of solder alloy, typically made of tin, lead, silver, or copper, depending on the specific application requirements.
- Flux Medium: A sticky paste that holds the solder particles in suspension and helps to clean and activate the metal surfaces during the soldering process.
Solder Paste Application Process
- Stencil Printing: A stencil with apertures corresponding to the PCB pads is aligned over the board. Solder paste is then spread across the stencil using a squeegee, depositing the paste onto the pads.
- Component Placement: Surface mount components are placed onto the solder paste deposits using pick-and-place machines or manual methods.
- Reflow Soldering: The PCB is heated in a reflow oven, causing the solder particles to melt and form a permanent bond between the components and the PCB pads.
- Inspection: The assembled PCB is inspected for any defects, such as solder bridging, insufficient solder joints, or misaligned components.
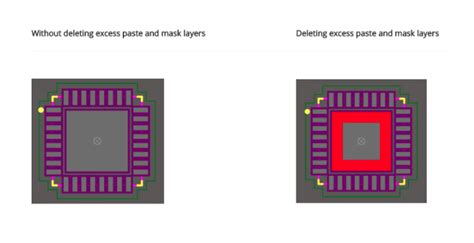
Key Differences Between Solder Mask and Solder Paste
Characteristic | Solder Mask | Solder Paste |
---|---|---|
Purpose | Insulation and protection | Forming electrical and mechanical connections |
Composition | Polymer coating | Solder alloy particles in flux medium |
Application | Liquid or dry film, applied to copper traces | Paste, applied to PCB pads |
Process Stage | PCB fabrication | PCB assembly |
Curing/Melting | UV light or heat curing | Reflow soldering |
FAQ
-
Can solder mask be used instead of solder paste?
No, solder mask and solder paste serve different purposes and cannot be used interchangeably. Solder mask is a protective coating, while solder paste is used for forming electrical connections. -
Is solder mask always green?
No, while green is the most common color for solder mask, it is available in various colors, such as red, blue, black, and white, depending on the manufacturer and customer preferences. -
What happens if solder paste is applied over solder mask?
Applying solder paste over solder mask is not recommended, as the mask will prevent the solder from forming a proper connection with the copper traces. Solder paste should only be applied to exposed PCB pads. -
Can solder paste be reused?
No, solder paste has a limited shelf life and cannot be reused once it has been exposed to air or heated. Unused solder paste should be stored in a refrigerator to extend its shelf life. -
Is it possible to have a PCB without solder mask?
Yes, it is possible to have a PCB without solder mask, but it is not recommended for most applications. The absence of solder mask leaves the copper traces exposed, increasing the risk of short circuits, oxidation, and physical damage.
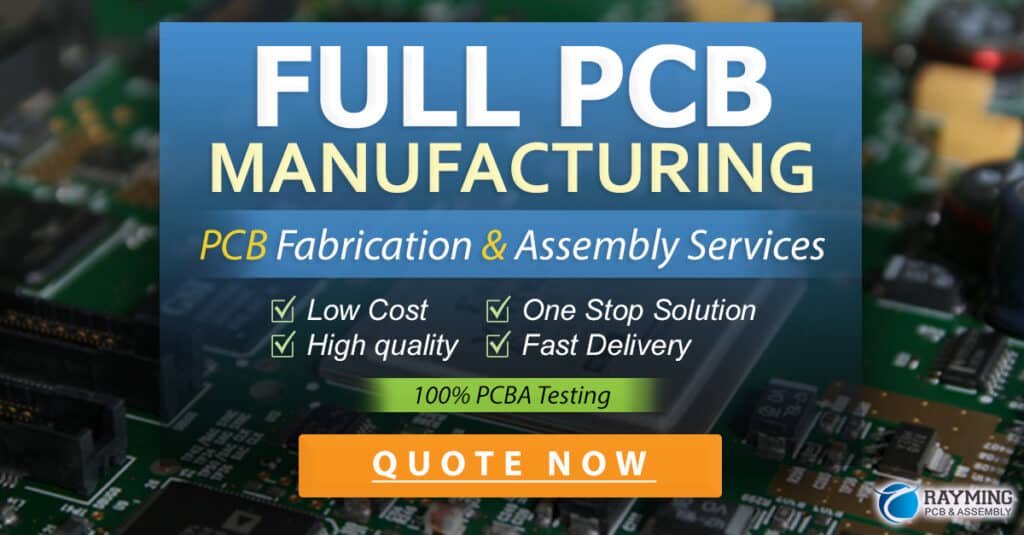
Conclusion
In summary, solder mask and solder paste are two essential materials used in the electronics manufacturing process, but they serve very different purposes. Solder mask is a protective coating applied to the copper traces of a PCB during fabrication, while solder paste is a mixture of solder particles and flux used to form electrical connections during assembly.
Understanding the difference between solder mask and solder paste is crucial for anyone involved in PCB design, fabrication, or assembly. By recognizing their distinct roles and properties, you can ensure that your PCBs are manufactured and assembled correctly, resulting in high-quality, reliable electronic products.
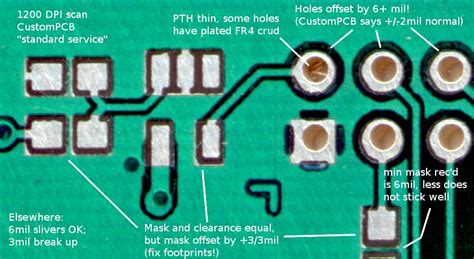
Leave a Reply