Understanding the Basics of FR4 and Rogers PCB Materials
When it comes to printed circuit board (PCB) design and manufacturing, choosing the right substrate material is crucial. Two of the most commonly used PCB materials are FR4 and Rogers. While both serve as a foundation for mounting electronic components and providing electrical connections, they have distinct characteristics that make them suitable for different applications.
What is FR4 Material?
FR4 (Flame Retardant 4) is a glass-reinforced epoxy laminate material. It is the most widely used PCB substrate material due to its cost-effectiveness, durability, and excellent electrical properties. FR4 is composed of woven fiberglass cloth impregnated with an epoxy resin binder. The “4” in FR4 represents the flammability rating, indicating that the material is self-extinguishing and does not promote flame propagation.
What is Rogers Material?
Rogers materials, on the other hand, are specialized PCB substrates designed for high-frequency and high-speed applications. Rogers Corporation, a leading manufacturer of engineered materials, offers a range of PCB laminates optimized for specific performance requirements. These materials are known for their low dielectric loss, high thermal conductivity, and excellent dimensional stability.
Key Differences Between FR4 and Rogers Materials
Dielectric Constant and Loss Tangent
One of the primary differences between FR4 and Rogers materials lies in their dielectric properties. The dielectric constant (Dk) and loss tangent (Df) are two essential parameters that describe how a material behaves in an electromagnetic field.
Material | Dielectric Constant (Dk) | Loss Tangent (Df) |
---|---|---|
FR4 | 4.2 – 4.6 | 0.02 – 0.03 |
Rogers | 2.2 – 10.2 | 0.0009 – 0.003 |
FR4 has a relatively high dielectric constant, typically ranging from 4.2 to 4.6, and a loss tangent of 0.02 to 0.03. This means that FR4 has higher dielectric losses compared to Rogers materials, which can lead to signal attenuation and reduced performance at higher frequencies.
Rogers materials, in contrast, offer a wide range of dielectric constants, from 2.2 to 10.2, depending on the specific grade. They also exhibit significantly lower loss tangents, typically in the range of 0.0009 to 0.003. This low-loss characteristic makes Rogers materials ideal for high-frequency applications where signal integrity is critical.
Thermal Management
Thermal management is another crucial factor to consider when selecting a PCB material. Efficient heat dissipation is essential to ensure the reliability and longevity of electronic components.
Material | Thermal Conductivity (W/mK) |
---|---|
FR4 | 0.3 – 0.4 |
Rogers | 0.6 – 2.5 |
FR4 has a relatively low thermal conductivity, ranging from 0.3 to 0.4 W/mK. This means that FR4 is not the best choice for applications that generate significant heat, as it may lead to thermal hot spots and reduced performance.
Rogers materials, on the other hand, offer superior thermal management properties. With thermal conductivities ranging from 0.6 to 2.5 W/mK, Rogers materials can effectively dissipate heat away from critical components. This is particularly important in high-power and high-density PCB designs.
Dimensional Stability
Dimensional stability refers to a material’s ability to maintain its shape and size under varying environmental conditions, such as temperature and humidity changes.
Material | CTE (ppm/°C) |
---|---|
FR4 | 12 – 16 |
Rogers | 8 – 20 |
FR4 has a coefficient of thermal expansion (CTE) ranging from 12 to 16 ppm/°C. This means that FR4 PCBs may experience some dimensional changes when subjected to temperature variations, which can lead to mechanical stress and potential reliability issues.
Rogers materials offer a range of CTE values, from 8 to 20 ppm/°C, depending on the specific grade. Some Rogers materials are engineered to have a CTE that closely matches that of copper (17 ppm/°C), ensuring excellent dimensional stability and reducing the risk of thermal stress-induced failures.
Cost and Availability
Cost and availability are practical considerations when choosing between FR4 and Rogers materials.
FR4 is widely available and relatively inexpensive compared to Rogers materials. It is the go-to choice for many general-purpose PCB applications where cost is a primary concern.
Rogers materials, being specialized high-performance substrates, come at a higher cost. They are typically used in demanding applications where the enhanced electrical and thermal properties justify the additional expense.
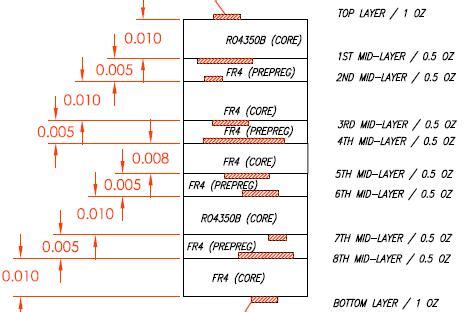
Applications of FR4 and Rogers Materials
FR4 Applications
FR4 is a versatile PCB material suitable for a wide range of applications, including:
- Consumer electronics
- Industrial control systems
- Automotive electronics
- Medical devices
- Telecommunications equipment
FR4’s cost-effectiveness, good electrical properties, and mechanical strength make it an excellent choice for many general-purpose PCB designs.
Rogers Applications
Rogers materials are specifically designed for high-frequency and high-speed applications that require superior electrical performance and thermal management. Some common applications include:
- Wireless communication systems (5G, IoT, etc.)
- Radar and satellite communications
- Automotive radar sensors
- High-speed digital circuits
- RF and microwave devices
Rogers materials’ low dielectric loss, high thermal conductivity, and dimensional stability make them the preferred choice for demanding applications where signal integrity and reliability are paramount.
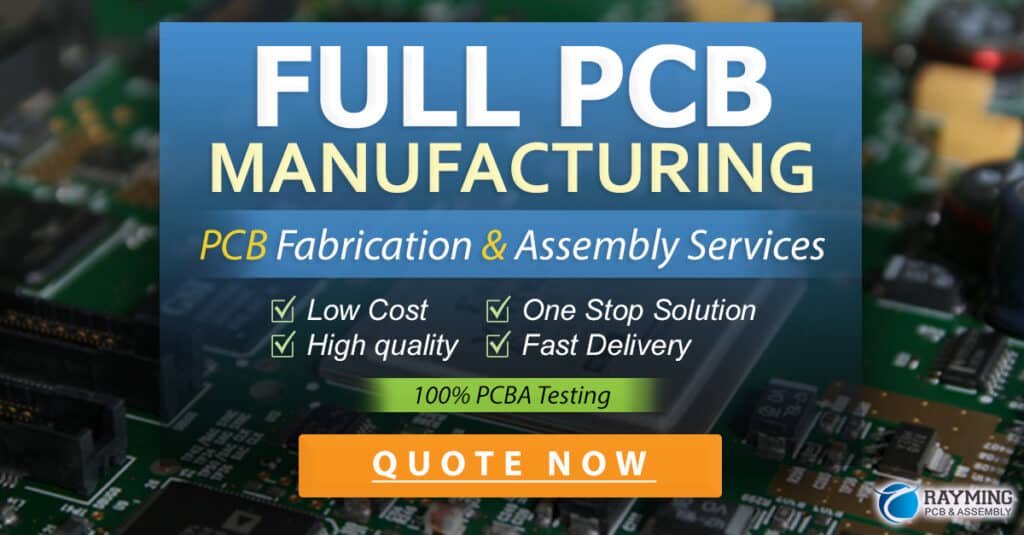
FAQ
-
Q: Can FR4 be used for high-frequency applications?
A: While FR4 can be used for some high-frequency applications, its higher dielectric loss and lower thermal conductivity may limit its performance compared to Rogers materials. FR4 is generally suitable for frequencies up to a few gigahertz, but for applications requiring higher frequencies and lower losses, Rogers materials are often the better choice. -
Q: Are Rogers materials always more expensive than FR4?
A: Yes, Rogers materials are generally more expensive than FR4 due to their specialized properties and manufacturing processes. However, the cost difference can be justified in applications where the enhanced electrical and thermal performance is critical to the overall system’s functionality and reliability. -
Q: Can Rogers materials be used for general-purpose PCB designs?
A: While Rogers materials can be used for general-purpose PCB designs, it is not always necessary or cost-effective to do so. FR4 is often sufficient for most general-purpose applications, and using Rogers materials in such cases may result in unnecessary added costs. -
Q: How do I choose between different Rogers material grades?
A: Choosing the appropriate Rogers material grade depends on the specific requirements of your application. Factors to consider include the operating frequency, dielectric constant, loss tangent, thermal conductivity, and dimensional stability needed for your design. Consult the manufacturer’s datasheets and application notes to select the most suitable Rogers material for your project. -
Q: Can FR4 and Rogers materials be combined in a single PCB design?
A: Yes, it is possible to use both FR4 and Rogers materials in a single PCB design, a technique known as hybrid stackup. This approach allows designers to leverage the benefits of both materials, using Rogers materials for critical high-frequency or high-speed sections of the board and FR4 for other areas. However, designing and manufacturing hybrid stackup PCBs requires careful consideration of the materials’ compatibility, bonding, and manufacturing processes.
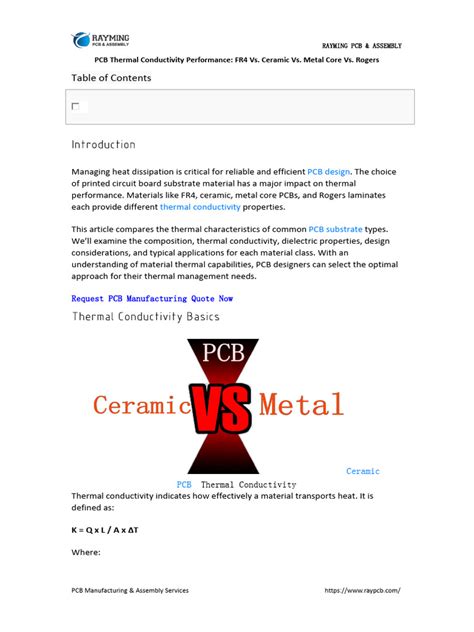
Conclusion
Understanding the differences between FR4 and Rogers materials is essential for making informed decisions when designing and manufacturing PCBs. FR4, with its cost-effectiveness and good electrical properties, is the go-to choice for many general-purpose applications. Rogers materials, on the other hand, offer superior electrical performance, low dielectric loss, high thermal conductivity, and excellent dimensional stability, making them the preferred choice for demanding high-frequency and high-speed applications.
When selecting between FR4 and Rogers materials, consider factors such as the operating frequency, signal integrity requirements, thermal management needs, and cost constraints of your specific application. By carefully evaluating these factors and consulting manufacturer datasheets and application notes, you can make the best material choice to ensure the optimal performance and reliability of your PCB design.
Leave a Reply