The Basics of PCB Design
PCB design is a complex process that requires a thorough understanding of electronics, materials, and manufacturing processes. The goal of PCB design is to create a functional and efficient Circuit Board that meets the requirements of the intended application.
Steps in PCB Design
The PCB design process typically involves the following steps:
-
Schematic Design: The first step in PCB design is to create a schematic diagram of the circuit. This involves defining the components, their connections, and the overall functionality of the circuit.
-
Component Placement: Once the schematic is complete, the next step is to place the components on the board. This involves determining the optimal location for each component based on factors such as signal integrity, power distribution, and thermal management.
-
Routing: After the components are placed, the next step is to route the traces that connect the components. This involves determining the optimal path for each trace based on factors such as signal integrity, impedance matching, and manufacturability.
-
Design Rule Check (DRC): Once the routing is complete, the design undergoes a Design Rule Check (DRC) to ensure that it meets all the necessary design rules and constraints. This includes checking for minimum trace widths, spacing, and other parameters.
-
Output Generation: After the DRC is complete, the final step is to generate the output files needed for manufacturing. This includes Gerber files, drill files, and assembly drawings.
Types of PCBs
There are several types of PCBs, each with its own unique characteristics and applications. The most common types of PCBs include:
Type | Layers | Applications |
---|---|---|
Single-sided | 1 | Simple, low-cost applications |
Double-sided | 2 | More complex applications |
Multi-layer | 3+ | High-density, high-speed applications |
Flexible | 1+ | Wearable devices, compact applications |
Rigid-Flex | 1+ | Combination of rigid and flexible sections |
PCB Design Software
PCB design software is an essential tool for creating PCBs. There are many different PCB design software packages available, each with its own strengths and weaknesses. Some of the most popular PCB design software packages include:
- Altium Designer
- KiCad
- Eagle
- OrCAD
- Cadence Allegro
When choosing a PCB design software package, it’s important to consider factors such as ease of use, features, and cost. Some software packages are more suited for beginners, while others are geared towards experienced designers.
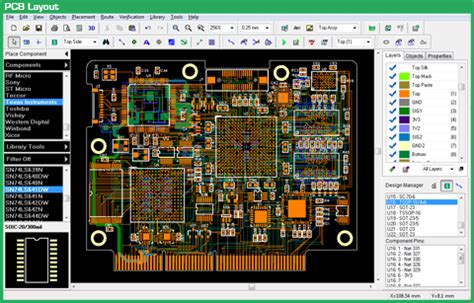
PCB Design Considerations
When designing a PCB, there are several important considerations to keep in mind. These include:
Signal Integrity
Signal integrity refers to the quality of the signals transmitted through the PCB. Poor signal integrity can lead to issues such as crosstalk, reflections, and noise. To ensure good signal integrity, designers must carefully consider factors such as trace routing, impedance matching, and termination.
Power Distribution
Power distribution is another important consideration in PCB design. The goal is to ensure that all components receive the necessary power while minimizing voltage drop and power loss. This involves careful placement of power and ground planes, as well as the use of decoupling capacitors and other power management techniques.
Thermal Management
Thermal management is critical in PCB design, especially for high-power applications. Poor thermal management can lead to component failure and reduced reliability. To ensure proper thermal management, designers must consider factors such as component placement, copper pour, and the use of thermal vias.
EMI/EMC
Electromagnetic Interference (EMI) and Electromagnetic Compatibility (EMC) are important considerations in PCB design. EMI refers to the unwanted electromagnetic energy emitted by a device, while EMC refers to a device’s ability to operate in the presence of EMI. To minimize EMI and ensure EMC, designers must carefully consider factors such as shielding, grounding, and filtering.
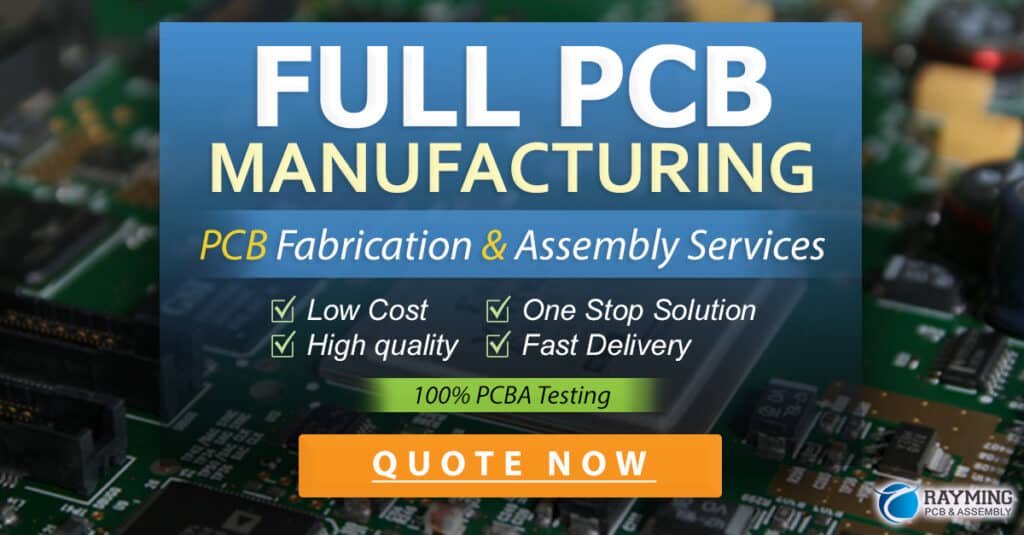
PCB Manufacturing
Once the PCB design is complete, the next step is to manufacture the board. PCB manufacturing involves several steps, including:
-
PCB Fabrication: The first step in PCB manufacturing is to fabricate the bare board. This involves creating the copper layers, drilling holes, and applying the solder mask and silkscreen.
-
Component Placement: After the bare board is fabricated, the next step is to place the components on the board. This is typically done using automated pick-and-place machines.
-
Soldering: Once the components are placed, the board is sent through a reflow oven to solder the components to the board.
-
Inspection and Testing: After the board is assembled, it undergoes inspection and testing to ensure that it meets all the necessary quality and functionality requirements.
PCB Manufacturing Considerations
When manufacturing a PCB, there are several important considerations to keep in mind. These include:
-
Material Selection: The choice of PCB material can have a significant impact on the performance and reliability of the board. Common PCB materials include FR-4, Rogers, and polyimide.
-
Copper Weight: The weight of the copper used in the PCB can affect the board’s electrical and thermal properties. Thicker copper can improve power handling and heat dissipation, but can also increase the cost and complexity of manufacturing.
-
Solder Mask and Silkscreen: The solder mask and silkscreen layers provide protection and identification for the components on the board. Careful consideration must be given to the color and placement of these layers to ensure proper functionality and aesthetics.
-
Panelization: Panelization refers to the process of arranging multiple PCBs on a single panel for manufacturing. Proper panelization can help to reduce manufacturing costs and improve yields.
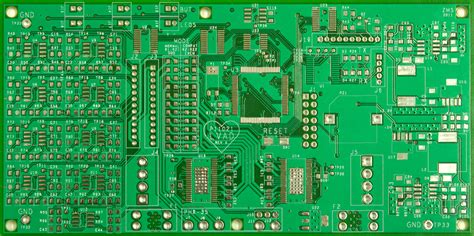
PCB Testing
After the PCB is manufactured, it must undergo testing to ensure that it meets all the necessary quality and functionality requirements. There are several types of PCB testing, including:
-
In-Circuit Testing (ICT): ICT involves testing the individual components on the board to ensure that they are functioning properly.
-
Functional Testing: Functional testing involves testing the overall functionality of the board to ensure that it meets the intended specifications.
-
Boundary Scan Testing: Boundary scan testing involves using a specialized test access port (TAP) to test the interconnections between components on the board.
-
Flying Probe Testing: Flying probe testing involves using a set of movable probes to test the board without the need for a custom test fixture.
Frequently Asked Questions (FAQ)
What is the difference between a schematic and a PCB layout?
A schematic is a diagram that shows the electrical connections between components, while a PCB layout shows the physical placement and routing of those components on the board.
What is the purpose of a solder mask?
The solder mask is a layer of polymer applied to the PCB that helps to prevent solder bridging and short circuits. It also provides protection for the copper traces on the board.
What is the difference between through-hole and surface-mount components?
Through-hole components have leads that are inserted through holes in the PCB and soldered on the opposite side, while surface-mount components are soldered directly to the surface of the board.
What is the purpose of a power plane?
A power plane is a large area of copper on the PCB that provides a low-impedance path for power distribution. It helps to reduce voltage drop and improve power integrity.
What is the difference between a rigid and a flexible PCB?
A rigid PCB is made from a solid substrate material, while a flexible PCB is made from a flexible substrate that can bend and conform to different shapes. Flexible PCBs are often used in applications where space is limited or where the board needs to be installed in a non-planar configuration.
Conclusion
PCB design is a complex and multifaceted process that requires a deep understanding of electronics, materials, and manufacturing processes. By carefully considering factors such as signal integrity, power distribution, thermal management, and EMI/EMC, designers can create functional and efficient PCBs that meet the needs of a wide range of applications.
Whether you are a seasoned PCB designer or just starting out, there is always more to learn and explore in this fascinating field. With the right tools, knowledge, and approach, anyone can become a skilled PCB designer and contribute to the ever-evolving world of electronics.
Leave a Reply