PCB vs PCBA: Understanding the Key Differences
When it comes to electronics manufacturing, two commonly used terms are PCB (Printed Circuit board) and PCBA (Printed Circuit Board Assembly). While they may sound similar, there are important distinctions between a PCB and a PCBA. In this article, we will explore the differences between PCB and PCBA in detail.
What is a PCB?
A PCB, or Printed Circuit Board, is the foundation of most electronic devices. It is a flat board made of insulating materials like fiberglass, with conductive copper traces printed on the surface. These copper traces connect various electronic components together to create a functional circuit.
PCBs are designed using specialized software that lays out the circuit diagram and translates it into a physical board design. The design is then used to manufacture the PCB through a process that involves applying a copper layer, etching away excess copper to form traces, drilling holes, and applying a protective solder mask and silkscreen layer.
Some key characteristics of PCBs include:
- Insulating substrate material (usually fiberglass)
- Copper traces for electrical connectivity
- Drilled holes for mounting components
- Solder mask layer to insulate copper traces
- Silkscreen layer for labeling components and test points
PCBs come in various types based on the number of layers, material used, and manufacturing process:
PCB Type | Description |
---|---|
Single-layer PCB | Has conductive copper traces on one side of the insulating substrate |
Double-layer PCB | Has conductive copper traces on both sides of the insulating substrate |
Multi-layer PCB | Has three or more layers of conductive copper traces separated by insulating layers |
Flexible PCB | Uses a flexible insulating substrate like polyimide, allowing the PCB to bend and flex |
Rigid-Flex PCB | Combines rigid and flexible sections in a single PCB |
High Density Interconnect (HDI) PCB | Uses smaller traces and vias to achieve higher component density |
What is a PCBA?
A PCBA, or Printed Circuit Board Assembly, is a PCB that has been populated with electronic components. It is the process of soldering or mounting components onto a bare PCB to create a functional electronic assembly.
The PCBA process involves several steps:
-
Solder Paste Application: Solder paste, a mixture of tiny solder balls and flux, is applied to the PCB’s pads using a stencil or screen printing process.
-
Component Placement: Electronic components are placed onto the PCB using automated pick-and-place machines or manual placement for smaller batches. The components are held in place by the solder paste.
-
Reflow Soldering: The PCB with components is passed through a reflow oven, which melts the solder paste, creating a permanent electrical and mechanical connection between the components and the PCB.
-
Inspection and Testing: The assembled PCBA undergoes visual inspection and electrical testing to ensure proper functionality and quality.
Some common types of components used in PCBA include:
- Surface Mount Devices (SMDs): Components that are directly soldered onto the PCB surface.
- Through-Hole Components: Components with leads that are inserted into drilled holes and soldered on the opposite side of the PCB.
- Ball Grid Array (BGA) Components: High-density components with an array of solder balls underneath for connection to the PCB.
Component Type | Mounting Method |
---|---|
Surface Mount Devices (SMDs) | Soldered directly onto PCB pads |
Through-Hole Components | Leads inserted into drilled holes and soldered |
Ball Grid Array (BGA) | Array of solder balls underneath component for high-density connection |
Key Differences Between PCB and PCBA
Now that we have a basic understanding of PCB and PCBA, let’s summarize the key differences:
- Definition:
- PCB is the bare printed circuit board without any components mounted.
-
PCBA is the assembled PCB with components soldered onto it.
-
Manufacturing Process:
- PCB manufacturing involves designing the circuit, applying copper, etching, drilling, and applying protective layers.
-
PCBA manufacturing involves applying solder paste, placing components, soldering, and testing the assembled board.
-
Functionality:
- A PCB alone does not have any functionality as it lacks components.
-
A PCBA is a functional electronic assembly that can perform its intended task.
-
Cost:
- PCBs are less expensive as they are the bare boards without components.
-
PCBAs are more expensive as they include the cost of components and the assembly process.
-
Design Considerations:
- PCB design focuses on the layout of copper traces, component footprints, and electrical characteristics.
-
PCBA design considers component selection, placement, soldering methods, and assembly process optimization.
-
Testing:
- PCBs undergo basic continuity and electrical tests to ensure trace integrity and proper manufacturing.
- PCBAs require thorough functional testing, boundary scan testing, and in-circuit testing to verify proper operation.
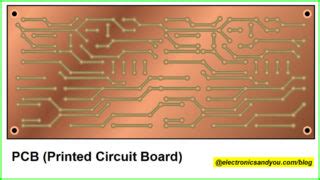
Applications of PCB and PCBA
PCBs and PCBAs find applications in a wide range of industries and products. Some common applications include:
- Consumer Electronics:
- Smartphones, tablets, laptops, and wearables
- Home appliances and smart home devices
-
Gaming consoles and peripherals
-
Automotive Electronics:
- Engine control units (ECUs)
- Infotainment systems and displays
-
Advanced driver assistance systems (ADAS)
-
Medical Devices:
- Diagnostic equipment and imaging systems
- Patient monitoring devices
-
Implantable devices and wearable health monitors
-
Industrial Automation:
- Programmable logic controllers (PLCs)
- Sensors and actuators
-
Industrial robots and machine controllers
-
Aerospace and Defense:
- Avionics systems and flight controllers
- Radar and communication equipment
-
Satellites and spacecraft electronics
-
Internet of Things (IoT):
- Connected sensors and devices
- Wireless communication modules
- Edge computing hardware
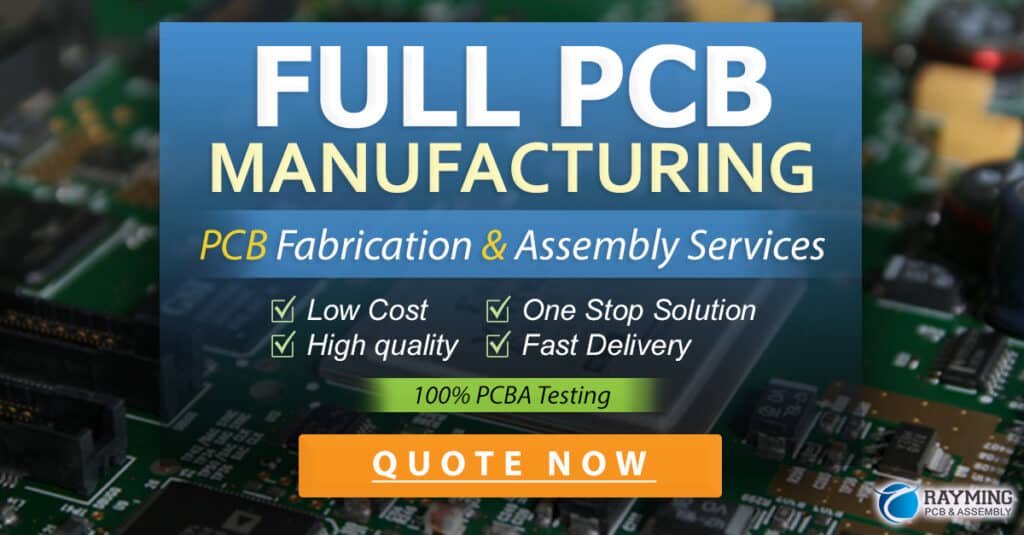
Advantages of PCBAs over PCBs
While PCBs are the foundation of electronic devices, PCBAs offer several advantages:
-
Functionality: PCBAs are fully functional electronic assemblies ready to be integrated into a device or system. They eliminate the need for additional assembly steps by the end-user.
-
Reliability: PCBAs are assembled using automated processes and undergo thorough testing, ensuring higher reliability compared to manually assembled circuits.
-
Miniaturization: PCBAs allow for high-density component placement, enabling smaller and more compact electronic devices.
-
Cost-effectiveness: Although PCBAs are more expensive than bare PCBs, they offer cost savings in terms of reduced assembly time and labor costs for the end-user.
-
Scalability: PCBAs can be mass-produced using automated assembly lines, making them suitable for high-volume production and scalability.
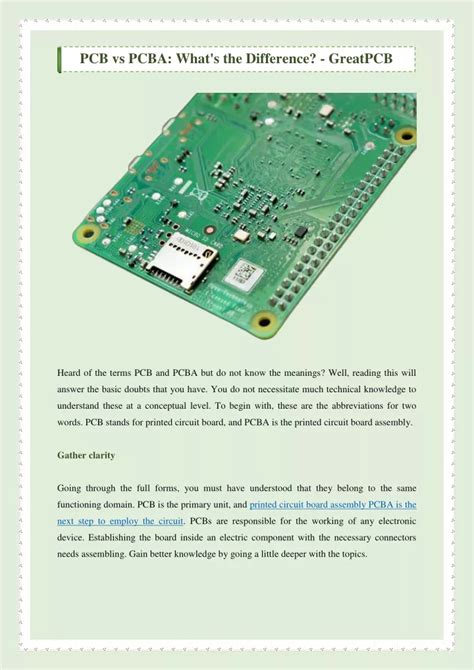
Choosing Between PCB and PCBA
The choice between using a PCB or a PCBA depends on various factors:
- Project Requirements:
- If the project requires a basic circuit without components, a PCB may suffice.
-
If the project needs a functional electronic assembly, a PCBA is necessary.
-
In-House Capabilities:
- If the company has the necessary equipment and expertise for assembly, using a PCB and performing in-house assembly may be feasible.
-
If the company lacks assembly capabilities, outsourcing PCBA manufacturing is more practical.
-
Cost and Time Constraints:
- PCBs are less expensive and faster to manufacture compared to PCBAs.
-
PCBAs offer cost savings in terms of reduced assembly time and labor but have higher upfront costs.
-
Volume and Scalability:
- For low-volume or prototype projects, using PCBs and manual assembly may be suitable.
-
For high-volume production, PCBAs offer scalability and automated assembly advantages.
-
Intellectual Property Protection:
- If the project involves sensitive intellectual property, using a PCBA with pre-programmed components can help protect the IP.
- PCBs expose the circuit design and may require additional measures to safeguard IP.
Frequently Asked Questions (FAQ)
- Can a PCB be used without components?
-
A: No, a PCB alone cannot function without components. It requires components to be mounted and soldered to create a functional electronic assembly (PCBA).
-
Are all PCBAs made from PCBs?
-
A: Yes, all PCBAs are built using PCBs as the foundation. The PCB is populated with components to create the PCBA.
-
Can PCBAs be repaired or reworked?
-
A: Yes, PCBAs can be repaired or reworked by skilled technicians. Common rework processes include replacing faulty components, resoldering connections, and modifying the circuit if necessary.
-
How long does it take to manufacture a PCBA?
-
A: The manufacturing time for a PCBA depends on various factors such as the complexity of the design, the number of components, and the manufacturer’s production capacity. Typically, PCBA manufacturing can take several days to a few weeks.
-
Are there any industry standards for PCB and PCBA manufacturing?
- A: Yes, there are several industry standards that govern PCB and PCBA manufacturing. Some common standards include IPC (Association Connecting Electronics Industries) standards, such as IPC-A-610 for acceptability of electronic assemblies and IPC-6012 for qualification and performance of rigid PCBs.
Conclusion
Understanding the difference between PCB and PCBA is crucial for anyone involved in electronics manufacturing or product development. While PCBs are the bare boards that form the foundation of electronic devices, PCBAs are the assembled boards with components soldered onto them, creating functional electronic assemblies.
PCBs and PCBAs have distinct manufacturing processes, costs, and design considerations. The choice between using a PCB or a PCBA depends on project requirements, in-house capabilities, cost and time constraints, production volume, and intellectual property protection needs.
By comprehending the key differences between PCB and PCBA, stakeholders can make informed decisions, optimize designs, and streamline manufacturing processes to create reliable and cost-effective electronic products.
As technology continues to advance, the demand for high-quality PCBs and PCBAs will only grow. Staying updated with the latest manufacturing techniques, materials, and industry standards is essential to remain competitive in the ever-evolving world of electronics.
Leave a Reply