The Role of a PCB in Electronic Devices
Providing a Stable Platform for Components
One of the primary functions of a PCB is to provide a stable platform for mounting electronic components. The PCB serves as a base upon which various components, such as resistors, capacitors, integrated circuits (ICs), and connectors, are soldered or attached. This stable platform ensures that the components remain securely in place, even when the device is subjected to vibrations, shocks, or other external forces.
The PCB’s surface is typically made of a non-conductive material, such as fiberglass or plastic, which provides electrical insulation between the components. This insulation prevents short circuits and ensures that the electrical signals travel only along the designated paths, known as traces or tracks.
Facilitating Electrical Connections
Another crucial function of a PCB is to facilitate electrical connections between components. The PCB features a network of conductive traces, usually made of copper, that are etched or printed onto the board’s surface. These traces act as pathways for electrical signals to travel between components, allowing them to communicate and interact with each other.
The layout of the traces on a PCB is carefully designed to minimize signal interference, ensure proper signal integrity, and optimize the overall performance of the electronic device. The width, thickness, and spacing of the traces are determined based on factors such as the current carrying capacity, signal frequency, and electromagnetic compatibility (EMC) requirements.
Providing Mechanical Support
In addition to providing a stable platform for components, PCBs also offer mechanical support to the electronic device. The PCB acts as a structural element, helping to distribute the weight of the components evenly and maintain the device’s shape and rigidity.
Many PCBs feature mounting holes, which allow them to be securely attached to the device’s enclosure or chassis. This mechanical support is particularly important in devices that are subject to physical stress, such as portable electronics or industrial equipment.
Enabling Heat Dissipation
Electronic components generate heat during operation, which can lead to performance degradation or even damage if not properly managed. PCBs play a vital role in enabling heat dissipation, helping to maintain the optimal operating temperature of the components.
The PCB’s copper traces and planes not only facilitate electrical connections but also serve as heat spreaders, conducting heat away from the components. Additionally, PCBs can incorporate thermal management features, such as heat sinks, thermal vias, or metal core substrates, to enhance heat dissipation and prevent overheating.
Facilitating Modularity and Scalability
PCBs enable modularity and scalability in electronic devices by allowing designers to break down complex systems into smaller, more manageable modules. Each module can be designed as a separate PCB, with its own set of components and functions, and then interconnected with other modules to form a complete system.
This modular approach offers several benefits, including easier maintenance, upgradability, and customization. If a particular module fails or needs to be updated, it can be replaced or upgraded without affecting the entire system. Moreover, modular PCB designs enable scalability, allowing manufacturers to create different product variants or configurations by combining different modules as needed.
Types of PCBs and Their Functions
There are several types of PCBs, each designed to serve specific functions and meet different requirements. Let’s explore some of the most common types of PCBs and their primary responsibilities.
Single-Layer PCBs
Single-layer PCBs, also known as single-sided PCBs, have conductive traces on only one side of the board. These PCBs are the simplest and most cost-effective type, making them suitable for basic, low-density electronic devices.
Characteristic | Single-Layer PCB |
---|---|
Layers | One |
Density | Low |
Cost | Low |
Complexity | Simple |
Single-layer PCBs are commonly used in applications such as:
– Simple consumer electronics (e.g., toys, calculators)
– Low-power devices (e.g., LED lights, simple sensors)
– Prototyping and educational projects
Double-Layer PCBs
Double-layer PCBs, also referred to as double-sided PCBs, have conductive traces on both sides of the board. These PCBs offer higher component density and more complex routing capabilities compared to single-layer PCBs.
Characteristic | Double-Layer PCB |
---|---|
Layers | Two |
Density | Medium |
Cost | Moderate |
Complexity | Moderate |
Double-layer PCBs are used in a wide range of applications, such as:
– Consumer electronics (e.g., smartphones, laptops)
– Industrial control systems
– Automotive electronics
– Medical devices
Multi-Layer PCBs
Multi-layer PCBs consist of three or more conductive layers, with insulating layers sandwiched between them. These PCBs offer the highest component density and the most complex routing capabilities, making them suitable for advanced electronic devices with high functionality and performance requirements.
Characteristic | Multi-Layer PCB |
---|---|
Layers | Three or more |
Density | High |
Cost | High |
Complexity | High |
Multi-layer PCBs are commonly used in applications such as:
– High-end consumer electronics (e.g., gaming consoles, smart TVs)
– Telecommunications equipment
– Aerospace and defense systems
– High-performance computing devices
Flexible PCBs
Flexible PCBs, also known as flex PCBs, are made from flexible substrate materials, such as polyimide or polyester. These PCBs can bend, fold, or twist without damaging the conductive traces or components, making them ideal for applications that require flexibility or space-saving designs.
Characteristic | Flexible PCB |
---|---|
Flexibility | High |
Density | Medium to High |
Cost | High |
Durability | High |
Flexible PCBs are used in various applications, including:
– Wearable electronics
– Medical implants and devices
– Aerospace and military equipment
– Robotics and automation systems
Rigid-Flex PCBs
Rigid-flex PCBs combine the benefits of both rigid and flexible PCBs, featuring rigid sections connected by flexible sections. This hybrid design allows for three-dimensional packaging and improved reliability in applications that require both stability and flexibility.
Characteristic | Rigid-Flex PCB |
---|---|
Flexibility | Selective |
Density | High |
Cost | Very High |
Complexity | Very High |
Rigid-flex PCBs are commonly used in applications such as:
– Aerospace and defense systems
– Medical devices
– High-density electronics with limited space
– Automotive electronics
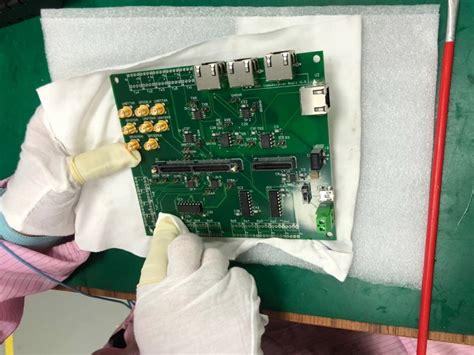
PCB Design Considerations
To ensure that a PCB effectively performs its functions, several design considerations must be taken into account. These considerations help to optimize the PCB’s performance, reliability, and manufacturability.
Component Placement
Proper component placement is crucial for ensuring the optimal performance and reliability of a PCB. Components should be placed in a way that minimizes signal interference, reduces the length of traces, and facilitates efficient routing. Additionally, components that generate significant heat should be placed in areas with adequate thermal management, such as near heat sinks or thermal vias.
Trace Routing
The routing of traces on a PCB plays a critical role in signal integrity and electromagnetic compatibility. Traces should be designed with appropriate width, thickness, and spacing to minimize signal loss, crosstalk, and electromagnetic interference (EMI). High-speed signals may require specialized routing techniques, such as matched-length traces or controlled impedance routing, to maintain signal integrity.
Power and Ground Management
Effective power and ground management is essential for the stable operation of a PCB. Power and ground planes should be designed to provide low-impedance paths for current flow and minimize voltage drops across the board. Decoupling capacitors should be placed close to power-hungry components to suppress high-frequency noise and prevent voltage fluctuations.
Electromagnetic Compatibility (EMC)
PCBs must be designed to meet electromagnetic compatibility (EMC) requirements, ensuring that they do not emit excessive electromagnetic interference (EMI) and can operate reliably in the presence of external electromagnetic fields. EMC considerations include proper grounding, shielding, and filtering techniques, as well as adherence to relevant EMC standards and regulations.
Manufacturing and Assembly
PCB design must also consider manufacturing and assembly requirements to ensure the board can be efficiently and reliably produced. This includes factors such as component footprints, solder pad sizes, and design for manufacturability (DFM) guidelines. Designers should work closely with PCB manufacturers and assembly partners to optimize the design for production and minimize potential issues.
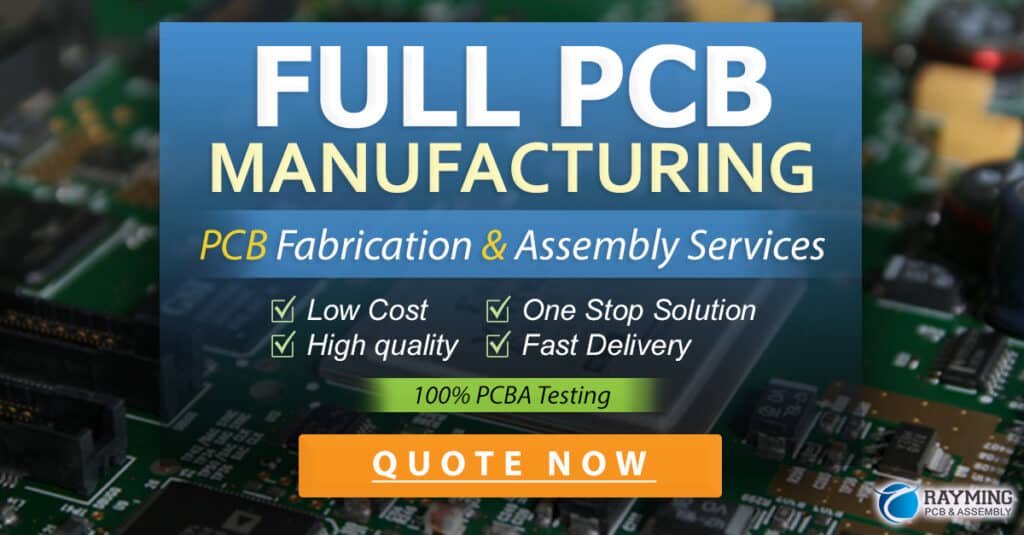
Frequently Asked Questions (FAQ)
-
What is the primary function of a PCB?
The primary function of a PCB is to provide a stable platform for mounting electronic components and facilitate electrical connections between them. -
How do PCBs enable heat dissipation in electronic devices?
PCBs enable heat dissipation through their copper traces and planes, which act as heat spreaders, conducting heat away from components. Additionally, PCBs can incorporate thermal management features, such as heat sinks or thermal vias, to enhance heat dissipation. -
What are the benefits of using multi-layer PCBs?
Multi-layer PCBs offer several benefits, including high component density, complex routing capabilities, improved signal integrity, and better electromagnetic compatibility. They are suitable for advanced electronic devices with high functionality and performance requirements. -
What is the importance of proper component placement on a PCB?
Proper component placement on a PCB is crucial for minimizing signal interference, reducing trace lengths, facilitating efficient routing, and ensuring adequate thermal management. It helps to optimize the PCB’s performance and reliability. -
Why is electromagnetic compatibility (EMC) an important consideration in PCB design?
Electromagnetic compatibility (EMC) is important in PCB design to ensure that the board does not emit excessive electromagnetic interference (EMI) and can operate reliably in the presence of external electromagnetic fields. Adhering to EMC standards and implementing proper grounding, shielding, and filtering techniques help to achieve EMC compliance.
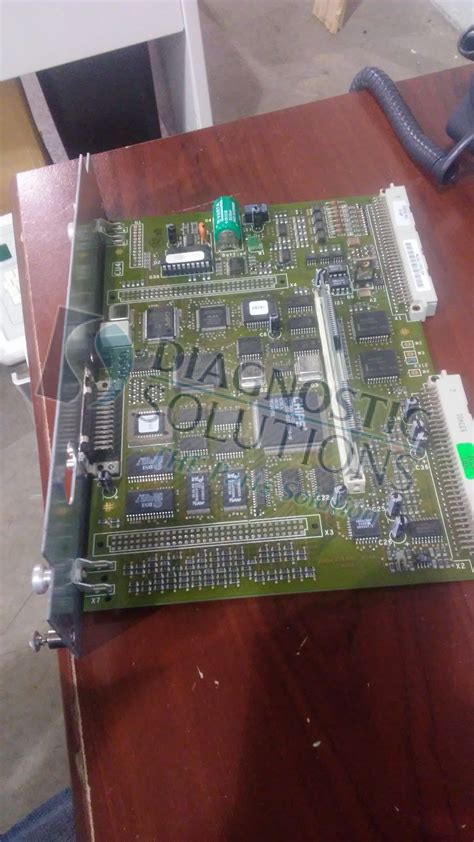
Conclusion
In conclusion, a PCB is responsible for several critical functions that enable the proper operation of electronic devices. It provides a stable platform for mounting components, facilitates electrical connections, offers mechanical support, enables heat dissipation, and facilitates modularity and scalability. Different types of PCBs, such as single-layer, double-layer, multi-layer, flexible, and rigid-flex PCBs, cater to various application requirements and offer specific benefits.
To ensure that a PCB effectively performs its functions, designers must consider factors such as component placement, trace routing, power and ground management, electromagnetic compatibility, and manufacturing and assembly requirements. By carefully addressing these design considerations, PCB designers can create boards that are optimized for performance, reliability, and manufacturability.
As electronic devices continue to evolve and become more sophisticated, the role of PCBs in enabling their functionality remains crucial. Advancements in PCB technology, such as the use of high-frequency materials, embedded components, and 3D printing, are opening up new possibilities for PCB design and expanding their capabilities. As a result, PCBs will continue to play a vital role in shaping the future of electronics, enabling the development of innovative and efficient devices across a wide range of industries.
Leave a Reply