Introduction
When it comes to mounting heatsinks on electronic components, choosing the right thermal interface material (TIM) is crucial for efficient heat dissipation. The two most common options are thermal pads and thermal paste. In this article, we will explore the differences between thermal pads and thermal paste, their advantages and disadvantages, and help you determine the best choice for your specific application.
What are Thermal Pads?
Thermal pads, also known as thermal interface pads, are pre-cut, compressible sheets of material designed to fill the gaps between a heatsink and the heat-generating component. They are typically made of silicone or other polymeric materials filled with thermally conductive particles, such as ceramic or graphite.
Advantages of Thermal Pads
- Easy to use: Thermal pads are pre-cut and can be easily applied to the surface of the component without the need for spreading or curing.
- No mess: Unlike thermal paste, thermal pads do not require any cleaning or removal of excess material after application.
- Electrical insulation: Most thermal pads are electrically insulating, which can help prevent short circuits and damage to components.
- Gap-filling properties: Thermal pads are designed to conform to surface irregularities, making them ideal for applications with larger gaps between the heatsink and the component.
Disadvantages of Thermal Pads
- Lower thermal conductivity: Compared to high-quality thermal pastes, thermal pads generally have lower thermal conductivity, which can result in slightly higher temperatures.
- Limited thickness options: Thermal pads are available in a limited range of thicknesses, which may not be suitable for all applications.
- Higher cost: Thermal pads are often more expensive than thermal paste, especially for larger surface areas.
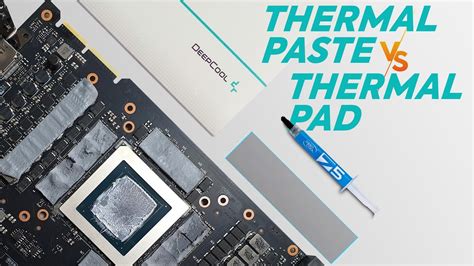
What is Thermal Paste?
Thermal paste, also known as thermal grease or thermal compound, is a viscous substance applied between a heatsink and a heat-generating component to enhance heat transfer. It is composed of a base material, such as silicone or oil, mixed with thermally conductive particles, such as silver, aluminum, or zinc oxide.
Advantages of Thermal Paste
- High thermal conductivity: High-quality thermal pastes offer excellent thermal conductivity, ensuring efficient heat transfer from the component to the heatsink.
- Versatility: Thermal paste can be applied to various surface sizes and shapes, making it suitable for a wide range of applications.
- Low cost: Thermal paste is generally less expensive than thermal pads, especially for smaller surface areas.
- Thin bond line: Thermal paste can create a very thin layer between the heatsink and the component, minimizing the thermal resistance.
Disadvantages of Thermal Paste
- Application process: Applying thermal paste requires more effort and skill compared to thermal pads, as it needs to be evenly spread across the surface of the component.
- Messy cleanup: Excess thermal paste needs to be cleaned from the surrounding area after application, which can be a messy process.
- Electrical conductivity: Some thermal pastes contain electrically conductive particles, which can cause short circuits if not applied carefully.
- Pump-out and dry-out: Over time, thermal paste can deteriorate due to pump-out (being squeezed out from between the surfaces) or dry-out, reducing its effectiveness.
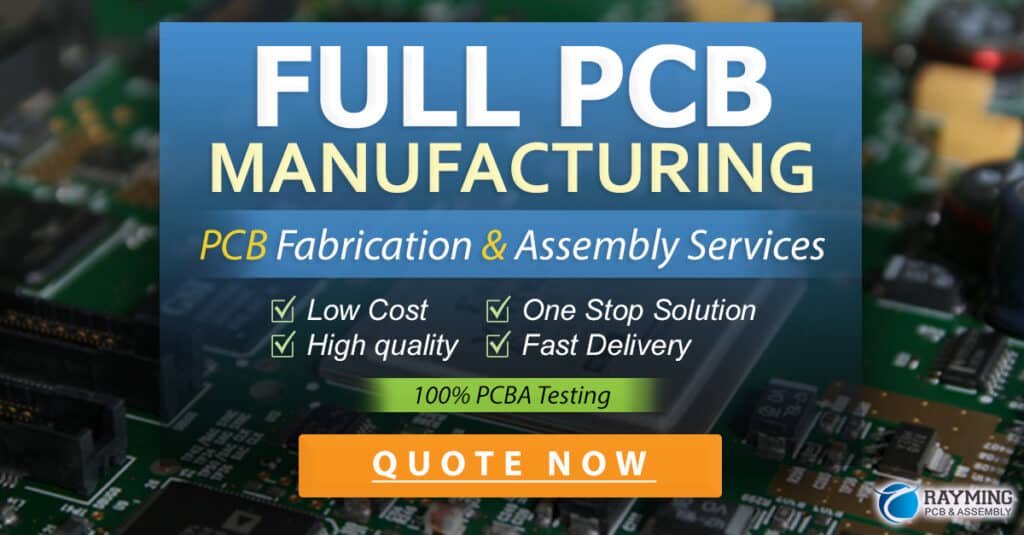
Thermal Conductivity Comparison
One of the key factors in choosing between thermal pads and thermal paste is their thermal conductivity. The following table compares the typical thermal conductivity ranges for various thermal interface materials:
Thermal Interface Material | Thermal Conductivity (W/mK) |
---|---|
Thermal Pads | 1.0 – 6.0 |
Standard Thermal Paste | 2.0 – 5.0 |
High-Performance Thermal Paste | 5.0 – 12.0 |
Liquid Metal Thermal Paste | 30.0 – 80.0 |
As seen in the table, high-performance thermal pastes offer significantly higher thermal conductivity compared to thermal pads. However, it is essential to note that the actual performance of a TIM also depends on factors such as bond line thickness, surface roughness, and pressure applied during installation.
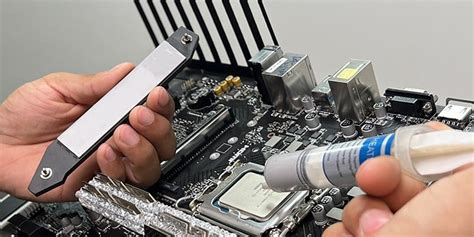
Application Techniques
Applying Thermal Pads
- Clean the surfaces of the heatsink and the component to remove any dust, dirt, or old thermal material.
- Cut the thermal pad to the required size, ensuring it covers the entire surface of the component without overlapping.
- Remove the protective film from one side of the thermal pad and place it on the surface of the component.
- Remove the protective film from the other side of the thermal pad and carefully place the heatsink on top, applying even pressure to ensure proper contact.
Applying Thermal Paste
- Clean the surfaces of the heatsink and the component to remove any dust, dirt, or old thermal material.
- Apply a small amount of thermal paste to the center of the component’s surface.
- Use a spreader or a credit card to evenly distribute the thermal paste across the entire surface, creating a thin and uniform layer.
- Carefully place the heatsink on top of the component, applying even pressure to ensure proper contact.
- Remove any excess thermal paste from the surrounding area using a lint-free cloth or cotton swab.
Choosing Between Thermal Pads and Thermal Paste
When deciding between thermal pads and thermal paste, consider the following factors:
- Surface irregularities: If the surfaces of the heatsink and the component are not perfectly flat or have significant gaps, thermal pads may be a better choice due to their gap-filling properties.
- Thermal performance: If maximum heat dissipation is required, high-performance thermal paste is generally the best option, as it offers higher thermal conductivity compared to thermal pads.
- Ease of use: Thermal pads are easier to apply and do not require any cleaning after installation, making them a good choice for beginners or quick installations.
- Cost: Thermal paste is usually more cost-effective for smaller surface areas, while thermal pads may be more economical for larger applications.
- Electrical insulation: If electrical insulation is a concern, thermal pads are the safer choice, as they are generally non-conductive.
Maintenance and Reapplication
Over time, both thermal pads and thermal paste can degrade, leading to reduced thermal performance. It is essential to regularly check the temperatures of your components and replace the thermal interface material when necessary.
For thermal pads, replacement is recommended if:
– The pad has become hardened or brittle
– There are visible signs of wear or damage
– The component’s temperature has significantly increased
For thermal paste, replacement is recommended if:
– The paste has dried out or become crumbly
– There are visible signs of pump-out or unevenness
– The component’s temperature has significantly increased
When replacing thermal pads or thermal paste, always clean the surfaces thoroughly using isopropyl alcohol or a dedicated cleaning solution to ensure optimal thermal contact.
Frequently Asked Questions (FAQ)
- Can I use thermal pads and thermal paste together?
-
While it is possible to use both thermal pads and thermal paste together, it is generally not recommended. Using both materials can lead to uneven pressure distribution and may actually decrease thermal performance.
-
Are thermal pads reusable?
-
Thermal pads are generally not reusable, as they can become compressed and lose their effectiveness after being installed. It is best to use a new thermal pad each time you remount a heatsink.
-
How much thermal paste should I apply?
-
A pea-sized amount of thermal paste is usually sufficient for most applications. Applying too much thermal paste can actually decrease thermal performance, as the excess material can act as an insulator.
-
Can I use thermal pads or thermal paste on a GPU or CPU?
-
Both thermal pads and thermal paste can be used on GPUs and CPUs. However, for optimal thermal performance, high-quality thermal paste is generally recommended, especially for high-end processors and graphics cards.
-
Do thermal pads and thermal paste expire?
- Thermal pads and thermal paste can degrade over time, even if unopened. Most manufacturers provide a shelf life for their products, which is typically around 2-5 years. It is best to use thermal interface materials before their expiration date to ensure optimal performance.
Conclusion
Choosing between thermal pads and thermal paste depends on various factors, such as surface irregularities, thermal performance requirements, ease of use, cost, and electrical insulation needs. While thermal pads offer convenience and gap-filling properties, thermal paste generally provides better thermal conductivity and is more versatile. By understanding the advantages and disadvantages of each option and considering your specific application, you can make an informed decision to ensure optimal heat dissipation and protect your electronic components from thermal damage.
Leave a Reply