Introduction
In the world of industrial automation and control systems, two of the most commonly used technologies are Programmable Logic Controllers (PLCs) and Embedded Systems. While both have their strengths and weaknesses, PLCs are often chosen over Embedded Systems despite their higher cost per unit. In this article, we will explore the reasons why PLCs are preferred in certain situations and when it makes sense to choose a PLC over an Embedded System.
What is a PLC?
A Programmable Logic Controller (PLC) is a computer-based control system that is designed to control industrial processes and machines. PLCs are highly reliable, rugged, and designed to withstand harsh industrial environments. They are programmed using ladder logic, a programming language that is easy to learn and understand, even for those without extensive programming experience.
Advantages of PLCs
-
Reliability: PLCs are designed to operate continuously, even in harsh industrial environments. They have a high tolerance for temperature, vibration, and electrical noise, making them ideal for use in industrial settings.
-
Ease of programming: PLCs are programmed using ladder logic, which is a simple and intuitive programming language. This makes it easy for technicians and engineers to program and maintain PLCs, even if they do not have extensive programming experience.
-
Scalability: PLCs are highly scalable and can be easily expanded to accommodate additional inputs and outputs as needed. This makes them ideal for use in large-scale industrial applications.
-
Interoperability: PLCs are designed to communicate with a wide range of devices and systems, including sensors, actuators, and other PLCs. This makes it easy to integrate PLCs into existing industrial control systems.
Disadvantages of PLCs
-
Higher cost per unit: PLCs are generally more expensive than Embedded Systems on a per-unit basis. This is due to their rugged design, extensive feature set, and high reliability.
-
Limited processing power: PLCs are designed for real-time control applications and may not have the processing power needed for complex data analysis or machine learning applications.
-
Proprietary hardware and software: Many PLCs use proprietary hardware and software, which can limit interoperability and make it difficult to integrate PLCs with other systems.
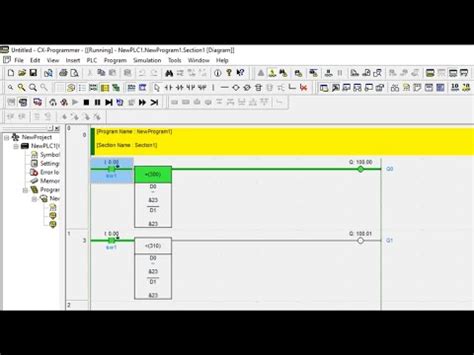
What is an Embedded System?
An Embedded System is a computer system that is designed to perform a specific function within a larger mechanical or electrical system. Embedded Systems are typically smaller and less expensive than PLCs and are often used in consumer electronics, medical devices, and automotive applications.
Advantages of Embedded Systems
-
Lower cost per unit: Embedded Systems are generally less expensive than PLCs on a per-unit basis. This is due to their simpler design and less extensive feature set.
-
Flexibility: Embedded Systems can be customized to meet the specific needs of a particular application. This makes them ideal for use in specialized or niche applications.
-
Small size: Embedded Systems are typically smaller than PLCs, making them ideal for use in space-constrained applications.
-
Low power consumption: Embedded Systems are designed to operate on low power, making them ideal for use in battery-powered or energy-constrained applications.
Disadvantages of Embedded Systems
-
Limited scalability: Embedded Systems are typically designed for a specific application and may not be easily expandable or scalable.
-
Limited interoperability: Embedded Systems may not be designed to communicate with other devices or systems, making it difficult to integrate them into larger control systems.
-
Complexity: Embedded Systems often require specialized programming skills and knowledge of the specific hardware being used. This can make them more difficult to program and maintain than PLCs.
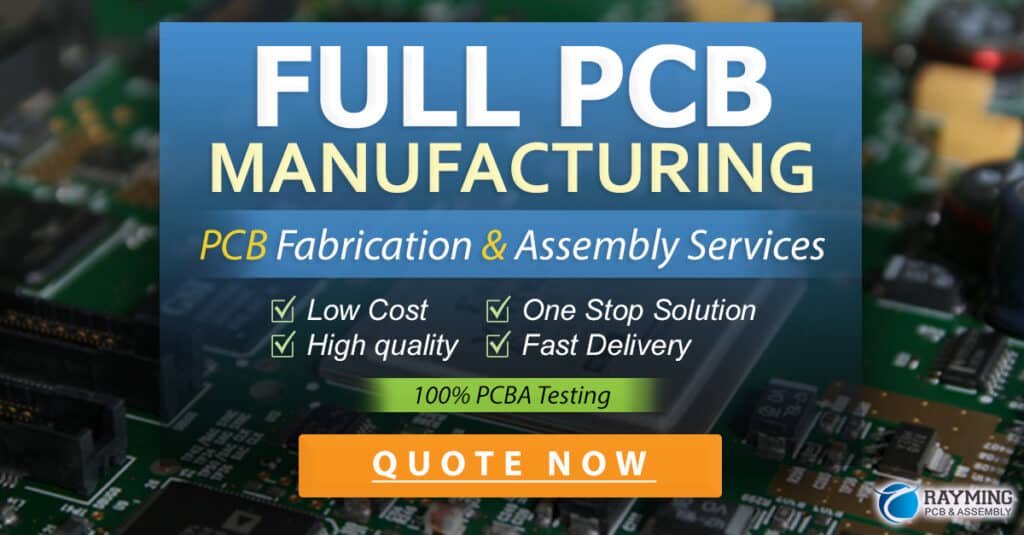
When to Choose a PLC Over an Embedded System
Despite their higher cost per unit, there are several situations where it makes sense to choose a PLC over an Embedded System. Here are a few examples:
1. Industrial Control Applications
PLCs are the preferred choice for industrial control applications due to their ruggedness, reliability, and ease of programming. PLCs are designed to withstand harsh industrial environments and can operate continuously for years without failure. They are also easy to program using ladder logic, which makes them accessible to a wide range of technicians and engineers.
2. Large-Scale Applications
PLCs are highly scalable and can be easily expanded to accommodate additional inputs and outputs as needed. This makes them ideal for use in large-scale industrial applications, such as manufacturing plants, power generation facilities, and water treatment plants.
3. Applications Requiring Interoperability
PLCs are designed to communicate with a wide range of devices and systems, including sensors, actuators, and other PLCs. This makes them ideal for use in applications that require interoperability with existing control systems or equipment.
4. Applications Requiring High Reliability
PLCs are designed for high reliability and are often used in applications where downtime is not an option. This includes applications such as power generation, oil and gas production, and transportation systems.
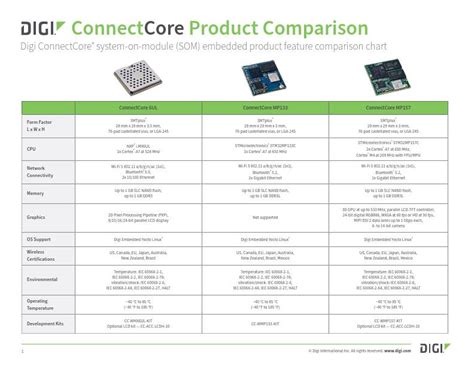
When to Choose an Embedded System Over a PLC
While PLCs are the preferred choice for many industrial control applications, there are situations where an Embedded System may be a better choice. Here are a few examples:
1. Cost-Sensitive Applications
Embedded Systems are generally less expensive than PLCs on a per-unit basis, making them a good choice for cost-sensitive applications. This includes applications such as consumer electronics, medical devices, and automotive systems.
2. Space-Constrained Applications
Embedded Systems are typically smaller than PLCs, making them ideal for use in space-constrained applications. This includes applications such as mobile devices, wearable technology, and aerospace systems.
3. Low Power Applications
Embedded Systems are designed to operate on low power, making them ideal for use in battery-powered or energy-constrained applications. This includes applications such as remote monitoring systems, wireless sensors, and portable medical devices.
4. Specialized Applications
Embedded Systems can be customized to meet the specific needs of a particular application, making them a good choice for specialized or niche applications. This includes applications such as robotics, machine vision, and scientific instrumentation.
Comparison Table: PLC vs Embedded System
Feature | PLC | Embedded System |
---|---|---|
Cost per unit | Higher | Lower |
Reliability | High | Moderate |
Scalability | High | Limited |
Interoperability | High | Limited |
Programming | Ladder Logic | C, C++, Assembly |
Size | Larger | Smaller |
Power Consumption | Higher | Lower |
Customization | Limited | High |
Frequently Asked Questions (FAQ)
1. What is the main difference between a PLC and an Embedded System?
The main difference between a PLC and an Embedded System is their intended use. PLCs are designed for industrial control applications and are highly reliable, scalable, and easy to program using ladder logic. Embedded Systems are designed for specific functions within a larger system and are typically smaller, less expensive, and more customizable than PLCs.
2. Can a PLC be used in a space-constrained application?
While PLCs are larger than Embedded Systems, they can still be used in space-constrained applications if the benefits of using a PLC (such as reliability and interoperability) outweigh the size constraints. However, in general, Embedded Systems are a better choice for space-constrained applications.
3. Can an Embedded System be used for industrial control applications?
While Embedded Systems can be used for industrial control applications, they may not be the best choice in many cases. PLCs are specifically designed for industrial control applications and offer higher reliability, scalability, and interoperability than Embedded Systems.
4. What programming languages are used for PLCs and Embedded Systems?
PLCs are typically programmed using ladder logic, which is a simple and intuitive programming language that is easy to learn and understand. Embedded Systems are typically programmed using languages such as C, C++, or Assembly, which require more specialized programming skills and knowledge of the specific hardware being used.
5. How do I choose between a PLC and an Embedded System for my application?
The choice between a PLC and an Embedded System depends on the specific requirements of your application. Factors to consider include cost, reliability, scalability, interoperability, size, power consumption, and customization. In general, PLCs are a good choice for industrial control applications that require high reliability, scalability, and interoperability, while Embedded Systems are a good choice for cost-sensitive, space-constrained, or specialized applications.
Conclusion
In conclusion, while PLCs and Embedded Systems both have their strengths and weaknesses, PLCs are often the preferred choice for industrial control applications despite their higher cost per unit. PLCs offer high reliability, scalability, interoperability, and ease of programming using ladder logic, making them ideal for use in harsh industrial environments and large-scale applications.
However, there are situations where an Embedded System may be a better choice, such as cost-sensitive, space-constrained, or specialized applications. Ultimately, the choice between a PLC and an Embedded System depends on the specific requirements of your application, and careful consideration should be given to factors such as cost, reliability, scalability, interoperability, size, power consumption, and customization.
By understanding the strengths and weaknesses of PLCs and Embedded Systems, and considering the specific requirements of your application, you can make an informed decision about which technology is best suited for your needs. Whether you choose a PLC or an Embedded System, both technologies have the potential to greatly improve the efficiency, reliability, and performance of your industrial control system.
Leave a Reply