Introduction to PCB Surface Finishes
Printed Circuit Boards (PCBs) are the backbone of modern electronic devices, providing a platform for interconnecting electronic components. The outer layer surface finish of a PCB plays a crucial role in ensuring reliable soldering, protection from environmental factors, and maintaining signal integrity. In this article, we will explore the various PCB surface finishes available, their characteristics, advantages, and considerations for selecting the most suitable finish for your PCB design.
Types of PCB Surface Finishes
1. Hot Air Solder Leveling (HASL)
HASL is one of the most common and cost-effective PCB surface finishes. In this process, the PCB is dipped into a molten solder bath, and then hot air is used to level the solder on the surface. HASL provides good solderability and is compatible with a wide range of components.
Advantages:
– Cost-effective
– Good solderability
– Suitable for both through-hole and surface-mount components
Disadvantages:
– Uneven surface due to solder dipping process
– Not suitable for fine-pitch components
– Potential for solder bridging
2. Organic Solderability Preservative (OSP)
OSP is a chemical coating applied to the copper pads of a PCB to prevent oxidation and maintain solderability. It is a thin, transparent layer that does not significantly affect the PCB’s thickness or flatness.
Advantages:
– Flat surface finish
– Suitable for fine-pitch components
– Cost-effective
– Environmentally friendly
Disadvantages:
– Limited shelf life (6-12 months)
– Sensitive to handling and moisture
– Not suitable for multiple reflow processes
3. Electroless Nickel Immersion Gold (ENIG)
ENIG is a two-layer surface finish consisting of a nickel layer plated onto the copper, followed by a thin gold layer. The nickel layer provides a barrier against copper diffusion, while the gold layer protects the nickel from oxidation and ensures good solderability.
Advantages:
– Flat surface finish
– Excellent solderability
– Long shelf life
– Suitable for fine-pitch components
– Good wire bonding capabilities
Disadvantages:
– Higher cost compared to HASL and OSP
– Potential for “black pad” defect due to improper plating process
– Gold can dissolve into solder during reflow, affecting joint reliability
4. Immersion Silver (IAg)
Immersion silver is a chemical process that deposits a thin layer of silver onto the copper pads of a PCB. It offers good solderability and is a cost-effective alternative to ENIG.
Advantages:
– Flat surface finish
– Good solderability
– Cost-effective compared to ENIG
– Suitable for fine-pitch components
Disadvantages:
– Tarnishes over time, affecting solderability
– Not suitable for high-temperature applications
– Can be affected by sulfur-containing atmospheres
5. Immersion Tin (ISn)
Immersion tin is a chemical process that deposits a thin layer of tin onto the copper pads of a PCB. It provides good solderability and is often used as a lead-free alternative to HASL.
Advantages:
– Flat surface finish
– Good solderability
– Suitable for fine-pitch components
– Lead-free and RoHS compliant
Disadvantages:
– Tin whiskers can form over time, causing short circuits
– Limited shelf life compared to ENIG
– Not suitable for high-temperature applications
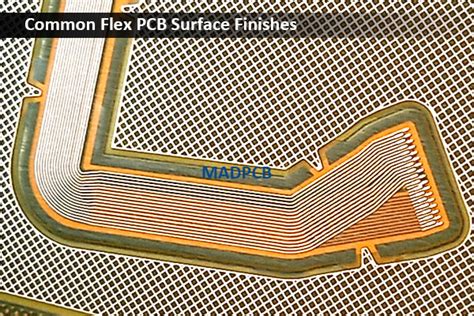
Comparison of PCB Surface Finishes
Surface Finish | Solderability | Shelf Life | Fine-Pitch Compatibility | Cost |
---|---|---|---|---|
HASL | Good | Long | Limited | Low |
OSP | Good | Short | Good | Low |
ENIG | Excellent | Long | Excellent | High |
IAg | Good | Moderate | Good | Moderate |
ISn | Good | Moderate | Good | Moderate |
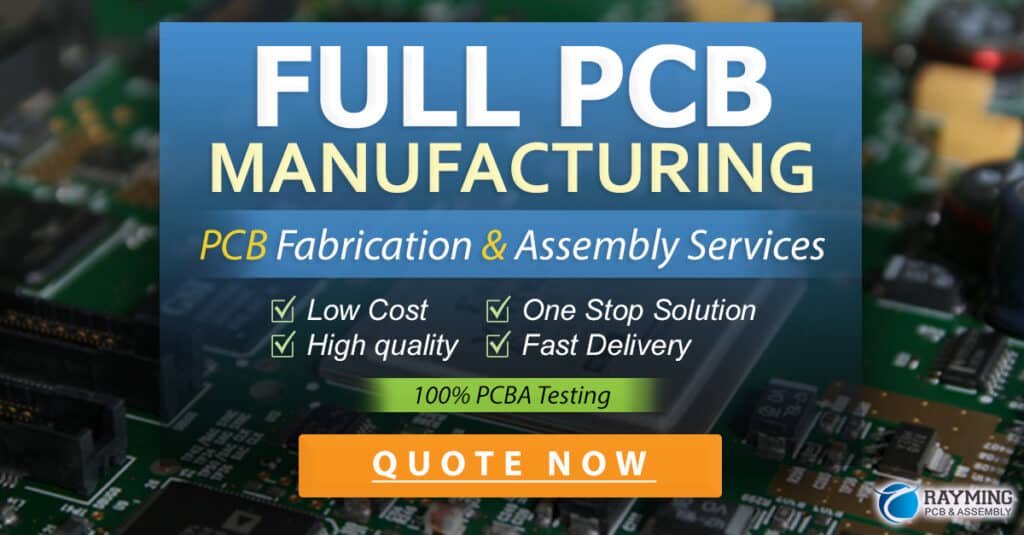
Considerations for Selecting PCB Surface Finishes
When choosing a PCB surface finish, several factors should be considered:
-
Application Requirements: Consider the specific requirements of your application, such as operating environment, temperature range, and signal integrity needs.
-
Component Compatibility: Ensure that the selected surface finish is compatible with the components used in your design, particularly for fine-pitch and BGA components.
-
Manufacturing Process: Consider the manufacturing capabilities of your PCB fabricator and their experience with different surface finishes.
-
Cost: Evaluate the cost implications of each surface finish and balance it with the required performance and reliability.
-
Shelf Life: Consider the expected shelf life of your product and choose a surface finish that maintains solderability and reliability over the desired period.
-
Environmental Regulations: Ensure that the selected surface finish complies with relevant environmental regulations, such as RoHS and REACH.

FAQs
-
Q: What is the most cost-effective PCB surface finish?
A: HASL and OSP are generally the most cost-effective PCB surface finishes. However, they may not be suitable for all applications, particularly those requiring fine-pitch components or long shelf life. -
Q: Which surface finish is best for fine-pitch components?
A: ENIG, IAg, and ISn are excellent choices for fine-pitch components due to their flat surface finish and good solderability. -
Q: Can HASL be used for lead-free soldering?
A: Yes, lead-free HASL is available, which uses a tin-based solder alloy instead of the traditional tin-lead solder. -
Q: What is the “black pad” defect in ENIG surface finish?
A: “Black pad” is a defect that can occur in ENIG surface finish where the nickel layer becomes brittle and separates from the copper pad. This is usually caused by improper plating processes or contamination. -
Q: How can I prevent tin whiskers in immersion tin surface finish?
A: To minimize the risk of tin whiskers, use a matte tin finish instead of bright tin, maintain proper storage conditions, and consider applying a conformal coating over the PCB surface.
Conclusion
Selecting the right PCB surface finish is critical for ensuring the reliability, solderability, and performance of your electronic devices. Each surface finish has its advantages and limitations, and the choice depends on various factors such as application requirements, component compatibility, cost, and manufacturing capabilities. By understanding the characteristics of different surface finishes and considering the specific needs of your project, you can make an informed decision and optimize your PCB design for success.
Leave a Reply