Introduction
When designing electronic devices, ensuring that the printed circuit board (PCB) fits properly within the enclosure is crucial for both functionality and aesthetics. Improper PCB fitment can lead to various issues, such as component damage, overheating, and compromised device performance. In this comprehensive guide, we will explore the key aspects of guaranteeing PCB fitment to your enclosures, including design considerations, manufacturing tolerances, and assembly techniques.
Understanding the Importance of PCB Fitment
The Role of PCBs in Electronic Devices
PCBs are the backbone of modern electronic devices, providing a platform for mounting and interconnecting electronic components. They are designed to carry electrical signals and power, enabling the device to perform its intended functions. PCBs come in various sizes, shapes, and layers, depending on the complexity and requirements of the device.
The Impact of Poor PCB Fitment
When a PCB does not fit properly within its enclosure, several problems can arise:
- Component Damage: Misaligned or poorly fitted PCBs can put undue stress on the mounted components, leading to damage or premature failure.
- Overheating: Insufficient clearance between the PCB and enclosure can restrict airflow, causing heat buildup and potentially damaging temperature-sensitive components.
- Electrical Shorts: If the PCB comes into contact with the enclosure or other conductive surfaces, it can cause electrical shorts, leading to device malfunction or safety hazards.
- Mechanical Interference: Poorly fitted PCBs may interfere with other components or moving parts within the enclosure, affecting the device’s overall functionality and reliability.
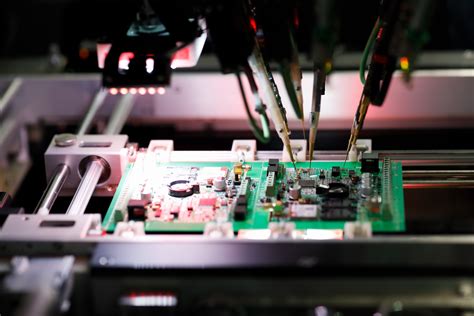
Design Considerations for PCB Fitment
PCB Dimensions and Shape
When designing a PCB, it is essential to consider the dimensions and shape of the enclosure it will be housed in. The PCB should be sized appropriately to fit within the available space, leaving adequate room for mounting, connectors, and other necessary components. Consider the following factors:
- Board Outline: Ensure that the PCB’s outline matches the designated space within the enclosure, taking into account any cutouts or protrusions.
- Component Placement: Position components on the PCB in a way that optimizes space utilization and allows for proper clearance from the enclosure walls.
- Mounting Holes: Include mounting holes on the PCB that align with the corresponding holes or standoffs in the enclosure, ensuring secure and stable mounting.
Clearance and Tolerances
To guarantee proper PCB fitment, it is crucial to maintain appropriate clearances and tolerances between the PCB and the enclosure. Consider the following guidelines:
- Component Height: Ensure that the maximum height of the components on the PCB does not exceed the available clearance within the enclosure.
- Board-to-Enclosure Clearance: Maintain a minimum clearance between the PCB and the enclosure walls to allow for thermal expansion, vibration, and manufacturing tolerances.
- Connector Clearance: Provide sufficient space around connectors and ports to facilitate easy cable attachment and removal without interfering with the enclosure.
Clearance Type | Minimum Recommended Clearance |
---|---|
Component Height | 2-3 mm |
Board-to-Enclosure | 1-2 mm |
Connector Clearance | 3-5 mm |
Thermal Management
Proper thermal management is essential for ensuring the long-term reliability and performance of electronic devices. When designing PCBs for enclosures, consider the following thermal management techniques:
- Heatsinks: Incorporate heatsinks on high-power components to dissipate heat effectively and prevent overheating.
- Thermal Interface Materials: Use thermal interface materials, such as thermal pads or thermal paste, to enhance heat transfer between the PCB and the enclosure.
- Airflow: Design the enclosure and PCB layout to facilitate adequate airflow, allowing for efficient cooling of components.
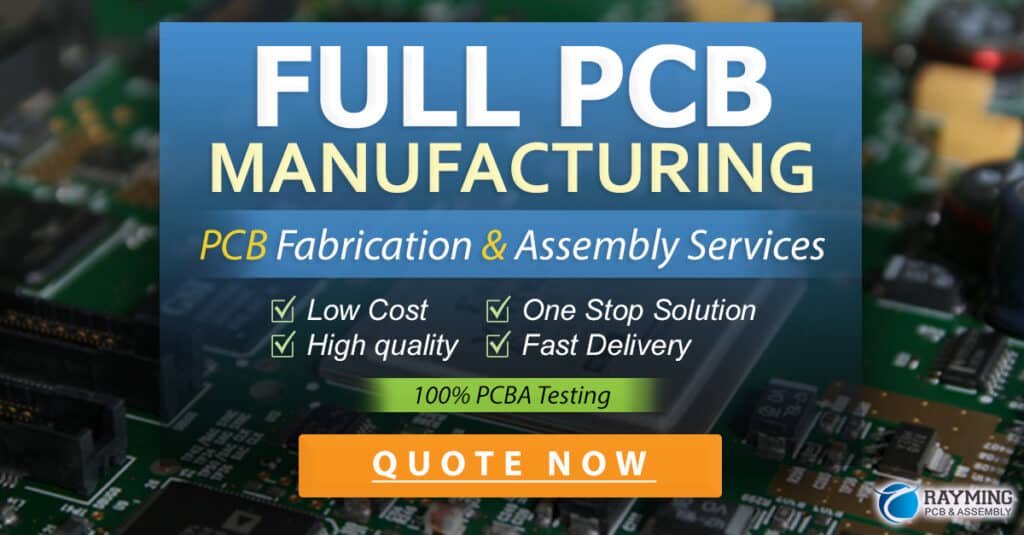
Manufacturing Tolerances and Verification
PCB Fabrication Tolerances
PCB fabrication involves various processes, each with its own set of tolerances. It is essential to understand and account for these tolerances to ensure proper PCB fitment. Key tolerances to consider include:
- Board Outline: The accuracy of the PCB outline can vary depending on the fabrication process, typically ranging from ±0.1mm to ±0.5mm.
- Hole Positioning: The position of mounting holes and vias can have tolerances of ±0.05mm to ±0.2mm.
- Copper Thickness: The thickness of the copper traces on the PCB can vary by ±10% to ±20%, affecting the overall thickness of the board.
Enclosure Manufacturing Tolerances
Similar to PCBs, enclosures are subject to manufacturing tolerances that can impact PCB fitment. Common enclosure manufacturing processes and their associated tolerances include:
Manufacturing Process | Typical Tolerances |
---|---|
Injection Molding | ±0.1mm to ±0.5mm |
CNC Machining | ±0.05mm to ±0.2mm |
Sheet Metal Fabrication | ±0.2mm to ±1.0mm |
Fitment Verification and Testing
To ensure proper PCB fitment, it is crucial to perform thorough verification and testing throughout the design and manufacturing process. Consider the following approaches:
- 3D Modeling: Create accurate 3D models of the PCB and enclosure to virtually assess fitment and identify potential issues.
- Prototyping: Produce physical prototypes of the PCB and enclosure to verify fitment, alignment, and clearances.
- Tolerance Stack-Up Analysis: Conduct a tolerance stack-up analysis to determine the cumulative effect of manufacturing tolerances on PCB fitment.
- Functional Testing: Perform functional testing on the assembled device to validate PCB fitment and ensure proper operation under various conditions.
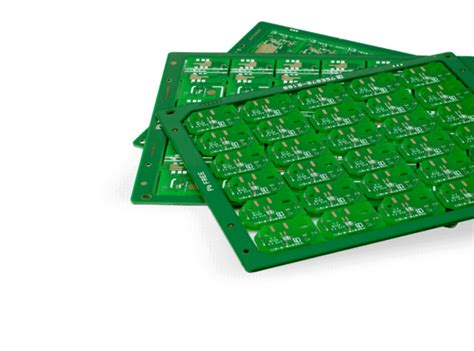
Assembly Techniques for Optimal PCB Fitment
Mounting Methods
Secure and stable mounting of the PCB within the enclosure is essential for maintaining proper fitment and preventing movement or vibration-induced damage. Common PCB mounting methods include:
- Screws and Standoffs: Use screws and standoffs to securely fasten the PCB to the enclosure at designated mounting points.
- Snap-Fit Features: Design snap-fit features into the enclosure to hold the PCB in place without the need for additional hardware.
- Slots and Guides: Incorporate slots or guides in the enclosure to align and support the PCB during assembly.
Strain Relief and Cable Management
Proper strain relief and cable management are crucial for maintaining PCB fitment and preventing damage to connectors and components. Consider the following techniques:
- Strain Relief Features: Incorporate strain relief features, such as cable clamps or grommet holes, to prevent excessive stress on PCB-mounted connectors.
- Cable Routing: Design the enclosure and PCB layout to accommodate neat and organized cable routing, minimizing interference with other components.
- Cable Ties and Adhesive Mounts: Use cable ties or adhesive mounts to secure cables and prevent them from shifting or applying undue stress on the PCB.
Best Practices for PCB Fitment
Collaborative Design Approach
Ensuring proper PCB fitment requires close collaboration between the PCB designer, mechanical engineer, and manufacturing team. Foster open communication and coordination throughout the design process to identify and address fitment challenges early on.
Design for Manufacturing (DFM)
Incorporate Design for Manufacturing (DFM) principles into your PCB and enclosure design to optimize manufacturability and minimize fitment issues. Consider factors such as component placement, board shape, and mounting hole locations to facilitate smooth assembly and fitment.
Documentation and Communication
Maintain clear and comprehensive documentation of PCB and enclosure designs, including dimensional specifications, tolerances, and assembly instructions. Effective communication among team members and with manufacturing partners is essential for ensuring consistent and accurate PCB fitment.
Frequently Asked Questions (FAQ)
-
Q: What is the minimum recommended clearance between the PCB and enclosure walls?
A: A minimum clearance of 1-2 mm between the PCB and enclosure walls is generally recommended to allow for thermal expansion, vibration, and manufacturing tolerances. -
Q: How can I ensure proper alignment of mounting holes on the PCB and enclosure?
A: Use accurate 3D modeling and prototyping to verify the alignment of mounting holes. Incorporate appropriate tolerances and conduct thorough testing to confirm proper fitment. -
Q: What are some common PCB mounting methods?
A: Common PCB mounting methods include using screws and standoffs, snap-fit features, and slots or guides in the enclosure to secure and align the PCB. -
Q: How can I prevent overheating issues related to PCB fitment?
A: Ensure adequate clearance for airflow, use heatsinks on high-power components, and consider thermal interface materials to enhance heat transfer between the PCB and enclosure. -
Q: What should I do if I encounter PCB fitment issues during the design or manufacturing process?
A: Collaborate closely with your design and manufacturing teams to identify the root cause of the fitment issues. Make necessary adjustments to the PCB or enclosure design, considering tolerances and assembly techniques, and perform thorough testing to validate the changes.
Conclusion
Guaranteeing proper PCB fitment to your enclosures is essential for the functionality, reliability, and overall success of your electronic devices. By carefully considering design factors such as PCB dimensions, clearances, and thermal management, and accounting for manufacturing tolerances and assembly techniques, you can ensure a seamless integration between the PCB and enclosure.
Remember to foster a collaborative design approach, implement DFM principles, and maintain clear documentation and communication throughout the process. By following the guidelines and best practices outlined in this article, you can overcome PCB fitment challenges and create electronic devices that are both functional and aesthetically pleasing.
Leave a Reply