Introduction to Design-for-Test (DFT) in Embedded Systems
Design-for-Test (DFT) is a crucial aspect of embedded system design that focuses on incorporating testability features into the system from the early stages of development. By employing DFT techniques, designers can ensure that their embedded systems are easily testable, maintainable, and reliable throughout their lifecycle. In this article, we will explore the key concepts, strategies, and best practices for designing testable embedded systems.
What is Design-for-Test?
Design-for-Test is a design methodology that aims to enhance the testability of a system by incorporating features and techniques that facilitate efficient testing and debugging. DFT involves designing the system with testing in mind, making it easier to verify the functionality, detect faults, and isolate issues during various stages of development and deployment.
Importance of DFT in Embedded Systems
Embedded systems are often complex, resource-constrained, and deployed in critical applications where reliability and robustness are paramount. DFT plays a vital role in ensuring the quality and dependability of these systems. By incorporating DFT techniques, designers can:
- Reduce test development time and effort
- Improve fault coverage and detection capabilities
- Facilitate easier debugging and fault isolation
- Enhance system maintainability and upgradability
- Increase overall system reliability and quality
Key Concepts in Design-for-Test
To effectively implement DFT in embedded systems, it is essential to understand the key concepts and techniques involved. Let’s explore some of the fundamental concepts in DFT.
Controllability and Observability
Controllability and observability are two critical aspects of DFT. Controllability refers to the ability to control the inputs and internal states of a system during testing. It enables the application of test stimuli and the setting of desired conditions. Observability, on the other hand, refers to the ability to observe and capture the outputs and internal states of a system during testing. It allows the monitoring and analysis of system behavior.
Designers should strive to maximize both controllability and observability in their embedded systems. This can be achieved through various techniques, such as:
- Providing access to internal signals and registers
- Incorporating test access mechanisms (e.g., JTAG, boundary scan)
- Designing for modularity and isolating components
- Implementing built-in self-test (BIST) capabilities
Test Access Mechanisms
Test access mechanisms (TAMs) are hardware and software features that provide access to the internal components and signals of an embedded system for testing purposes. TAMs enable the application of test stimuli, capture of test responses, and control of test modes. Some common TAMs used in DFT include:
- JTAG (Joint Test Action Group): A standardized interface for accessing and controlling test features in a system.
- Boundary Scan: A technique that allows the testing of interconnections and logic between components using a chain of boundary scan cells.
- Scan Chains: A method of converting sequential circuits into combinational circuits by replacing flip-flops with scannable flip-flops, enabling easier testing.
- Built-In Self-Test (BIST): A mechanism that incorporates self-test capabilities within the system itself, allowing it to test its own functionality.
Fault Models and Coverage
Fault models are abstractions used to represent the types of faults that can occur in a system. They provide a basis for generating test patterns and evaluating fault coverage. Some common fault models used in DFT include:
- Stuck-at faults: Faults where a signal or node is permanently stuck at a logical ‘0’ or ‘1’.
- Transition faults: Faults where a signal fails to transition from one logic level to another.
- Bridging faults: Faults caused by unintended connections between two or more signals.
- Delay faults: Faults that cause a signal to arrive too late or too early, violating timing constraints.
Fault coverage refers to the percentage of potential faults that can be detected by a given set of tests. Designers should aim for high fault coverage to ensure the effectiveness of their testing efforts. Techniques such as automatic test pattern generation (ATPG) and fault simulation can be used to generate test patterns and evaluate fault coverage.
Design for Manufacturability (DFM)
Design for Manufacturability (DFM) is an approach that considers the manufacturing process during the design phase to ensure the producibility and reliability of the embedded system. DFM techniques aim to minimize manufacturing defects, reduce production costs, and improve yield. Some DFM considerations in the context of DFT include:
- Testability: Designing the system to facilitate testing during manufacturing, such as incorporating test points and boundary scan capabilities.
- Design rules: Adhering to manufacturing design rules to avoid potential issues during fabrication, such as minimum spacing and width requirements.
- Yield optimization: Employing techniques to maximize the yield of good devices, such as redundancy, fault tolerance, and design marginality reduction.
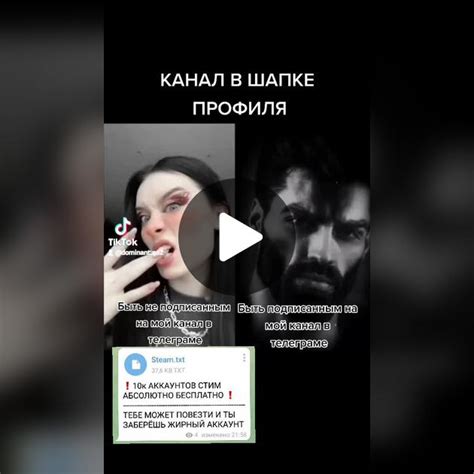
DFT Strategies and Techniques
Now that we have covered the key concepts in DFT, let’s explore some specific strategies and techniques that can be applied in embedded system design.
Scan-Based Testing
Scan-based testing is a widely used DFT technique that involves converting sequential circuits into combinational circuits by replacing flip-flops with scannable flip-flops. This enables easier testing and fault detection. The basic steps in scan-based testing are:
- Scan-in: The test pattern is shifted into the scannable flip-flops through a scan chain.
- Capture: The system is allowed to operate for one or more clock cycles, and the response is captured in the flip-flops.
- Scan-out: The captured response is shifted out of the flip-flops through the scan chain for analysis.
Scan-based testing provides high fault coverage and enables efficient test pattern generation using ATPG tools.
Boundary Scan Testing
Boundary scan testing, based on the IEEE 1149.1 standard, is a technique used to test the interconnections and logic between components on a printed circuit board (PCB). It involves placing boundary scan cells at the input and output pins of each component, forming a boundary scan chain. The basic operations in boundary scan testing are:
- Extest: Tests the interconnections between components by applying test patterns to the boundary scan cells and capturing the responses.
- Intest: Tests the internal logic of a component by applying test patterns to its inputs and capturing the responses at its outputs.
- Sample/Preload: Captures the current state of the component’s inputs and outputs or preloads a specific state into the boundary scan cells.
Boundary scan testing enables efficient testing of interconnects and facilitates board-level diagnostics and debugging.
Built-In Self-Test (BIST)
Built-In Self-Test (BIST) is a DFT technique where the system incorporates self-test capabilities, allowing it to test its own functionality. BIST eliminates the need for external test equipment and enables in-system testing. The main components of a BIST architecture are:
- Test Pattern Generator (TPG): Generates the test patterns to be applied to the system under test.
- Test Controller: Controls the execution of the self-test, including test pattern application and response capture.
- Output Response Analyzer (ORA): Compares the captured responses with the expected responses to determine the presence of faults.
BIST can be implemented for various components, such as memories (Memory BIST), logic blocks (Logic BIST), and analog circuits (Analog BIST). It provides fast and efficient testing capabilities and can be executed during system startup or periodically during operation.
Design for Debug (DFD)
Design for Debug (DFD) is a DFT approach that focuses on incorporating features and mechanisms to facilitate debugging and fault isolation during system development and deployment. DFD techniques include:
- Trace and debug interfaces: Providing access to internal signals and buses for real-time monitoring and debugging, such as using JTAG or proprietary debug interfaces.
- Embedded instrumentation: Incorporating instrumentation logic, such as event counters, performance monitors, and assertion checkers, to collect runtime information and detect anomalies.
- On-chip debugging: Integrating debug cores or debug subsystems that enable interactive debugging, breakpoint setting, and register access.
- Error logging and reporting: Implementing mechanisms to log and report error conditions, exceptions, and system states for post-mortem analysis.
DFD techniques enhance the observability and controllability of the system, making it easier to identify and isolate faults during debugging sessions.
Design Marginality Reduction
Design marginality refers to the susceptibility of a system to failures due to variations in manufacturing processes, environmental conditions, or aging effects. Design marginality reduction techniques aim to improve the robustness and reliability of the system by minimizing the impact of these variations. Some techniques include:
- Worst-case design: Designing the system to operate correctly under the worst-case conditions, such as extreme temperature, voltage, or process variations.
- Guard-banding: Adding extra margins to the design parameters to accommodate potential variations and ensure proper functionality.
- Adaptive voltage and frequency scaling (AVFS): Dynamically adjusting the voltage and frequency of the system based on operating conditions to optimize performance and power consumption while maintaining reliability.
- Aging monitoring and compensation: Incorporating mechanisms to monitor and compensate for the effects of aging, such as using sensors or adaptive circuits to adjust system parameters over time.
By reducing design marginality, designers can improve the overall reliability and robustness of the embedded system.
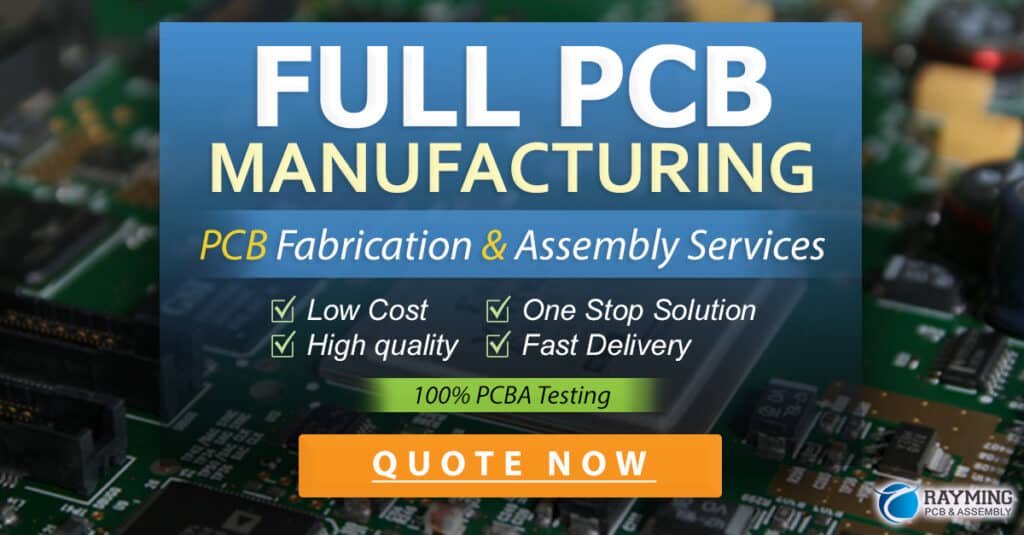
Best Practices for Design-for-Test
To effectively implement DFT in embedded systems, designers should follow certain best practices. Here are some key recommendations:
- Start early: Incorporate DFT considerations from the early stages of the design process to ensure testability is an integral part of the system.
- Modularize the design: Divide the system into smaller, testable modules to facilitate easier testing, debugging, and maintenance.
- Use standard interfaces: Adopt standardized test interfaces, such as JTAG or boundary scan, to leverage existing tools and methodologies.
- Plan for test coverage: Define test coverage goals and develop a comprehensive test plan that includes various testing techniques and fault models.
- Automate testing: Utilize automated test generation tools, such as ATPG, to create efficient test patterns and minimize manual effort.
- Consider manufacturing testability: Design the system with manufacturability in mind, incorporating features that facilitate testing during production.
- Document the design: Maintain clear and comprehensive documentation of the DFT features, test procedures, and debugging guidelines.
- Collaborate with test engineers: Foster close collaboration between design and test teams to ensure the effectiveness and efficiency of the DFT implementation.
By following these best practices, designers can create embedded systems that are more testable, maintainable, and reliable.
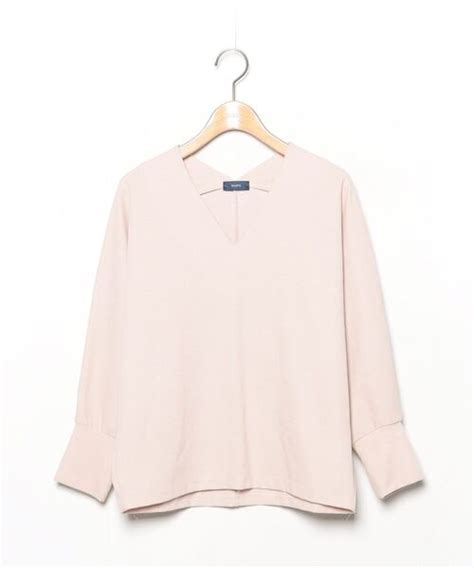
Frequently Asked Questions (FAQ)
- What is the difference between Design-for-Test (DFT) and Design-for-Manufacturability (DFM)?
-
DFT focuses on incorporating testability features into the system design to facilitate efficient testing and debugging. DFM, on the other hand, aims to optimize the design for manufacturability, considering factors such as producibility, yield, and cost.
-
What are the benefits of using scan-based testing in embedded systems?
-
Scan-based testing provides several benefits, including high fault coverage, efficient test pattern generation, and the ability to test sequential circuits as combinational circuits. It enables easier testing and fault detection, reducing test development time and effort.
-
How does boundary scan testing differ from traditional testing methods?
-
Boundary scan testing focuses on testing the interconnections and logic between components on a PCB using a chain of boundary scan cells. It enables efficient testing of interconnects without the need for physical access to individual pins. Traditional testing methods, such as in-circuit testing or functional testing, may require direct access to pins and may not provide the same level of interconnect testing capabilities.
-
What are the advantages of incorporating Built-In Self-Test (BIST) in embedded systems?
-
BIST provides several advantages, including fast and efficient testing capabilities, reduced reliance on external test equipment, and the ability to perform in-system testing. It enables the system to test its own functionality, facilitating early detection of faults and reducing test time and cost.
-
How can design marginality reduction techniques improve the reliability of embedded systems?
- Design marginality reduction techniques, such as worst-case design, guard-banding, and adaptive voltage and frequency scaling, help improve the robustness and reliability of embedded systems by minimizing the impact of manufacturing variations, environmental conditions, and aging effects. These techniques ensure that the system operates correctly under a wide range of conditions, reducing the likelihood of failures and improving overall system reliability.
Conclusion
Design-for-Test is a critical aspect of embedded system design that enables the creation of testable, maintainable, and reliable systems. By incorporating DFT techniques and following best practices, designers can enhance the controllability and observability of their systems, facilitate efficient testing and debugging, and improve overall system quality.
This article has covered the key concepts, strategies, and techniques involved in DFT for embedded systems. We explored the importance of controllability and observability, test access mechanisms, fault models and coverage, and design for manufacturability. We also delved into specific DFT techniques, such as scan-based testing, boundary scan testing, BIST, and design for debug.
To effectively implement DFT, designers should start early, modularize their designs, use standard interfaces, plan for test coverage, automate testing, consider manufacturing testability, document their designs, and collaborate closely with test engineers.
By embracing DFT principles and techniques, embedded system designers can create systems that are easier to test, debug, and maintain, ultimately leading to improved reliability, reduced development time, and lower costs. As the complexity of embedded systems continues to grow, the importance of DFT will only increase, making it a crucial skill for designers to master.
Leave a Reply