Understanding PCB Mask Expansion
PCB mask expansion, also known as solder mask expansion or solder mask overdraw, is a crucial aspect of printed circuit board (PCB) design and manufacturing. It refers to the additional area of solder mask that extends beyond the copper pad on a PCB. This expansion helps to prevent solder bridges, ensures proper insulation, and improves the overall reliability of the PCB.
What is PCB Mask Expansion?
PCB mask expansion is the process of extending the solder mask beyond the copper pad to create a barrier between adjacent pads. The solder mask is a thin layer of polymer that is applied to the PCB surface to protect the copper traces and prevent solder bridging. By expanding the mask, designers can ensure that there is sufficient clearance between the pads, reducing the risk of short circuits and improving the manufacturing yield.
Why is PCB Mask Expansion Important?
PCB mask expansion plays a crucial role in ensuring the reliability and functionality of a PCB. Here are some reasons why mask expansion is important:
-
Prevents Solder Bridging: Solder bridging occurs when solder inadvertently connects two adjacent pads, causing a short circuit. Mask expansion helps to prevent this by creating a physical barrier between the pads.
-
Improves Insulation: The solder mask acts as an insulating layer, protecting the copper traces from environmental factors such as moisture, dust, and debris. By expanding the mask, designers can enhance the insulation properties of the PCB.
-
Enhances Manufacturing Yield: Proper mask expansion can significantly improve the manufacturing yield of a PCB. It reduces the likelihood of defects such as solder bridging, which can lead to costly rework or scrapped boards.
-
Facilitates Soldering: Mask expansion creates a well-defined area for soldering components to the PCB. It helps to contain the solder within the desired pad area, preventing it from spreading to adjacent pads or traces.
Factors Affecting PCB Mask Expansion
Several factors influence the amount of mask expansion required for a PCB design. Understanding these factors is essential for determining the optimal mask expansion value.
PCB Manufacturing Process
The PCB manufacturing process plays a significant role in determining the mask expansion requirements. Different manufacturing processes have varying tolerances and capabilities when it comes to applying the solder mask.
Manufacturing Process | Typical Mask Expansion |
---|---|
Liquid Photo Imageable (LPI) | 0.05mm – 0.1mm |
Dry Film Solder Mask | 0.075mm – 0.125mm |
Ink Jet Printing | 0.05mm – 0.075mm |
As seen in the table above, the mask expansion values vary depending on the manufacturing process used. LPI and ink jet printing processes generally require smaller mask expansion compared to dry film solder mask processes.
PCB Materials
The choice of PCB materials also affects the mask expansion requirements. Different substrate materials have varying surface properties and adhesion characteristics, which can impact the Solder mask application.
PCB Material | Recommended Mask Expansion |
---|---|
FR-4 | 0.075mm – 0.1mm |
High Tg FR-4 | 0.075mm – 0.1mm |
Polyimide | 0.05mm – 0.075mm |
Flex PCB | 0.05mm – 0.075mm |
The table above shows the recommended mask expansion values for common PCB materials. FR-4 and High Tg FR-4 materials typically require slightly larger mask expansion compared to polyimide and flex PCB materials.
Component Pitch and Density
The pitch and density of components on a PCB also influence the mask expansion requirements. As the component pitch decreases and the density increases, the clearance between pads becomes more critical.
Component Pitch | Recommended Mask Expansion |
---|---|
≥ 0.8mm | 0.05mm – 0.075mm |
0.5mm – 0.8mm | 0.075mm – 0.1mm |
≤ 0.5mm | 0.1mm – 0.125mm |
The table above provides guidelines for mask expansion based on component pitch. For larger pitch components (≥ 0.8mm), smaller mask expansion values can be used. As the pitch decreases, larger mask expansion is recommended to ensure sufficient clearance between pads.
PCB Layer Stack-up
The PCB layer stack-up, which refers to the arrangement of conductive and insulating layers, can also impact the mask expansion requirements. The thickness and type of insulating materials used between layers affect the registration accuracy of the solder mask.
Layer Stack-up | Recommended Mask Expansion |
---|---|
2-Layer PCB | 0.05mm – 0.075mm |
4-Layer PCB | 0.075mm – 0.1mm |
6-Layer PCB | 0.075mm – 0.1mm |
8-Layer PCB | 0.1mm – 0.125mm |
The table above shows the recommended mask expansion values for different PCB layer stack-ups. As the number of layers increases, larger mask expansion is generally required to accommodate the increased complexity and registration challenges.
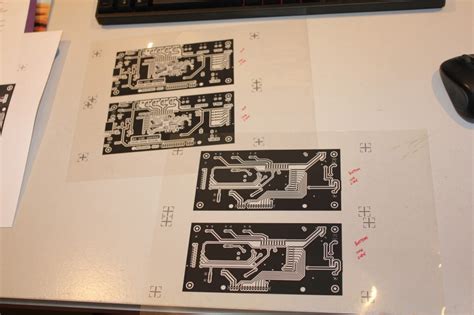
Consequences of Excessive Mask Expansion
While mask expansion is necessary for ensuring the reliability and manufacturability of a PCB, excessive expansion can lead to several issues. Here are some potential consequences of excessive mask expansion:
-
Reduced Pad Size: Excessive mask expansion can reduce the available pad size for soldering components. This can make it challenging to achieve proper solder joint formation and may lead to poor component attachment.
-
Decreased Clearance Between Pads: If the mask expansion is too large, it can reduce the clearance between adjacent pads. This can increase the risk of solder bridging and short circuits, especially for high-density designs.
-
Impaired Visual Inspection: Excessive mask expansion can make it difficult to visually inspect the solder joints during the assembly process. The solder mask may obscure the solder joint, making it challenging to identify any defects or issues.
-
Increased Manufacturing Costs: Overly large mask expansion can increase the manufacturing costs of a PCB. It may require additional processing steps, such as solder mask trimming or selective soldering, which can add to the overall production time and expenses.
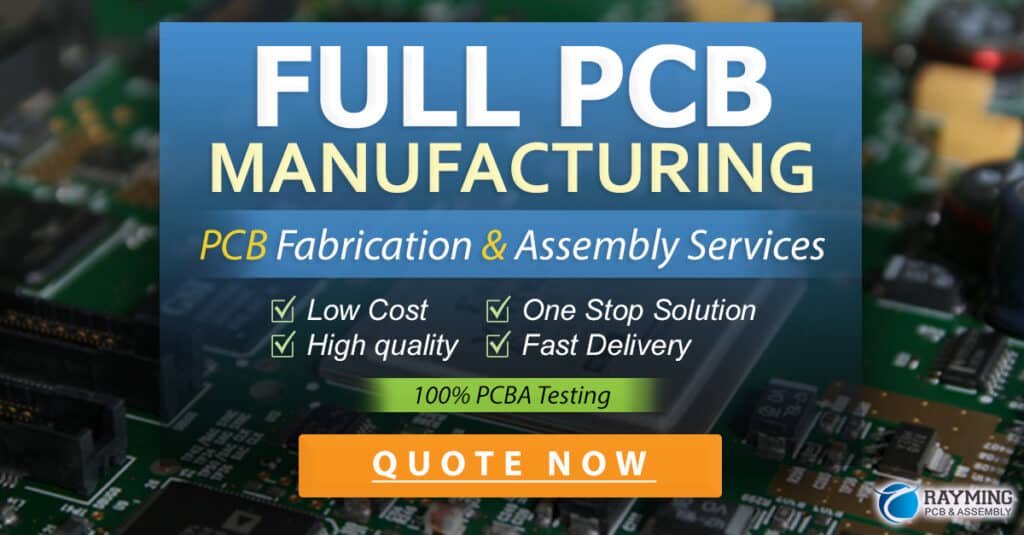
Guidelines for Optimal Mask Expansion
To ensure the optimal performance and manufacturability of a PCB, it is essential to follow guidelines for mask expansion. Here are some general guidelines to consider:
-
Follow Manufacturer’s Recommendations: Consult with the PCB manufacturer and follow their recommended mask expansion values for the specific manufacturing process and materials being used.
-
Consider Component Pitch and Density: Adjust the mask expansion based on the component pitch and density of the PCB design. Use smaller expansion values for larger pitch components and increase the expansion for higher-density designs.
-
Maintain Sufficient Clearance: Ensure that there is sufficient clearance between adjacent pads after applying the mask expansion. A minimum clearance of 0.1mm is generally recommended, but this may vary depending on the PCB design and manufacturing process.
-
Conduct Design Reviews: Perform thorough design reviews to assess the mask expansion requirements and identify any potential issues. Collaborate with the PCB manufacturer and assembly team to ensure that the mask expansion meets their requirements and capabilities.
-
Perform Prototype Testing: Before mass production, conduct prototype testing to validate the mask expansion settings. This allows for any necessary adjustments to be made and ensures the reliability and manufacturability of the final PCB.
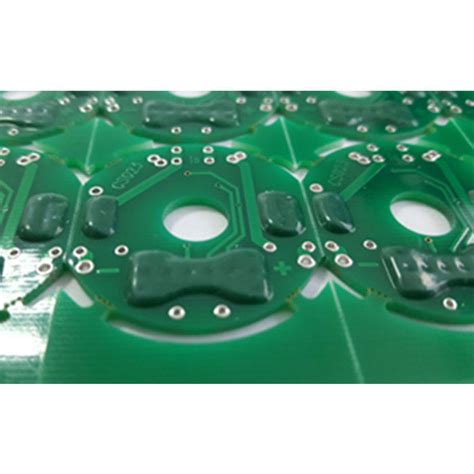
Frequently Asked Questions (FAQ)
-
What is the typical range of mask expansion values?
The typical range of mask expansion values is between 0.05mm and 0.125mm, depending on the PCB manufacturing process, materials, and design requirements. -
Can mask expansion be different for different areas of the PCB?
Yes, mask expansion can be adjusted for different areas of the PCB based on the specific requirements of each region. For example, areas with high-density components may require larger mask expansion compared to areas with larger pitch components. -
How does mask expansion affect the assembly process?
Mask expansion affects the assembly process by defining the available pad area for soldering components. Excessive mask expansion can make it challenging to achieve proper solder joint formation and may require additional processing steps, such as selective soldering. -
What happens if the mask expansion is too small?
If the mask expansion is too small, it can increase the risk of solder bridging and short circuits between adjacent pads. It may also result in insufficient insulation and protection for the copper traces. -
Can mask expansion be adjusted after the PCB has been manufactured?
No, mask expansion cannot be adjusted after the PCB has been manufactured. It is crucial to determine the appropriate mask expansion values during the design and prototyping stages to ensure the desired results in the final PCB.
Conclusion
PCB mask expansion is a critical aspect of PCB design and manufacturing that ensures the reliability, functionality, and manufacturability of the final product. It involves extending the solder mask beyond the copper pads to create a barrier between adjacent pads, prevent solder bridging, and improve insulation.
The amount of mask expansion required depends on various factors, including the PCB manufacturing process, materials, component pitch and density, and layer stack-up. Excessive mask expansion can lead to reduced pad size, decreased clearance between pads, impaired visual inspection, and increased manufacturing costs.
To achieve optimal results, it is essential to follow guidelines for mask expansion, consult with the PCB manufacturer, consider the specific design requirements, and conduct thorough design reviews and prototype testing.
By understanding the importance of PCB mask expansion and implementing appropriate strategies, designers and manufacturers can ensure the production of high-quality, reliable PCBs that meet the demands of today’s electronic applications.
Leave a Reply