What is a Bill of Materials?
A bill of materials (BOM) is a hierarchical list that outlines all the components, parts, and materials needed to create a product. It includes the quantity, description, and specifications of each item, as well as their relationships to one another. The BOM acts as a blueprint for the manufacturing process, ensuring that all necessary components are available and assembled in the correct order.
Types of Bill of Materials
There are several types of bill of materials, each serving a specific purpose:
-
Engineering BOM (EBOM): This type of BOM is created by the engineering team and focuses on the product’s design and functionality. It includes all the components and their specifications required to build the product.
-
Manufacturing BOM (MBOM): The MBOM is derived from the EBOM and is tailored to the manufacturing process. It includes additional information such as packaging materials, assembly instructions, and production steps.
-
Sales BOM (SBOM): The SBOM is used by the sales team to communicate the product’s components and features to customers. It may include customizable options and pricing information.
-
Service BOM (SBOM): This type of BOM is used for after-sales support and maintenance. It includes spare parts, consumables, and other items required to service the product.
Benefits of Creating a Bill of Materials
Creating a comprehensive and accurate bill of materials offers numerous benefits for your organization:
1. Improved Inventory Management
A well-structured BOM helps you maintain optimal inventory levels by providing a clear understanding of the components required for each product. This information allows you to:
- Accurately forecast demand for raw materials and components
- Avoid stockouts and overstocking
- Reduce inventory carrying costs
- Streamline purchasing processes
2. Enhanced Supply Chain Efficiency
By sharing the BOM with suppliers, you can ensure that they have a clear understanding of your requirements. This collaboration leads to:
- Faster sourcing and procurement of materials
- Reduced lead times
- Improved supplier relationships
- Better quality control
3. Streamlined Production Processes
A detailed BOM serves as a roadmap for the production team, enabling them to:
- Plan and schedule production efficiently
- Reduce errors and rework
- Optimize resource allocation
- Improve overall productivity
4. Better Cost Control
Creating a BOM helps you identify the cost of each component and the total cost of the product. This information allows you to:
- Monitor and control production costs
- Identify opportunities for cost reduction
- Make informed pricing decisions
- Improve profitability
5. Enhanced Product Quality
A comprehensive BOM ensures that all components meet the required specifications and quality standards. This attention to detail leads to:
- Consistent product quality
- Reduced defects and warranty claims
- Improved customer satisfaction
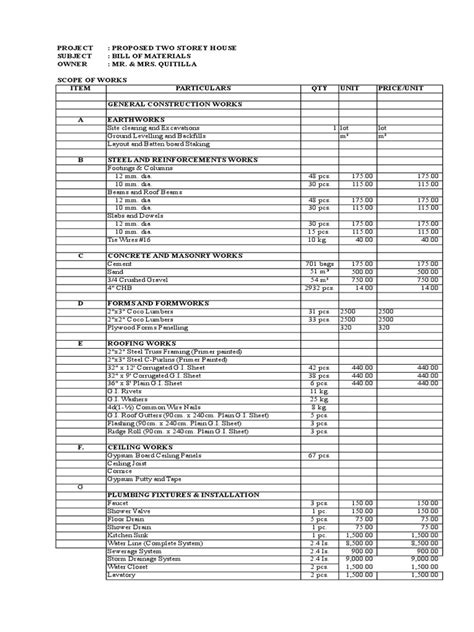
How to Create a Bill of Materials
Creating a bill of materials involves several steps:
-
Define the product structure: Break down the product into its main assemblies, subassemblies, and components.
-
Identify components: List all the components required for each assembly and subassembly, including their quantities and specifications.
-
Assign unique identifiers: Allocate a unique part number or code to each component to ensure easy identification and tracking.
-
Specify relationships: Clearly define the relationships between components, assemblies, and subassemblies using a hierarchical structure.
-
Include additional information: Add relevant details such as supplier information, lead times, costs, and any special instructions.
-
Review and update: Regularly review and update the BOM to reflect any changes in the product design, components, or suppliers.
BOM Example
Here’s a simplified example of a BOM for a bicycle:
Level | Part Number | Description | Quantity |
---|---|---|---|
0 | BK-001 | Bicycle | 1 |
1 | FR-001 | Frame | 1 |
1 | WH-001 | Wheel Set | 1 |
2 | WH-002 | Front Wheel | 1 |
2 | WH-003 | Rear Wheel | 1 |
3 | SP-001 | Spokes | 36 |
3 | RI-001 | Rim | 1 |
3 | HU-001 | Hub | 1 |
1 | DR-001 | Drivetrain | 1 |
2 | CH-001 | Chain | 1 |
2 | CR-001 | Crankset | 1 |
2 | DE-001 | Derailleur | 1 |
1 | BR-001 | Brakes | 1 |
2 | BR-002 | Front Brake | 1 |
2 | BR-003 | Rear Brake | 1 |
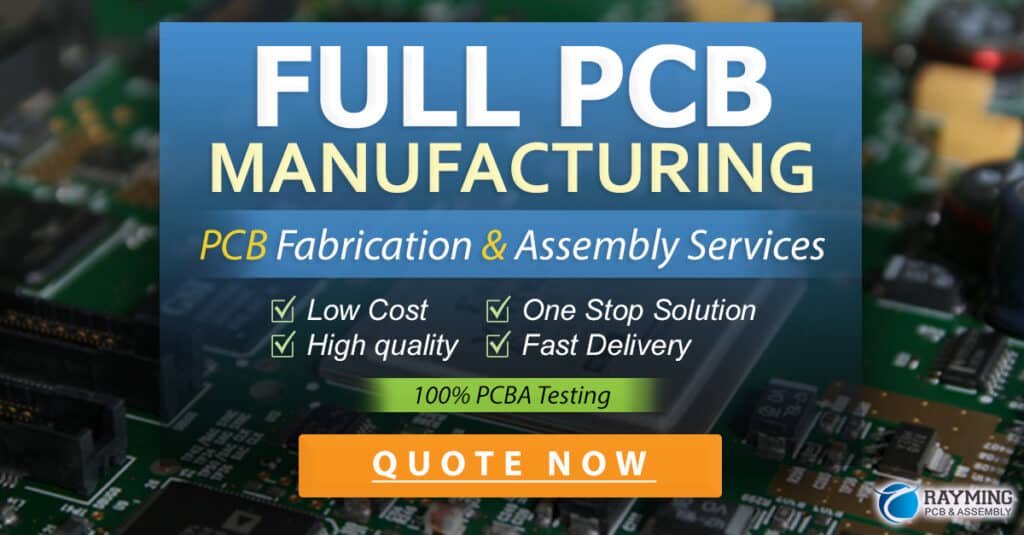
Challenges in Managing Bill of Materials
While creating and maintaining a bill of materials offers significant benefits, there are also some challenges to consider:
1. Complexity
As products become more complex, with numerous components and subassemblies, managing the BOM can become increasingly difficult. It’s essential to have a well-structured and organized BOM to ensure accuracy and efficiency.
2. Version Control
Products often undergo revisions and updates, which means the BOM must be updated accordingly. Maintaining version control and ensuring that all stakeholders are using the most current version of the BOM can be challenging.
3. Integration with Other Systems
The BOM must integrate seamlessly with other systems, such as enterprise resource planning (ERP), manufacturing execution systems (MES), and product lifecycle management (PLM) software. Ensuring data consistency and accuracy across these systems can be complex.
4. Supplier Collaboration
Collaborating with suppliers to ensure they have access to the latest BOM and can meet your requirements can be challenging, especially when dealing with multiple suppliers across different locations.
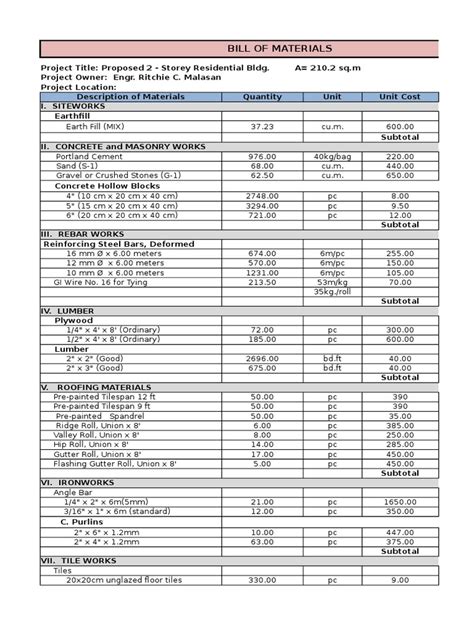
Best Practices for Bill of Materials Management
To overcome these challenges and ensure effective BOM management, consider the following best practices:
-
Use a centralized BOM system: Implement a centralized system to manage your BOMs, ensuring that all stakeholders have access to the most up-to-date information.
-
Establish clear naming conventions: Develop a consistent naming convention for components and assemblies to avoid confusion and ensure easy identification.
-
Implement version control: Establish a robust version control system to track changes and revisions to the BOM, ensuring that everyone is working with the most current version.
-
Integrate with other systems: Ensure that your BOM system integrates seamlessly with other software systems, such as ERP and PLM, to maintain data consistency and accuracy.
-
Collaborate with suppliers: Foster strong relationships with your suppliers and provide them with access to the relevant parts of the BOM to ensure they can meet your requirements.
-
Conduct regular audits: Perform regular audits of your BOM to identify and correct any errors, inconsistencies, or outdated information.
Frequently Asked Questions (FAQ)
-
What is the difference between a bill of materials and a parts list?
A bill of materials is a hierarchical list that includes all the components, parts, and materials required to manufacture a product, along with their quantities and relationships. A parts list, on the other hand, is a simple list of all the parts needed for a product, without the hierarchical structure or detailed information found in a BOM. -
How often should I update my bill of materials?
You should update your bill of materials whenever there are changes to the product design, components, or suppliers. It’s essential to keep the BOM current to ensure accurate inventory management, procurement, and production processes. -
Can I use the same BOM for different product variants?
While it’s possible to use the same BOM for different product variants, it’s often better to create separate BOMs for each variant to ensure accuracy and clarity. This approach allows you to account for any differences in components or quantities between variants. -
How do I handle custom or made-to-order components in my BOM?
For custom or made-to-order components, you can include them in your BOM with a special designation or note indicating their unique status. Be sure to include any specific requirements or specifications for these components to ensure they are manufactured correctly. -
What are the risks of having an inaccurate or outdated BOM?
An inaccurate or outdated BOM can lead to numerous problems, such as: - Incorrect component ordering and inventory management
- Production delays and errors
- Increased costs due to rework or excess inventory
- Reduced product quality and customer satisfaction
By maintaining a comprehensive and up-to-date bill of materials, you can mitigate these risks and ensure a smooth, efficient manufacturing process.
Conclusion
Creating and maintaining a comprehensive and accurate bill of materials is essential for streamlining your manufacturing operations and meeting your organization’s needs. A well-structured BOM offers numerous benefits, including improved inventory management, enhanced supply chain efficiency, streamlined production processes, better cost control, and improved product quality.
To ensure effective BOM management, it’s crucial to follow best practices such as using a centralized system, establishing clear naming conventions, implementing version control, integrating with other systems, collaborating with suppliers, and conducting regular audits.
By investing time and resources into creating and maintaining a robust bill of materials, you can unlock the full potential of your manufacturing operations and drive long-term success for your organization.
Leave a Reply