Introduction to PFAS and PCBs
Per- and polyfluoroalkyl substances (PFAS) are a group of over 4,000 man-made chemicals that have been used in various industries since the 1940s. These chemicals are known for their unique properties, such as water and oil repellency, temperature resistance, and friction reduction. PFAS have been widely used in the production of many consumer goods, including non-stick cookware, food packaging, textiles, and firefighting foams.
In the electronics industry, PFAS have been used in the manufacturing of printed circuit boards (PCBs). PCBs are essential components in almost all electronic devices, from smartphones and computers to automotive and aerospace systems. PFAS are used in PCBs for their ability to repel water, oil, and other contaminants, which helps to protect the delicate electronic components and ensure the reliability of the devices.
However, in recent years, concerns have been raised about the potential health and environmental risks associated with PFAS. Studies have shown that these chemicals can persist in the environment for long periods and accumulate in the bodies of humans and animals. Exposure to PFAS has been linked to various health problems, including cancer, thyroid disease, and developmental issues.
The EU’s Proposed Ban on PFAS
In response to growing concerns about the risks of PFAS, the European Union (EU) has proposed a ban on the use of these chemicals in various products, including PCBs. The proposed ban is part of the EU’s Chemicals Strategy for Sustainability, which aims to protect human health and the environment from harmful chemicals.
The EU’s proposed ban on PFAS would prohibit the use of these chemicals in the production of PCBs and other electronic components. The ban would apply to all PFAS, including those that are currently used as substitutes for older PFAS that have already been phased out.
The proposed ban is expected to have significant implications for the electronics industry, particularly for manufacturers of PCBs. Many companies have relied on PFAS for decades to ensure the reliability and performance of their products. The ban would force these companies to find alternative materials and processes that can provide similar benefits without the associated health and environmental risks.
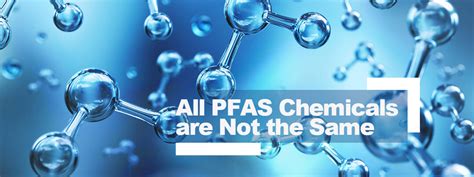
Implications for PCB Manufacturers
The EU’s proposed ban on PFAS in PCBs would have significant implications for manufacturers of these components. PCB manufacturers would need to find alternative materials and processes that can provide similar benefits to PFAS without the associated risks.
One potential alternative to PFAS in PCBs is the use of halogen-free materials. Halogen-free materials, such as polyphenylene oxide (PPO) and polyethylene terephthalate (PET), have been used in some PCB applications as a safer alternative to PFAS. These materials have similar properties to PFAS, such as water and oil repellency, but do not contain the same potentially harmful chemicals.
Another potential alternative is the use of conformal coatings. Conformal coatings are thin layers of protective material that are applied to PCBs to protect them from moisture, dust, and other contaminants. These coatings can be made from various materials, including acrylics, epoxies, and polyurethanes, and can provide similar benefits to PFAS without the associated risks.
However, transitioning to these alternative materials and processes may not be a simple or inexpensive process for PCB manufacturers. Companies may need to invest in new equipment, train their employees on new processes, and potentially redesign their products to accommodate the new materials. These changes could result in increased costs and potentially longer lead times for PCB production.
Material | Advantages | Disadvantages |
---|---|---|
Halogen-free (PPO, PET) | – Similar properties to PFAS (water/oil repellency) | – May not provide same level of performance as PFAS |
– Safer alternative without harmful chemicals | – Potentially more expensive than PFAS | |
Conformal coatings | – Thin protective layer for PCBs | – May not provide same level of protection as PFAS |
– Can be made from various safer materials | – Requires additional manufacturing step, increasing costs |
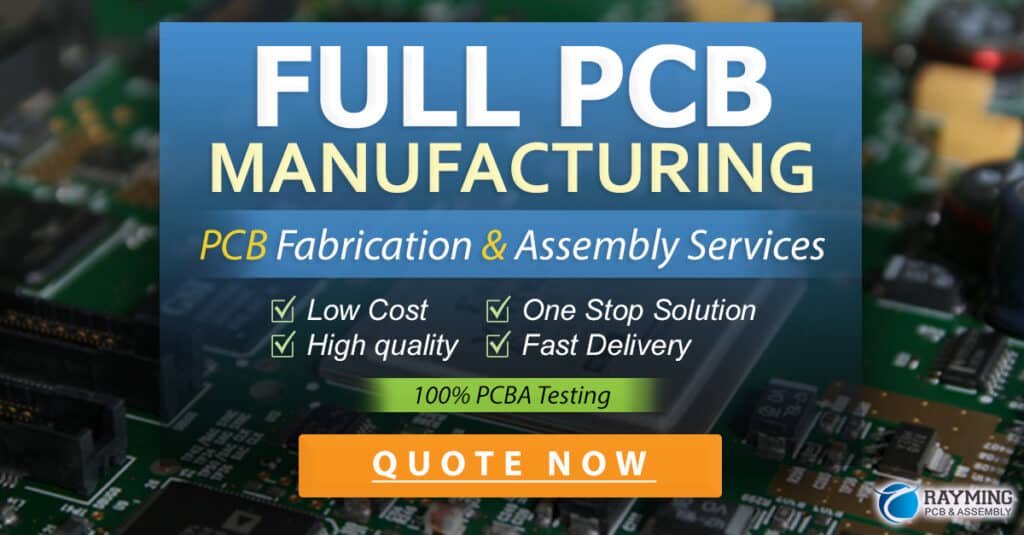
Impact on the Electronics Industry
The EU’s proposed ban on PFAS in PCBs would not only affect PCB manufacturers but also have broader implications for the electronics industry as a whole. Many electronic devices rely on PCBs that contain PFAS, and a ban on these chemicals could potentially disrupt the supply chain and increase costs for manufacturers.
In addition, the ban could also affect the performance and reliability of electronic devices. PFAS have been used in PCBs for decades because of their unique properties, and finding alternative materials that can provide the same level of performance may be challenging. This could potentially lead to reduced reliability and shorter lifespans for electronic devices.
However, the ban could also provide an opportunity for innovation in the electronics industry. Companies that are able to successfully transition to safer alternative materials and processes could potentially gain a competitive advantage in the market. Consumers are increasingly demanding products that are safer and more environmentally friendly, and companies that can meet these demands may be well-positioned for success in the future.
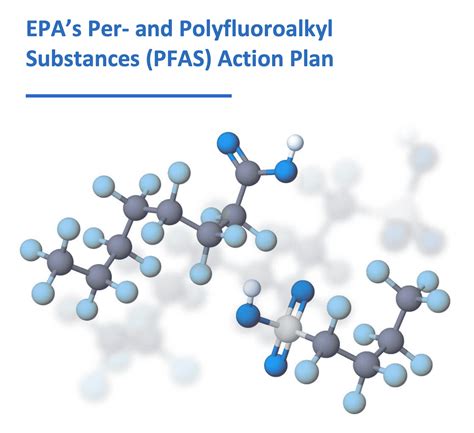
Conclusion
The EU’s proposed ban on PFAS in PCBs is a significant development that could have far-reaching implications for the electronics industry. PCB manufacturers would need to find alternative materials and processes that can provide similar benefits to PFAS without the associated health and environmental risks. This could result in increased costs and potentially longer lead times for PCB production.
However, the ban could also provide an opportunity for innovation in the industry, as companies seek to develop safer and more sustainable alternatives to PFAS. Ultimately, the success of the transition away from PFAS will depend on the ability of PCB manufacturers and the broader electronics industry to adapt to these changes and find new ways to ensure the reliability and performance of their products.
FAQ
-
What are PFAS, and why are they used in PCBs?
PFAS (per- and polyfluoroalkyl substances) are a group of man-made chemicals known for their water and oil repellency, temperature resistance, and friction reduction properties. They have been used in PCBs to protect the delicate electronic components from moisture, dust, and other contaminants, ensuring the reliability of the devices. -
Why is the EU proposing a ban on PFAS in PCBs?
The EU is proposing a ban on PFAS in PCBs due to growing concerns about the potential health and environmental risks associated with these chemicals. Studies have shown that PFAS can persist in the environment for long periods and accumulate in the bodies of humans and animals, potentially leading to various health problems. -
What are some potential alternatives to PFAS in PCBs?
Potential alternatives to PFAS in PCBs include halogen-free materials, such as polyphenylene oxide (PPO) and polyethylene terephthalate (PET), which have similar properties to PFAS but do not contain the same potentially harmful chemicals. Another alternative is the use of conformal coatings, which are thin layers of protective material applied to PCBs to protect them from contaminants. -
How might the EU’s proposed ban on PFAS affect the electronics industry?
The EU’s proposed ban on PFAS could disrupt the supply chain and increase costs for manufacturers in the electronics industry. Many electronic devices rely on PCBs containing PFAS, and finding alternative materials that provide the same level of performance may be challenging. However, the ban could also provide an opportunity for innovation, as companies seek to develop safer and more sustainable alternatives to PFAS. -
What challenges might PCB manufacturers face in transitioning away from PFAS?
PCB manufacturers may face challenges such as investing in new equipment, training employees on new processes, and potentially redesigning products to accommodate new materials when transitioning away from PFAS. These changes could result in increased costs and potentially longer lead times for PCB production. Additionally, finding alternative materials that provide the same level of performance as PFAS may be difficult.
Leave a Reply