Introduction to Rigid-Flex PCBs
Rigid-flex PCBs are a unique type of printed circuit board that combines the best features of rigid and flexible PCBs. They consist of rigid PCB sections connected by flexible PCB sections, enabling the board to be bent and folded to fit into tight spaces or unique enclosures.
Rigid-flex PCBs offer several advantages over traditional rigid PCBs:
- Space savings: The ability to fold the PCB allows for more compact and space-efficient designs
- Increased reliability: Integrated flexible connections eliminate the need for connectors and cables that can fail
- Improved signal integrity: Shorter traces enabled by the compact folded design minimize signal loss and interference
- Design versatility: Unique 3D designs and shapes are possible to fit the PCB into any enclosure
While rigid-flex PCBs provide compelling benefits, one of the main considerations is cost. In this article, we will dive into a detailed cost comparison of rigid-flex vs traditional rigid PCBs to help you make an informed decision for your next PCB design.
Factors Affecting Rigid-Flex PCB Cost
Several factors contribute to the higher cost of rigid-flex PCBs compared to rigid PCBs:
Materials Cost
Rigid-flex PCBs require specialty materials for the flexible circuit portions, such as polyimide films. These materials are more expensive than standard FR-4 materials used in rigid PCBs.
Flexible copper-clad laminates (FCCL) used in the flex layers also cost more than rigid copper-clad laminates. The table below shows a cost comparison of common FCCL and rigid materials:
Material | Typical Thickness | Cost per sq. meter |
---|---|---|
FR-4 | 0.4mm – 3.2mm | $10 – $30 |
Polyimide | 0.025mm – 0.127mm | $80 – $200 |
Flex adhesive | 0.025mm – 0.051mm | $50 – $100 |
As you can see, the raw material cost for flex layers can be 5-10x higher than rigid materials. For a rigid-flex PCB with multiple flexible layers, the material cost adds up quickly.
Fabrication and Assembly Complexity
The fabrication and assembly processes for rigid-flex PCBs are more complex and time-consuming compared to standard rigid PCBs:
- Flexible layers require special handling to prevent damage and maintain tight tolerances
- Adhesion of flexible and rigid layers requires precision lamination with careful heat and pressure control
- Coverlay application to protect and insulate flex layers adds an additional processing step
- SMT assembly of flex layers may require specialized equipment to handle the pliable surfaces
This added complexity translates to higher labor and overhead costs for the PCB manufacturer, which gets passed on to the customer.
Smaller Form Factors and Finer Features
Rigid-flex PCBs are often used to achieve high density interconnect (HDI) designs with fine lines and spaces to fit into compact products like smartphones, wearables, and medical implants.
Finer lines/spaces and microvias are more expensive to fabricate than standard larger geometry PCBs. The smaller the features, the higher the cost. A cost comparison of different HDI technologies is shown below:
HDI Technology | Typical Features | Fab Cost Adder |
---|---|---|
HDI Type I (1+N+1) | 4/4mil line/space, 0.006″ vias | 30-50% |
HDI Type II (2+N+2) | 3/3mil line/space, 0.004″ vias | 60-100% |
HDI Type III (3+N+3) | 2/2mil line/space, 0.002″ vias | 100-200% |
The combination of flex materials and HDI fabrication can result in rigid-flex PCBs costing 2-5x more than an equivalent rigid HDI board before even considering the additional flex fabrication and assembly steps.
Design and Engineering Effort
Rigid-flex PCB design requires additional skills and effort beyond standard rigid PCB design:
- 3D mechanical CAD modeling to define flex bend requirements and fit into the product enclosure
- Layer stackup design with careful consideration of rigid and flex layer sequencing
- Defining appropriate stiffener and coverlay areas
- Following flex and rigid-flex DFM guidelines to ensure manufacturability
- Working with the fabricator to validate the design, materials, stackup, and construction
Many PCB designers are not experienced with rigid-flex constructions and require additional training. The extra engineering effort and time spent on rigid-flex design, prototypes, and validation adds development cost to the project.
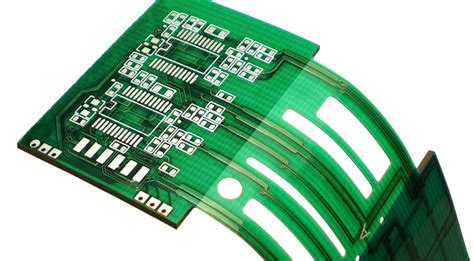
Rigid-Flex PCB Cost Comparison Examples
To put some real numbers to the relative cost differences, let’s look at a few rigid-flex PCB design examples and cost estimates from PCB manufacturers.
Example 1: Simple 4-layer rigid-flex
- 2″ x 3″ board size
- 4 layers (2 rigid, 2 flex)
- 6mil min trace/space
- Flex area 1″ x 2″
- 1oz copper, ENIG finish
- No components
Quantity | Rigid Cost | Rigid-Flex Cost | Multiplier |
---|---|---|---|
5 | $100 | $400 | 4.0x |
100 | $300 | $900 | 3.0x |
1000 | $800 | $2000 | 2.5x |
At production volumes, the rigid-flex adder drops to about 2.5x the cost of the equivalent rigid design.
Example 2: Complex 10-layer rigid-flex
- 3″ x 5″ board size
- 10 layers (4 rigid, 6 flex)
- 4mil min trace/space
- 2 flex areas 1″ x 3″
- Mixed 1oz/0.5oz copper, ENIG
- No components
Quantity | Rigid Cost | Rigid-Flex Cost | Multiplier |
---|---|---|---|
5 | $500 | $2500 | 5.0x |
100 | $1500 | $5000 | 3.3x |
1000 | $4000 | $10000 | 2.5x |
Even at higher volumes, a complex rigid-flex can still cost 2.5-3x more than a multilayer rigid board.
Example 3: Rigid-flex + component assembly
- 2″ x 4″ board size
- 6 layers (4 rigid, 2 flex)
- 5mil min trace/space
- 1 flex area 1″ x 2″
- 1oz copper, ENIG
- 50 SMT components
Quantity | Rigid Cost | Rigid-Flex Cost | Multiplier |
---|---|---|---|
5 | $400 | $1500 | 3.8x |
100 | $1000 | $3000 | 3.0x |
1000 | $3000 | $7000 | 2.3x |
With the component assembly included, the overall cost multiplier of the rigid-flex drops somewhat since the assembly effort is similar between the rigid and rigid-flex boards. But the premium for rigid-flex is still substantial.
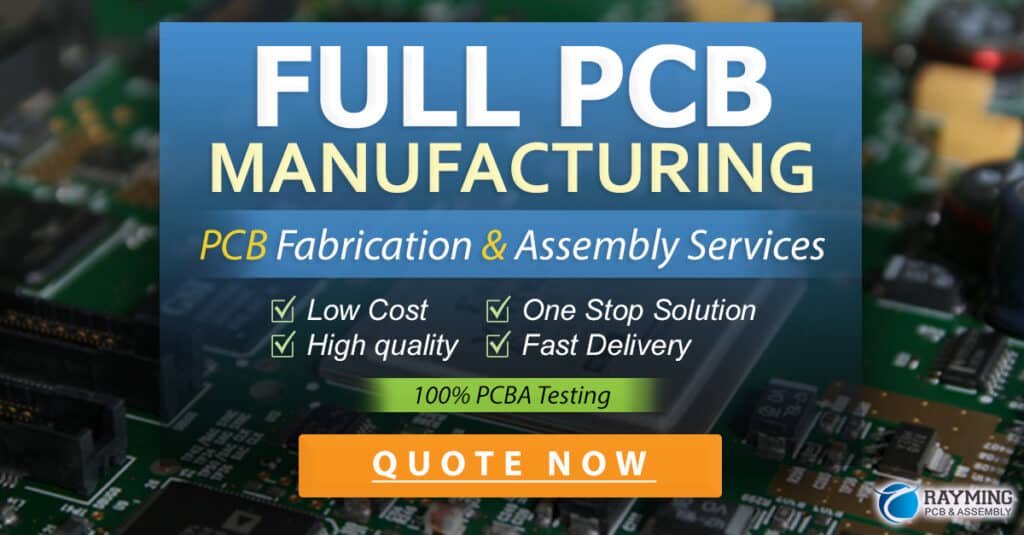
Weighing Cost vs Benefits for Rigid-Flex
Given the significant cost premium for rigid-flex PCBs, it’s important to carefully weigh the cost vs benefits to determine if the additional expense is justified for your specific application.
Rigid-flex makes sense when:
- The space savings, reliability, and performance benefits are critical to the product’s value proposition and competitive differentiation
- The product has a high enough selling price and margins to absorb the higher PCBA cost
- The expected production volumes are high enough to amortize the NRE and setup costs
- The PCBA is a small portion of the total product BOM cost
- Rigid-flex enables a compact, elegant product design that would be impossible otherwise
On the other hand, rigid-flex may not be worth the cost when:
- The product has slim margins and is highly cost sensitive
- Lower production volumes make it hard to recover high NRE costs
- The PCBA makes up a large portion of the product BOM cost
- A larger or less integrated product design using rigid PCBs is acceptable
- The specific rigid-flex benefits don’t add meaningful value to the end product
Ultimately, it’s up to you and your product team to determine if the benefits of rigid-flex outweigh the higher costs for your particular project.
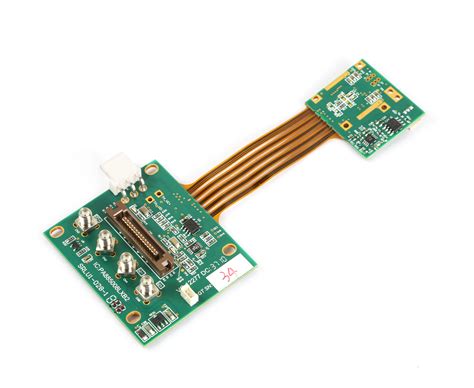
Strategies to Reduce Rigid-Flex PCB Costs
If you’ve determined that rigid-flex is the right solution for your product, here are some strategies to help reduce the cost:
Limit flex layer count
Each additional flex layer adds significant material and processing cost. Use the minimum number of flex layers required to route all signals and make the necessary connections between rigid sections.
Simplify the stackup
Minimize the number of different materials and transition layers in the stackup. A simpler stackup is easier and cheaper to fabricate. Consult with your fabricator for stackup recommendations to meet your requirements.
Avoid thin flexible laminates
Whenever possible, use flexible laminates that are at least 2 mils (50 microns) thick. Thinner laminates are more difficult to handle and laminate, requiring extra care that adds cost.
Increase flex feature sizes
Use wider traces and spaces on flexible layers to improve yields and reduce cost. Avoid pushing the fab limits unless absolutely necessary.
Panelize designs
If your design is smaller than the maximum panel size, panelize multiple copies onto one panel to amortize the fab and assembly setup costs.
Consider alternative constructions
Variations on classic rigid-flex can provide a good balance of flexibility and cost. For example:
- Rigid-flex-rigid: Rigid boards connected by flex jumpers without flex layers in the rigid areas
- Flex tails: Rigid board with a flex extension for connectors
- Multi-step rigid: Multiple rigid PCBs with stepped contours connected by a flex section
Discuss options with your manufacturer to identify the most cost-effective approach for your design.
Conclusion
In summary, rigid-flex PCBs offer many compelling benefits over traditional rigid PCBs but come with a significant cost premium due to materials, complexity, and NRE. A rigid-flex PCB can easily cost 2-5x more than an equivalent rigid PCB.
Consider rigid-flex when the space, reliability, and performance advantages are critical to the success of your product and can justify the higher cost. Work closely with your design team and fabricator to minimize layer counts, materials, and features and identify the most cost-effective construction.
By making informed design decisions and tradeoffs, you can harness the benefits of rigid-flex technology while keeping costs in check. The result will be an elegant, integrated, high-performance product that delights your customers and beats the competition.
Frequently Asked Questions
1. When is rigid-flex the right choice for a product?
Rigid-flex is ideal when space savings, reliability, and signal integrity are top priorities and the product has sufficient margins and volumes to absorb the higher cost. It enables sleek packaging of electronics in tight spaces.
2. What are the key cost drivers for rigid-flex PCBs?
The main cost drivers are specialty flex materials, complex fabrication and assembly processes for combining rigid and flex layers, finer feature sizes, and additional engineering effort required for rigid-flex design and DFM compared to rigid boards.
3. How much more does a rigid-flex PCB cost vs a rigid PCB?
The cost multiplier depends on the complexity of the design, but a typical rigid-flex board will cost 2-5 times more than an equivalent rigid PCB, with the premium being higher for lower volumes.
4. Are there any ways to reduce the cost of rigid-flex?
Yes, you can reduce rigid-flex costs by limiting the number of flex layers, simplifying the stackup, using thicker flex materials, increasing flex feature sizes, panelizing the design, and considering alternative rigid-flex constructions. Work closely with your PCB supplier for cost-optimized recommendations.
5. What if rigid-flex is too expensive for my product?
If rigid-flex is cost-prohibitive but you still need some flexibility, consider alternative constructions like rigid-flex-rigid, flex tails, or multi-step rigid designs that provide a good balance of flexibility and cost. You can also explore rigid PCB designs with cables and connectors, although this may compromise reliability and the slimness of packaging.
Leave a Reply