Why Copper Efficiency Matters in Electronics
Copper is one of the most widely used materials in electronics due to its excellent electrical and thermal conductivity properties. It is a key component in printed circuit boards (PCBs), wiring, connectors, transistors, integrated circuits, and many other electronic devices and components.
However, copper is also a relatively expensive metal. The price of copper has risen significantly in recent years due to growing global demand, supply constraints, and other market factors. This has put pressure on electronics manufacturers to optimize their use of copper in order to control costs while still delivering high-performance products.
Copper efficiency refers to the ability to maximize the functionality and performance of electronics while minimizing the amount of copper used. Improving copper efficiency can provide several important benefits for electronics designers and manufacturers:
- Lower material costs
- Smaller and lighter products
- Improved electrical efficiency
- Better thermal management
- Enhanced reliability and durability
In this article, we’ll take an in-depth look at copper efficiency and its impact on electronics design and manufacturing. We’ll explore the key factors that influence copper efficiency, best practices and strategies for optimizing copper usage, and the latest trends and innovations in this important field.
Key Factors Affecting Copper Efficiency
There are several critical factors that impact overall copper efficiency in electronics:
Copper Purity and Conductivity
The purity and conductivity of the copper used plays a major role in efficiency. Higher purity copper generally has better conductivity, allowing electrical current to flow with less resistance. This means that less copper is needed to achieve the same level of electrical performance.
Common grades of copper used in electronics include:
Copper Grade | Purity | Conductivity (% IACS) |
---|---|---|
C101xx | 99.99% | 101% |
C110xx | 99.90% | 100% |
C102xx | 99.95% | 100% |
*IACS = International Annealed Copper Standard
Using the highest purity copper appropriate for the application helps maximize copper efficiency. However, ultra-high purity copper is also more expensive, so designers must balance performance and cost considerations.
Copper Thickness and Weight
The thickness and weight of the copper used also significantly impacts efficiency. In general, thinner and lighter copper traces, layers, and components allow material usage to be minimized while still providing the necessary connectivity and current carrying capacity.
However, using copper that is too thin for the application can degrade performance and reliability. Copper traces and wires must be sized appropriately to handle the required current loads without excessive resistive losses or heat generation.
IPC standards provide guidelines for minimum copper thickness and width based on current carrying requirements:
Current (amps) | Minimum Copper Thickness (μm) |
---|---|
0.2 | 17.5 |
0.5 | 35 |
1 | 70 |
2 | 140 |
*Per IPC-2152 for external layers at 10°C rise above ambient.
Designers must balance the need to minimize copper weight and thickness with the electrical and thermal demands of the application. Using copper that is too thin can result in issues like voltage drop, power loss, overheating, and device failure.
Circuit Density and Routing
The density and routing of copper traces and interconnects on PCBs and substrates also play a key role in copper efficiency. Denser circuits with finer pitch traces, vias, and components allow functionality to be maximized in a smaller area.
However, denser, more complex circuits are also more challenging to route effectively. Signal integrity issues like crosstalk, EMI, and impedance mismatches become more likely as trace spacing decreases. Smaller vias and pads are more prone to manufacturing defects that can impact reliability.
Designing circuits with the optimal balance of density, routing efficiency, manufacturability, and performance is critical for maximizing copper efficiency. Tools like PCB layout software, simulation, and design for manufacturing (DFM) analysis help engineers find the sweet spot.
3D and Additive Manufacturing
Newer manufacturing technologies like 3D printing and additive manufacturing of electronics provide additional opportunities for improving copper efficiency. 3D circuits allow more creative routing and component placement in three dimensions, enabling smaller, denser designs.
Additive manufacturing techniques like inkjet printing can allow finer, variable-thickness copper traces to be deposited on-demand, reducing waste. However, the conductivity and performance of printed copper is generally lower than solid copper foil. Designers must carefully evaluate the tradeoffs of these emerging technologies.
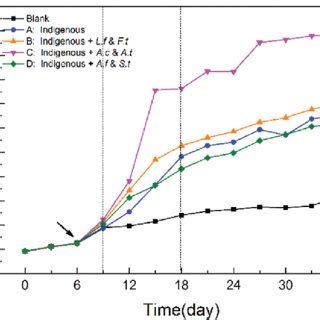
Strategies for Optimizing Copper Efficiency
So how can electronics designers and manufacturers optimize copper efficiency in practice? Here are some key strategies and best practices:
Optimize PCB Layer Stack-Up
Effective PCB layer stack-up design is one of the most important considerations for copper efficiency. The number, thickness, and arrangement of copper and insulating layers determines many key aspects of performance, manufacturability, and material usage.
Some best practices for optimizing stack-ups include:
- Use the minimum number of layers required to route all signals and power traces effectively
- Use thinner copper for high-density signal layers and thicker copper for power traces
- Use a symmetrical stack-up to minimize warpage and simplify manufacturing
- Consider HDI techniques like blind and buried vias to maximize routing density
- Use wider traces for improved current capacity and thinner traces for density as needed
Designers must collaborate closely with manufacturers to develop stack-ups that balance all electrical, mechanical, thermal, and economic requirements. Simulation tools can help validate the performance of proposed stack-ups prior to building physical prototypes.
Use Copper Pours and Planes
Using large copper pours and planes instead of individual traces can significantly improve copper utilization and efficiency. Copper pours help minimize resistance and inductance, provide shielding, and aid heat dissipation.
Some tips for effective use of copper pours and planes include:
- Use pours to provide low-impedance current paths and minimize loop area
- Use copper planes to distribute power and ground with low resistance
- Use pours as EMI shields to contain high-frequency noises
- Tie copper pours to ground with vias to provide shielding and heat sinking
- Size copper pours appropriately for current loads to avoid excessive waste
Copper pours and planes do consume more area than individual traces. Designers must balance the electrical benefits with density and routing considerations. Pours should be used strategically in areas that require the most shielding, power delivery, or heat sinking capacity.
Minimize Plated Through-Hole Vias
Plated through-hole (PTH) vias can be a significant source of copper usage in multi-layer PCB designs. Large vias that span the entire board consume more copper and occupy more space than smaller blind and buried vias or microvias.
Strategies to minimize the impact of PTH vias include:
- Use blind and buried vias to connect only the layers required, reducing overall span
- Use microvias to minimize diameter and capture pad size
- Optimize via placement to minimize stub length and improve routing
- Use via-in-pad techniques to place vias directly under components
- Fill unused vias to improve copper utilization and structural integrity
However, HDI techniques like blind/buried vias and microvias do add manufacturing cost and complexity compared to simple PTH designs. Designers must weigh the copper efficiency benefits against any tradeoffs in cost, reliability, or turnaround time.
Optimize Pad and Foot Geometries
The size and shape of component pads and lead foot geometries also impact copper efficiency. Smaller pads and finer-pitch leads consume less copper and allow denser component placement. However, overly small pads and feet can pose manufacturing and reliability challenges.
Some strategies for optimizing pad and foot geometries include:
- Use the smallest pad size appropriate for the component and assembly process
- Use oblong or rectangular pads to maximize copper utilization
- Optimize pad-to-hole ratio for PTH components to minimize annular ring
- Use fine-pitch leads like QFN and BGA to minimize foot size
- Use copper defined pads to maximize utilization on fine-pitch components
The specific pad and foot geometries used must be carefully matched to the capabilities of the manufacturing process. Designers should work closely with manufacturers to ensure that proposed geometries are achievable and reliable in high-volume production.
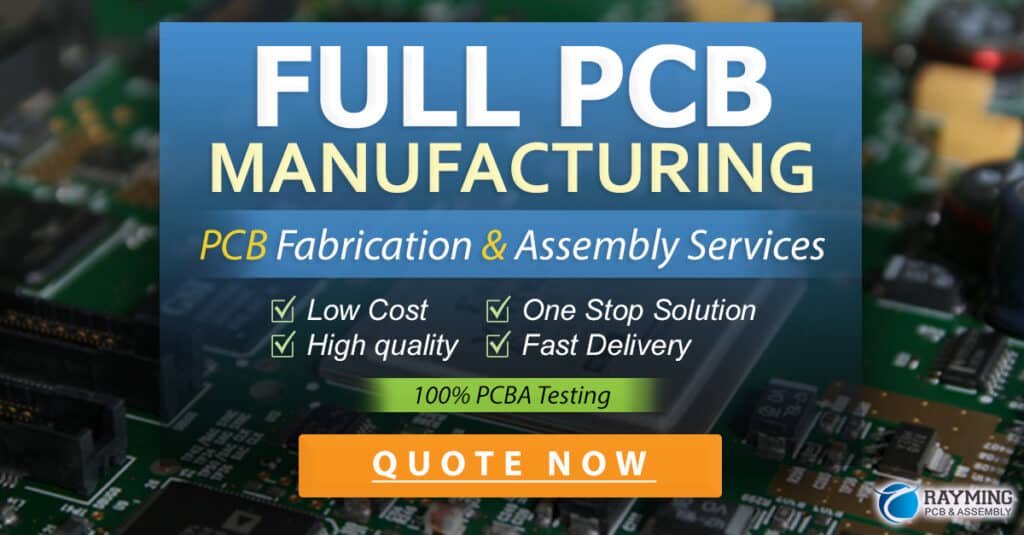
Industry Trends and Innovations
The electronics industry is continually innovating to improve copper efficiency and performance. Here are some of the latest trends and developments:
HDI and Advanced Packaging
High-density interconnect (HDI) and advanced packaging technologies are enabling denser, more efficient electronics designs. HDI techniques like blind/buried vias, microvias, and via-in-pad allow more interconnects to be routed in a smaller area.
Advanced packaging technologies like 2.5D interposers and 3D stacked die also improve efficiency by allowing chips to be interconnected vertically rather than horizontally. This enables shorter, denser interconnects compared to traditional PCB-level routing.
Flexible and Stretchable Electronics
Flexible and stretchable electronics are an emerging field that allows circuits to be built on thin, bendable substrates like polymers or textiles. This enables novel form factors and applications like wearables, medical implants, and soft robotics.
Copper traces on flex circuits can be built with thinner, more ductile copper foils that enable flexibility while minimizing material usage. However, the mechanical stresses of bending and stretching pose challenges for maintaining conductivity and reliability over time.
Graphene and Carbon Nanotubes
Graphene and carbon nanotubes (CNTs) are nanomaterials with excellent electrical and thermal conductivity properties. They have the potential to augment or replace copper in some electronics applications, enabling thinner, lighter, and more efficient designs.
However, the manufacturing processes for graphene and CNT electronics are still relatively immature compared to traditional PCB and semiconductor fabrication. More research is needed to scale up these technologies for high-volume, cost-sensitive applications.
Digital Twin and Simulation
Digital twin and simulation technologies are helping electronics designers optimize copper efficiency and performance in the virtual world before committing to physical prototypes. These tools allow engineers to model and analyze the electrical, thermal, and mechanical behavior of proposed designs in great detail.
By simulating the impact of different materials, geometries, and layouts, designers can find the optimal balance of copper usage, performance, and manufacturability for each application. Digital twins also enable more rapid iteration and optimization cycles, reducing time-to-market and development costs.
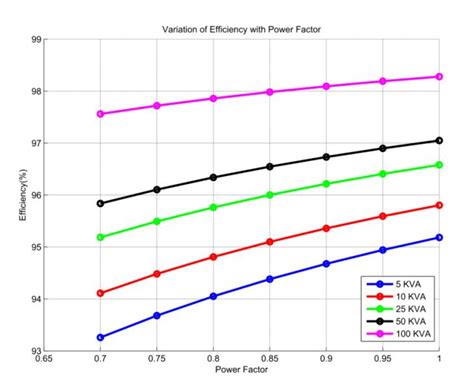
Frequently Asked Questions
What is copper efficiency and why is it important in electronics?
Copper efficiency refers to the ability to maximize the functionality and performance of electronics while minimizing the amount of copper used. It is important because copper is a relatively expensive material, and using it efficiently can help reduce costs, improve performance, and enable smaller and lighter products.
What are some key factors that affect copper efficiency?
Some of the key factors that affect copper efficiency include:
- Copper purity and conductivity
- Copper thickness and weight
- Circuit density and routing
- 3D and additive manufacturing technologies
Designers must balance these factors to find the optimal combination of performance, manufacturability, and cost for each application.
What are some strategies for optimizing copper efficiency in PCBs?
Some strategies for optimizing copper efficiency in PCBs include:
- Optimizing layer stack-up with the minimum number of layers and appropriate copper weights
- Using copper pours and planes for shielding, power delivery, and heat dissipation
- Minimizing plated through-hole vias with HDI techniques like blind/buried vias and microvias
- Optimizing component pad and lead foot geometries for density and manufacturability
Designers should collaborate closely with manufacturers to ensure that proposed strategies are achievable and reliable in high-volume production.
What are some of the latest industry trends and innovations related to copper efficiency?
Some of the latest trends and innovations related to copper efficiency include:
- HDI and advanced packaging technologies like 2.5D interposers and 3D stacked die
- Flexible and stretchable electronics with thin, ductile copper traces
- Graphene and carbon nanotube nanomaterials with excellent conductivity properties
- Digital twin and simulation tools for virtual optimization and analysis
These emerging technologies are enabling new levels of density, performance, and efficiency in electronics design and manufacturing.
How can designers balance copper efficiency with other important factors like cost and reliability?
Balancing copper efficiency with cost and reliability requires careful tradeoffs and analysis. Some strategies include:
- Using the highest-purity copper appropriate for the application while considering cost
- Optimizing copper thickness and geometry for current carrying capacity and manufacturability
- Leveraging simulation and digital twin tools to find the optimal balance of factors
- Collaborating closely with manufacturers to ensure designs are producible and reliable
Ultimately, the specific balance of copper efficiency, cost, and reliability will depend on the unique requirements and constraints of each application. Designers must carefully weigh the tradeoffs and make informed decisions based on data and analysis.
Conclusion
Copper efficiency is a critical consideration for electronics designers and manufacturers looking to optimize performance, cost, and form factor. By understanding the key factors that influence copper usage and implementing best practices for design and manufacturing, engineers can create more efficient and effective products.
As the demand for smaller, lighter, and more powerful electronics continues to grow, innovations in materials, packaging, and manufacturing technologies will play an increasingly important role in driving copper efficiency forward. By staying at the forefront of these trends and leveraging the latest tools and techniques, the electronics industry can continue to push the boundaries of what is possible.
Ultimately, the goal of copper efficiency is not just to use less material, but to create electronics that are more sustainable, affordable, and impactful for society as a whole. By working together to optimize this vital resource, we can enable a new generation of devices and applications that transform the way we live, work, and communicate.
Leave a Reply