What is FR4 PCB?
FR4 PCB, also known as Flame Retardant 4 Printed Circuit Board, is a type of printed circuit board made from a composite material composed of woven fiberglass cloth with an epoxy resin binder. The “FR” stands for Flame Retardant, and the “4” indicates the grade of the material. FR4 is the most commonly used PCB material due to its excellent mechanical, electrical, and thermal properties.
Composition of FR4 PCB
FR4 PCB is made up of two main components:
- Fiberglass cloth: This is a woven fabric made from fine glass fibers, which provides the PCB with its strength and dimensional stability.
- Epoxy resin: This is a thermosetting polymer that acts as a binder, holding the fiberglass cloth together and providing insulation between the copper layers.
The combination of these two materials creates a strong, durable, and electrically insulating substrate for the copper traces and components that make up the circuit.
Properties of FR4 PCB
FR4 PCB has several desirable properties that make it a popular choice for a wide range of applications:
- High mechanical strength: The fiberglass reinforcement provides excellent tensile and flexural strength, making FR4 PCBs resistant to bending and breaking.
- Flame retardancy: The epoxy resin used in FR4 PCBs is designed to be flame-retardant, which helps prevent the spread of fire in case of overheating or short circuits.
- Good electrical insulation: FR4 has a high dielectric constant and low dielectric loss, which makes it an excellent electrical insulator.
- Thermal stability: FR4 PCBs have a glass transition temperature (Tg) of around 130°C to 140°C, which means they can withstand high temperatures without deforming or losing their mechanical properties.
- Moisture resistance: The epoxy resin in FR4 PCBs provides good resistance to moisture absorption, which helps maintain the board’s electrical and mechanical properties in humid environments.
Applications of FR4 PCB
Due to its versatility and desirable properties, FR4 PCB is used in a wide range of applications, including:
- Consumer electronics: Smartphones, laptops, tablets, and other consumer devices often use FR4 PCBs due to their durability and reliability.
- Industrial electronics: FR4 PCBs are used in industrial control systems, automation equipment, and power electronics due to their ability to withstand harsh environments.
- Medical devices: The flame retardancy and high electrical insulation of FR4 PCBs make them suitable for use in medical equipment, such as patient monitors and diagnostic devices.
- Automotive electronics: FR4 PCBs are used in various automotive applications, including engine control units, infotainment systems, and driver assistance systems.
- Telecommunications: Network switches, routers, and other telecommunications equipment often use FR4 PCBs due to their high-speed signal integrity and reliability.
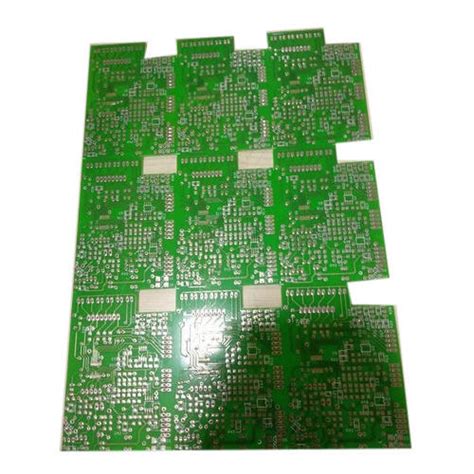
Manufacturing Process of FR4 PCB
The manufacturing process of FR4 PCB involves several steps:
- Designing the PCB layout: The first step is to design the PCB layout using specialized software, which includes placing components, routing traces, and defining the board’s dimensions.
- Printing the circuit pattern: The designed circuit pattern is printed onto a photosensitive film or directly onto the copper-clad laminate using a laser printer or photoplotter.
- Etching the copper: The printed circuit pattern is used as a mask to selectively remove the unwanted copper from the laminate using a chemical etching process, leaving only the desired traces and pads.
- Drilling holes: Holes are drilled through the board to accommodate through-hole components and provide electrical connections between layers.
- Applying solder mask and silkscreen: A solder mask is applied to the board to protect the copper traces from oxidation and prevent solder bridges during assembly. A silkscreen layer is then added to provide component labels and other markings.
- Surface finishing: The exposed copper pads are coated with a surface finish, such as HASL (Hot Air Solder Leveling), ENIG (Electroless Nickel Immersion Gold), or OSP (Organic Solderability Preservative), to protect the copper from oxidation and improve solderability.
- Electrical testing: The finished PCB undergoes electrical testing to ensure that all connections are correct and there are no short circuits or open connections.
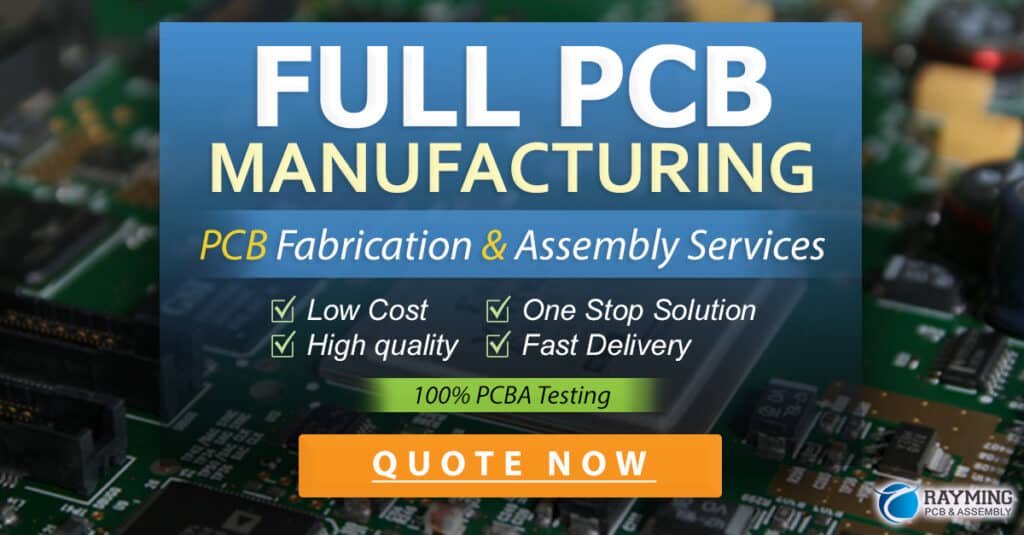
Advantages of FR4 PCB
FR4 PCB offers several advantages over other PCB materials:
- Cost-effectiveness: FR4 is relatively inexpensive compared to other PCB materials, making it a cost-effective choice for many applications.
- Wide availability: FR4 is the most widely used PCB material, which means it is readily available from many suppliers and manufacturers.
- Versatility: FR4 PCBs can be used in a wide range of applications due to their excellent mechanical, electrical, and thermal properties.
- Reliability: The high strength and durability of FR4 PCBs make them reliable for long-term use, even in harsh environments.
- Ease of manufacturing: FR4 PCBs can be easily manufactured using standard PCB fabrication processes, which helps reduce production costs and lead times.
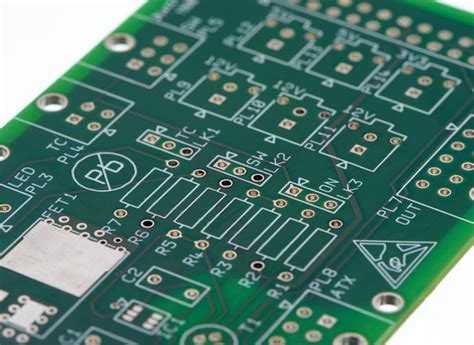
Disadvantages of FR4 PCB
Despite its many advantages, FR4 PCB also has some limitations:
- Limited high-frequency performance: FR4 PCBs have a relatively high dielectric constant and dissipation factor, which can limit their performance at high frequencies (above 1 GHz).
- Moisture absorption: Although FR4 PCBs have good moisture resistance, they can still absorb some moisture over time, which can affect their electrical and mechanical properties.
- Thermal expansion: FR4 PCBs have a higher coefficient of thermal expansion (CTE) compared to some other PCB materials, which can lead to thermal stress and warping in high-temperature applications.
Variations of FR4 PCB
There are several variations of FR4 PCB that offer improved properties for specific applications:
- High Tg FR4: This variation uses an epoxy resin with a higher glass transition temperature (Tg), typically around 170°C to 180°C, which provides better thermal stability and resistance to thermal stress.
- Halogen-free FR4: This variation uses a halogen-free epoxy resin, which reduces the environmental impact of the PCB and complies with regulations such as RoHS (Restriction of Hazardous Substances).
- Low-loss FR4: This variation uses a special epoxy resin formulation that provides lower dielectric loss and improved high-frequency performance compared to standard FR4.
Comparison of FR4 PCB with Other PCB Materials
There are several other PCB materials available, each with its own unique properties and advantages. Here is a comparison of FR4 PCB with some common alternatives:
Material | Advantages | Disadvantages |
---|---|---|
FR4 | Cost-effective, widely available, versatile, reliable | Limited high-frequency performance, moisture absorption, thermal expansion |
Rogers | Excellent high-frequency performance, low dielectric loss, stable dielectric constant | Expensive, limited availability, more difficult to manufacture |
Polyimide | High temperature resistance, low CTE, high flexibility | Expensive, moisture-sensitive, more difficult to process |
Alumina | Excellent thermal conductivity, high strength, low dielectric loss | Brittle, expensive, limited design flexibility |
The choice of PCB material depends on the specific requirements of the application, such as operating frequency, temperature range, environmental conditions, and cost constraints.
FAQ
1. What does FR4 stand for in FR4 PCB?
FR4 stands for Flame Retardant 4, which refers to the grade of the flame-retardant epoxy resin used in the PCB material.
2. Is FR4 PCB suitable for high-frequency applications?
Standard FR4 PCB has limitations in high-frequency applications (above 1 GHz) due to its relatively high dielectric constant and dissipation factor. For high-frequency applications, low-loss FR4 or other specialized materials like Rogers may be more suitable.
3. Can FR4 PCB be used in high-temperature environments?
Standard FR4 PCB has a glass transition temperature (Tg) of around 130°C to 140°C, which limits its use in high-temperature environments. For applications that require higher temperature resistance, high Tg FR4 or other materials like polyimide may be more appropriate.
4. Is FR4 PCB environmentally friendly?
Standard FR4 PCB contains halogenated flame retardants, which can have a negative environmental impact. However, halogen-free FR4 variations are available that comply with environmental regulations like RoHS.
5. How does the cost of FR4 PCB compare to other PCB materials?
FR4 PCB is generally more cost-effective compared to other PCB materials like Rogers, polyimide, and alumina. Its wide availability and ease of manufacturing contribute to its lower cost.
Conclusion
FR4 PCB is the most widely used PCB material due to its excellent balance of mechanical, electrical, and thermal properties, as well as its cost-effectiveness and wide availability. Its versatility makes it suitable for a wide range of applications, from consumer electronics to industrial and medical devices.
While FR4 PCB has some limitations, such as its performance at high frequencies and its thermal expansion, variations like high Tg FR4 and low-loss FR4 can address these issues for specific applications. Additionally, other PCB materials like Rogers, polyimide, and alumina offer unique properties that may be more suitable for certain applications.
When selecting a PCB material, it is essential to consider the specific requirements of the application, such as the operating frequency, temperature range, environmental conditions, and cost constraints. By understanding the properties and advantages of FR4 PCB and its variations, designers and engineers can make informed decisions when designing and manufacturing electronic devices.
Leave a Reply