What is a Bill of Materials (BOM)?
A Bill of Materials (BOM) is a hierarchical document that lists all the components, parts, and materials needed to manufacture a product. It includes the quantity of each item required, as well as information about their procurement, such as supplier details and lead times. The BOM is an essential tool for production planning, as it helps manufacturers determine the resources needed to complete a project and ensures that all necessary components are available when required.
The Importance of BOM in Production Planning
The BOM is a critical component of production planning for several reasons:
-
Resource Allocation: The BOM helps manufacturers allocate resources efficiently by providing a clear understanding of the materials and components required for production.
-
Cost Estimation: By listing all the necessary components and their quantities, the BOM enables manufacturers to estimate the total cost of production accurately.
-
Inventory Management: The BOM helps manufacturers maintain optimal inventory levels by providing information about the required quantities of each component, ensuring that there are no shortages or excess inventory.
-
Production Scheduling: The BOM aids in creating a production schedule by providing information about the lead times for each component, allowing manufacturers to plan accordingly.
BOM Levels in Production
The BOM is structured in a hierarchical manner, with different levels representing the various stages of production. Each level provides a more detailed breakdown of the components and materials required for that particular stage. The number of levels in a BOM depends on the complexity of the product being manufactured. Here are the most common BOM levels:
Level 0: End Product
The highest level in the BOM hierarchy is Level 0, which represents the finished product. This level provides an overview of the entire product and lists the main components or subassemblies that make up the final product. For example, in the BOM for a computer, Level 0 would list the main components such as the motherboard, processor, RAM, storage, and case.
Level 1: Main Components or Subassemblies
Level 1 of the BOM breaks down the main components or subassemblies listed in Level 0 into their constituent parts. This level provides more detail about each main component and lists the parts required to assemble them. In the computer example, Level 1 would list the specific components needed for each main component, such as the CPU, GPU, and power supply for the motherboard.
Level 2: Sub-Components
Level 2 of the BOM further breaks down the sub-components listed in Level 1 into their individual parts. This level provides a more granular view of the components required for each sub-assembly. In the computer example, Level 2 might list the specific capacitors, resistors, and integrated circuits needed for the motherboard’s power supply.
Level 3 and Beyond: Raw Materials
As the BOM progresses to Level 3 and beyond, it starts to list the raw materials required to manufacture the individual parts listed in the previous levels. These raw materials can include items such as metal sheets, plastic pellets, or electronic components. The number of levels in the BOM depends on the complexity of the product and the level of detail required for production planning.
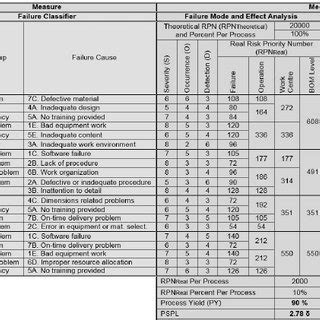
Example of a BOM for a Computer
To better understand the concept of BOM levels, let’s take a look at an example BOM for a computer:
Level | Component | Quantity |
---|---|---|
0 | Computer | 1 |
1 | Motherboard | 1 |
1 | Processor | 1 |
1 | RAM | 2 |
1 | Storage (SSD) | 1 |
1 | Case | 1 |
2 | Motherboard – CPU Socket | 1 |
2 | Motherboard – GPU Slot | 1 |
2 | Motherboard – RAM Slots | 2 |
2 | Motherboard – Power Supply | 1 |
3 | CPU Socket – LGA1151 | 1 |
3 | GPU Slot – PCIe 3.0 x16 | 1 |
3 | RAM Slots – DDR4 | 2 |
3 | Power Supply – ATX 12V | 1 |
In this example, the BOM starts with Level 0, which lists the computer as the end product. Level 1 breaks down the computer into its main components, such as the motherboard, processor, RAM, storage, and case. Level 2 further breaks down the motherboard into its sub-components, such as the CPU socket, GPU slot, RAM slots, and power supply. Finally, Level 3 lists the specific raw materials or components required for each sub-component, such as the LGA1151 socket for the CPU and the DDR4 slots for the RAM.
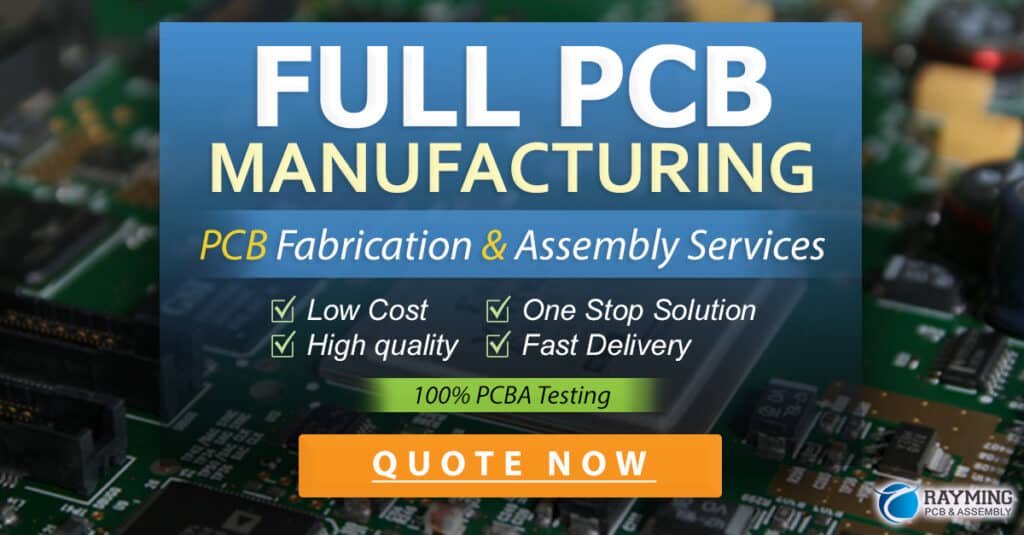
Benefits of Using a Multi-Level BOM
Using a multi-level BOM offers several benefits for production planning and execution:
-
Improved Visibility: A multi-level BOM provides a clear and detailed view of all the components and materials required for production, enabling better decision-making and resource allocation.
-
Enhanced Collaboration: By breaking down the product into multiple levels, a multi-level BOM facilitates collaboration among different teams, such as design, engineering, and procurement, ensuring that everyone is working towards the same goal.
-
Increased Efficiency: A well-structured multi-level BOM helps streamline the production process by providing a clear understanding of the components required at each stage, reducing the likelihood of delays or bottlenecks.
-
Better Inventory Management: By listing the exact quantities of components needed at each level, a multi-level BOM helps manufacturers maintain optimal inventory levels, reducing the risk of stockouts or overstocking.
-
Accurate Cost Estimation: A multi-level BOM enables manufacturers to estimate the total cost of production more accurately by providing a detailed breakdown of the costs associated with each component and material.
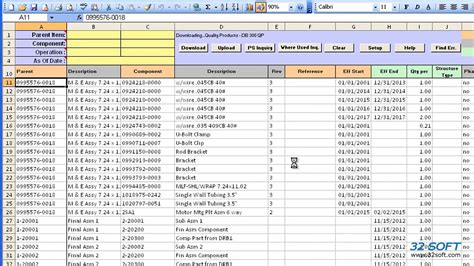
Challenges in Managing Multi-Level BOMs
While multi-level BOMs offer numerous benefits, they also present some challenges that manufacturers must address:
-
Complexity: As the number of levels in a BOM increases, so does its complexity. Managing a complex BOM requires robust systems and processes to ensure accuracy and consistency.
-
Data Management: Maintaining accurate and up-to-date information across multiple levels of a BOM can be challenging, especially when dealing with large and complex products. Manufacturers must invest in reliable data management systems to ensure the integrity of their BOM data.
-
Change Management: Any changes to the product design or components must be accurately reflected across all levels of the BOM. Manufacturers must have effective change management processes in place to ensure that all stakeholders are informed of any changes and that the BOM remains accurate.
-
Supplier Collaboration: Managing a multi-level BOM often involves coordinating with multiple suppliers, each responsible for providing different components or materials. Manufacturers must establish strong relationships with their suppliers and ensure that they can meet the required delivery schedules and quality standards.
Best Practices for Managing Multi-Level BOMs
To effectively manage multi-level BOMs and overcome the associated challenges, manufacturers should follow these best practices:
-
Use a Centralized BOM System: Implement a centralized BOM management system that allows all stakeholders to access and update BOM data in real-time, ensuring consistency and accuracy across all levels.
-
Establish Clear Naming Conventions: Develop and enforce clear naming conventions for components and materials to avoid confusion and ensure that all stakeholders are using the same terminology.
-
Implement Version Control: Use version control to track changes to the BOM over time, ensuring that all stakeholders are working with the most up-to-date information.
-
Conduct Regular BOM Reviews: Regularly review and update the BOM to ensure that it remains accurate and reflects any changes in the product design or components.
-
Collaborate with Suppliers: Foster strong relationships with suppliers and involve them in the BOM planning process to ensure that they can meet the required delivery schedules and quality standards.
Frequently Asked Questions (FAQ)
-
What is the difference between a single-level and multi-level BOM?
A single-level BOM lists all the components and materials required for a product in a single list, without breaking them down into sub-assemblies or sub-components. In contrast, a multi-level BOM organizes the components and materials into a hierarchical structure, with each level representing a different stage of the production process. -
How does a multi-level BOM help in cost estimation?
A multi-level BOM provides a detailed breakdown of the costs associated with each component and material, enabling manufacturers to estimate the total cost of production more accurately. By listing the exact quantities of components needed at each level, manufacturers can also identify opportunities for cost optimization. -
What are the key challenges in managing a multi-level BOM?
The key challenges in managing a multi-level BOM include complexity, data management, change management, and supplier collaboration. As the number of levels in a BOM increases, so does its complexity, requiring robust systems and processes to ensure accuracy and consistency. Maintaining accurate and up-to-date information across multiple levels of a BOM can also be challenging, especially when dealing with large and complex products. -
How can manufacturers ensure the accuracy of their multi-level BOM?
To ensure the accuracy of their multi-level BOM, manufacturers should implement a centralized BOM management system that allows all stakeholders to access and update BOM data in real-time. They should also establish clear naming conventions for components and materials, use version control to track changes over time, and conduct regular BOM reviews to ensure that the BOM remains accurate and reflects any changes in the product design or components. -
Why is supplier collaboration important in managing a multi-level BOM?
Managing a multi-level BOM often involves coordinating with multiple suppliers, each responsible for providing different components or materials. Collaborating with suppliers and involving them in the BOM planning process helps ensure that they can meet the required delivery schedules and quality standards, reducing the risk of delays or quality issues in the production process.
In conclusion, the different levels of production in BOM planning play a crucial role in ensuring the success of a manufacturing project. By breaking down the product into its constituent components and materials, a multi-level BOM provides a clear and detailed view of the resources required for production, enabling better decision-making, resource allocation, and cost estimation. While managing a multi-level BOM can be challenging, following best practices such as implementing a centralized BOM system, establishing clear naming conventions, and collaborating with suppliers can help manufacturers overcome these challenges and reap the benefits of a well-structured BOM.
Leave a Reply