Introduction to PCB Design Collaboration
Printed Circuit Board (PCB) design is a complex process that often involves multiple team members working together to create a functional and efficient board. PCB design collaboration is crucial for ensuring that all team members are on the same page, and that the final product meets the required specifications. With the advent of digital tools and software, PCB design collaboration has become easier and more efficient than ever before.
Benefits of PCB Design Collaboration
- Improved communication between team members
- Faster design iterations and revisions
- Reduced errors and mistakes
- Increased productivity and efficiency
- Better quality control and assurance
Key Features to Look for in a PCB Design Collaboration Tool
When selecting a tool for PCB design collaboration, there are several key features to look for that can greatly enhance the collaboration process and improve the overall quality of the final product.
1. Real-Time Collaboration
One of the most important features of a PCB design collaboration tool is the ability for team members to work together in real-time. This means that multiple users can access and edit the same PCB design simultaneously, without the need for manual file sharing or version control.
Real-time collaboration allows team members to communicate and make changes to the design in real-time, reducing the risk of errors and ensuring that everyone is working with the most up-to-date version of the design.
2. Version Control
Another essential feature of a PCB design collaboration tool is version control. Version control allows team members to track changes made to the design over time, and easily revert back to previous versions if needed.
This is particularly useful in situations where multiple team members are working on the same design simultaneously, as it allows for easy identification and resolution of conflicts or errors.
3. Design Rule Checking (DRC)
Design Rule Checking (DRC) is a critical feature of any PCB design software, and it is especially important in a collaborative environment. DRC ensures that the PCB design meets all of the necessary manufacturing and assembly requirements, such as minimum trace widths, clearances, and hole sizes.
A PCB design collaboration tool with built-in DRC can automatically check the design for errors and violations in real-time, reducing the risk of costly mistakes and ensuring that the final product is manufacturable.
4. Schematic Capture
Schematic capture is the process of creating a graphical representation of the electronic circuit that will be implemented on the PCB. A PCB design collaboration tool with schematic capture capabilities allows team members to easily create and edit schematics, and ensure that the schematic matches the physical layout of the board.
5. Bill of Materials (BOM) Management
A Bill of Materials (BOM) is a list of all the components and materials required to manufacture the PCB. A PCB design collaboration tool with BOM Management capabilities allows team members to easily create, edit, and share BOMs, ensuring that all necessary components are accounted for and ordered in a timely manner.
6. Integration with Other Tools
PCB design often involves the use of multiple tools and software, such as simulation software, CAD tools, and manufacturing tools. A PCB design collaboration tool that integrates with these other tools can greatly streamline the design process and reduce the risk of errors or incompatibilities.
For example, a PCB design collaboration tool that integrates with a CAD tool can allow team members to easily import and export design files, without the need for manual file conversions or translations.
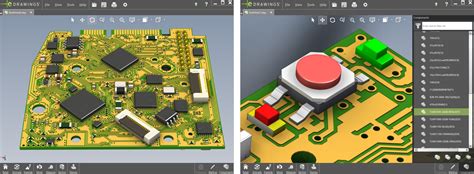
Top PCB Design Collaboration Tools
There are several PCB design collaboration tools available on the market, each with its own unique features and capabilities. Here are some of the top tools to consider:
1. Altium Designer
Altium Designer is a comprehensive PCB design software that includes powerful collaboration features, such as real-time collaboration, version control, and design rule checking. It also includes schematic capture and BOM management capabilities, and integrates with a wide range of other tools and software.
2. Cadence OrCAD
Cadence OrCAD is another popular PCB design software that includes collaboration features such as real-time collaboration and version control. It also includes schematic capture and BOM management capabilities, and integrates with other Cadence tools such as Allegro PCB Designer.
3. Mentor Graphics PADS
Mentor Graphics PADS is a PCB design software that includes collaboration features such as real-time collaboration and version control. It also includes schematic capture and BOM management capabilities, and integrates with other Mentor Graphics tools such as HyperLynx and Xpedition.
4. Zuken CR-8000
Zuken CR-8000 is a PCB design software that includes collaboration features such as real-time collaboration and version control. It also includes schematic capture and BOM management capabilities, and integrates with other Zuken tools such as E3.series and DS-CR.
5. Upverter
Upverter is a cloud-based PCB design collaboration tool that allows team members to work together in real-time, without the need for local software installations. It includes version control, design rule checking, and BOM management capabilities, and integrates with a wide range of other tools and software.
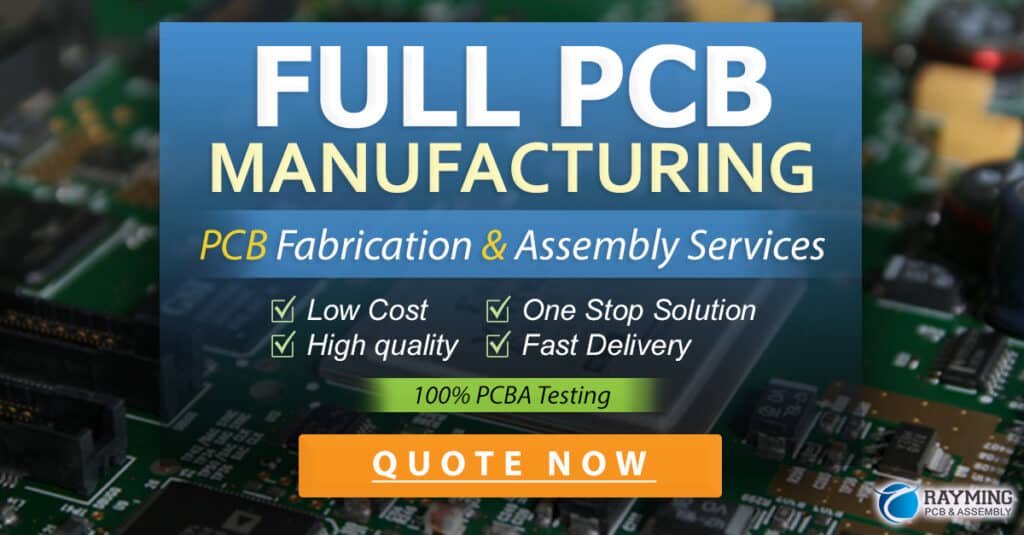
Comparison of PCB Design Collaboration Tools
Tool | Real-Time Collaboration | Version Control | DRC | Schematic Capture | BOM Management | Integration |
---|---|---|---|---|---|---|
Altium Designer | Yes | Yes | Yes | Yes | Yes | Wide range of tools |
Cadence OrCAD | Yes | Yes | Yes | Yes | Yes | Cadence tools |
Mentor Graphics PADS | Yes | Yes | Yes | Yes | Yes | Mentor Graphics tools |
Zuken CR-8000 | Yes | Yes | Yes | Yes | Yes | Zuken tools |
Upverter | Yes | Yes | Yes | Yes | Yes | Wide range of tools |
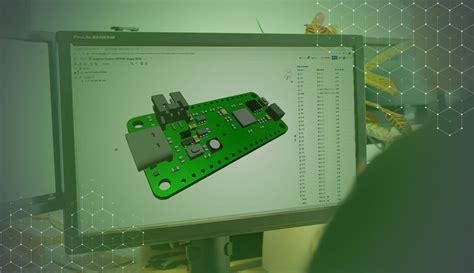
Factors to Consider When Selecting a PCB Design Collaboration Tool
When selecting a PCB design collaboration tool, there are several factors to consider to ensure that the tool meets the specific needs of your team and project.
1. Team Size and Structure
The size and structure of your team can greatly impact the type of collaboration tool that is best suited for your needs. For example, a small team may not require all of the advanced features and capabilities of a larger enterprise-level tool, while a larger team may require more robust collaboration and version control features to ensure smooth and efficient collaboration.
2. Project Complexity
The complexity of your PCB design project can also impact the type of collaboration tool that is best suited for your needs. A simple PCB design may not require all of the advanced features and capabilities of a more complex tool, while a highly complex design may require more advanced collaboration and design rule checking features to ensure accuracy and manufacturability.
3. Budget and Pricing
PCB design collaboration tools can vary greatly in terms of pricing and licensing models, so it is important to consider your budget and the long-term costs of the tool when making a selection. Some tools may require a significant upfront investment, while others may offer more flexible pricing models such as subscription-based or pay-per-use.
4. User Experience and Learning Curve
The user experience and learning curve of a PCB design collaboration tool can greatly impact the adoption and success of the tool within your team. A tool with a steep learning curve may require significant training and support, while a more intuitive and user-friendly tool may allow for faster adoption and more efficient collaboration.
5. Integration with Existing Tools and Workflows
Finally, it is important to consider how well the PCB design collaboration tool integrates with your existing tools and workflows. A tool that seamlessly integrates with your current CAD software, simulation tools, and manufacturing processes can greatly streamline the design process and reduce the risk of errors or incompatibilities.
Best Practices for PCB Design Collaboration
Once you have selected a PCB design collaboration tool that meets your specific needs, there are several best practices to follow to ensure successful and efficient collaboration within your team.
1. Establish Clear Communication Channels
Clear and open communication is essential for successful collaboration, so it is important to establish clear communication channels within your team. This may include regular team meetings, chat or messaging tools, or project management software to ensure that everyone is on the same page and working towards the same goals.
2. Define Roles and Responsibilities
Defining clear roles and responsibilities within your team can help ensure that everyone knows what is expected of them and can work together more efficiently. This may include assigning specific tasks or areas of responsibility to individual team members, or establishing a clear hierarchy or chain of command for decision-making and problem-solving.
3. Use Version Control Effectively
Version control is a critical feature of PCB design collaboration tools, but it is only effective if used properly. Establish clear guidelines for using version control within your team, such as creating new branches for each new feature or change, and merging changes back into the main branch only after thorough testing and review.
4. Conduct Regular Design Reviews
Regular design reviews can help catch errors or inconsistencies early in the design process, reducing the risk of costly mistakes or delays later on. Establish a regular schedule for design reviews, and involve all relevant team members to ensure that everyone has a chance to provide feedback and input.
5. Document Everything
Documentation is essential for successful collaboration, as it ensures that everyone has access to the same information and can refer back to previous decisions or changes as needed. Establish clear guidelines for documenting design changes, decisions, and rationales within your team, and use your collaboration tool’s built-in documentation features whenever possible.
FAQs
1. What is PCB design collaboration?
PCB design collaboration refers to the process of multiple team members working together to design and develop a printed circuit board (PCB). This can involve various team members with different skills and expertise, such as electrical engineers, PCB designers, and manufacturing specialists.
2. Why is PCB design collaboration important?
PCB design collaboration is important because it allows team members to work together more efficiently and effectively, reducing the risk of errors or delays and ensuring that the final product meets all necessary requirements and specifications. By collaborating closely throughout the design process, team members can catch potential issues early on, provide valuable feedback and input, and ensure that the final PCB design is optimized for manufacturability and performance.
3. What are some key features to look for in a PCB design collaboration tool?
Some key features to look for in a PCB design collaboration tool include real-time collaboration capabilities, version control, design rule checking (DRC), schematic capture, bill of materials (BOM) management, and integration with other tools and software. Other important factors to consider include ease of use, pricing and licensing models, and the specific needs and requirements of your team and project.
4. How do I choose the right PCB design collaboration tool for my team?
To choose the right PCB design collaboration tool for your team, consider factors such as team size and structure, project complexity, budget and pricing, user experience and learning curve, and integration with existing tools and workflows. It may also be helpful to evaluate and compare different tools based on their specific features and capabilities, and to seek input and feedback from other team members and stakeholders.
5. What are some best practices for successful PCB design collaboration?
Some best practices for successful PCB design collaboration include establishing clear communication channels, defining roles and responsibilities, using version control effectively, conducting regular design reviews, and documenting everything. By following these best practices and selecting the right collaboration tool for your needs, you can ensure that your team is able to work together efficiently and effectively to create high-quality PCB designs.
Conclusion
PCB design collaboration is a critical aspect of the PCB design process, allowing team members to work together more efficiently and effectively to create high-quality, manufacturable PCB designs. By selecting the right collaboration tool for your needs and following best practices for collaboration, you can streamline your design process, reduce the risk of errors and delays, and ensure that your final product meets all necessary requirements and specifications.
When selecting a PCB design collaboration tool, be sure to consider factors such as team size and structure, project complexity, budget and pricing, user experience and learning curve, and integration with existing tools and workflows. And once you have selected a tool, establish clear guidelines and best practices for collaboration within your team to ensure success.
By prioritizing collaboration and selecting the right tools and practices for your needs, you can take your PCB design process to the next level and create high-quality, innovative products that meet the needs of your customers and stakeholders.
Leave a Reply