The Importance of Substrate Focus in PCB Manufacturing
In the world of printed circuit board (PCB) manufacturing, the substrate is the foundation upon which everything else is built. Choosing the right substrate is critical to ensuring the performance, reliability, and longevity of the final product. That’s why the IPC, the global trade association for the electronics manufacturing industry, has been putting an increased focus on substrates in recent years.
What is a PCB Substrate?
A PCB substrate is the base material upon which the conductive copper traces and other components are attached. It provides mechanical support and electrical insulation for the circuit. The most common substrates used in PCB manufacturing are:
Substrate Material | Characteristics |
---|---|
FR-4 | Glass-reinforced epoxy laminate, good thermal and mechanical properties |
Polyimide | High temperature resistance, used in flexible PCBs |
Ceramic | Excellent thermal conductivity and stability, used in high-power applications |
Metal Core | Aluminum or copper base for improved heat dissipation |
IPC Standards for Substrates
The IPC has developed several standards related to PCB substrates to ensure consistency and quality across the industry. Some of the key standards include:
- IPC-4101: Specification for Base Materials for Rigid and Multilayer Printed Boards
- IPC-4202: Flexible Base Dielectrics for Use in Flexible Printed Circuitry
- IPC-4103: Specification for Base Materials for High Speed/High Frequency Applications
- IPC-4204: Flexible Metal-Clad Dielectrics for Use in Fabrication of Flexible Printed Circuitry
These standards provide guidelines for substrate material properties, testing methods, and quality requirements. By adhering to these standards, PCB manufacturers can ensure that their products meet the necessary performance and reliability criteria.
Trends in PCB Substrate Materials
As electronic devices continue to advance, so too must the substrates used in their construction. Here are some of the key trends driving substrate material selection and development:
High Frequency and High Speed Applications
With the increasing demand for 5G networks, IoT devices, and high-speed data transmission, PCBs must be able to handle higher frequencies and faster signal speeds. This requires substrates with lower dielectric constants and dissipation factors to minimize signal loss and distortion. Some of the materials being used for these applications include:
- Low-Dk/Df glass-reinforced hydrocarbon and ceramic laminates
- PTFE (Teflon) based substrates
- Liquid crystal polymer (LCP) films
Thermal Management
As electronic components become more powerful and densely packed, managing heat dissipation becomes a critical challenge. Substrates with high thermal conductivity help to spread heat more efficiently and prevent hot spots from forming. Metal core substrates, such as aluminum or copper, are commonly used for this purpose. Ceramic substrates, like aluminum nitride or beryllium oxide, offer even higher thermal conductivity for the most demanding applications.
Flexible and Wearable Electronics
The rise of wearable devices and flexible displays has driven demand for flexible PCB substrates. Polyimide films have been the go-to material for flexible PCBs due to their high temperature resistance and mechanical stability. However, newer materials like thermoplastic polyurethane (TPU) and polyethylene naphthalate (PEN) are being explored for their improved flexibility and cost-effectiveness.
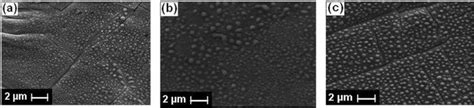
PCB Manufacturers’ Focus on Board-Level Considerations
While the IPC is focused on substrate standards, PCB manufacturers must also consider the bigger picture of the overall board design and fabrication process. Some of the key factors that manufacturers focus on include:
Layer Stack-Up Design
The arrangement of copper layers and dielectric materials in a PCB, known as the stack-up, plays a crucial role in signal integrity and EMI performance. Manufacturers work closely with designers to optimize the stack-up for the specific application, taking into account factors such as:
- Number of layers
- Thickness of copper and dielectric layers
- Dielectric constant and dissipation factor of substrate materials
- Controlled impedance requirements
Via Structure and Placement
Vias are the conductive holes that connect different layers of a PCB. The size, shape, and placement of vias can have a significant impact on signal quality and manufacturing yield. PCB manufacturers use advanced via technologies like microvias, blind and buried vias, and via-in-pad to achieve higher densities and better signal integrity.
Surface Finish Selection
The surface finish on a PCB serves to protect the exposed copper traces and pads from oxidation and provide a solderable surface for component attachment. The choice of surface finish depends on factors such as cost, reliability requirements, and compatibility with the assembly process. Some common surface finishes include:
- Hot Air Solder Leveling (HASL)
- Electroless Nickel Immersion Gold (ENIG)
- Immersion Silver
- Organic Solderability Preservative (OSP)
Manufacturability and Yield Optimization
PCB manufacturers continuously strive to improve their processes to achieve higher yields and lower costs. This involves optimizing every step of the fabrication process, from imaging and etching to lamination and testing. Some of the techniques used to improve manufacturability include:
- Design for Manufacturing (DFM) analysis
- Panelization and routing optimization
- Process control and statistical monitoring
- Automated optical inspection (AOI) and electrical testing
By focusing on these board-level considerations, PCB manufacturers can ensure that their products meet the required quality and reliability standards while also being cost-effective to produce.
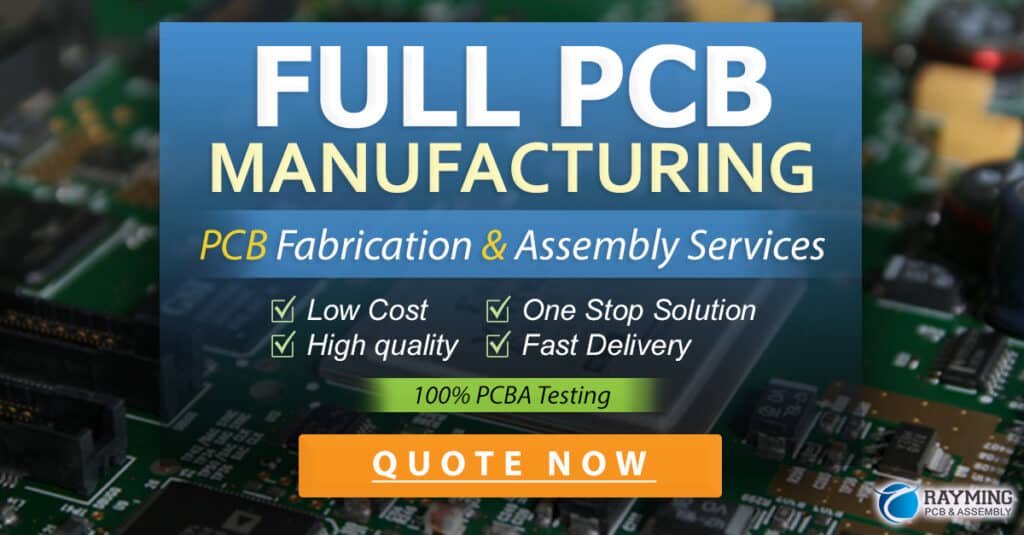
FAQ
Q1: What is the most common substrate material used in PCB manufacturing?
A1: FR-4, a glass-reinforced epoxy laminate, is the most widely used substrate material in PCB manufacturing due to its good balance of thermal, mechanical, and electrical properties.
Q2: Why are low-Dk and low-Df substrates important for high-speed applications?
A2: Substrates with low dielectric constant (Dk) and dissipation factor (Df) are important for high-speed applications because they minimize signal loss and distortion, allowing for faster signal transmission and higher frequencies.
Q3: What are the benefits of using metal core substrates in PCBs?
A3: Metal core substrates, such as aluminum or copper, offer improved thermal conductivity compared to traditional FR-4 substrates. This helps to spread heat more efficiently and prevent hot spots, making them ideal for applications with high power densities or thermal management challenges.
Q4: What is the role of surface finish in PCB manufacturing?
A4: The surface finish on a PCB serves two main purposes: protecting the exposed copper traces and pads from oxidation, and providing a solderable surface for component attachment during assembly. The choice of surface finish depends on factors such as cost, reliability requirements, and compatibility with the assembly process.
Q5: How can PCB manufacturers improve yield and reduce costs?
A5: PCB manufacturers can improve yield and reduce costs by optimizing every step of the fabrication process, from design to testing. This involves techniques such as Design for Manufacturing (DFM) analysis, process control and statistical monitoring, automated inspection, and continuous process improvement initiatives.
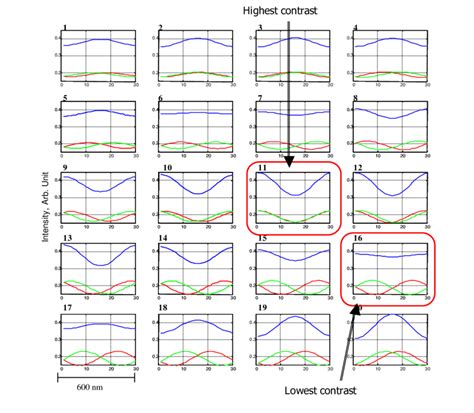
Conclusion
The importance of substrate focus in PCB manufacturing cannot be overstated. As the foundation of every circuit board, the substrate material choice has a profound impact on the performance, reliability, and manufacturability of the final product. The IPC’s increased focus on substrate standards, coupled with manufacturers’ attention to board-level considerations, ensures that the electronics industry can continue to push the boundaries of innovation while maintaining the highest levels of quality and consistency.
As new applications and technologies emerge, the demand for advanced substrate materials will only continue to grow. From high-speed digital to flexible and wearable electronics, the substrate will play a crucial role in enabling the next generation of electronic devices. By staying at the forefront of substrate development and manufacturing best practices, the PCB industry can meet these challenges head-on and deliver the cutting-edge solutions that our increasingly connected world demands.
Leave a Reply