Introduction
When designing electronic devices, one of the crucial decisions engineers face is choosing the right type of printed circuit board (PCB) for their application. Two common options are Rigid-Flex PCBs and multi-board PCBs. Both have their advantages and disadvantages, and the choice ultimately depends on the specific requirements of the project. In this article, we will explore the differences between rigid-flex PCBs and multi-board PCBs, their applications, and the factors to consider when deciding between the two.
What is a Rigid-Flex PCB?
A rigid-flex PCB is a hybrid circuit board that combines both rigid and flexible substrates. The rigid sections provide structural support and house the majority of the components, while the flexible sections allow for bending and folding, enabling the PCB to fit into tight spaces or conform to unique shapes. Rigid-flex PCBs are manufactured by laminating together multiple layers of rigid and flexible materials, such as polyimide or polyester, with copper traces and vias connecting the layers.
Advantages of Rigid-Flex PCBs
- Space Savings: Rigid-flex PCBs can be folded and shaped to fit into compact spaces, reducing the overall size of the device.
- Increased Reliability: By eliminating the need for connectors between rigid sections, rigid-flex PCBs minimize the risk of connection failures and improve overall reliability.
- Improved Signal Integrity: The continuous copper traces in rigid-flex PCBs reduce signal loss and interference compared to multi-board designs with connectors.
- Reduced Weight: Rigid-flex PCBs often require fewer components and connectors, resulting in a lighter overall assembly.
- Enhanced Durability: The flexible sections of rigid-flex PCBs can withstand repeated bending and flexing, making them suitable for applications with frequent movement or vibration.
Disadvantages of Rigid-Flex PCBs
- Higher Cost: Rigid-flex PCBs are generally more expensive to manufacture than multi-board PCBs due to the specialized materials and processing techniques required.
- Complex Design: Designing rigid-flex PCBs can be more challenging, as engineers must account for the mechanical properties of the flexible sections and ensure proper signal integrity.
- Limited Component Placement: The flexible sections of rigid-flex PCBs have limitations on the types and sizes of components that can be placed on them.
- Longer Lead Times: Manufacturing rigid-flex PCBs often requires more time due to the additional processing steps and specialized equipment involved.

What are Multi-Board PCBs?
Multi-board PCBs, also known as board-to-board or module-to-module PCBs, consist of multiple rigid circuit boards connected using connectors, cables, or board-to-board (B2B) stacking. Each board in a multi-board design can be optimized for its specific function, such as power management, signal processing, or user interface. The boards are then interconnected to form a complete system.
Advantages of Multi-Board PCBs
- Cost-Effective: Multi-board PCBs are typically less expensive to manufacture than rigid-flex PCBs, as they use standard rigid PCB materials and processes.
- Easier to Design: Designing multi-board PCBs is often simpler than rigid-flex PCBs, as each board can be designed independently and then integrated into the final assembly.
- Modular Design: Multi-board PCBs allow for a modular approach, where individual boards can be easily replaced or upgraded without redesigning the entire system.
- Flexibility in Component Placement: Multi-board designs offer more flexibility in component placement, as each board can be optimized for its specific components and functions.
- Shorter Lead Times: Manufacturing multi-board PCBs generally requires less time than rigid-flex PCBs, as the individual boards can be produced simultaneously using standard PCB fabrication processes.
Disadvantages of Multi-Board PCBs
- Larger Size: Multi-board PCBs often require more space than rigid-flex PCBs due to the need for connectors and cables between the boards.
- Lower Reliability: The use of connectors and cables in multi-board designs introduces potential points of failure, reducing overall reliability compared to rigid-flex PCBs.
- Signal Integrity Issues: Signal integrity can be compromised in multi-board designs due to the impedance mismatch and signal loss introduced by connectors and cables.
- Increased Weight: The additional connectors and cables in multi-board PCBs can result in a heavier overall assembly compared to rigid-flex PCBs.
- Reduced Durability: Multi-board PCBs may be less durable than rigid-flex PCBs, as the connectors and cables are susceptible to damage from vibration, shock, or repeated mating cycles.
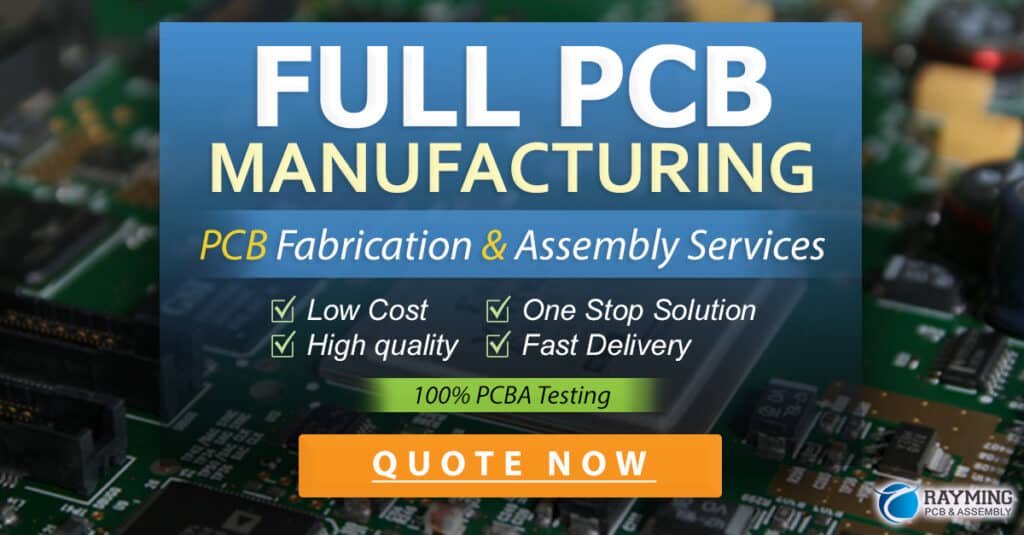
Factors to Consider When Choosing Between Rigid-Flex and Multi-Board PCBs
When deciding between rigid-flex and multi-board PCBs, engineers should consider the following factors:
- Space Constraints: If the device has limited space or requires a compact form factor, rigid-flex PCBs may be the better choice due to their ability to fold and conform to tight spaces.
- Reliability Requirements: For applications that demand high reliability, such as medical devices or aerospace systems, rigid-flex PCBs may be preferred due to their fewer points of failure and improved signal integrity.
- Cost and Budget: Multi-board PCBs are generally more cost-effective than rigid-flex PCBs, making them a better choice for projects with tight budgets or high-volume production.
- Design Complexity: Rigid-flex PCBs require more complex design considerations, such as the mechanical properties of the flexible sections and the placement of components. Multi-board PCBs may be simpler to design, as each board can be optimized independently.
- Time-to-Market: If a shorter development cycle is critical, multi-board PCBs may be the better option, as they typically have shorter lead times and can be designed and manufactured more quickly than rigid-flex PCBs.
- Modularity and Upgradability: Multi-board PCBs offer greater modularity, allowing for easier upgrades or replacements of individual boards without redesigning the entire system.
- Environmental Factors: Consider the operating environment of the device, such as temperature, humidity, vibration, and shock. Rigid-flex PCBs may be more suitable for applications with frequent movement or harsh conditions due to their enhanced durability.
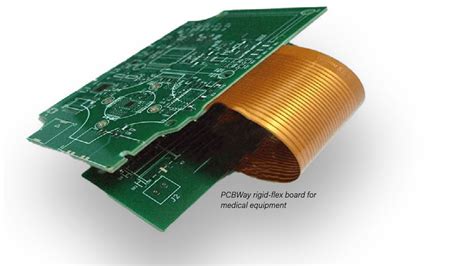
Applications of Rigid-Flex PCBs
Rigid-flex PCBs are commonly used in applications that require compact, reliable, and durable electronic assemblies. Some examples include:
- Wearable Devices: Smartwatches, fitness trackers, and medical wearables often use rigid-flex PCBs to achieve a compact and comfortable form factor.
- Aerospace and Defense: Rigid-flex PCBs are used in avionics, satellites, and military equipment due to their high reliability and ability to withstand harsh environments.
- Medical Devices: Implantable devices, surgical instruments, and diagnostic equipment may use rigid-flex PCBs for their compact size and reliability.
- Automotive Electronics: Rigid-flex PCBs are used in vehicle control modules, infotainment systems, and sensor assemblies, where space is limited and reliability is critical.
- Industrial Automation: Robots, machine vision systems, and control panels may employ rigid-flex PCBs for their durability and resistance to vibration and shock.
Applications of Multi-Board PCBs
Multi-board PCBs are used in a wide range of electronic devices and systems, particularly those that require modularity, cost-effectiveness, or easier maintenance. Some examples include:
- Consumer Electronics: Smartphones, tablets, laptops, and gaming consoles often use multi-board PCBs to allow for modular designs and easier upgrades.
- Industrial Equipment: Multi-board PCBs are used in control systems, power supplies, and data acquisition devices, where modularity and cost-effectiveness are important.
- Telecommunications: Network switches, routers, and base stations may use multi-board PCBs for their scalability and ability to accommodate various functions and components.
- Medical Devices: Non-implantable medical equipment, such as patient monitors and imaging systems, may use multi-board PCBs for their modularity and easier maintenance.
- Aerospace and Defense: Some aerospace and defense applications, such as ground control stations and test equipment, may use multi-board PCBs for their flexibility in component placement and easier upgrades.
Comparison Table: Rigid-Flex PCBs vs. Multi-Board PCBs
Factor | Rigid-Flex PCBs | Multi-Board PCBs |
---|---|---|
Space Savings | High | Low |
Reliability | High | Moderate |
Signal Integrity | High | Moderate |
Cost | High | Moderate |
Design Complexity | High | Moderate |
Component Placement | Limited on flexible sections | Flexible |
Lead Time | Longer | Shorter |
Modularity | Low | High |
Durability | High | Moderate |
Weight | Low | Moderate |
FAQ
-
Q: Can rigid-flex PCBs be repaired if damaged?
A: Repairing rigid-flex PCBs can be challenging due to their complex structure and the specialized materials used. In most cases, it is more cost-effective to replace the entire assembly rather than attempting to repair it. -
Q: Are there any limitations on the number of layers in a rigid-flex PCB?
A: The number of layers in a rigid-flex PCB is limited by the manufacturing capabilities of the PCB fabricator. Most rigid-flex PCBs have between 4 and 20 layers, although some advanced designs may have more. -
Q: Can multi-board PCBs be used in high-speed applications?
A: Multi-board PCBs can be used in high-speed applications, but careful design considerations are required to maintain signal integrity. Techniques such as impedance matching, shielding, and proper connector selection can help mitigate signal integrity issues. -
Q: How do the environmental effects (e.g., temperature, humidity) impact the choice between rigid-flex and multi-board PCBs?
A: Rigid-flex PCBs are generally more resistant to environmental factors due to their continuous structure and lack of connectors. Multi-board PCBs may be more susceptible to issues caused by temperature fluctuations, humidity, and vibration, as the connectors and cables can be affected by these factors. -
Q: Are there any specific design guidelines for rigid-flex PCBs?
A: When designing rigid-flex PCBs, engineers should consider factors such as bend radius, stiffener placement, and the mechanical properties of the flexible materials. It is essential to work closely with the PCB fabricator to ensure that the design is manufacturable and meets the required specifications.
Conclusion
Choosing between rigid-flex PCBs and multi-board PCBs depends on the specific requirements of the project, such as space constraints, reliability, cost, and time-to-market. Rigid-flex PCBs offer advantages in terms of space savings, reliability, and signal integrity, but they come at a higher cost and longer lead times. Multi-board PCBs are more cost-effective and offer greater modularity and flexibility in component placement, but they may have limitations in terms of size, reliability, and signal integrity.
When making the decision, engineers should carefully consider the factors discussed in this article and weigh the trade-offs between the two options. By understanding the strengths and weaknesses of rigid-flex and multi-board PCBs, designers can make informed choices that optimize the performance, reliability, and cost-effectiveness of their electronic devices.
Leave a Reply