Introduction to 3D-Printed Electronics
3D-printed electronics is an emerging field that combines additive manufacturing techniques with electronic components and conductive materials to create functional electronic devices and circuits. This technology has the potential to revolutionize the way we design, prototype, and manufacture electronics by enabling faster iteration, greater customization, and more complex geometries compared to traditional manufacturing methods.
The process of 3D printing electronics typically involves depositing conductive inks or pastes onto a substrate layer-by-layer to form interconnects, passive components (like resistors and capacitors), and even active components (like transistors and sensors). Various 3D printing technologies can be used, including:
Technology | Description |
---|---|
Inkjet Printing | Deposits droplets of conductive ink onto a substrate |
Aerosol Jet Printing | Uses a focused aerosol beam to deposit fine features |
Screen Printing | Pushes ink through a patterned mesh screen onto a substrate |
Extrusion Printing | Dispenses conductive paste through a nozzle |
These printing methods can be combined with traditional 3D printing techniques like fused deposition modeling (FDM) or stereolithography (SLA) to create multi-material, multi-functional 3D-printed devices.
Advantages and Applications of 3D-Printed Electronics
Rapid Prototyping and Iteration
One of the main advantages of 3D-printed electronics is the ability to quickly prototype and iterate on designs. Traditional PCB Fabrication methods can be time-consuming and expensive, especially for small batches or complex designs. With 3D printing, designers can create functional prototypes in a matter of hours, test them, and make changes as needed. This rapid iteration cycle can significantly speed up the product development process and reduce costs.
Customization and Personalization
3D printing allows for a high degree of customization and personalization in electronic devices. Instead of being limited to standard PCB designs and form factors, designers can create electronics that are tailored to specific applications or user needs. For example, 3D-printed wearable electronics can be designed to fit the exact contours of a person’s body, or sensors can be embedded directly into 3D-printed objects for Internet of Things (IoT) applications.
Complex Geometries and Unconventional Form Factors
Traditional PCB manufacturing is largely limited to 2D designs, with components mounted on flat substrates. 3D printing opens up new possibilities for creating electronics with complex 3D geometries and unconventional form factors. For example, antennas can be printed with optimized 3D shapes for better performance, or electronics can be integrated seamlessly into curved or irregular surfaces.
Potential Applications
3D-printed electronics have a wide range of potential applications across various industries:
Industry | Applications |
---|---|
Aerospace | Lightweight, conformal antennas and sensors |
Automotive | Customized dashboard electronics, embedded sensors |
Healthcare | Personalized wearable devices, biocompatible implants |
IoT | Rapid prototyping of sensors and connected devices |
Wearables | Customized, form-fitting smart clothing and accessories |
Robotics | Integrated sensors and circuits for soft robotics |
These are just a few examples of how 3D-printed electronics could be used to create innovative products and solutions.
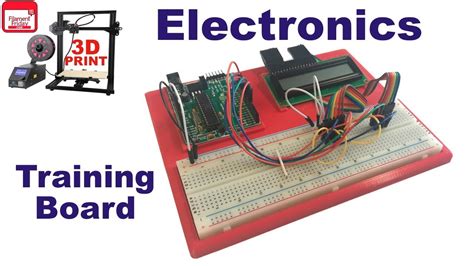
Challenges and Limitations
Despite the many promising applications of 3D-printed electronics, there are still several challenges and limitations that need to be addressed for this technology to reach its full potential.
Material Properties and Performance
One of the main challenges is developing conductive materials that have suitable electrical and mechanical properties for 3D printing. Conductive inks and pastes need to have low resistivity, good adhesion to substrates, and compatibility with various printing processes. They also need to be able to withstand the stresses and strains of 3D-printed structures without cracking or delaminating.
In addition, the performance of 3D-printed electronics is often lower than that of traditionally manufactured components. Printed conductors have higher resistivity than bulk metals, which can limit the current-carrying capacity and power efficiency of devices. Printed dielectrics may have lower breakdown voltages or higher losses compared to conventional materials.
Researchers are continually working on improving the properties of 3D-printable electronic materials, but there is still a gap in performance compared to traditional electronics.
Resolution and Feature Size
Another challenge is achieving high resolution and small feature sizes with 3D printing processes. While some methods like aerosol jet printing can produce features as small as 10 microns, most 3D printing techniques have lower resolution compared to photolithography used in PCB manufacturing. This limits the density and complexity of circuits that can be printed.
Advances in printing technology, such as using smaller nozzles or droplets, can help improve resolution. However, there is a trade-off between feature size and printing speed, as smaller features require more precise control and slower deposition rates.
Integration with Other Components
3D-printed electronics often need to be integrated with other components like microchips, sensors, batteries, and displays to create complete functional devices. This integration can be challenging due to differences in materials, processes, and form factors.
One approach is to use hybrid manufacturing techniques that combine 3D printing with traditional assembly methods. For example, a 3D-printed circuit board could have pockets or sockets where standard components are inserted and connected using conductive adhesives or solders. Another approach is to develop fully printable versions of active components, but this is still an area of active research.
Scalability and Cost
While 3D printing is well-suited for rapid prototyping and low-volume production, scaling up to mass manufacturing can be challenging. 3D printing is generally slower and more expensive than traditional high-volume manufacturing methods like injection molding or roll-to-roll processing.
To make 3D-printed electronics more viable for larger-scale production, improvements are needed in printing speed, material costs, and process automation. Some companies are developing scalable 3D printing platforms specifically for electronics, but the technology is still maturing.
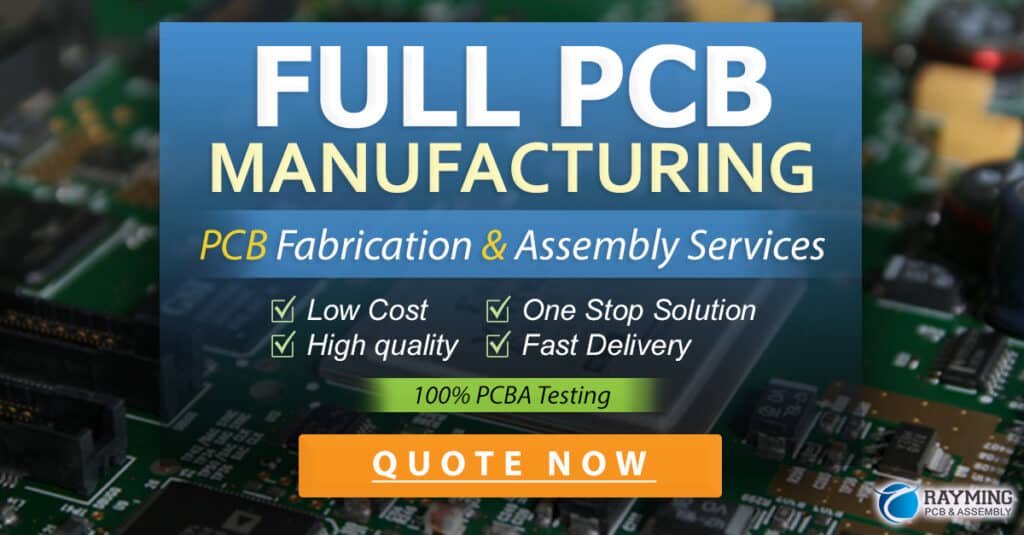
Future Outlook and Research Directions
Despite the challenges, the future outlook for 3D-printed electronics is promising. As printing technologies advance and new materials are developed, we can expect to see more sophisticated and higher-performing 3D-printed devices.
Some key areas of research and development include:
- Multimaterial printing: Combining multiple conductive, dielectric, and semiconducting materials in a single printing process to create more complex and functional devices.
- Embedded components: Developing methods to print active components like transistors, sensors, and displays directly into 3D-printed structures.
- Intelligent materials: Incorporating stimuli-responsive or self-healing properties into 3D-printed electronics for improved durability and adaptability.
- Sustainability: Exploring the use of biodegradable or recyclable materials for 3D-printed electronics to reduce electronic waste.
- Printing speed and scalability: Improving the throughput and efficiency of 3D printing processes for electronics to enable larger-scale manufacturing.
As 3D-printed electronics continue to evolve, we can expect to see more innovative applications and products that leverage the benefits of this technology.
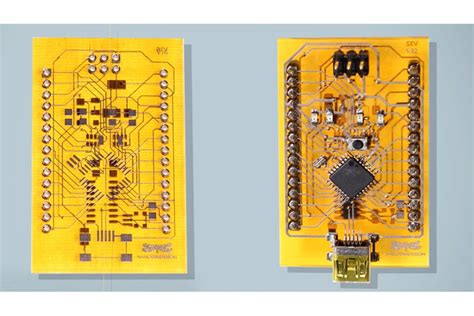
Frequently Asked Questions (FAQ)
1. What is the difference between 3D-printed electronics and traditional PCB manufacturing?
Traditional PCB manufacturing involves etching conductive traces on a flat substrate and soldering components onto the board. 3D-printed electronics, on the other hand, use additive manufacturing techniques to deposit conductive materials directly onto 3D structures, allowing for more complex geometries and integrated functionality.
2. Can 3D-printed electronics replace traditional PCBs?
While 3D-printed electronics offer unique advantages in terms of customization, rapid prototyping, and form factor flexibility, they are not yet a complete replacement for traditional PCBs in all applications. The performance, resolution, and scalability of 3D-printed electronics are still limited compared to conventional manufacturing methods. However, as the technology advances, 3D-printed electronics may become a viable alternative in more and more use cases.
3. What are the most common materials used in 3D-printed electronics?
The most common materials used in 3D-printed electronics are conductive inks and pastes, which typically contain metal particles (such as silver, copper, or gold) suspended in a polymer binder. These inks can be deposited using various printing methods and then sintered or cured to form conductive traces. Other materials used include conductive polymers, carbon-based materials (like graphene or carbon nanotubes), and even semiconducting materials for printed active components.
4. How long does it take to 3D print an electronic device?
The time it takes to 3D print an electronic device depends on several factors, including the size and complexity of the design, the printing technology used, and the materials involved. Simple circuits or antennas can be printed in a matter of minutes or hours, while more complex devices with multiple layers and components may take several hours or even days. However, compared to traditional PCB manufacturing and assembly processes, 3D printing can still provide significant time savings, especially for prototyping and low-volume production.
5. What are some of the most promising applications for 3D-printed electronics?
Some of the most promising applications for 3D-printed electronics include:
- Wearable devices: 3D printing allows for customized, form-fitting electronics that can be integrated into clothing or worn directly on the skin.
- IoT sensors: Rapid prototyping of sensors and connected devices for the Internet of Things, with the ability to embed electronics directly into 3D-printed structures.
- Aerospace and automotive: Lightweight, conformal antennas and sensors that can be integrated into complex shapes and surfaces.
- Healthcare: Personalized medical devices, such as prosthetics or implants, with embedded sensors and electronics.
- Robotics: Integrated sensors and circuits for soft robotics and other advanced robotic applications.
As the technology continues to develop, we can expect to see even more innovative applications emerge.
Conclusion
3D-printed electronics represent a promising and rapidly evolving field that has the potential to transform the way we design, prototype, and manufacture electronic devices. By enabling greater customization, faster iteration, and more complex geometries, 3D printing opens up new possibilities for creating innovative and high-performance electronics.
However, there are still significant challenges to overcome, including limitations in material properties, resolution, integration, and scalability. Researchers and companies are actively working to address these challenges through advances in materials science, printing technologies, and manufacturing processes.
As 3D-printed electronics continue to mature, we can expect to see more widespread adoption across various industries, from consumer electronics to healthcare to aerospace. With ongoing research and development, the future of 3D-printed electronics looks bright, and we can anticipate many exciting applications and innovations in the years to come.
Leave a Reply