What Goes Into Successful Electronic Product Design?
Designing a successful electronic product requires careful planning and execution across multiple disciplines. The key elements of the electronic product design process include:
- Defining product requirements
- System architecture and hardware design
- Firmware/software development
- Industrial design and mechanical engineering
- Prototyping and testing
- Manufacturing
Having a clear vision for your product and a solid plan to realize that vision through the design phases is critical to bringing a great electronic device to market. Let’s explore each of these areas in more detail.
Defining Product Requirements
Understand Your Target Market and Use Cases
Before starting to design any new electronic product, it’s essential to have a deep understanding of your target customers and the key use cases your product will address. Consider questions like:
- Who will be using this product?
- What problems does it solve for them?
- What environments and conditions will it be used in?
- What features and functionality are most important?
- How should it be priced?
Doing market research, analyzing competing products, and gathering input directly from potential users helps inform your product requirements. The requirements document you create will guide the entire development process.
Prioritize Features vs Cost and Time-to-Market
With your list of desired features and specifications in hand, you’ll need to make hard choices about what to include in your product. Every feature you add incurs a cost – in components, engineering time, manufacturing complexity, and ultimately the retail price.
Ruthlessly prioritize the features that deliver the most value to your target user while controlling cost and time-to-market. You may need to leave some desirable bells and whistles on the cutting room floor. Focus on nailing the core user experience first.
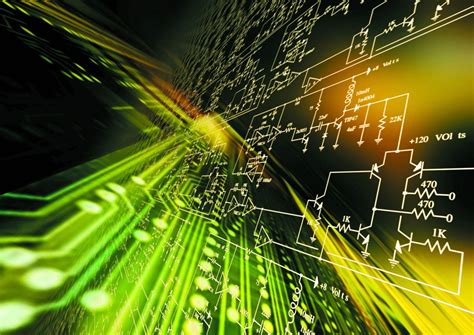
System Architecture and Hardware Design
Choosing Components and Designing Schematics
The electronic guts of your product – the PCB(s), processors, memory, sensors, power management, and other components – are critical to get right. Your system architecture lays out how all the electronic subsystems will work together to deliver the functionality you’ve defined.
Key considerations when designing your hardware architecture and choosing components include:
- Processing power and memory to meet software requirements
- Interfaces between components (serial, I2C, SPI, etc.)
- Wireless connectivity (Bluetooth, Wi-Fi, cellular, etc.)
- Power consumption, battery life, charging
- Component cost, availability and lead times
- Compliance and certification requirements (FCC, UL, etc.)
Component selection requires carefully balancing tradeoffs between performance, power, cost and complexity. Integrated SoC (system-on-chip) solutions like Raspberry Pi and Arduino modules can dramatically simplify system design for some applications.
PCB Layout and Design for Manufacturing
With components selected and schematics drawn, the physical PCB layout is the next critical step. Important PCB layout considerations include:
- Component placement for optimal routing and signal integrity
- Trace widths and spacings to handle required current
- Proper grounding and avoiding antenna effects
- Minimizing EMI and cross-talk
- Testability and access to debug interfaces
- Mechanical constraints and component clearances
- Design for manufacturing and assembly
PCBs should be designed thoughtfully to avoid potential manufacturing and reliability issues down the road. Whenever possible, design for automated assembly and test.
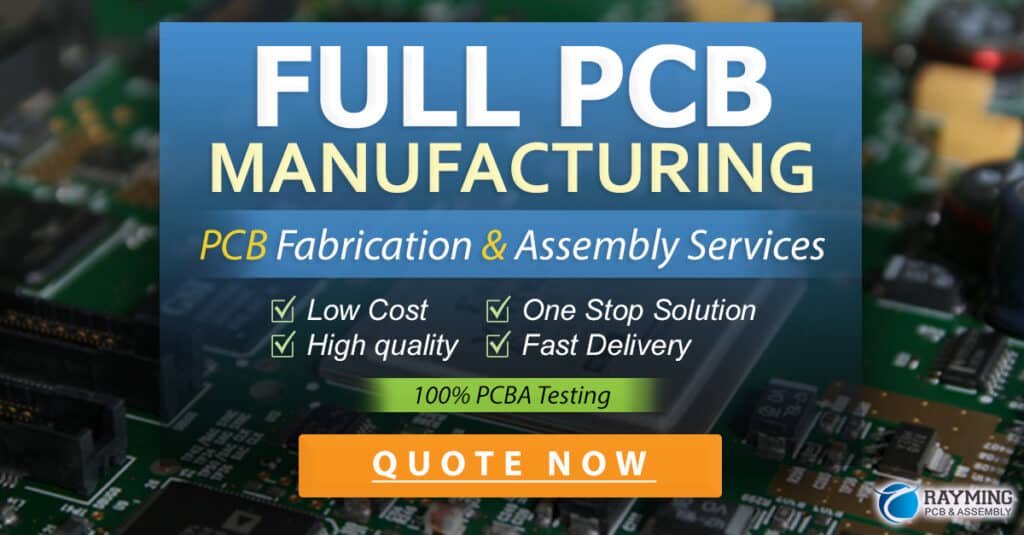
Firmware and Software Development
Firmware Development and Debugging
Firmware is the low-level software that directly controls your product’s hardware. It’s typically written in C or C++ and runs on a microcontroller. Key aspects of firmware development include:
- Bootloader and startup code
- Hardware abstraction layer and device drivers
- Peripheral and sensor interfaces
- Power management and sleep/wake handling
- Communication protocols and data storage
- Logging and debugging support
Firmware must be robust, efficient, and able to gracefully handle error conditions. Careful design of APIs between firmware and higher level software is also critical.
Application Software and User Interface Design
Most electronic products also require higher-level application software, often with a graphical user interface (GUI). This may run on an embedded processor or on a tethered device like a smartphone. Key considerations for application software include:
- Choice of OS (embedded Linux, Android, FreeRTOS, bare-metal, etc.)
- Programming language(s) and development environment
- Frameworks and libraries for GUI, databases, wireless, etc.
- Communication and data synchronization with firmware, cloud services, etc.
- Over-the-air updates and security
- Use of off-the-shelf vs. custom-developed software components
Thoughtful, user-centric UI design is critical to delivering a polished product experience. UI design should be an integral part of the product development process from the earliest stages.
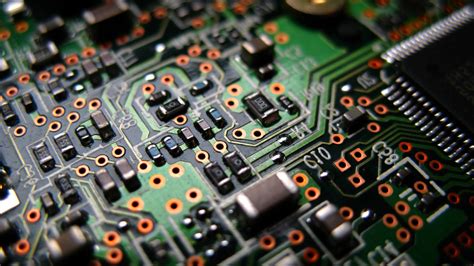
Industrial Design and Mechanical Engineering
Industrial Design and Form Factor
Your product’s industrial design brings together its branding, aesthetics, ergonomics, and user interactions into a cohesive whole. Key aspects of industrial design include:
- Overall form factor, look and feel
- Materials, colors and finishes
- Physical user interfaces (buttons, knobs, sliders, touchscreens)
- Ergonomics and usability
- Packaging and unboxing experience
The industrial design should communicate your brand values and product vision, differentiate your product from competitors, and make it a joy to use.
Mechanical Engineering and System Integration
Your mechanical engineering brings together the electronics, sensors, batteries, displays, and UI elements into a finished physical form that realizes the vision established by your industrial designers. Mechanical design considerations include:
- Placement of boards, buttons, connectors, antennas, etc.
- Component access for assembly and disassembly
- Structural elements and fastening
- Thermal management, heat sinks and airflow
- Environmental sealing against dust and moisture
- Strain relief for cables and moving parts
- DFM and tooling design for high volume production
3D CAD tools like Solidworks are essential for designing and validating the mechanical packaging and fit. Tight collaboration between mechanical and electrical engineers is a must.
Prototyping and Testing
Proof of Concept and MVP Development
Before investing in production tooling and large component buys, you’ll want to build and test prototypes to validate your design. Early “proof of concept” prototypes using development kits, evaluation modules or 3D printed mechanics are great for testing core functionality.
As the design matures, you’ll build minimum viable product (MVP) prototypes with custom electronics and mechanics that closely approximate the final design intent. These are used for more rigorous testing and may also be shared with early pilot customers for feedback.
Design Verification and Validation Testing
Your prototypes should undergo thorough design verification testing (DVT) for electronics, mechanics and software. Verification testing checks that your product meets its design specifications, including:
- Functional testing of all features
- Wireless range and performance
- Battery life and charging
- Environmental and durability (temperature, humidity, shock, vibration)
- EMC and RF emissions
- Safety and regulatory compliance
- Manufacturability and yield
You’ll likely go through multiple prototype build and test cycles to improve the design and resolve issues. Formal DVT is done on late-stage prototypes, preferably built using production processes and tooling.
Design validation testing focuses on the user experience and checks that your product is ready for real-world use. You might conduct:
- User testing with your target market
- Field testing in actual use environments
- Beta testing with friendly customers
- Packaging and shipping testing
- Instructions and customer support readiness
Only once you’ve passed DVT and validation should you ramp into production.
Manufacturing
Choosing a Contract Manufacturer
Taking your product into volume production requires lining up your supply chain and choosing the right manufacturing partner(s). Top considerations for selecting a contract manufacturer (CM) include:
- Technical capabilities and experience with your product type
- Quality systems and certifications (ISO9001, etc.)
- Geographic location and logistics
- Communication and responsiveness
- Cost and flexibility for your volumes
- Intellectual property protection
Visit the factory and ask for references before making your decision. Work closely with the CM’s engineers to optimize your design for their processes and equipment.
Production Testing and Quality Control
Catching problems in manufacturing requires a robust system of production testing and quality control. Common techniques include:
- Automated optical inspection (AOI) for PCB and assembly defects
- Flying probe and ICT for PCB electrical defects
- Functional circuit board testing
- Performance testing of wireless, sensors, UI, etc.
- Accelerated life and stress testing
- Visual cosmetic inspection
Work with your CM to define and implement the right combination of tests for your product and volume. Make sure to track metrics like first pass yield and defect rates.
Certifications and Regulatory Approvals
Most electronic products require various regulatory certifications before they can be legally sold, such as:
- FCC (EMC and wireless)
- UL or IEC (safety)
- Bluetooth SIG
- Cellular carrier certifications
- RoHS (environmental)
Engage with testing labs early to fully understand the requirements. Make sure to budget time and money to complete all necessary certifications.
FAQ
How much does it cost to develop a new electronic product?
Total development costs can range from tens of thousands to millions of dollars depending on the product complexity, volume, and level of innovation required. Typical costs include:
- Engineering time for hardware, software, mechanical design
- Prototypes and testing
- Certifications and regulatory fees
- Tooling for plastics, metals, and PCBs
- Minimum order quantities for components
How long does it take to go from concept to mass production?
Again this varies widely based on complexity, but 1-2 years is typical for commercial electronic products. Key factors are:
- Complexity of electronics and software
- Mechanical packaging challenges
- Certification requirements and lead times
- Supply chain and component lead times
- Maturity of underlying technology
Generally plan for multiple prototype iterations over several months before locking down a final production design.
Should I consider crowdfunding for my electronic product?
Crowdfunding platforms like Kickstarter can be a great way to validate market demand and raise funds for development. However, delivering a hardware product is very different than software:
- You’ll need to have a mature, working prototype before launching
- Forecast your funding goal based on detailed cost estimates for development and production
- Understand the cost and schedule risks of scaling production to meet backer demand
- Plan to continue supporting and selling your product after campaign
Many high-profile crowdfunded hardware products have struggled or failed to deliver, so proceed carefully. Treat crowdfunding as a stepping stone, not an end goal.
What’s the biggest mistake hardware startups make?
One of the most common pitfalls is underestimating the time and cost required to go from a great prototype to a reliable, top quality product at scale. A few specific traps to avoid:
- Don’t assume your development and material costs will match long term production pricing
- Budget adequate time for testing, certification and production ramp
- Staff your team with experienced hardware developers who’ve shipped before
- Raise enough capital to survive long component lead times and unforeseeable delays
- Resist pressure to overpromise features or delivery dates
Delivering a successful product requires thoughtful planning, hard work, and always a bit of luck. But the satisfaction of watching your creation come to life in the hands of happy customers is well worth the effort.
Leave a Reply