Introduction to PCB Design
Printed Circuit Board (PCB) design is a critical aspect of electronic product development. It involves the creation of a board that connects electronic components together to form a functional circuit. PCB design is a complex process that requires a deep understanding of electronic principles, materials, and manufacturing processes.
In this article, we will explore the fundamentals of PCB design, including the design process, tools, and considerations. We will also discuss the importance of PCB design in the electronics industry and its impact on product performance and reliability.
The PCB Design Process
The PCB design process typically involves several stages, including:
-
Schematic Design: The first step in PCB design is to create a schematic diagram of the circuit. This diagram shows the electronic components and their interconnections. The schematic is created using specialized software tools, such as OrCAD or Eagle.
-
Component Selection: Once the schematic is complete, the next step is to select the appropriate components for the circuit. This involves choosing components based on their electrical characteristics, size, and cost.
-
PCB Layout: After the components are selected, the PCB layout is created. This involves arranging the components on the board and routing the traces between them. The layout is created using specialized software tools, such as Altium Designer or KiCad.
-
Design Rule Check (DRC): Once the layout is complete, a Design Rule Check (DRC) is performed to ensure that the layout meets the manufacturing constraints and design rules. This includes checking for minimum trace widths, spacing between components, and other factors.
-
Gerber File Generation: After the DRC is passed, the PCB design is exported as a set of Gerber files. These files contain the information needed to manufacture the PCB, including the copper layers, solder mask, and silkscreen.
-
Prototyping and Testing: Once the Gerber files are generated, a prototype of the PCB is manufactured and tested to ensure that it functions as intended. Any issues identified during testing are addressed before the final production run.
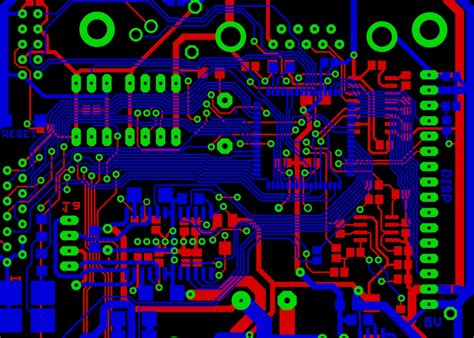
PCB Design Tools
There are several specialized software tools used in PCB design, including:
-
Schematic Capture Tools: These tools are used to create the schematic diagram of the circuit. Examples include OrCAD, Eagle, and KiCad.
-
PCB Layout Tools: These tools are used to create the PCB layout, including component placement and trace routing. Examples include Altium Designer, Cadence Allegro, and Mentor Graphics PADS.
-
Simulation Tools: These tools are used to simulate the behavior of the circuit and identify potential issues before the PCB is manufactured. Examples include LTSpice, PSpice, and Multisim.
-
3D Modeling Tools: These tools are used to create 3D models of the PCB and its components, which can be used for visualization and mechanical design. Examples include SolidWorks, Autodesk Fusion 360, and Creo.
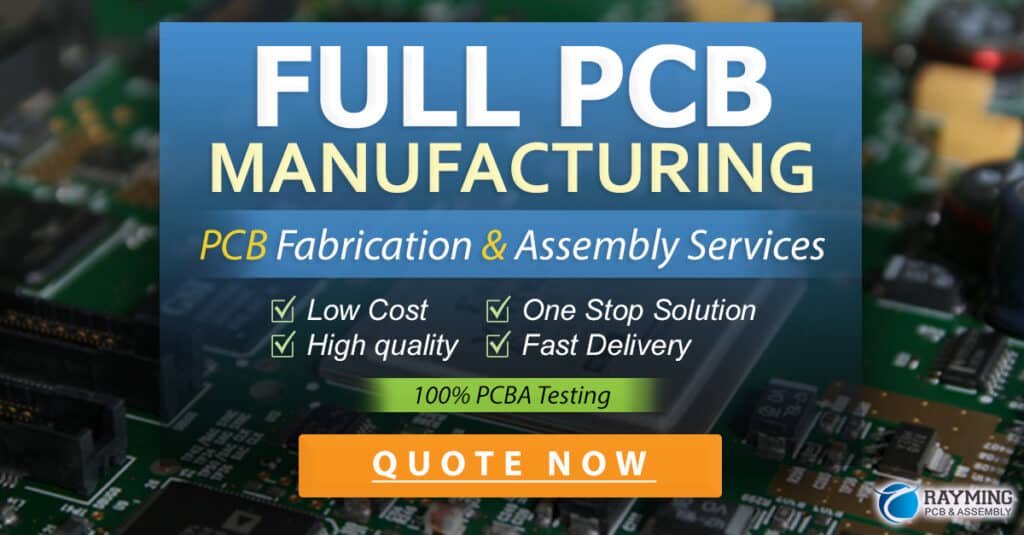
PCB Design Considerations
There are several important considerations in PCB design, including:
-
Signal Integrity: Signal integrity refers to the quality of the electrical signals transmitted through the PCB. Factors that can affect signal integrity include trace length, impedance, and crosstalk.
-
Electromagnetic Compatibility (EMC): EMC refers to the ability of the PCB to operate without causing or being affected by electromagnetic interference (EMI). Factors that can affect EMC include component placement, shielding, and grounding.
-
Thermal Management: Thermal management refers to the ability of the PCB to dissipate heat generated by the components. Factors that can affect thermal management include component placement, copper thickness, and the use of thermal vias.
-
Manufacturing Constraints: PCB design must also consider manufacturing constraints, such as minimum trace widths, spacing between components, and the number of layers in the board.
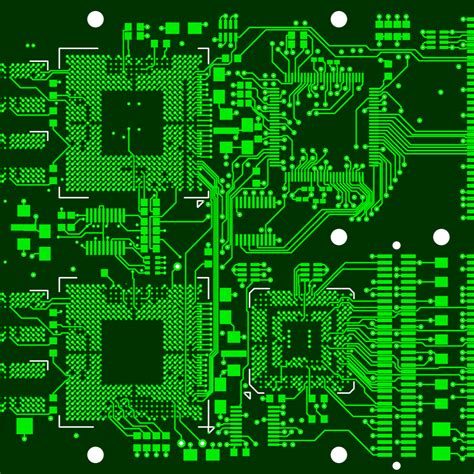
The Importance of PCB Design
PCB design is a critical aspect of electronic product development, and it has a significant impact on product performance and reliability. A well-designed PCB can:
-
Improve Signal Integrity: A well-designed PCB can minimize signal distortion and ensure that signals are transmitted accurately and reliably.
-
Reduce Electromagnetic Interference (EMI): A well-designed PCB can minimize EMI and ensure that the product meets regulatory requirements for electromagnetic compatibility.
-
Improve Thermal Management: A well-designed PCB can effectively dissipate heat generated by the components, which can improve product reliability and longevity.
-
Reduce Manufacturing Costs: A well-designed PCB can minimize manufacturing costs by reducing the number of layers, minimizing the use of expensive materials, and simplifying the assembly process.
PCB Design Best Practices
To ensure a successful PCB design, there are several best practices that should be followed, including:
-
Use a Modular Design Approach: A modular design approach involves breaking the circuit into smaller, self-contained modules that can be designed and tested independently. This approach can simplify the design process and improve reliability.
-
Use a Hierarchical Design Approach: A hierarchical design approach involves organizing the circuit into a hierarchy of subsystems and components. This approach can make the design more manageable and easier to understand.
-
Use Simulation Tools: Simulation tools can be used to identify potential issues with the circuit before the PCB is manufactured. This can save time and reduce the risk of costly redesigns.
-
Follow Design Rules: PCB design rules are established to ensure that the PCB can be manufactured reliably and cost-effectively. It is important to follow these rules to avoid manufacturing issues and delays.
-
Document the Design: Proper documentation of the PCB design is essential for future reference and troubleshooting. This includes the schematic diagram, PCB layout, and bill of materials (BOM).
PCB Manufacturing Process
Once the PCB design is complete, the next step is to manufacture the board. The PCB manufacturing process typically involves the following steps:
-
PCB Fabrication: The PCB is fabricated using a process called photolithography. This involves applying a photoresist material to the copper-clad board, exposing it to UV light through a photomask, and then etching away the unwanted copper.
-
Drilling: Holes are drilled in the PCB to allow for the insertion of components and vias.
-
Plating: The holes are plated with a conductive material, such as copper, to ensure electrical continuity.
-
Solder Mask Application: A solder mask is applied to the PCB to protect the copper traces and prevent short circuits.
-
Silkscreen Printing: A silkscreen is printed on the PCB to label components and provide assembly instructions.
-
Surface Finishing: A surface finish, such as HASL (Hot Air Solder Leveling) or ENIG (Electroless Nickel Immersion Gold), is applied to the PCB to protect the copper and improve solderability.
-
Electrical Testing: The PCB is tested to ensure that it functions as intended and meets the required specifications.
Common PCB Design Challenges
PCB design can be a challenging process, and there are several common issues that can arise, including:
-
Signal Integrity Issues: Signal integrity issues can occur when the PCB layout is not optimized for the specific application. This can result in signal distortion, crosstalk, and other issues that can affect the performance of the circuit.
-
EMC Issues: EMC issues can occur when the PCB is not designed to minimize EMI. This can result in interference with other electronic devices and can cause the product to fail regulatory compliance tests.
-
Thermal Management Issues: Thermal management issues can occur when the PCB is not designed to effectively dissipate heat generated by the components. This can result in overheating, which can reduce the reliability and longevity of the product.
-
Manufacturing Issues: Manufacturing issues can occur when the PCB design does not follow the established design rules or when the design is too complex to be manufactured reliably and cost-effectively.
PCB Design Case Studies
To illustrate the importance of PCB design, let’s look at a few case studies:
Case Study 1: Automotive ECU Design
An automotive electronics manufacturer was experiencing reliability issues with its Engine Control Unit (ECU). The ECU was failing prematurely due to overheating, which was causing significant warranty claims and customer dissatisfaction.
The manufacturer hired a PCB design consultant to analyze the ECU design and identify the root cause of the overheating issue. The consultant found that the PCB layout was not optimized for thermal management, and the components were not placed in a way that allowed for effective heat dissipation.
The consultant redesigned the PCB layout to improve thermal management, including the use of thermal vias and the placement of components in a way that allowed for better airflow. The redesigned ECU was tested and found to have significantly improved thermal performance, which reduced the number of warranty claims and improved customer satisfaction.
Case Study 2: Medical Device Design
A medical device manufacturer was developing a new diagnostic instrument that required a complex PCB design with high-speed digital signals and sensitive analog circuits. The manufacturer was concerned about signal integrity and EMC issues that could affect the accuracy and reliability of the instrument.
The manufacturer hired a PCB design consultant with experience in medical device design to assist with the project. The consultant worked closely with the manufacturer’s engineering team to develop a PCB layout that was optimized for signal integrity and EMC.
The consultant used simulation tools to analyze the circuit and identify potential issues before the PCB was manufactured. The consultant also recommended the use of shielding and grounding techniques to minimize EMI and ensure that the instrument met regulatory requirements.
The instrument was successfully launched and received positive feedback from customers for its accuracy and reliability.
FAQ
-
What is PCB design?
PCB design is the process of creating a printed circuit board that connects electronic components to form a functional circuit. -
What are the main steps in the PCB design process?
The main steps in the PCB design process include schematic design, component selection, PCB layout, design rule check, Gerber file generation, and prototyping and testing. -
What are some common PCB design challenges?
Common PCB design challenges include signal integrity issues, EMC issues, thermal management issues, and manufacturing issues. -
What are some best practices for PCB design?
Some best practices for PCB design include using a modular design approach, using a hierarchical design approach, using simulation tools, following design rules, and documenting the design. -
What is the importance of PCB design in the electronics industry?
PCB design is critical in the electronics industry because it directly affects the performance, reliability, and cost of electronic products. A well-designed PCB can improve signal integrity, reduce EMI, improve thermal management, and reduce manufacturing costs.
Conclusion
PCB design is a complex process that requires a deep understanding of electronic principles, materials, and manufacturing processes. It is a critical aspect of electronic product development that directly affects the performance, reliability, and cost of the final product.
To ensure a successful PCB design, it is important to follow best practices, such as using a modular and hierarchical design approach, using simulation tools, following design rules, and documenting the design. It is also important to consider factors such as signal integrity, EMC, thermal management, and manufacturing constraints.
By investing in PCB design and working with experienced PCB design consultants, electronics manufacturers can develop products that are more reliable, efficient, and cost-effective. This can lead to increased customer satisfaction, reduced warranty claims, and improved profitability.
Step | Description |
---|---|
Schematic Design | Create a schematic diagram of the circuit using specialized software tools |
Component Selection | Select appropriate components based on electrical characteristics, size, and cost |
PCB Layout | Arrange components on the board and route traces between them using specialized software tools |
Design Rule Check (DRC) | Ensure that the layout meets manufacturing constraints and design rules |
Gerber File Generation | Export the PCB design as a set of Gerber files for manufacturing |
Prototyping and Testing | Manufacture a prototype of the PCB and test it to ensure proper functionality |
Table 1: Main steps in the PCB design process
Consideration | Description |
---|---|
Signal Integrity | Ensure that electrical signals are transmitted accurately and reliably |
Electromagnetic Compatibility (EMC) | Minimize electromagnetic interference (EMI) and ensure compliance with regulations |
Thermal Management | Effectively dissipate heat generated by components to improve reliability and longevity |
Manufacturing Constraints | Consider minimum trace widths, component spacing, and the number of layers in the board |
Table 2: Important considerations in PCB design
In summary, PCB design is a vital aspect of electronic product development that requires careful planning, attention to detail, and a commitment to best practices. By prioritizing PCB design, electronics manufacturers can create products that are more reliable, efficient, and cost-effective, ultimately leading to greater success in the marketplace.
Leave a Reply