Introduction to PCB
Printed Circuit Boards (PCBs) are essential components in modern electronics. They are the foundation upon which electronic devices are built, providing a platform for mounting and connecting electronic components. PCBs have revolutionized the electronics industry by enabling the creation of compact, reliable, and cost-effective electronic devices. In this article, we will explore the Main purpose of PCBs and their significance in the world of electronics.
The Role of PCBs in Electronic Devices
PCBs play a crucial role in the functioning of electronic devices. They serve as the backbone of these devices, providing a means for interconnecting various electronic components such as resistors, capacitors, integrated circuits, and sensors. The main purposes of PCBs include:
-
Component Mounting: PCBs provide a stable and secure platform for mounting electronic components. The components are soldered onto the PCB, ensuring a reliable electrical connection and mechanical stability.
-
Electrical Connectivity: PCBs facilitate the electrical connectivity between different components. The conductive traces etched on the PCB allow for the flow of electrical signals and power between the components, enabling the device to function as intended.
-
Circuit Design: PCBs are designed to implement specific circuit designs. The layout of the components and the routing of the conductive traces on the PCB are carefully planned to achieve the desired functionality and performance of the electronic device.
-
Miniaturization: PCBs enable the miniaturization of electronic devices. By allowing components to be densely packed and interconnected on a small board, PCBs contribute to the development of compact and portable electronic devices.
-
Cost Reduction: PCBs help in reducing the overall cost of electronic devices. Mass production of PCBs is cost-effective, and the use of automated assembly processes further reduces manufacturing costs.
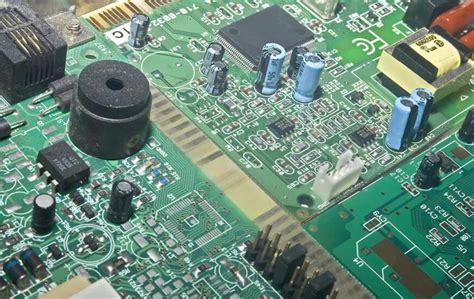
Types of PCBs
PCBs come in different types, each serving specific purposes and catering to different design requirements. The main types of PCBs include:
-
Single-Sided PCBs: These PCBs have conductive traces on only one side of the board. They are the simplest and most economical type of PCB, suitable for basic electronic circuits.
-
Double-Sided PCBs: Double-sided PCBs have conductive traces on both sides of the board. They offer higher component density and more complex routing capabilities compared to single-sided PCBs.
-
Multi-Layer PCBs: Multi-layer PCBs consist of multiple layers of conductive traces sandwiched between insulating layers. They are used in complex electronic devices that require high component density and intricate routing.
-
Flexible PCBs: Flexible PCBs are made from flexible materials, allowing them to bend and conform to different shapes. They are used in applications where flexibility and space constraints are critical, such as wearable electronics and medical devices.
-
Rigid-Flex PCBs: Rigid-flex PCBs combine the benefits of both rigid and flexible PCBs. They consist of rigid PCB sections connected by flexible PCB sections, providing a balance between stability and flexibility.
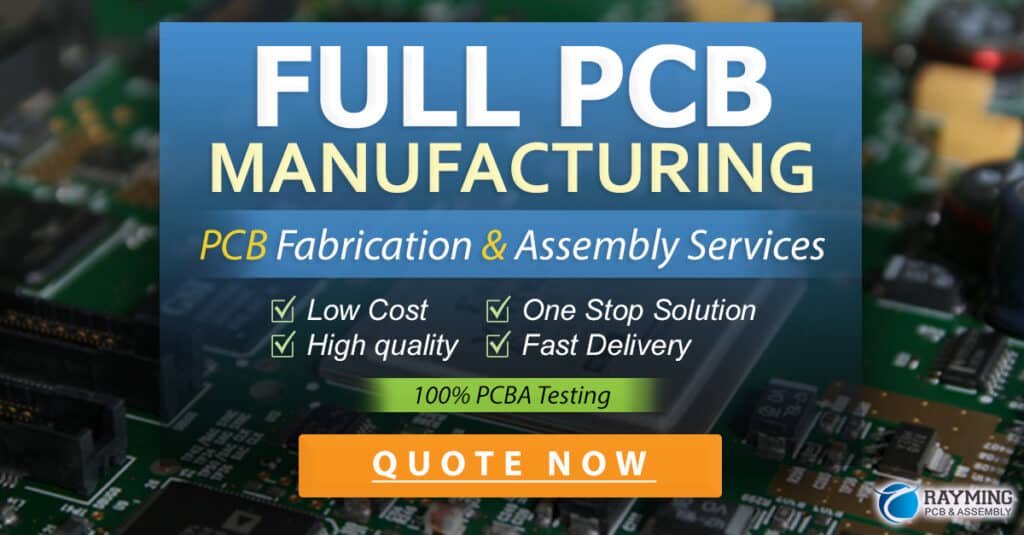
PCB Manufacturing Process
The manufacturing process of PCBs involves several steps to transform the circuit design into a physical board. The main stages of PCB manufacturing include:
-
Design: The PCB design is created using specialized software tools. The schematic diagram and layout of the components and traces are defined in this stage.
-
Fabrication: The PCB fabrication process begins with the creation of a copper-clad laminate board. The copper layer is etched away to form the desired conductive traces based on the PCB design.
-
Drilling: Holes are drilled into the PCB to accommodate through-hole components and provide interconnections between layers in multi-layer PCBs.
-
Plating: The drilled holes are plated with a conductive material, typically copper, to establish electrical connectivity between layers.
-
Solder Mask Application: A solder mask layer is applied to the PCB to protect the copper traces from oxidation and prevent short circuits during soldering.
-
Silkscreen Printing: The silkscreen layer is printed on the PCB to provide text, symbols, and component identifiers for easier assembly and troubleshooting.
-
Surface Finish: A surface finish, such as HASL (Hot Air Solder Leveling) or ENIG (Electroless Nickel Immersion Gold), is applied to the exposed copper areas to enhance solderability and protect against corrosion.
-
Assembly: The electronic components are placed and soldered onto the PCB using automated assembly machines or manual soldering techniques.
-
Testing: The assembled PCB undergoes various testing procedures to ensure functionality, reliability, and compliance with design specifications.
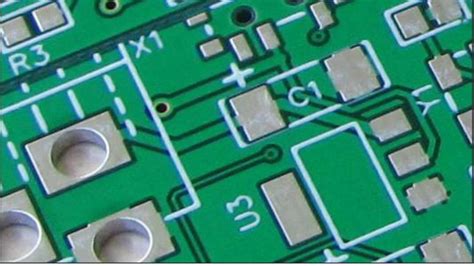
Advantages of Using PCBs
The use of PCBs offers several advantages in the design and manufacturing of electronic devices:
-
Miniaturization: PCBs enable the miniaturization of electronic devices by allowing components to be densely packed on a small board. This reduces the overall size and weight of the device.
-
Reliability: PCBs provide a reliable means of interconnecting electronic components. The robust mechanical structure and soldered connections ensure stable and secure electrical connections.
-
Consistency: PCBs enable consistent and repeatable manufacturing processes. Automated assembly techniques and standardized PCB designs ensure uniformity and reliability across multiple devices.
-
Cost-Effectiveness: PCBs are cost-effective for mass production. The automated manufacturing processes and the ability to produce large quantities of identical PCBs reduce the overall production costs.
-
Design Flexibility: PCBs offer design flexibility by allowing for customization and modifications based on specific requirements. Different layers, materials, and component placements can be used to optimize the performance and functionality of the device.
-
Improved Signal Integrity: PCBs provide controlled impedance and reduced electromagnetic interference (EMI), enhancing signal integrity and reducing signal distortion.
-
Thermal Management: PCBs can be designed with thermal management techniques, such as heat sinks and thermal vias, to dissipate heat efficiently and ensure the reliable operation of components.
Applications of PCBs
PCBs find applications in a wide range of industries and electronic devices. Some common applications include:
-
Consumer Electronics: PCBs are extensively used in consumer electronics such as smartphones, laptops, televisions, and home appliances.
-
Automotive Electronics: PCBs are employed in various automotive electronic systems, including engine control units, infotainment systems, and advanced driver assistance systems (ADAS).
-
Industrial Electronics: PCBs are used in industrial control systems, automation equipment, and monitoring devices.
-
Medical Devices: PCBs are critical components in medical devices such as patient monitoring systems, diagnostic equipment, and implantable devices.
-
Aerospace and Defense: PCBs are used in avionics systems, radar equipment, and military communication devices, where reliability and performance are paramount.
-
IoT Devices: PCBs are essential for the development of Internet of Things (IoT) devices, enabling the integration of sensors, wireless connectivity, and processing capabilities.
-
Wearable Technology: PCBs, particularly flexible PCBs, are used in wearable devices such as smartwatches, fitness trackers, and medical monitoring devices.
Future Trends in PCB Technology
The PCB industry is constantly evolving to meet the demands of advancing technology and emerging applications. Some of the future trends in PCB technology include:
-
High-Density Interconnect (HDI) PCBs: HDI PCBs offer higher component density and finer trace widths, enabling further miniaturization and improved performance.
-
Embedded Components: The integration of passive components, such as resistors and capacitors, directly into the PCB substrate is gaining traction. Embedded components save space and improve signal integrity.
-
3D Printing of PCBs: 3D printing technology is being explored for the fabrication of PCBs, offering the potential for rapid prototyping and customization.
-
Advanced Materials: The use of advanced materials, such as high-frequency laminates and thermal management materials, is becoming more prevalent to meet the demands of high-speed and high-power applications.
-
Eco-Friendly PCBs: There is a growing focus on developing eco-friendly PCB materials and manufacturing processes to reduce environmental impact and comply with regulations.
Frequently Asked Questions (FAQ)
-
What is the difference between a PCB and a breadboard?
A PCB is a printed circuit board that has conductive traces and pads for soldering components, while a breadboard is a prototyping tool that allows for temporary connections without soldering. -
Can PCBs be repaired if they are damaged?
Yes, PCBs can be repaired depending on the extent of the damage. Minor issues like broken traces or lifted pads can be repaired using techniques such as jumper wires or conductive epoxy. However, severe damage may require replacing the entire PCB. -
What is the typical lifespan of a PCB?
The lifespan of a PCB depends on various factors, including the quality of materials used, the manufacturing process, and the operating environment. Generally, a well-designed and manufactured PCB can last for several years or even decades, depending on the application. -
How do I choose the right PCB manufacturer?
When choosing a PCB manufacturer, consider factors such as their experience, capabilities, quality control processes, certifications, and customer support. Look for manufacturers with a proven track record and positive customer reviews. -
Can I design my own PCB?
Yes, you can design your own PCB using specialized PCB design software. There are various software tools available, ranging from free open-source options to professional-grade commercial software. However, designing a PCB requires knowledge of electronics, PCB layout principles, and design guidelines.
Conclusion
PCBs are the unsung heroes of the electronics world, serving as the foundation for countless devices that we rely on every day. The main purpose of PCBs is to provide a reliable and efficient means of interconnecting electronic components, enabling the creation of compact, high-performance, and cost-effective electronic devices.
From consumer electronics to industrial automation, medical devices to aerospace systems, PCBs find applications in virtually every sector. The PCB industry continues to evolve, embracing new technologies and materials to meet the ever-increasing demands for miniaturization, functionality, and reliability.
Understanding the purpose, types, manufacturing process, and advantages of PCBs is essential for anyone involved in electronics design, manufacturing, or troubleshooting. By leveraging the capabilities of PCBs, we can continue to push the boundaries of electronic innovation and create devices that enhance our lives in countless ways.
PCB Type | Characteristics |
---|---|
Single-Sided PCB | – Conductive traces on one side of the board – Simple and economical – Suitable for basic electronic circuits |
Double-Sided PCB | – Conductive traces on both sides of the board – Higher component density and more complex routing – Widely used in various applications |
Multi-Layer PCB | – Multiple layers of conductive traces sandwiched between insulating layers – High component density and intricate routing – Used in complex electronic devices |
Flexible PCB | – Made from flexible materials – Can bend and conform to different shapes – Used in wearable electronics and medical devices |
Rigid-Flex PCB | – Combines rigid and flexible PCB sections – Provides stability and flexibility – Used in applications with space constraints and unique packaging requirements |
Table 1: Types of PCBs and their characteristics
As we continue to push the boundaries of technology, PCBs will undoubtedly remain at the heart of electronic innovation. By understanding the purpose and capabilities of PCBs, we can harness their potential to create groundbreaking devices that shape our future.
Leave a Reply