PCB Applications in Consumer Electronics
Consumer electronics are perhaps the most common application of PCBs. Almost every electronic device we use in our daily lives, such as smartphones, laptops, televisions, and home appliances, contains one or more PCBs. These boards are responsible for the proper functioning and performance of these devices.
Smartphones and Tablets
Smartphones and tablets rely heavily on PCBs to integrate various components, such as processors, memory, sensors, and communication modules, into a compact and lightweight design. The complex circuitry required for these devices is made possible by the use of multilayer PCBs, which allow for high component density and efficient signal routing.
Laptops and Computers
PCBs are the backbone of laptops and computers, housing the central processing unit (CPU), memory modules, graphics cards, and other essential components. The motherboard, which is the main PCB in a computer, connects all these components and enables communication between them. Additionally, PCBs are used in peripherals such as keyboards, mice, and external storage devices.
Home Appliances
Modern home appliances, such as refrigerators, washing machines, and microwave ovens, also rely on PCBs for their functionality. These boards control the various functions of the appliances, such as temperature regulation, motor control, and user interface. The use of PCBs in home appliances has enabled the integration of advanced features, such as smart connectivity and energy efficiency.
PCB Applications in Industrial Electronics
PCBs play a crucial role in industrial electronics, enabling the automation and control of various processes. Industrial PCBs are designed to withstand harsh environments, such as extreme temperatures, vibrations, and exposure to chemicals, ensuring reliable operation in demanding conditions.
Industrial Automation
PCBs are extensively used in industrial automation systems, such as programmable logic controllers (PLCs), human-machine interfaces (HMIs), and sensors. These boards enable the control and monitoring of industrial processes, improving efficiency, productivity, and safety. Industrial PCBs often feature ruggedized designs and robust connectors to ensure reliable operation in challenging environments.
Power Electronics
Power electronics, such as motor drives, power supplies, and inverters, rely on PCBs to control and regulate the flow of electrical power. These boards must be designed to handle high currents and voltages, as well as dissipate heat efficiently. PCBs used in power electronics often incorporate heavy copper layers and thermal management techniques to ensure optimal performance and longevity.
Aerospace and Defense
PCBs used in aerospace and defense applications must meet stringent requirements for reliability, durability, and performance. These boards are subjected to extreme environmental conditions, such as high altitudes, radiation exposure, and intense vibrations. Aerospace and defense PCBs often feature specialized materials, such as polyimide substrates and conformal coatings, to ensure their integrity in these demanding applications.
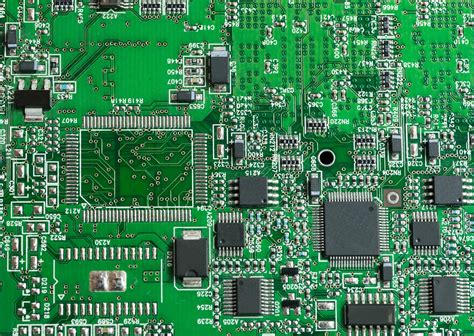
PCB Applications in Medical Equipment
Medical equipment relies on PCBs to enable accurate diagnosis, monitoring, and treatment of patients. PCBs used in medical applications must adhere to strict quality and safety standards to ensure patient safety and device reliability.
Diagnostic Imaging Equipment
PCBs are used in various diagnostic imaging equipment, such as X-ray machines, MRI scanners, and ultrasound devices. These boards control the acquisition, processing, and display of medical images, enabling healthcare professionals to make accurate diagnoses and treatment decisions.
Patient Monitoring Systems
Patient monitoring systems, such as electrocardiograms (ECGs), pulse oximeters, and blood pressure monitors, use PCBs to acquire and process vital signs data. These boards must be designed to ensure high signal integrity and low noise, as even small errors can have significant consequences in medical applications.
Implantable Medical Devices
Implantable medical devices, such as pacemakers, defibrillators, and drug delivery systems, rely on miniaturized PCBs to perform their life-sustaining functions. These boards must be designed to operate reliably for extended periods, often under harsh conditions within the human body. Implantable PCBs require specialized materials and coatings to ensure biocompatibility and protect against corrosion.
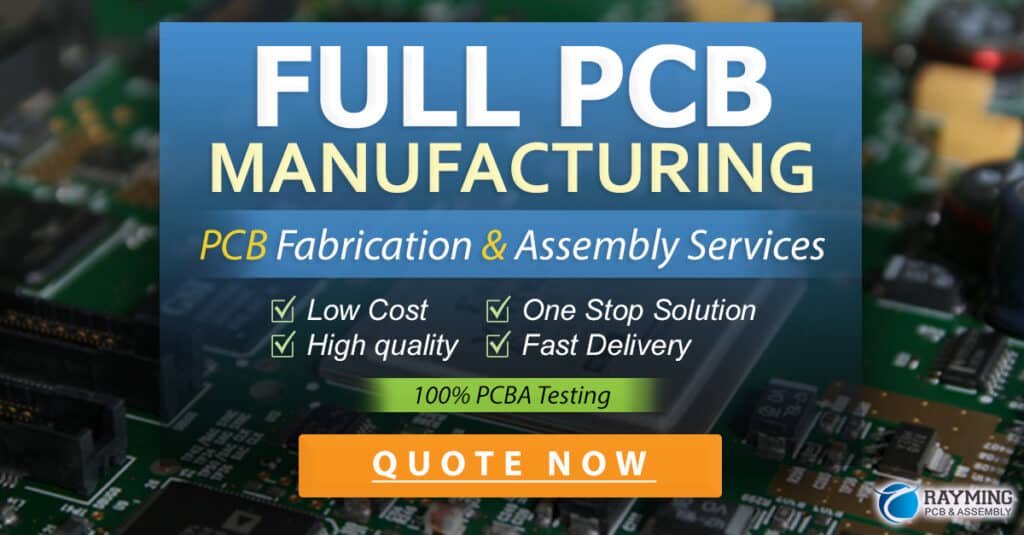
PCB Applications in Automotive Electronics
The automotive industry has seen a significant increase in the use of PCBs, driven by the growing demand for advanced safety features, infotainment systems, and electric vehicles. Automotive PCBs must be designed to withstand the harsh environment of a vehicle, including temperature extremes, vibrations, and exposure to moisture and chemicals.
Engine Control Units (ECUs)
ECUs are responsible for controlling various aspects of a vehicle’s engine, such as fuel injection, ignition timing, and emission control. These units rely on PCBs to process sensor data and execute control algorithms, ensuring optimal engine performance and fuel efficiency. Automotive PCBs used in ECUs must be designed to handle high temperatures and vibrations, as they are often located in close proximity to the engine.
Advanced Driver Assistance Systems (ADAS)
ADAS, such as lane departure warning, adaptive cruise control, and automatic emergency braking, rely on PCBs to process data from various sensors, including cameras, radar, and lidar. These boards must be capable of real-time processing and decision-making to ensure the safety of the vehicle and its occupants.
Infotainment Systems
Modern vehicles feature sophisticated infotainment systems that provide navigation, entertainment, and connectivity features. PCBs used in these systems must support high-speed data communication, graphics processing, and audio/video playback. Automotive infotainment PCBs often incorporate advanced features, such as touch screens and wireless connectivity.
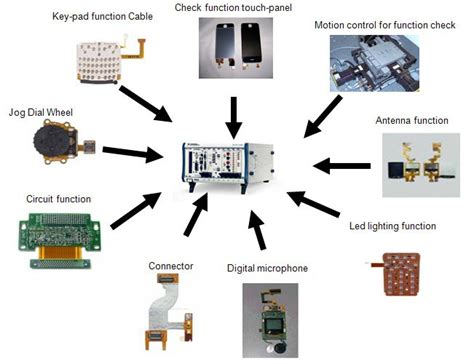
PCB Applications in Telecommunications
PCBs are essential components in telecommunication systems, enabling the transmission and reception of voice, data, and video signals. Telecommunication PCBs must be designed to handle high frequencies, ensure signal integrity, and provide reliable performance.
Base Stations
Base stations, which are responsible for transmitting and receiving wireless signals, rely on PCBs to process and route communication data. These boards must be capable of handling high-power signals and provide efficient heat dissipation to ensure reliable operation. PCBs used in base stations often feature multilayer designs and advanced materials to minimize signal loss and interference.
Networking Equipment
Networking equipment, such as routers, switches, and modems, use PCBs to process and route data packets between devices. These boards must support high-speed data communication and provide reliable performance to ensure the smooth operation of communication networks. Networking PCBs often incorporate advanced features, such as quality of service (QoS) and security protocols, to optimize network performance and protect against cyber threats.
Satellite Communication
PCBs used in satellite communication systems must be designed to withstand the harsh environment of space, including extreme temperatures, radiation exposure, and vacuum conditions. These boards must also be highly reliable, as repairs or replacements in space are often impractical or impossible. Satellite communication PCBs often feature specialized materials and redundant designs to ensure their long-term performance and reliability.
PCB Applications in Renewable Energy
The growing demand for clean and sustainable energy sources has led to an increased use of PCBs in renewable energy systems, such as solar panels and wind turbines. PCBs used in these applications must be designed to handle high voltages and currents, as well as withstand harsh environmental conditions.
Solar Power Systems
PCBs are used in various components of solar power systems, such as inverters, charge controllers, and monitoring devices. These boards are responsible for converting the DC power generated by solar panels into AC power suitable for grid integration or local consumption. Solar power PCBs must be designed to handle high voltages and provide efficient power conversion to maximize energy output.
Wind Turbine Control Systems
Wind turbines rely on PCBs to control and monitor various aspects of their operation, such as blade pitch, generator speed, and yaw orientation. These boards must be capable of real-time processing and decision-making to ensure optimal energy production and protect the turbine from damage in extreme wind conditions. PCBs used in wind turbine control systems must be designed to withstand the vibrations and temperature fluctuations experienced in the nacelle of the turbine.
Energy Storage Systems
PCBs are also used in energy storage systems, such as battery management systems (BMS) and grid-tied storage solutions. These boards are responsible for monitoring and controlling the charging and discharging of batteries, ensuring their safe and efficient operation. Energy storage PCBs must be designed to handle high currents and provide accurate monitoring to maximize the lifespan and performance of the storage system.
Frequently Asked Questions (FAQ)
- Q: What are the benefits of using PCBs in electronic devices?
A: PCBs offer several benefits, including: - Compact and efficient design, enabling the creation of smaller and more powerful devices
- Improved reliability and durability, as components are securely mounted and interconnected
- Reduced wiring complexity, making devices easier to assemble and maintain
-
Lower manufacturing costs, especially for high-volume production
-
Q: What materials are PCBs typically made from?
A: PCBs are typically made from a combination of materials, including: - Substrate: Usually a fiberglass-reinforced epoxy, such as FR-4, which provides mechanical support and electrical insulation
- Copper: Used for the conductive traces and pads, enabling electrical connections between components
- Solder mask: A protective layer that covers the copper traces, preventing short circuits and providing insulation
-
Silkscreen: A printed layer that adds labels, logos, and other identifying information to the PCB
-
Q: What are the different types of PCBs?
A: There are several types of PCBs, each suited for different applications: - Single-layer PCBs: Having conductive traces on only one side of the substrate, these are the simplest and most cost-effective option
- Double-layer PCBs: With conductive traces on both sides of the substrate, these offer more design flexibility and higher component density than single-layer PCBs
- Multilayer PCBs: Consisting of three or more layers of conductive traces, these are used for complex designs that require high component density and signal integrity
- Flexible PCBs: Made from flexible materials, such as polyimide, these can be bent or folded to fit into tight spaces or conform to unique shapes
-
Rigid-flex PCBs: Combining rigid and flexible sections, these offer the benefits of both types of PCBs, enabling unique and compact designs
-
Q: How are PCBs designed and manufactured?
A: The PCB design and manufacturing process typically involves the following steps: - Schematic design: Creating a diagram that represents the electrical connections between components
- PCB layout: Translating the schematic into a physical layout, determining the placement of components and routing of traces
- Fabrication: Manufacturing the PCB using processes such as etching, drilling, and plating
- Component assembly: Soldering or mounting components onto the PCB using techniques like surface-mount technology (SMT) or through-hole mounting
-
Testing and inspection: Verifying the functionality and quality of the assembled PCB, ensuring it meets the required specifications
-
Q: What are the challenges in PCB design for high-frequency applications?
A: Designing PCBs for high-frequency applications, such as wireless communication and radar systems, presents several challenges: - Signal integrity: Ensuring the quality and fidelity of high-frequency signals as they propagate through the PCB, minimizing losses and distortion
- Electromagnetic compatibility (EMC): Preventing interference between different signals and circuits on the PCB, as well as mitigating the impact of external electromagnetic interference (EMI)
- Thermal management: Dissipating the heat generated by high-frequency components to prevent performance degradation and ensure long-term reliability
- Material selection: Choosing PCB materials with suitable dielectric properties and low loss tangents to minimize signal attenuation and distortion at high frequencies
Conclusion
PCBs are essential components in a wide range of electronic applications, from consumer devices to industrial equipment, medical systems, and renewable energy solutions. Their versatility, reliability, and cost-effectiveness have made them indispensable in the modern world. As technology continues to advance, the demand for more complex and specialized PCBs is expected to grow, driving innovation in PCB design and manufacturing processes. By understanding the various applications of PCBs and their critical role in electronics, engineers and technicians can develop more efficient, reliable, and innovative solutions to meet the evolving needs of their respective industries.
Leave a Reply