What are Flexible Printed Circuits?
Flexible printed circuits are a type of printed circuit board (PCB) that consists of a thin, flexible substrate with conductive traces and components mounted on its surface. Unlike traditional rigid PCBs, FPCs can be bent, twisted, and folded to fit into tight spaces or conform to the shape of the device in which they are used. This flexibility is achieved by using materials such as polyimide, polyester, or PEEK (polyetheretherketone) as the base substrate, which can withstand repeated bending and flexing without breaking or losing their electrical properties.
Types of Flexible Printed Circuits
There are several types of flexible printed circuits, each designed to meet specific requirements and applications. The most common types include:
Single-sided Flex Circuits
Single-sided flex circuits have conductive traces and components on only one side of the flexible substrate. They are the simplest and most cost-effective type of FPC, suitable for applications that require basic interconnections and minimal flexibility.
Double-sided Flex Circuits
Double-sided flex circuits have conductive traces and components on both sides of the flexible substrate, with interconnections between the layers achieved through plated through-holes (PTHs). These circuits offer higher component density and more complex routing compared to single-sided FPCs.
Multi-layer Flex Circuits
Multi-layer flex circuits consist of three or more conductive layers, separated by insulating layers and interconnected through PTHs. These circuits provide the highest level of complexity and density, allowing for the integration of multiple functions and components in a single, compact package.
Rigid-Flex Circuits
Rigid-flex circuits combine the benefits of both rigid and flexible PCBs by incorporating rigid sections for mounting components and flexible sections for interconnections. This hybrid design allows for greater design flexibility, improved reliability, and reduced assembly costs compared to using separate rigid and flexible circuits.
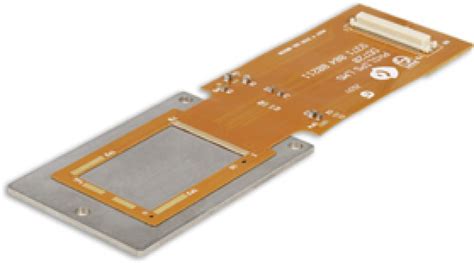
Benefits of Flexible Printed Circuits
Flexible printed circuits offer several advantages over traditional rigid PCBs, making them the preferred choice for many applications. Some of the key benefits include:
Flexibility and Durability
The most obvious benefit of FPCs is their flexibility, which allows them to be bent, twisted, and folded to fit into tight spaces or conform to the shape of the device. This flexibility also makes them more durable and resistant to vibration and shock, as they can absorb mechanical stresses without breaking or losing their electrical properties.
Lightweight and Compact
FPCs are typically thinner and lighter than rigid PCBs, making them ideal for use in portable and wearable devices where weight and size are critical factors. Their compact design also allows for greater component density and more efficient use of space, reducing the overall size of the device.
Improved Signal Integrity
The thin, flexible nature of FPCs allows for shorter signal paths and reduced parasitic capacitance and inductance, resulting in improved signal integrity and reduced electromagnetic interference (EMI). This is particularly important in high-speed and high-frequency applications, such as telecommunications and radar systems.
Cost-effective
FPCs can be more cost-effective than rigid PCBs in certain applications, especially when considering the total cost of ownership. Their flexibility and durability can reduce the need for additional connectors and cables, simplifying the assembly process and reducing manufacturing costs. Additionally, their compact design can lead to reduced material usage and inventory costs.
Design Freedom
The flexibility of FPCs allows for greater design freedom, enabling engineers to create complex, three-dimensional structures that would be impossible with rigid PCBs. This design freedom can lead to more innovative and efficient products, as well as improved aesthetics and user experience.
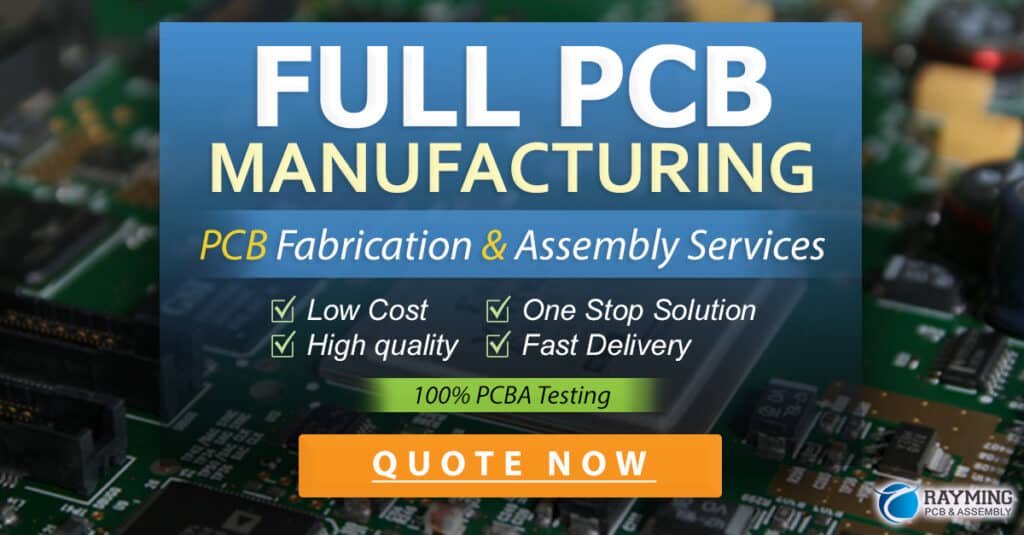
Applications of Flexible Printed Circuits
Flexible printed circuits find applications in a wide range of industries, from consumer electronics to aerospace and defense. Some of the most common applications include:
Consumer Electronics
FPCs are widely used in consumer electronics, such as smartphones, tablets, laptops, and wearable devices. They enable the creation of slim, lightweight, and flexible designs that can withstand the rigors of daily use. Examples include the flexible displays and touch screens in smartphones, the hinge connections in laptops, and the sensor arrays in smartwatches.
Medical Devices
The flexibility and biocompatibility of FPCs make them ideal for use in medical devices, such as implantable sensors, pacemakers, and surgical instruments. They can conform to the shape of the body, reducing patient discomfort and improving device performance. Additionally, their compact design allows for the creation of smaller, less invasive devices that can be easily inserted and removed.
Automotive Electronics
FPCs are increasingly used in automotive electronics, such as infotainment systems, instrument clusters, and advanced driver assistance systems (ADAS). They offer improved reliability and durability compared to rigid PCBs, as they can withstand the harsh environmental conditions and vibrations encountered in vehicles. Their lightweight and compact design also contributes to fuel efficiency and reduced vehicle weight.
Aerospace and Defense
In the aerospace and defense industry, FPCs are used in a variety of applications, such as avionics, satellites, and military communications systems. Their flexibility and durability make them ideal for use in harsh environments, such as extreme temperatures, high altitudes, and high-vibration conditions. Additionally, their lightweight and compact design helps reduce the overall weight of aircraft and spacecraft, improving fuel efficiency and payload capacity.
Industrial Equipment
FPCs are used in various types of industrial equipment, such as robotics, automation systems, and process control devices. Their flexibility allows for the creation of complex, three-dimensional structures that can fit into tight spaces and conform to the shape of the equipment. Their durability and resistance to harsh environments also make them suitable for use in industrial settings, where they may be exposed to chemicals, extreme temperatures, and mechanical stresses.
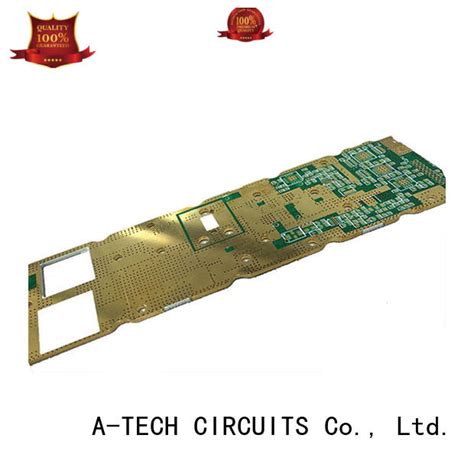
Advantages of Flexible Printed Circuits over Traditional Wiring Methods
Flexible printed circuits offer several advantages over traditional wiring methods, such as wire harnesses and cable assemblies. These advantages include:
Space and Weight Reduction
FPCs are thinner and lighter than traditional wiring methods, allowing for more compact and lightweight designs. This is particularly important in applications where space and weight are critical factors, such as aerospace and wearable devices.
Improved Reliability
FPCs eliminate the need for individual wires and connectors, reducing the number of potential failure points in the system. Additionally, their flexibility and durability make them more resistant to vibration, shock, and other mechanical stresses, improving overall system reliability.
Simplified Assembly
FPCs simplify the assembly process by integrating multiple components and interconnections into a single, compact package. This reduces the need for manual wiring and soldering, leading to faster and more efficient assembly times.
Reduced EMI and Crosstalk
The thin, flexible nature of FPCs allows for shorter signal paths and reduced parasitic capacitance and inductance, minimizing electromagnetic interference (EMI) and crosstalk between signals. This is particularly important in high-speed and high-frequency applications, where signal integrity is critical.
Comparison of Flexible Printed Circuits and Rigid Printed Circuit Boards
Characteristic | Flexible Printed Circuits | Rigid Printed Circuit Boards |
---|---|---|
Flexibility | High | Low |
Durability | High | Moderate |
Weight | Low | Moderate to High |
Thickness | Thin (typically 0.1-0.3 mm) | Thicker (typically 0.4-2.0 mm) |
Component Density | High | Moderate to High |
Signal Integrity | High | Moderate to High |
EMI and Crosstalk | Low | Moderate to High |
Assembly Complexity | Low to Moderate | Moderate to High |
Cost | Low to Moderate | Moderate to High |
FAQs
1. What is the difference between a flexible printed circuit and a rigid printed circuit board?
A flexible printed circuit is a type of PCB that uses a flexible substrate material, allowing it to bend and flex without breaking or losing its electrical properties. In contrast, a rigid printed circuit board uses a rigid substrate material, such as FR-4, which does not allow for flexibility. FPCs are typically thinner, lighter, and more durable than rigid PCBs, making them ideal for applications that require flexibility, compact design, and resistance to mechanical stresses.
2. What materials are used to make flexible printed circuits?
The most common materials used for the flexible substrate in FPCs are polyimide, polyester, and PEEK (polyetheretherketone). Polyimide is the most widely used material due to its excellent mechanical, thermal, and electrical properties. The conductive traces on FPCs are typically made of copper, which is bonded to the flexible substrate using adhesives or lamination techniques.
3. Can flexible printed circuits be used in high-temperature applications?
Yes, certain types of FPCs can be designed to withstand high temperatures. For example, polyimide-based FPCs can operate at temperatures up to 200°C, while PEEK-based FPCs can withstand temperatures up to 260°C. However, the specific temperature range will depend on the materials used and the design of the circuit.
4. How are components mounted on flexible printed circuits?
Components can be mounted on FPCs using various techniques, such as surface mount technology (SMT), chip-on-flex (COF), and flip-chip bonding. SMT is the most common method, where components are soldered directly onto the surface of the FPC. COF and flip-chip bonding are used for more advanced applications, where bare die or unpackaged components are directly bonded to the FPC substrate.
5. What are the challenges in designing and manufacturing flexible printed circuits?
Designing and manufacturing FPCs can be more challenging than rigid PCBs due to their unique properties and requirements. Some of the key challenges include:
- Ensuring the flexibility and durability of the circuit under repeated bending and flexing
- Maintaining signal integrity and minimizing EMI and crosstalk in high-speed and high-frequency applications
- Selecting the appropriate materials and adhesives for the specific application and environmental conditions
- Developing specialized manufacturing processes and equipment for handling and assembling thin, flexible substrates
- Testing and validating the performance and reliability of FPCs under various mechanical and environmental stresses
To overcome these challenges, designers and manufacturers of FPCs need to have a deep understanding of the materials, processes, and applications involved, as well as access to advanced design tools and manufacturing capabilities.
Conclusion
Flexible printed circuits have become an essential component in a wide range of electronic devices and systems, offering numerous benefits over traditional rigid PCBs and wiring methods. Their flexibility, durability, lightweight, and compact design make them ideal for applications that require conformity to complex shapes, resistance to mechanical stresses, and efficient use of space and weight.
As technology continues to advance and new applications emerge, the demand for flexible printed circuits is expected to grow rapidly. From consumer electronics and medical devices to automotive and aerospace systems, FPCs will play an increasingly important role in enabling the development of more innovative, efficient, and reliable products.
By understanding the different types of flexible printed circuits, their benefits, and their applications, engineers and designers can make informed decisions when selecting the appropriate interconnect solution for their projects. With the right design, materials, and manufacturing processes, flexible printed circuits can help bring new ideas to life and push the boundaries of what is possible in the world of electronics.
Leave a Reply