Introduction to Copper Clad Laminate
Copper Clad Laminate (CCL) is a fundamental material used in the fabrication of printed circuit boards (PCBs). It consists of a thin layer of copper foil bonded to a dielectric substrate, typically made of glass-reinforced epoxy resin or other composite materials. CCL serves as the foundation for creating conductive paths, pads, and other features on PCBs, which are essential components in electronic devices.
Composition of Copper Clad Laminate
A typical Copper Clad Laminate consists of three main components:
-
Copper foil: A thin layer of pure copper, usually ranging from 9 to 175 microns (0.0004 to 0.007 inches) in thickness. The copper foil provides the conductive layer for the PCB.
-
Dielectric substrate: A non-conductive material, often made of glass-reinforced epoxy resin (FR-4), polyimide, or other composite materials. The substrate provides mechanical support and electrical insulation between the copper layers.
-
Adhesive: A bonding agent that adheres the copper foil to the dielectric substrate, ensuring a strong and stable connection.
Manufacturing Process of Copper Clad Laminate
The production of Copper Clad Laminate involves several steps:
-
Substrate preparation: The dielectric substrate is cut to the desired size and shape, and its surface is cleaned and treated to enhance adhesion.
-
Copper foil preparation: The copper foil is also cut to size and cleaned to remove any contaminants or oxides.
-
Lamination: The prepared substrate and copper foil are placed together with the adhesive and subjected to high temperature and pressure in a lamination press. This process bonds the layers together, creating a solid, uniform sheet of CCL.
-
Cooling and inspection: After lamination, the CCL is cooled and inspected for any defects, such as delamination, blistering, or inconsistent copper thickness.
-
Cutting and packaging: The CCL is then cut to the desired dimensions and packaged for shipment to PCB manufacturers.
Types of Copper Clad Laminate
There are several types of Copper Clad Laminate, each with unique properties and applications:
FR-4 Copper Clad Laminate
FR-4 (Flame Retardant 4) is the most common type of CCL used in the electronics industry. It consists of a glass-reinforced epoxy resin substrate and is known for its excellent mechanical, thermal, and electrical properties. FR-4 CCL is suitable for a wide range of applications, from consumer electronics to industrial equipment.
High-Frequency Copper Clad Laminate
High-frequency CCLs are designed for applications that require low dielectric loss and stable performance at high frequencies, such as in radio frequency (RF) and microwave circuits. These laminates often use specialized substrate materials, such as polytetrafluoroethylene (PTFE) or hydrocarbon ceramic, which have low dielectric constants and dissipation factors.
Flexible Copper Clad Laminate
Flexible CCLs use flexible dielectric substrates, such as polyimide or polyester, to create bendable and conformable PCBs. These laminates are essential for applications that require flexibility, such as wearable electronics, flexible displays, and compact devices with limited space.
Metal Core Copper Clad Laminate
Metal core CCLs feature a metal baseplate, typically made of aluminum or copper, sandwiched between the dielectric substrate and the copper foil. The metal core provides excellent thermal conductivity, allowing for efficient heat dissipation in high-power applications, such as LED lighting and automotive electronics.
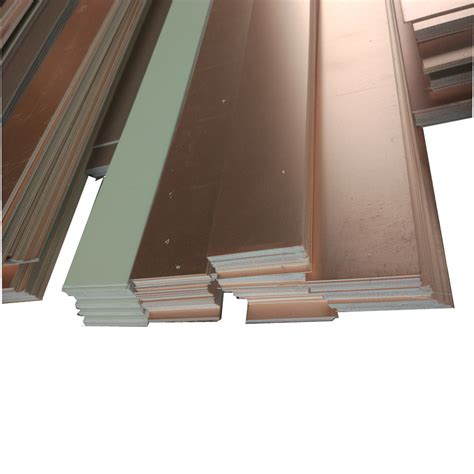
Properties of Copper Clad Laminate
The performance of a Copper Clad Laminate depends on several key properties:
Copper Thickness
The thickness of the copper foil determines the current-carrying capacity and the ability to create fine-pitch features on the PCB. Common copper thicknesses range from 9 to 175 microns (0.0004 to 0.007 inches), with thinner foils used for high-density designs and thicker foils for power electronics.
Dielectric Constant (Dk)
The dielectric constant is a measure of a material’s ability to store electrical energy. A lower Dk value indicates better signal integrity and reduced signal propagation delay, which is essential for high-frequency applications. Common dielectric constants for CCLs range from 2.2 to 4.8.
Dissipation Factor (Df)
The dissipation factor, or loss tangent, represents the amount of energy lost as heat when an alternating current passes through the dielectric material. A lower Df value indicates lower signal loss and better performance at high frequencies. Typical dissipation factors for CCLs range from 0.002 to 0.02.
Thermal Conductivity
Thermal conductivity is a measure of a material’s ability to conduct heat. Higher thermal conductivity allows for better heat dissipation, which is crucial for high-power applications. Metal core CCLs offer the highest thermal conductivity, followed by ceramic-filled substrates and standard FR-4 laminates.
Mechanical Strength
The mechanical strength of a CCL determines its ability to withstand stress and strain during manufacturing and use. Factors such as the type of reinforcement (e.g., glass fibers), resin composition, and lamination process affect the mechanical properties of the laminate.
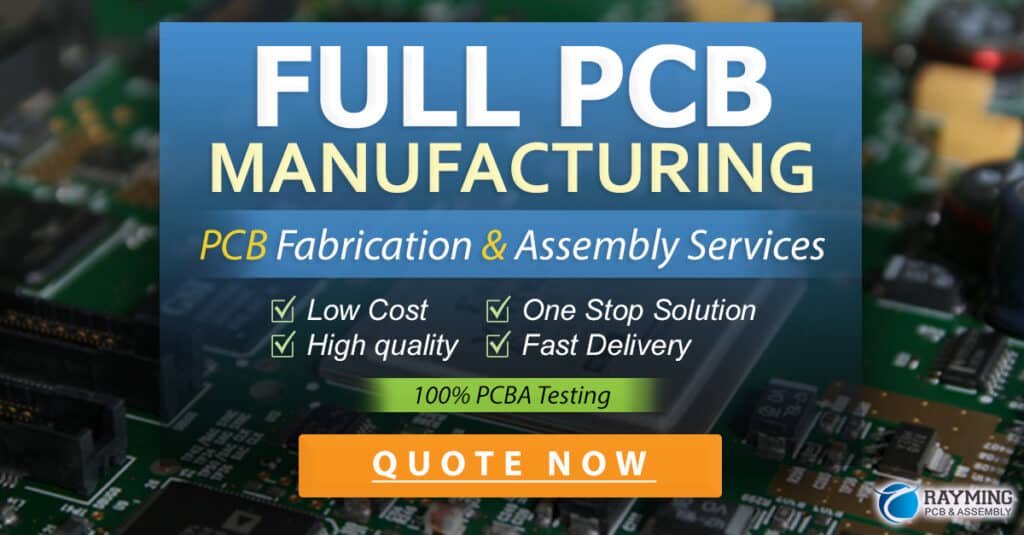
Applications of Copper Clad Laminate
Copper Clad Laminates are used in a wide range of electronic applications, including:
- Consumer electronics: Smartphones, tablets, laptops, televisions, and home appliances.
- Automotive electronics: Engine control units, infotainment systems, and advanced driver assistance systems (ADAS).
- Industrial electronics: Process control systems, automation equipment, and power electronics.
- Medical devices: Diagnostic equipment, monitoring systems, and implantable devices.
- Aerospace and defense: Avionics, radar systems, and satellite communication equipment.
- Telecommunications: Base stations, routers, switches, and fiber optic networks.
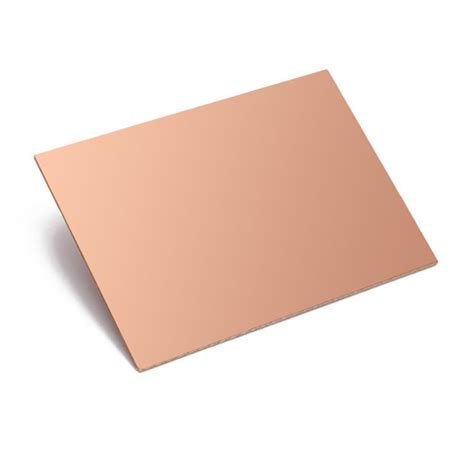
Advantages of Copper Clad Laminate
Copper Clad Laminates offer several advantages in the production of PCBs:
- Consistency: CCLs provide a consistent and reliable foundation for creating conductive patterns on PCBs, ensuring uniform electrical performance.
- Customization: With a wide range of substrate materials, copper thicknesses, and dielectric properties available, CCLs can be tailored to meet the specific requirements of different applications.
- Scalability: CCLs are manufactured in large sheets, allowing for high-volume production of PCBs and reducing overall costs.
- Durability: The lamination process creates a strong bond between the copper foil and the substrate, resulting in a durable and stable product that can withstand the rigors of manufacturing and use.
- Thermal management: Metal core CCLs and other specialized laminates offer enhanced thermal conductivity, enabling efficient heat dissipation in high-power applications.
Challenges and Future Trends in Copper Clad Laminate
As electronic devices continue to evolve, Copper Clad Laminates face new challenges and opportunities:
- Miniaturization: The demand for smaller, more compact devices requires thinner and more precise CCLs, pushing the limits of current manufacturing techniques.
- High-speed applications: The increasing use of high-frequency technologies, such as 5G and millimeter-wave communications, necessitates the development of low-loss, high-performance CCLs.
- Environmental concerns: The electronics industry is moving towards more sustainable and eco-friendly materials, driving the development of halogen-free and low-toxicity CCLs.
- Flexible and wearable electronics: The growth of flexible and wearable devices requires the continued development of flexible CCLs with improved mechanical and electrical properties.
- Advanced manufacturing: Innovations in lamination processes, such as the use of laser direct imaging (LDI) and additive manufacturing techniques, may lead to new possibilities in CCL production and PCB fabrication.
Property | FR-4 | High-Frequency | Flexible | Metal Core |
---|---|---|---|---|
Dielectric Constant (Dk) | 4.2 – 4.8 | 2.2 – 3.5 | 3.0 – 4.0 | 4.0 – 4.5 |
Dissipation Factor (Df) | 0.02 | 0.002 – 0.01 | 0.002 – 0.01 | 0.01 – 0.02 |
Thermal Conductivity (W/mK) | 0.3 – 0.4 | 0.2 – 0.3 | 0.2 – 0.3 | 1.0 – 3.0 |
Typical Applications | General electronics | RF and microwave | Wearables and flexible devices | High-power and thermal management |
Frequently Asked Questions (FAQ)
1. What is the difference between single-sided and double-sided Copper Clad Laminate?
Single-sided CCL has a layer of copper foil on one side of the dielectric substrate, while double-sided CCL has copper foil on both sides. Double-sided CCL allows for the creation of more complex PCB designs with interconnections between layers.
2. Can Copper Clad Laminate be recycled?
Yes, Copper Clad Laminate can be recycled. The copper foil can be separated from the substrate and recycled as pure copper, while the substrate can be ground down and used as a filler material in other applications.
3. How does the thickness of the copper foil affect the performance of the PCB?
Thicker copper foils offer higher current-carrying capacity and better heat dissipation, making them suitable for power electronics. Thinner foils allow for the creation of finer pitch features and are used in high-density PCB designs.
4. What is the purpose of the adhesive in Copper Clad Laminate?
The adhesive is used to bond the copper foil to the dielectric substrate, creating a strong and stable connection. The quality of the adhesive is crucial for preventing delamination and ensuring the long-term reliability of the PCB.
5. Are there any alternatives to traditional Copper Clad Laminate materials?
Yes, there are several alternative materials being developed and used in specific applications. These include metal-clad polymers, carbon fiber composites, and ceramic substrates. Each of these materials offers unique properties and benefits, such as enhanced thermal conductivity, improved mechanical strength, or better high-frequency performance.
Conclusion
Copper Clad Laminate is a crucial component in the production of printed circuit boards, serving as the foundation for creating conductive patterns and interconnections in electronic devices. With a wide range of materials, properties, and applications, CCLs offer designers and manufacturers the flexibility to create PCBs tailored to specific requirements.
As the electronics industry continues to evolve, Copper Clad Laminates will play a vital role in enabling new technologies and innovations. By understanding the composition, types, properties, and applications of CCLs, engineers and designers can make informed decisions when selecting materials for their projects and developing the next generation of electronic devices.
Leave a Reply