Understanding PCB Thickness
PCB thickness is measured in mils (thousandths of an inch) or millimeters (mm). The most common PCB thicknesses range from 0.8mm to 2.0mm, with 1.6mm being the most widely used standard thickness. However, the choice of thickness depends on several factors, including the application, the number of layers, the components used, and the manufacturing process.
Standard PCB Thicknesses
Thickness (mm) | Thickness (mils) | Common Applications |
---|---|---|
0.8mm | 31.5 mils | Flexible PCBs, high-density designs |
1.0mm | 39.4 mils | Compact devices, mobile phones |
1.2mm | 47.2 mils | General-purpose PCBs |
1.6mm | 63.0 mils | Most common thickness, suitable for a wide range of applications |
2.0mm | 78.7 mils | High-power applications, industrial controls |
Factors Influencing PCB Thickness Choice
1. Application Requirements
The intended application of your PCB prototype is a primary factor in determining the appropriate thickness. Different applications have varying requirements in terms of mechanical strength, thermal management, and electrical performance. For example:
- Flexible PCBs used in wearable devices or compact spaces often require thinner boards (0.8mm or less) to ensure flexibility and fit.
- High-power applications, such as industrial controls or power electronics, may demand thicker boards (2.0mm or more) to dissipate heat effectively and provide structural stability.
2. Number of Layers
The number of layers in your PCB design also influences the choice of thickness. As the number of layers increases, the overall thickness of the board typically increases as well. This is because each additional layer requires its own substrate and copper foil, adding to the total thickness of the PCB.
Number of Layers | Typical Thickness Range |
---|---|
1-2 layers | 0.8mm – 1.6mm |
4 layers | 1.0mm – 2.0mm |
6-8 layers | 1.6mm – 2.5mm |
10+ layers | 2.0mm – 3.5mm |
3. Component Requirements
The components used in your PCB design can also dictate the thickness of the board. Some components, such as through-hole components or heavy power components, may require a thicker board to provide adequate support and heat dissipation. Surface-mount components, on the other hand, can often be accommodated on thinner boards.
4. Manufacturing Process
The manufacturing process employed for your PCB prototype can influence the choice of thickness. Different PCB manufacturers may have specific capabilities and limitations when it comes to handling different board thicknesses. It’s essential to consult with your chosen manufacturer to ensure they can accommodate your desired thickness and provide guidance on the most suitable option for your design.
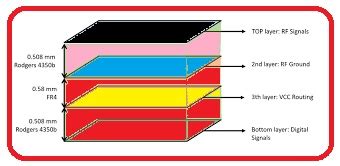
Benefits of Choosing the Right PCB Thickness
Selecting the appropriate PCB thickness for your prototype offers several benefits:
-
Improved Mechanical Stability: A PCB with the right thickness will have better mechanical stability, reducing the risk of warping, bending, or damage during handling and operation.
-
Enhanced Thermal Management: Thicker PCBs can dissipate heat more effectively, preventing overheating and ensuring optimal performance of components.
-
Increased Durability: Choosing the correct thickness ensures that your PCB can withstand the rigors of its intended application, resulting in a more durable and reliable product.
-
Cost Optimization: By selecting the appropriate thickness, you can avoid unnecessary costs associated with over-specifying or under-specifying the PCB thickness for your prototype.
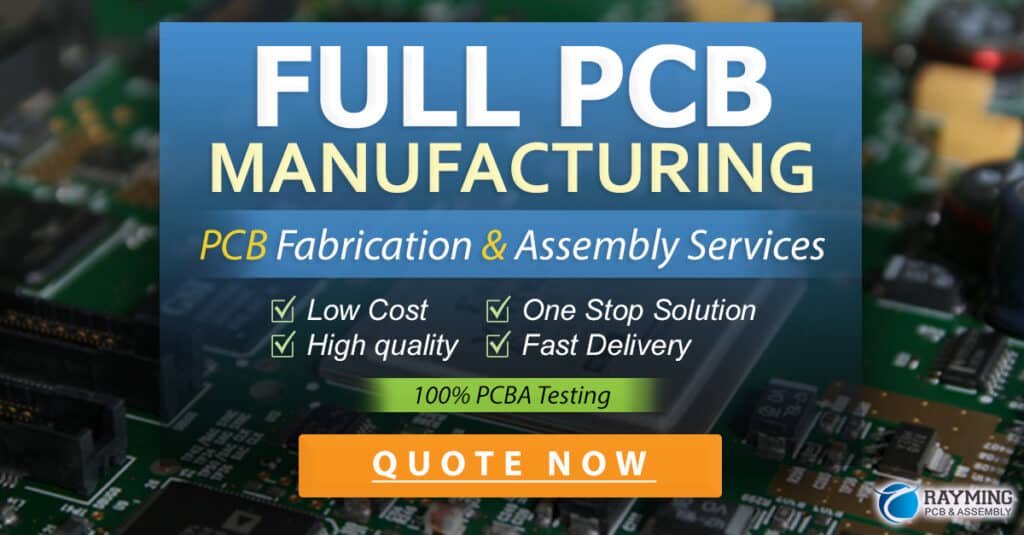
Common PCB Thickness Challenges and Solutions
Challenge 1: Balancing Thickness and Flexibility
In applications that require flexibility, such as wearable devices or compact spaces, finding the right balance between thickness and flexibility can be challenging. Thinner PCBs offer better flexibility but may compromise mechanical stability and durability.
Solution: Consider using flexible PCB materials, such as polyimide or polyester, which can provide the necessary flexibility while maintaining structural integrity. Additionally, employing reinforcement techniques, such as using stiffeners or strategic component placement, can help improve the mechanical stability of thin PCBs.
Challenge 2: Managing High-Power Applications
High-power applications often generate significant heat, which needs to be dissipated effectively to prevent component failure and ensure reliable operation. Thicker PCBs are typically preferred for better thermal management, but this can increase the overall size and weight of the board.
Solution: Incorporate thermal management techniques, such as using thermal vias, heat sinks, or thermal interface materials, to enhance heat dissipation even with thinner PCBs. Additionally, consider using high-thermal-conductivity PCB materials, such as metal-core PCBs or aluminum-backed PCBs, which can effectively transfer heat away from critical components.
Challenge 3: Accommodating High-Density Designs
As electronic devices become more compact and sophisticated, PCB designs often require high component density. Thinner PCBs are preferred for high-density designs to minimize the overall size of the device. However, thinner boards can pose challenges in terms of signal integrity and manufacturability.
Solution: Employ advanced PCB design techniques, such as high-density interconnect (HDI) technology, which allows for finer trace widths and smaller via sizes. HDI PCBs enable higher component density while maintaining signal integrity. Additionally, work closely with your PCB manufacturer to ensure they have the capabilities to handle high-density designs on thinner boards.
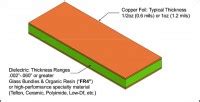
FAQ
-
Q: What is the most common PCB thickness used in the industry?
A: The most common PCB thickness used in the industry is 1.6mm (63 mils). This thickness offers a good balance between mechanical stability, thermal management, and compatibility with a wide range of applications. -
Q: Can I use a thinner PCB for my high-power application to save space?
A: While using a thinner PCB can save space, it’s essential to prioritize thermal management in high-power applications. Thinner PCBs may not dissipate heat as effectively, leading to component failure and reliability issues. It’s recommended to use thicker PCBs (2.0mm or more) for high-power applications and incorporate additional thermal management techniques if space is a constraint. -
Q: How does the number of layers affect the thickness of a PCB?
A: As the number of layers in a PCB increases, the overall thickness of the board typically increases as well. Each additional layer requires its own substrate and copper foil, contributing to the total thickness. For example, a 4-layer PCB will generally be thicker than a 2-layer PCB. -
Q: Are there any limitations on the minimum thickness of a PCB?
A: The minimum thickness of a PCB is primarily determined by the manufacturing capabilities of your chosen PCB manufacturer. Some manufacturers can produce ultra-thin PCBs down to 0.2mm or even thinner. However, it’s crucial to discuss your specific requirements with your manufacturer to ensure they can accommodate your desired thickness while maintaining the necessary performance and reliability. -
Q: Can I mix different thicknesses within the same PCB design?
A: Yes, it is possible to have different thicknesses within the same PCB design, known as a hybrid or variable-thickness PCB. This approach allows you to optimize the thickness in specific areas of the board based on component requirements, thermal management needs, or mechanical constraints. However, designing and manufacturing hybrid PCBs can be more complex and costly compared to standard uniform-thickness PCBs.
Conclusion
Choosing the correct thickness for your PCB prototype is a critical decision that impacts the performance, reliability, and overall success of your electronic device. By understanding the factors that influence PCB thickness, such as application requirements, the number of layers, component needs, and manufacturing processes, you can make an informed choice that balances functionality, durability, and cost-effectiveness.
Remember to consider the specific challenges and solutions associated with different PCB thicknesses, such as balancing thickness and flexibility, managing high-power applications, and accommodating high-density designs. Working closely with your PCB manufacturer and leveraging their expertise can help you navigate these challenges and arrive at the optimal thickness for your PCB prototype.
By selecting the right PCB thickness, you can ensure that your prototype meets the demands of its intended application, performs reliably, and sets the foundation for a successful final product. So, take the time to carefully evaluate your requirements and consult with industry professionals to make the best choice for your PCB thickness.
Leave a Reply