Understanding Microcontroller Failure
Microcontroller failure refers to the inability of a microcontroller to perform its intended functions correctly. This can manifest in various ways, such as:
- Incorrect output or behavior
- Unresponsive or frozen state
- Complete failure to operate
These failures can lead to system malfunctions, reduced performance, or even complete device failure. Understanding the causes of microcontroller failure is crucial for designing reliable and robust electronic systems.
Common Microcontroller Failure Modes
1. Electrical Overstress (EOS)
Electrical overstress occurs when a microcontroller is subjected to voltage or current levels that exceed its maximum ratings. This can happen due to various reasons, such as:
- Power supply fluctuations
- Electrostatic discharge (ESD)
- Incorrect connections or wiring
EOS can cause permanent damage to the microcontroller’s internal circuitry, leading to immediate failure or reduced lifespan.
Prevention methods:
– Use appropriate voltage regulators and power supply filtering
– Implement ESD protection measures, such as using ESD-safe handling procedures and ESD protection devices
– Follow proper wiring and connection guidelines
2. Thermal Stress
Microcontrollers generate heat during operation, and excessive heat can lead to thermal stress. High temperatures can cause:
- Accelerated aging of the microcontroller
- Reduced performance and reliability
- Permanent damage to the internal components
Thermal stress can be caused by:
– Inadequate cooling or ventilation
– High ambient temperatures
– Excessive power dissipation
Prevention methods:
– Use appropriate heat sinks or cooling mechanisms
– Ensure proper ventilation and airflow in the device enclosure
– Monitor and control the operating temperature using temperature sensors and thermal management techniques
3. Software Issues
Software-related issues can also lead to microcontroller failure. These can include:
- Bugs or errors in the firmware or application code
- Incorrect configuration or settings
- Memory corruption or overflow
Software issues can cause unexpected behavior, system crashes, or even permanent damage to the microcontroller.
Prevention methods:
– Follow best practices in software development, such as code review, testing, and debugging
– Use reliable and well-tested libraries and frameworks
– Implement error handling and recovery mechanisms in the software
4. Mechanical Stress
Microcontrollers can be subjected to mechanical stress due to:
- Vibration or shock
- Bending or flexing of the PCB
- Connector or solder joint failures
Mechanical stress can cause physical damage to the microcontroller package or the PCB, leading to electrical failures or intermittent issues.
Prevention methods:
– Use appropriate mounting and support mechanisms to minimize mechanical stress
– Follow proper PCB design guidelines, such as using strain relief and avoiding sharp bends
– Use high-quality connectors and solder joints
5. Environmental Factors
Microcontrollers can be affected by various environmental factors, such as:
- Humidity and moisture
- Corrosive gases or liquids
- Dust or particulate matter
These factors can cause corrosion, short-circuits, or other physical damage to the microcontroller.
Prevention methods:
– Use appropriate enclosures or protective coatings to shield the microcontroller from environmental factors
– Implement sealing and gaskets to prevent ingress of moisture or contaminants
– Use conformal coatings or potting compounds for additional protection
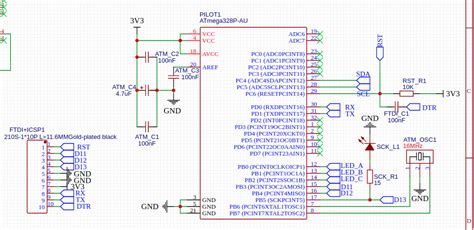
Microcontroller Failure Analysis Techniques
When a microcontroller failure occurs, it is important to analyze the root cause to prevent future occurrences and improve system reliability. Some common failure analysis techniques include:
1. Visual Inspection
Visual inspection involves examining the microcontroller and the surrounding components for any visible signs of damage or abnormalities. This can include:
- Burnt or discolored components
- Cracked or deformed packages
- Broken or corroded connections
Visual inspection can provide initial clues about the failure mode and guide further analysis.
2. Electrical Testing
Electrical testing involves measuring various electrical parameters of the microcontroller and comparing them with the expected values. This can include:
- Supply voltage and current measurements
- Input/output pin voltage and current measurements
- Oscilloscope waveform analysis
Electrical testing can help identify issues such as short-circuits, open-circuits, or signal integrity problems.
3. Fault Injection
Fault injection is a technique where deliberate faults are introduced into the system to observe the microcontroller’s behavior and response. This can help identify weaknesses or vulnerabilities in the design and improve fault tolerance.
Examples of fault injection techniques include:
– Power supply voltage variations
– Electromagnetic interference (EMI) injection
– Software-induced faults
4. Failure Mode and Effects Analysis (FMEA)
FMEA is a systematic approach to identifying potential failure modes and their effects on the system. It involves:
- Identifying the potential failure modes of the microcontroller
- Assessing the severity, occurrence, and detectability of each failure mode
- Prioritizing the failure modes based on their risk level
- Implementing corrective actions to mitigate or eliminate the failure modes
FMEA can help identify and prioritize the most critical failure modes and guide the development of preventive measures.
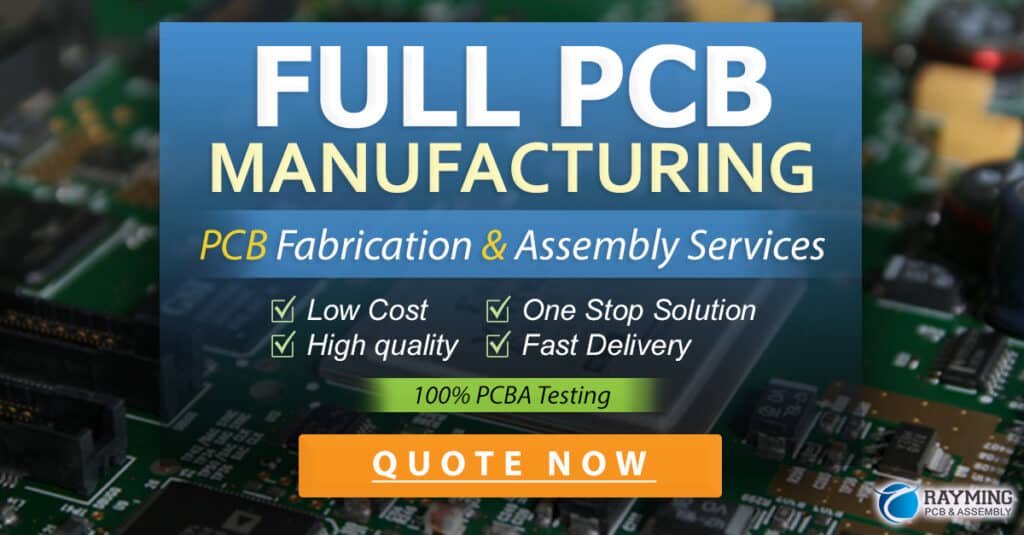
Best Practices for Preventing Microcontroller Failure
To minimize the risk of microcontroller failure, designers and developers should follow these best practices:
1. Robust Design
- Use appropriate voltage regulators and power supply filtering
- Implement ESD protection measures
- Use appropriate heat sinks and cooling mechanisms
- Follow proper PCB design guidelines
2. Rigorous Testing
- Perform comprehensive functional testing to verify the microcontroller’s behavior
- Conduct environmental testing to ensure the microcontroller’s reliability under various conditions
- Perform stress testing to identify potential weaknesses or failure modes
3. Defensive Programming
- Implement error handling and recovery mechanisms in the software
- Use watchdog timers to detect and recover from software crashes or hangs
- Implement memory protection and overflow prevention techniques
4. Regular Maintenance and Monitoring
- Perform regular visual inspections and cleaning of the microcontroller and surrounding components
- Monitor the operating conditions, such as temperature and voltage, to detect any anomalies
- Implement predictive maintenance techniques, such as condition monitoring or prognostics, to anticipate and prevent failures
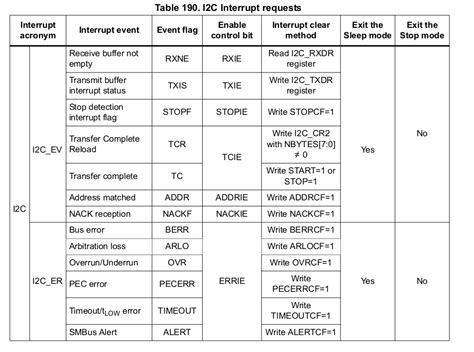
Frequently Asked Questions (FAQ)
1. What are the most common causes of microcontroller failure?
The most common causes of microcontroller failure include electrical overstress (EOS), thermal stress, software issues, mechanical stress, and environmental factors.
2. How can I prevent ESD damage to my microcontroller?
To prevent ESD damage, use appropriate ESD protection measures, such as ESD-safe handling procedures, ESD protection devices, and proper grounding techniques.
3. What should I do if my microcontroller is overheating?
If your microcontroller is overheating, ensure proper cooling and ventilation, use appropriate heat sinks or cooling mechanisms, and monitor the operating temperature using temperature sensors.
4. How can I identify the root cause of a microcontroller failure?
To identify the root cause of a microcontroller failure, use failure analysis techniques such as visual inspection, electrical testing, fault injection, and failure mode and effects analysis (FMEA).
5. What are some best practices for designing reliable microcontroller-based systems?
Best practices for designing reliable microcontroller-based systems include using robust design techniques, conducting rigorous testing, implementing defensive programming practices, and performing regular maintenance and monitoring.
Failure Mode | Causes | Prevention Methods |
---|---|---|
Electrical Overstress | – Power supply fluctuations – Electrostatic discharge – Incorrect connections |
– Use voltage regulators and power supply filtering – Implement ESD protection measures – Follow proper wiring guidelines |
Thermal Stress | – Inadequate cooling – High ambient temperatures – Excessive power dissipation |
– Use appropriate heat sinks or cooling mechanisms – Ensure proper ventilation – Monitor and control operating temperature |
Software Issues | – Bugs or errors in firmware/code – Incorrect configuration – Memory corruption |
– Follow best practices in software development – Use reliable libraries and frameworks – Implement error handling and recovery |
Mechanical Stress | – Vibration or shock – Bending or flexing of PCB – Connector or solder joint failures |
– Use appropriate mounting and support mechanisms – Follow proper PCB design guidelines – Use high-quality connectors and solder joints |
Environmental Factors | – Humidity and moisture – Corrosive gases or liquids – Dust or particulate matter |
– Use appropriate enclosures or protective coatings – Implement sealing and gaskets – Use conformal coatings or potting compounds |
Conclusion
Microcontroller failure is a significant concern in the design and development of electronic systems. By understanding the common failure modes, their causes, and prevention methods, designers and developers can create more reliable and robust microcontroller-based systems. Implementing best practices such as robust design, rigorous testing, defensive programming, and regular maintenance can greatly reduce the risk of microcontroller failure and ensure the long-term reliability of electronic devices.
Leave a Reply