Introduction to PCB Cooling and Heat Sinks
Printed Circuit Boards (PCBs) are the backbone of modern electronic devices, ranging from smartphones and laptops to industrial control systems and automotive electronics. As these devices become more compact and powerful, the challenge of managing heat dissipation becomes increasingly critical. Overheating can lead to reduced performance, reliability issues, and even complete system failure. To address this challenge, designers often employ surface mount heat sinks to enhance PCB cooling. In this article, we will explore the best design practices for implementing surface mount heat sinks to maximize PCB cooling efficiency.
Understanding the Basics of Heat Transfer in PCBs
Before diving into the design practices for surface mount heat sinks, it is essential to understand the fundamentals of heat transfer in PCBs. There are three primary mechanisms of heat transfer: conduction, convection, and radiation.
-
Conduction: Heat transfer through direct contact between materials. In PCBs, heat conducts from components to the PCB substrate and then to the heat sink.
-
Convection: Heat transfer through the movement of fluids (e.g., air or liquid coolants). Natural convection occurs due to temperature differences, while forced convection involves the use of fans or pumps.
-
Radiation: Heat transfer through electromagnetic waves. This mechanism is less significant in PCB cooling compared to conduction and convection.
The primary goal of PCB cooling is to efficiently move heat away from heat-generating components and dissipate it into the surrounding environment. Surface mount heat sinks play a crucial role in this process by providing a low-resistance thermal path and increasing the surface area for heat dissipation.
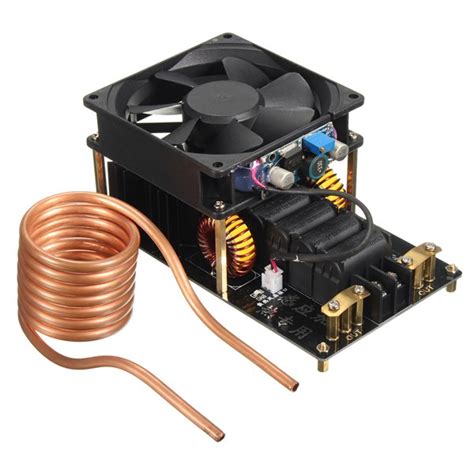
Selecting the Right Surface Mount Heat Sink Material
The choice of heat sink material is a critical factor in maximizing PCB cooling performance. The most common materials used for surface mount heat sinks are:
-
Aluminum: Aluminum is the most widely used material for heat sinks due to its excellent thermal conductivity, low cost, and ease of manufacturing. It is suitable for most applications with moderate heat dissipation requirements.
-
Copper: Copper has a higher thermal conductivity than aluminum, making it an ideal choice for high-performance applications. However, it is more expensive and has a higher density, which may be a concern in weight-sensitive applications.
-
Aluminum-copper composite: These heat sinks combine the benefits of both materials, offering high thermal conductivity and reduced weight compared to pure copper.
The table below compares the thermal conductivity and density of aluminum and copper:
Material | Thermal Conductivity (W/mK) | Density (g/cm³) |
---|---|---|
Aluminum | 205 | 2.70 |
Copper | 401 | 8.96 |
When selecting the heat sink material, consider factors such as the required cooling performance, weight restrictions, and cost constraints.
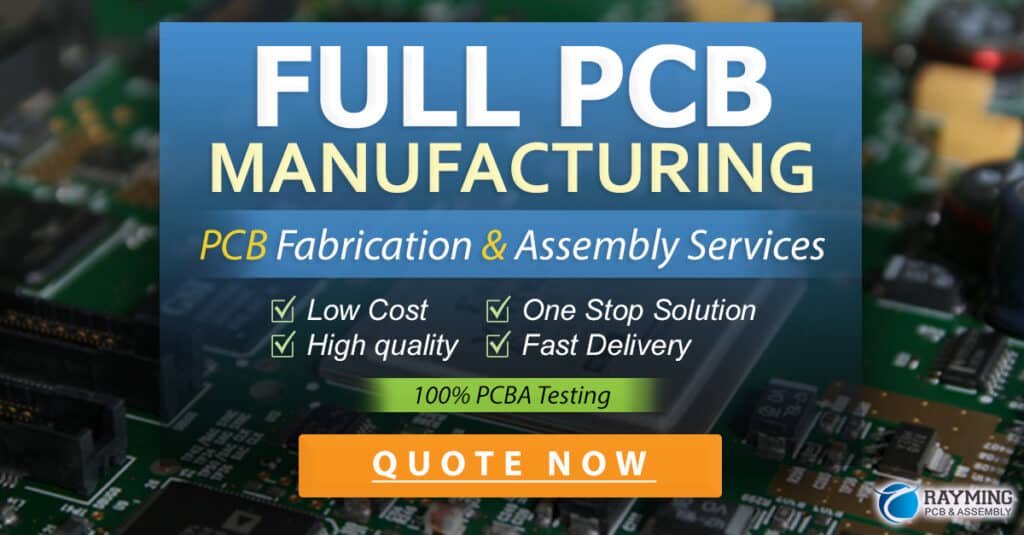
Optimizing Heat Sink Geometry for Enhanced Cooling
The geometry of a surface mount heat sink plays a vital role in its cooling performance. Several design factors can be optimized to maximize heat dissipation:
Fin Design
Heat sink fins increase the surface area for heat dissipation and promote convective heat transfer. The following fin design considerations can enhance cooling performance:
-
Fin Spacing: Optimal fin spacing allows for sufficient airflow between fins while maintaining a high surface area. Fin spacing should be determined based on the expected airflow conditions and the heat sink’s orientation.
-
Fin Thickness: Thinner fins offer more surface area for a given volume but may be more susceptible to mechanical damage. Thicker fins provide better structural integrity but reduce the overall surface area.
-
Fin Height: Taller fins increase the surface area and heat dissipation capacity but may be limited by the available space and airflow conditions.
Base Plate Design
The heat sink base plate is responsible for conducting heat from the PCB components to the fins. Consider the following factors when designing the base plate:
-
Thickness: A thicker base plate reduces thermal resistance and improves heat spreading. However, it also increases the overall heat sink weight and may be limited by space constraints.
-
Surface Finish: A smooth, flat surface finish ensures optimal contact between the heat sink and the PCB components. Poor surface quality can lead to air gaps and increased thermal resistance.
-
Mounting Holes: Properly sized and positioned mounting holes facilitate secure attachment of the heat sink to the PCB while minimizing stress on the components.
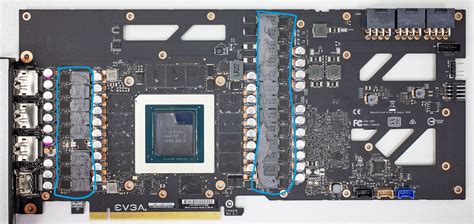
Enhancing Thermal Interface Materials (TIMs)
Thermal Interface Materials (TIMs) are crucial for ensuring efficient heat transfer between PCB components and the heat sink. TIMs fill the microscopic air gaps between surfaces, reducing thermal resistance. The most common types of TIMs used in PCB cooling are:
-
Thermal Greases: These are viscous, silicone-based compounds that offer excellent thermal conductivity and conformability. They are best suited for applications with high heat dissipation requirements and irregular mating surfaces.
-
Thermal Pads: These are pre-cut, elastomeric pads that provide a simple and clean installation process. They are ideal for applications with moderate heat dissipation needs and flat mating surfaces.
-
Phase Change Materials (PCMs): PCMs are solid at room temperature but melt at elevated temperatures, conforming to surface irregularities and improving thermal contact. They offer a balance between the performance of thermal greases and the ease of use of thermal pads.
When selecting a TIM, consider factors such as thermal conductivity, bond line thickness, ease of application, and long-term reliability. Proper TIM application and compression are essential for optimal thermal performance.
Incorporating Airflow Management Techniques
Effective airflow management is critical for maximizing the cooling performance of surface mount heat sinks. Consider the following techniques:
-
Component Placement: Strategically place heat-generating components to minimize thermal interaction and optimize airflow paths. Avoid clustering high-power components together, and position them near the edge of the PCB for better access to cooling air.
-
Airflow Direction: Orient heat sinks and components to align with the prevailing airflow direction in the enclosure. This ensures that cool air reaches the heat sinks and hot air is efficiently exhausted.
-
Ducting and Baffles: Use ducting and baffles to guide cool air directly to the heat sinks and prevent hot air recirculation. This can significantly improve cooling efficiency, especially in densely packed PCBs.
-
Fan Selection and Placement: When using active cooling, select fans with appropriate airflow and static pressure characteristics for the specific application. Position fans to optimize airflow over the heat sinks and avoid dead spots.
Thermal Simulation and Testing
Thermal simulation and testing are essential for validating the cooling performance of surface mount heat sinks and identifying potential issues before physical prototyping. There are two main approaches:
-
Computational Fluid Dynamics (CFD) Simulation: CFD software allows designers to simulate the airflow and heat transfer in a virtual environment. This helps optimize heat sink geometry, component placement, and airflow management strategies.
-
Thermal Testing: Physical thermal testing using thermocouples, infrared cameras, and thermal test boards provides real-world data on the cooling performance of the PCB assembly. This data can be used to validate simulation results and fine-tune the design.
Incorporating thermal simulation and testing into the design process enables iterative optimization and reduces the risk of thermal issues in the final product.
Best Practices for Heat Sink Installation
Proper installation of surface mount heat sinks is crucial for ensuring optimal cooling performance. Follow these best practices:
-
Surface Preparation: Clean the mating surfaces of the PCB components and heat sink to remove any dirt, grease, or oxidation. This ensures optimal thermal contact and prevents air gaps.
-
TIM Application: Apply the thermal interface material evenly and in the appropriate quantity. Excessive TIM can increase thermal resistance, while insufficient TIM may lead to air gaps.
-
Mounting Pressure: Apply consistent and adequate mounting pressure to ensure proper compression of the TIM and minimize thermal resistance. Use appropriate fasteners or clips to secure the heat sink to the PCB.
-
Inspection and Rework: Visually inspect the installed heat sink for any signs of misalignment, uneven contact, or excessive TIM squeeze-out. If necessary, rework the installation to ensure optimal thermal performance.
Following these best practices ensures that the surface mount heat sink performs as intended and maximizes PCB cooling efficiency.
Frequently Asked Questions (FAQ)
-
What is the most important factor in selecting a surface mount heat sink for PCB cooling?
The most important factor is the heat sink’s ability to dissipate the required amount of heat while meeting the space and weight constraints of the application. This involves considering factors such as heat sink material, geometry, and thermal interface material. -
Can I use a larger heat sink than necessary to ensure better cooling performance?
While a larger heat sink may provide better cooling performance, it is essential to balance the heat sink size with other design constraints such as available space, weight, and cost. Overdesigning the heat sink can lead to unnecessary expenses and potential compatibility issues. -
How do I determine the optimal fin spacing for my surface mount heat sink?
The optimal fin spacing depends on the expected airflow conditions and the heat sink’s orientation. In general, wider fin spacing is suitable for natural convection or low-airflow conditions, while narrower fin spacing is better for forced convection or high-airflow environments. CFD simulation and thermal testing can help determine the optimal fin spacing for a specific application. -
What is the most effective thermal interface material for high-performance PCB cooling?
Thermal greases offer the highest thermal conductivity and conformability, making them the most effective TIM for high-performance PCB cooling applications. However, they can be messy to apply and may require regular maintenance. For ease of use and cleanliness, thermal pads or phase change materials may be preferred. -
How often should I perform thermal testing on my PCB assembly with surface mount heat sinks?
Thermal testing should be performed during the initial design validation phase to ensure that the cooling solution meets the required performance targets. Additionally, periodic testing should be conducted during production to identify any quality issues or variations in the manufacturing process that may impact cooling performance.
Conclusion
Maximizing PCB cooling with surface mount heat sinks requires careful consideration of various design factors, including heat sink material, geometry, thermal interface materials, and airflow management. By following best design practices and incorporating thermal simulation and testing, designers can create efficient and reliable cooling solutions that ensure optimal performance and long-term reliability of electronic devices.
As the demand for high-performance, compact electronics continues to grow, the importance of effective PCB cooling will only increase. Staying up-to-date with the latest advancements in heat sink technology and design methodologies is essential for engineers and designers looking to push the boundaries of thermal management in PCB design.
Leave a Reply