Introduction to PCB Assembly and Production
Printed Circuit Board (PCB) assembly and production are crucial processes in the electronics industry. A well-designed and efficiently manufactured PCB is the foundation of any electronic device, from smartphones to medical equipment. In this article, we will explore the various aspects of PCB assembly and production, and how to keep these processes seamless for optimal results.
The Importance of Seamless PCB Assembly and Production
Benefits of a Seamless Process
A seamless PCB assembly and production process offers several benefits:
- Reduced lead times
- Lower production costs
- Improved product quality
- Increased customer satisfaction
Consequences of a Fragmented Process
On the other hand, a fragmented PCB assembly and production process can lead to:
- Delays in product delivery
- Increased manufacturing costs
- Inconsistent product quality
- Dissatisfied customers
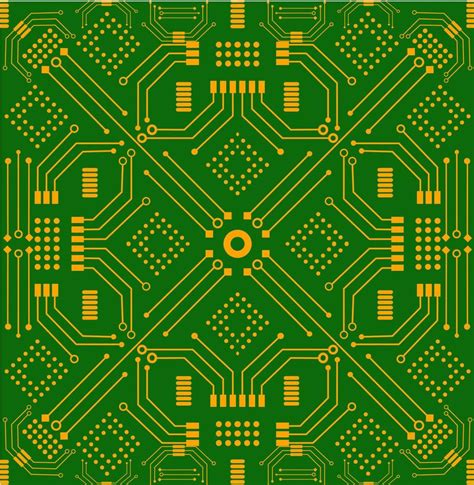
Key Steps in PCB Assembly and Production
PCB Design and Layout
The first step in the PCB assembly and production process is designing the circuit and creating the PCB layout. This involves:
- Schematic capture
- Component placement
- Routing
- Design rule checks (DRC)
PCB Fabrication
Once the PCB design is finalized, the next step is fabrication. This process includes:
- Printing the circuit pattern on the copper-clad board
- Etching away the unwanted copper
- Drilling holes for through-hole components
- Applying solder mask and silkscreen
Component Sourcing and Procurement
Sourcing and procuring the necessary components for PCB assembly is a critical step. This involves:
- Identifying reliable suppliers
- Negotiating prices and lead times
- Ensuring component quality and authenticity
- Managing inventory
PCB Assembly
With the fabricated PCB and components ready, the assembly process can begin. This step includes:
- Solder paste application
- Component placement (SMT and THT)
- Reflow soldering
- Wave soldering (if required)
- Inspection and testing
Quality Control and Testing
To ensure the final product meets the required specifications and standards, quality control and testing are essential. This process involves:
- Visual inspection
- Automated optical inspection (AOI)
- X-ray inspection
- In-circuit testing (ICT)
- Functional testing
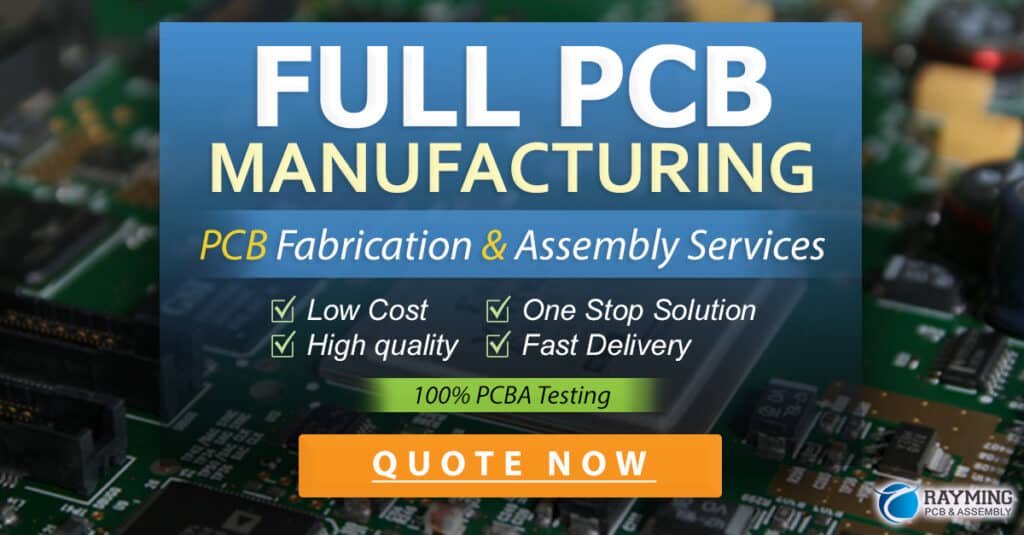
Best Practices for Seamless PCB Assembly and Production
Design for Manufacturability (DFM)
Designing PCBs with manufacturability in mind is crucial for a seamless production process. Some DFM guidelines include:
- Choosing appropriate component packages
- Maintaining proper spacing between components
- Avoiding acute angles in traces
- Providing clear silkscreen markings
Effective Communication and Collaboration
Seamless PCB assembly and production rely on effective communication and collaboration among all stakeholders, including:
- PCB designers
- Component suppliers
- PCB fabricators
- Assembly houses
- Quality control teams
Regular meetings, clear documentation, and a centralized project management system can help streamline communication and collaboration.
Automation and Technology
Implementing automation and advanced technology can significantly improve the efficiency and accuracy of PCB assembly and production. Some examples include:
- Computer-aided design (CAD) software
- Automated pick-and-place machines
- Robotic soldering systems
- Automated optical inspection (AOI) equipment
Continuous Improvement and Lean Manufacturing
Adopting a continuous improvement mindset and implementing lean manufacturing principles can help optimize PCB assembly and production processes. Some key practices include:
- Value stream mapping
- 5S workplace organization
- Kaizen events
- Just-in-time (JIT) inventory management
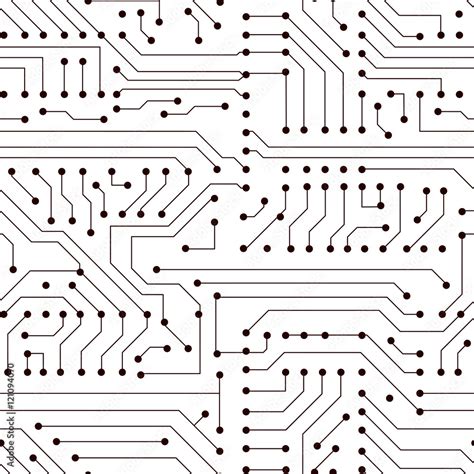
Case Studies
Company A: Streamlining PCB Assembly with Automation
Company A, a leading electronics manufacturer, faced challenges with inconsistent product quality and long lead times. By investing in automated pick-and-place machines and robotic soldering systems, they were able to:
- Reduce assembly time by 40%
- Improve product quality by 25%
- Decrease lead times by 30%
Company B: Implementing Lean Manufacturing for Seamless Production
Company B, a mid-sized PCB fabricator, struggled with inefficient processes and high production costs. By adopting lean manufacturing principles, such as value stream mapping and 5S workplace organization, they achieved:
- A 20% reduction in production costs
- A 15% increase in productivity
- A 10% improvement in on-time delivery
Frequently Asked Questions (FAQ)
- What is the difference between SMT and THT assembly?
-
Surface Mount Technology (SMT) involves placing components directly onto the surface of the PCB, while Through-Hole Technology (THT) requires inserting component leads through holes in the PCB and soldering them on the opposite side.
-
How can I ensure the quality of the components I source for my PCB assembly?
-
To ensure component quality, source from reputable suppliers, request certificates of conformance (COC), and consider implementing incoming quality control (IQC) procedures.
-
What are some common PCB assembly defects, and how can they be prevented?
-
Common PCB assembly defects include solder bridges, tombstoning, and component misalignment. These can be prevented by ensuring proper solder paste application, maintaining appropriate reflow profiles, and implementing automated optical inspection (AOI).
-
How can I choose the right PCB assembly partner for my project?
-
When selecting a PCB assembly partner, consider factors such as their experience, capabilities, quality control processes, and customer support. Request references and samples to evaluate their work.
-
What are the benefits of implementing automation in PCB assembly and production?
- Automation in PCB assembly and production can lead to increased efficiency, improved accuracy, reduced human error, and lower labor costs. It also enables faster production times and more consistent product quality.
Conclusion
Keeping your PCB assembly and production processes seamless is essential for delivering high-quality products on time and within budget. By focusing on design for manufacturability, effective communication and collaboration, automation and technology, and continuous improvement, you can optimize your PCB assembly and production processes for success.
Remember, a seamless PCB assembly and production process is the foundation of a successful electronics manufacturing operation. By implementing the best practices and strategies discussed in this article, you can ensure that your PCBs are produced efficiently, consistently, and to the highest standards of quality.
Leave a Reply