Introduction
The evolution of printed circuit board (PCB) design has been a crucial factor in enabling SpaceX to achieve its ambitious goals in space exploration. PCBs are the backbone of modern electronics, and their design and manufacturing processes have undergone significant advancements over the years. These advancements have allowed SpaceX to develop cutting-edge technologies that are essential for their rockets, spacecraft, and satellites.
In this article, we will explore how the evolution of PCB design has contributed to SpaceX’s success and how it has enabled them to push the boundaries of space exploration. We will also discuss the key aspects of PCB design that are critical for space applications and how SpaceX has leveraged these aspects to create reliable and high-performance systems.
The Role of PCBs in Space Applications
PCBs play a vital role in space applications, as they are responsible for interconnecting and supporting various electronic components within a system. In the harsh environment of space, PCBs must be able to withstand extreme temperatures, radiation, and vibrations. Additionally, they must be lightweight, compact, and highly reliable to ensure the success of the mission.
SpaceX has recognized the importance of PCB design in their space applications and has invested heavily in developing advanced PCB technologies. They have collaborated with leading PCB manufacturers and design firms to create custom PCBs that meet their specific requirements.
Key Aspects of PCB Design for Space Applications
-
Material Selection: The choice of materials used in PCB fabrication is crucial for space applications. The materials must be able to withstand extreme temperatures, radiation, and outgassing. SpaceX uses high-quality, space-grade materials such as polyimide, PTFE, and ceramic for their PCBs.
-
Thermal Management: PCBs in space applications must be able to dissipate heat efficiently to prevent overheating and ensure reliable operation. SpaceX uses advanced thermal management techniques such as heat sinks, thermal vias, and phase change materials to keep their PCBs cool.
-
Signal Integrity: Maintaining signal integrity is essential for ensuring the proper functioning of electronic systems in space. SpaceX uses advanced signal integrity analysis tools and techniques to optimize their PCB designs for high-speed and high-frequency applications.
-
Reliability: PCBs in space applications must be highly reliable and able to withstand the harsh environment of space for extended periods. SpaceX uses rigorous testing and qualification processes to ensure the reliability of their PCBs.
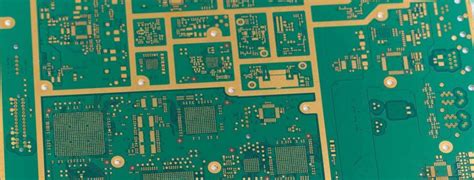
The Evolution of PCB Design
The evolution of PCB design has been driven by the ever-increasing demands for higher performance, smaller form factors, and lower costs. Over the years, PCB design has undergone significant advancements in terms of materials, manufacturing processes, and design tools.
Advancements in PCB Materials
One of the key advancements in PCB design has been the development of new materials that offer improved performance and reliability. Some of the most notable advancements in PCB materials include:
-
High-Temperature Materials: The development of high-temperature materials such as polyimide and PTFE has enabled the design of PCBs that can withstand extreme temperatures.
-
Low-Loss Materials: The use of low-loss materials such as Rogers and Isola has enabled the design of high-frequency PCBs with improved signal integrity.
-
Flexible Materials: The development of flexible materials such as polyimide and PET has enabled the design of flexible PCBs that can conform to unique shapes and sizes.
Advancements in PCB Manufacturing Processes
Another key advancement in PCB design has been the development of new manufacturing processes that offer improved precision, reliability, and cost-effectiveness. Some of the most notable advancements in PCB manufacturing processes include:
-
High-Density Interconnect (HDI): HDI technology has enabled the design of highly compact and dense PCBs with improved signal integrity and reduced signal loss.
-
Embedded Components: The ability to embed components such as resistors, capacitors, and inductors within the PCB has enabled the design of highly integrated and compact systems.
-
3D Printing: The use of 3D printing technology has enabled the rapid prototyping and manufacturing of complex PCB designs with unique shapes and structures.
Advancements in PCB Design Tools
The evolution of PCB design has also been driven by the development of advanced design tools that offer improved automation, simulation, and optimization capabilities. Some of the most notable advancements in PCB design tools include:
-
Automated Design Rule Checking (DRC): DRC tools have enabled the automatic verification of PCB designs against a set of predefined design rules, reducing the risk of errors and improving the quality of the final product.
-
Signal Integrity Analysis: Signal integrity analysis tools have enabled the simulation and optimization of high-speed and high-frequency PCB designs, ensuring reliable and robust performance.
-
Thermal Analysis: Thermal analysis tools have enabled the simulation and optimization of PCB thermal management, ensuring reliable operation in extreme temperature environments.
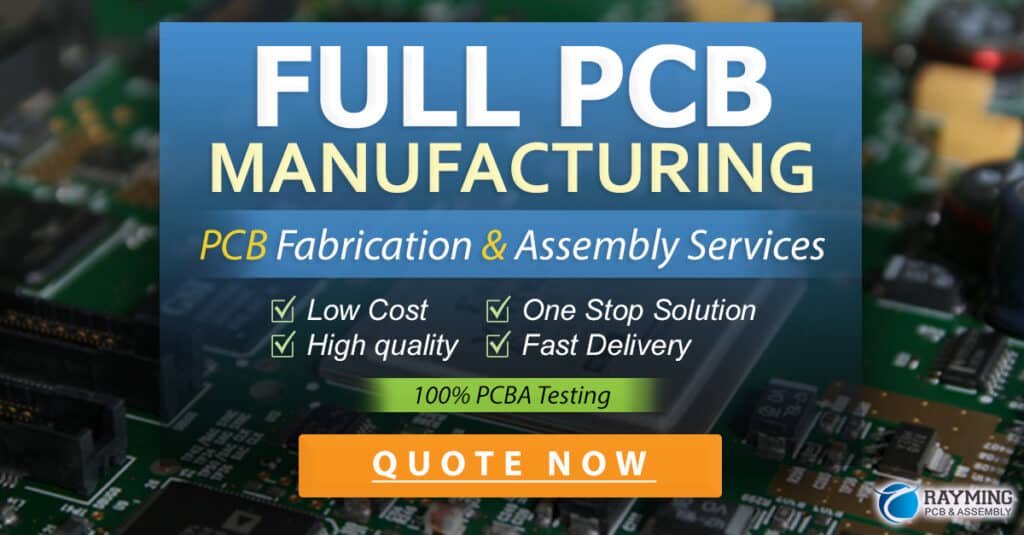
How SpaceX Has Leveraged the Evolution of PCB Design
SpaceX has been at the forefront of leveraging the evolution of PCB design to create advanced and reliable systems for their space applications. Some of the key ways in which SpaceX has leveraged the evolution of PCB design include:
Custom PCB Design
SpaceX has invested heavily in custom PCB design to create highly optimized and reliable systems for their space applications. They have collaborated with leading PCB design firms and manufacturers to create custom PCBs that meet their specific requirements.
Advanced Materials
SpaceX has leveraged the advancements in PCB materials to create PCBs that can withstand the harsh environment of space. They have used high-temperature materials such as polyimide and PTFE, as well as low-loss materials such as Rogers and Isola, to create PCBs with improved performance and reliability.
High-Density Interconnect (HDI)
SpaceX has leveraged HDI technology to create highly compact and dense PCBs for their space applications. This has enabled them to create smaller and lighter systems that are essential for reducing the cost and complexity of space missions.
Embedded Components
SpaceX has leveraged the ability to embed components within the PCB to create highly integrated and compact systems. This has enabled them to reduce the size and weight of their systems, as well as improve their reliability and performance.
Advanced Design Tools
SpaceX has leveraged advanced PCB design tools to optimize their designs for high-speed and high-frequency applications. They have used signal integrity analysis tools to ensure reliable and robust performance, as well as thermal analysis tools to optimize their thermal management strategies.
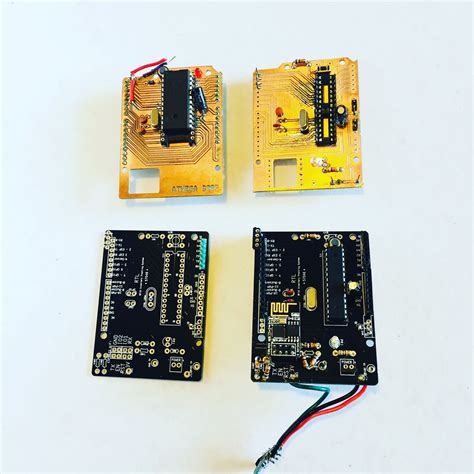
The Future of PCB Design in Space Applications
The future of PCB design in space applications is expected to be driven by the continued advancements in materials, manufacturing processes, and design tools. Some of the key trends that are expected to shape the future of PCB design in space applications include:
-
Miniaturization: The trend towards miniaturization is expected to continue, with the development of even smaller and more compact PCBs that can be used in a wide range of space applications.
-
Increased Integration: The trend towards increased integration is expected to continue, with the development of PCBs that can integrate more components and functions within a single package.
-
Advanced Materials: The development of advanced materials with improved performance and reliability is expected to continue, enabling the design of PCBs that can withstand even harsher environments and conditions.
-
Additive Manufacturing: The use of additive manufacturing techniques such as 3D printing is expected to become more prevalent in PCB design, enabling the rapid prototyping and manufacturing of complex PCB designs.
Conclusion
The evolution of PCB design has been a critical factor in enabling SpaceX to achieve its ambitious goals in space exploration. The advancements in materials, manufacturing processes, and design tools have enabled SpaceX to create highly optimized and reliable systems that are essential for their space applications.
As the demands for space exploration continue to grow, the evolution of PCB design is expected to play an even more critical role in enabling the development of advanced and reliable systems. With the continued advancements in materials, manufacturing processes, and design tools, the future of PCB design in space applications looks bright, and we can expect to see even more ambitious and exciting space missions in the years to come.
Frequently Asked Questions (FAQ)
-
What is a printed circuit board (PCB)?
A printed circuit board (PCB) is a flat board made of insulating material with conductive tracks on one or both sides. It is used to mechanically support and electrically connect electronic components using conductive pathways, tracks, or signal traces etched from copper sheets laminated onto a non-conductive substrate. -
Why are PCBs important for space applications?
PCBs are essential for space applications because they provide a reliable and compact way to interconnect and support various electronic components within a system. In the harsh environment of space, PCBs must be able to withstand extreme temperatures, radiation, and vibrations, while being lightweight and highly reliable to ensure the success of the mission. -
What are some of the key advancements in PCB materials for space applications?
Some of the key advancements in PCB materials for space applications include the development of high-temperature materials such as polyimide and PTFE, low-loss materials such as Rogers and Isola, and flexible materials such as polyimide and PET. These materials offer improved performance and reliability in the harsh environment of space. -
How has SpaceX leveraged the evolution of PCB design?
SpaceX has leveraged the evolution of PCB design by investing in custom PCB design, using advanced materials, leveraging high-density interconnect (HDI) technology, embedding components within the PCB, and using advanced design tools such as signal integrity analysis and thermal analysis tools. -
What are some of the future trends in PCB design for space applications?
Some of the future trends in PCB design for space applications include continued miniaturization, increased integration, the development of advanced materials with improved performance and reliability, and the use of additive manufacturing techniques such as 3D printing for rapid prototyping and manufacturing of complex PCB designs.
PCB Evolution Timeline
Year | Advancement | Impact |
---|---|---|
1936 | First PCB developed | Revolutionized electronics manufacturing |
1943 | Double-sided PCBs introduced | Allowed for more complex circuits and higher component density |
1960 | Through-hole technology becomes widespread | Improved reliability and made assembly easier |
1970 | Multi-layer PCBs introduced | Enabled even higher component density and more complex designs |
1980 | Surface mount technology (SMT) introduced | Allowed for smaller components and higher density PCBs |
1990 | High-density interconnect (HDI) developed | Enabled even smaller and more complex PCBs with finer pitch and higher layer counts |
2000 | Flexible PCBs gain popularity | Allowed for PCBs to be used in applications where flexibility and conformity are required |
2010 | Advanced materials and processes developed | Improved thermal management, signal integrity, and reliability for high-performance applications |
2020 | Additive manufacturing techniques introduced | Enabled rapid prototyping and manufacturing of complex PCB designs |
This timeline showcases some of the key advancements in PCB design over the years, highlighting how each advancement has contributed to the evolution of PCB technology and its impact on various industries, including space applications.
Leave a Reply